ASM aluminum silicon alloy die casting: the best choice for modern manufacturing industry
In modern manufacturing industry, ASM aluminum silicon die casting parts have attracted much attention due to their unique characteristics. They have excellent performance and are widely used in automotive, aerospace, electronics and other fields. The basis of many key details. Material selection.
1.Basic knowledge of ASM aluminum silicon alloy
(1) Definition and characteristics of aluminum silicon alloy
ASM aluminum silicon die casting is mainly composed of aluminum and silicon, of which the silicon content is generally 5%-23%. This die casting alloy has many advantages. First, it is light in weight but high in strength, and can provide sufficient mechanical properties while ensuring the lightweight of the product. Secondly, it has good thermal conductivity, heat resistance and electrical conductivity, suitable for various applications. In addition, it also has good corrosion resistance and can maintain stable performance even in harsh environments. Due to its excellent casting performance, low expansion coefficient and good wear resistance, it is widely used in automotive, aerospace, electrical and other industrial fields.
(2) Definition of aluminum silicon alloy in ASM standard
ASM (American Society for Metals) standard specifies the composition, mechanical properties and application of aluminum silicon alloy in detail, providing reliable reference information for manufacturers and users and ensuring product quality. Cast aluminum silicon alloys that meet ASM standards have a high degree of acceptance in the market.
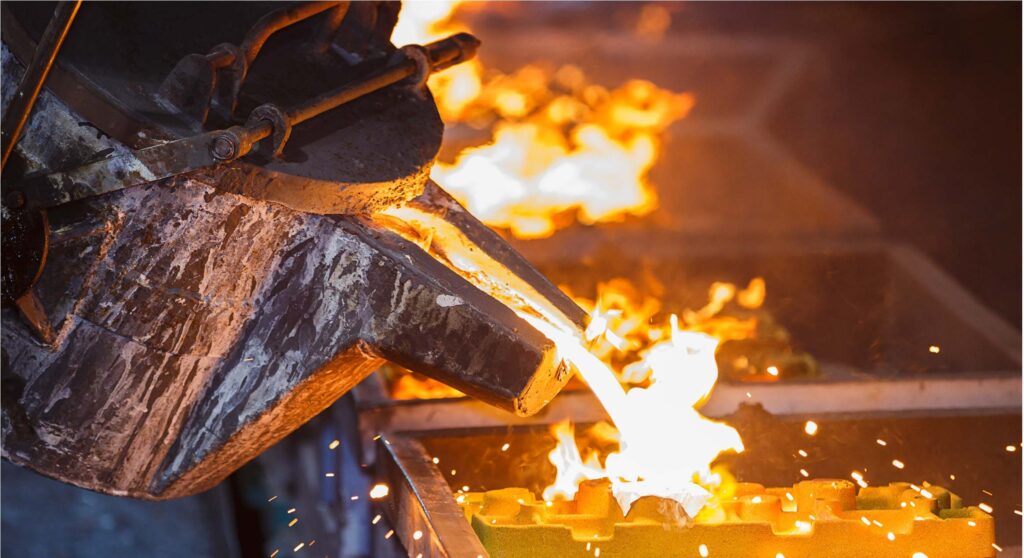
2.ASM aluminum silicon die casting: die casting machine and production
(1) The role of injection molding machine
Die casting machine is the main equipment for producing ASM aluminum silicon die castings. The die casting process is to inject molten alloy into the mold cavity under high pressure to produce castings with complex shapes and high dimensional accuracy. The performance of the die casting machine directly affects the die casting quality, such as surface quality, dimensional accuracy, etc.
(2) Selecting a suitable die casting machine
When selecting a die casting machine, manufacturers must comprehensively consider the alloy characteristics, production scale and part complexity. For ASM aluminum silicon die casting, cold chamber die casting machines are usually a more suitable choice because they can process the alloy at higher temperatures and avoid the problem of high temperature damage suffered by hot chamber die casting machines. In addition, cold chamber die casting machines are very suitable for manufacturing large and complex parts.
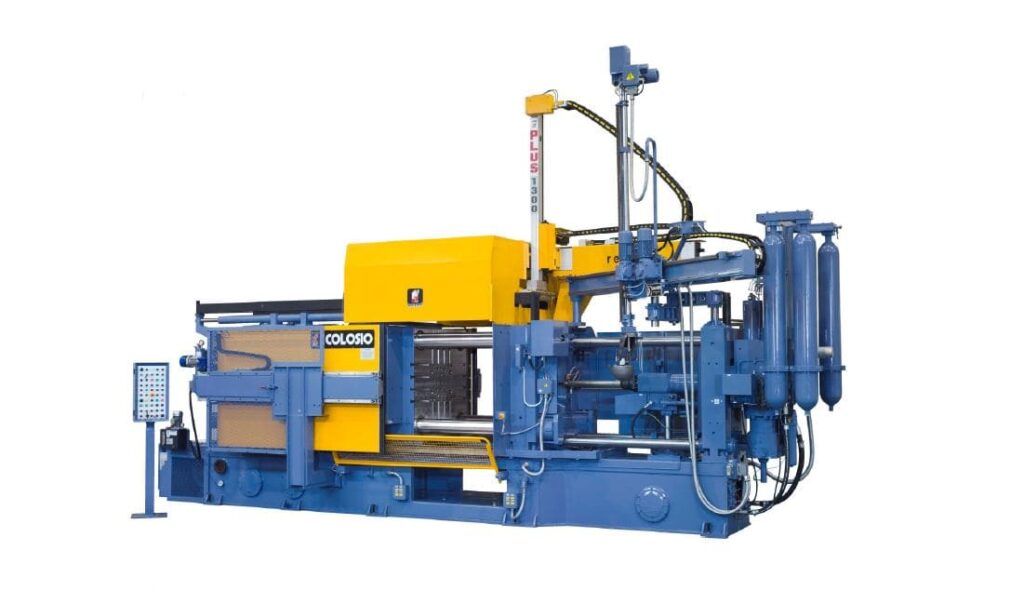
П
3.ASM aluminum silicon die casting production process
(1) Material preparation
Selecting the right aluminum alloy is crucial for die casting. First, ensure that the alloy used meets the ASM standard to ensure the quality of the finished product. Second, during the smelting process, the temperature and time must be strictly controlled to prevent changes in the alloy composition.
(2) Die casting process
The die casting process includes melting, injection, cooling and demolding. Accurate control of die casting machine parameters such as pressure, speed and temperature is crucial to ensure the quality of the final product. For aluminum silicon alloy, due to its high melting point and low expansion coefficient, the control of mold temperature during cooling is particularly important to prevent cracking or warping of the casting.
(3) Post-processing
After demolding, ASM aluminum silicon die casting parts usually require a series of post-processing steps, such as deburring, heat treatment, surface treatment, etc. Heat treatment can improve the mechanical properties of the alloy, and surface treatment can improve corrosion resistance and appearance quality.
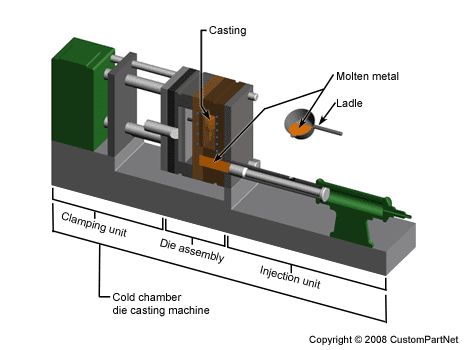
4.Application of ASM aluminum silicon die casting
(1) Automobile industry
Aluminum silicon alloy is widely used in automobile engine blocks, cylinder heads, gearbox housings and wheels due to its superior wear resistance and light weight. The main components are usually cast with aluminum silicon alloy molds, which not only reduces the weight of the whole vehicle and improves fuel efficiency, but also improves the reliability and durability of the components. The ASM standard ensures the high reliability and long service life of these key components.
(2) Aerospace industry
In the aerospace industry, weight and performance requirements are extremely high. Due to the superior performance of aluminum silicon alloy die castings, they are used to produce lightweight, high-strength aircraft engine components and structural parts, such as fuselage frames, engine components, etc. These parts must not only have excellent mechanical properties, but also remain stable under extreme temperatures. The ASM standard is particularly important in such applications.
(3) Electrical and electronic fields
ASM aluminum silicon die casting is increasingly used in electronic and electrical equipment, especially electronic equipment housings, radiators, connectors and other components. These components must not only have good heat dissipation and conductivity, but also have certain corrosion resistance and oxidation resistance.
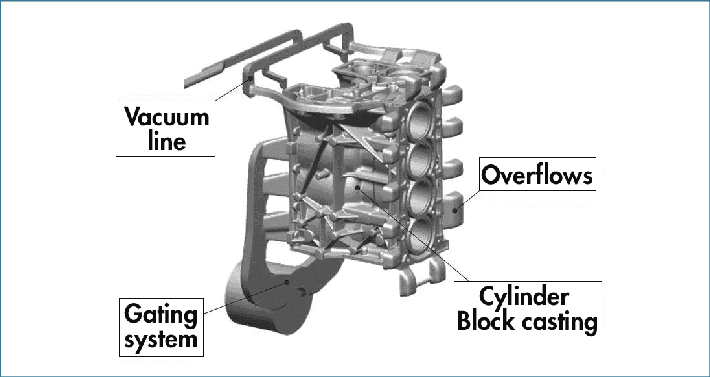
5.How to improve the quality of ASM aluminum silicon die casting parts
(1) Die casting machine parameter optimization
In order to improve the quality of aluminum silicon die castings, manufacturers must continuously optimize die casting machine parameters. Accurate control of feed speed, die pressure and temperature can greatly reduce casting defects such as pores, shrinkage and cracks.
(2) Introducing automated and intelligent production
The introduction of automated technologies such as robot die casting systems and die temperature control can significantly improve production efficiency and product uniformity. In addition, technologies such as real-time monitoring and big data analysis in intelligent manufacturing can help manufacturers adjust production parameters in a timely manner and prevent quality problems.
(3) Strengthen quality control
During the production process, advanced testing equipment such as X-ray detectors and three-coordinate measuring machines are used to perform high-precision inspections on the internal structure and external dimensions of castings to ensure that the products meet strict requirements.
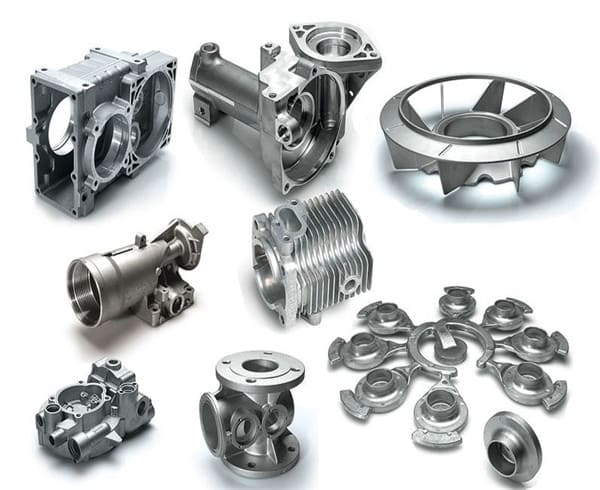
6.The future of ASM aluminum silicon die casting
With the development of science and technology, aluminum silicon alloy die castings have a bright future. Advances in materials science are optimizing their composition characteristics to meet the needs of various fields. Innovations in die casting processes and casting machines will improve quality and efficiency. At the same time, environmental protection requirements will help it develop in the direction of green energy saving.
As an important injection molding material, ASM aluminum silicon die-casting parts have become the first choice of many industries with their superior performance and wide applicability. Reasonable selection of die-casting machines, optimization of process flow, and strengthening of quality management enable us to produce high-quality products that meet market demand.
This article provides users with comprehensive knowledge, which is undoubtedly an indispensable reference for those who seek to improve product quality or gain in-depth understanding of the application of ASM aluminum silicon die-casting.