Application of investment castings in the aerospace industry
Investment casting, also known as precision casting or lost wax casting, is a casting process widely used in the aerospace manufacturing field.
Aerospace investment castings mainly include key components such as aircraft engine parts, aerospace structural parts and connectors. The production and manufacturing of these parts are crucial to the aerospace industry.
This article will discuss in detail the characteristics of investment castings and their specific applications in the aerospace field.
1.The production principle and characteristics of investment castings
(1) The production principle and process of investment castings
The principle of investment casting is to use fusible materials (such as wax) to make a precise fusible model, and then apply several layers of refractory coating on the model, which is dried and hardened to form an integral shell. Then the shell is heated to melt and discharge the model, and then it is calcined at high temperature to make the shell a refractory cavity.
Finally, liquid metal is poured into the cavity and the casting is formed after cooling. The specific process includes: mold material preparation (wax mold), mold assembly and mold repair, coating and sanding, demolding and roasting, pouring and cooling, sand removal and cleaning.
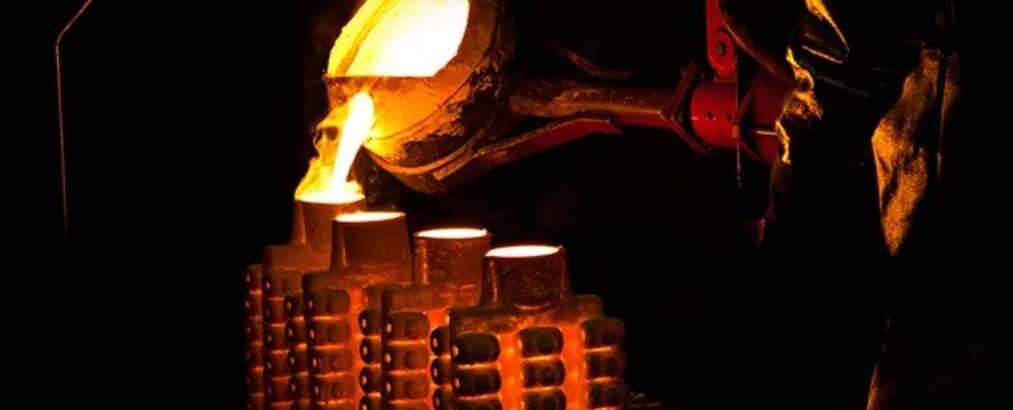
(2) Significant features of investment castings
1) High dimensional accuracy:
The dimensional accuracy of investment castings is high, generally up to CT4-6, and the surface finish is also good, usually up to Ra.1.6~3.2μm. This is because the use of fusible models and refractory coatings avoids dimensional errors in traditional casting methods.
2) Good surface quality:
The surface finish of investment castings is high, which reduces the amount of subsequent processing, can achieve less or no cutting processing, and save machine tools and processing time.
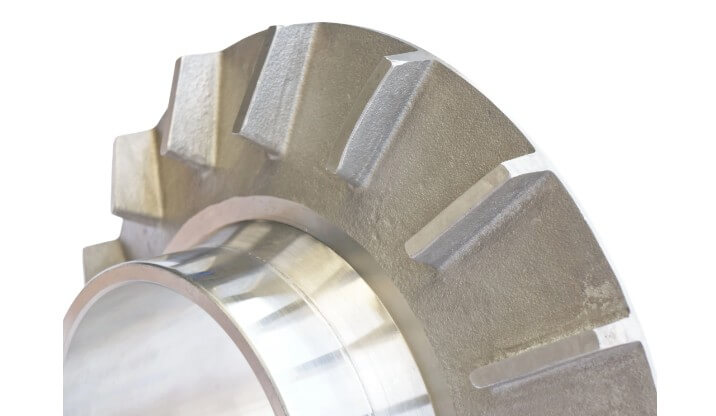
3) Strong adaptability:
Applicable to various alloy materials, including carbon steel, stainless steel, alloy steel, cast iron, copper, aluminum alloy, etc., especially suitable for high melting point and difficult to process high alloy steel.
4) Complex shapes can be cast:
It can cast castings with complex shapes that are difficult to process by other methods, such as impellers, hollow blades, etc. It can also cast castings with thinner wall thickness and lighter weight.
5) Flexible production batch:
The investment casting process is suitable for single-piece, batch and mass production. The production batch is not limited and can meet the production needs of different scales.
6) High material utilization rate:
The use of molten metal casting reduces material waste and improves material utilization rate.
7) No parting surface:
Due to the use of an integral shell, investment casting does not require a parting surface, thus avoiding the dimensional error and surface defects caused by the parting surface.
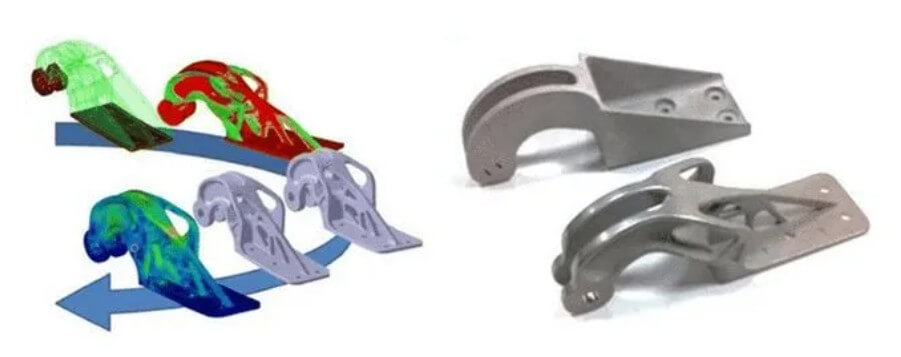
2.Specific applications of aerospace investment castings
(1) Aircraft engine components
1) Turbine blades:
Investment casting can produce turbine blades with high dimensional accuracy, complex shapes and the ability to withstand high temperature and high pressure. These blades are the core components of aircraft engines and directly affect the performance and reliability of the engine.
2) Integral blade disk:
Integral blade disk is made by casting blades and impeller as a whole, which reduces the use of connecting parts and improves the efficiency and reliability of the engine. Investment casting is an ideal process for manufacturing integral blade disk.
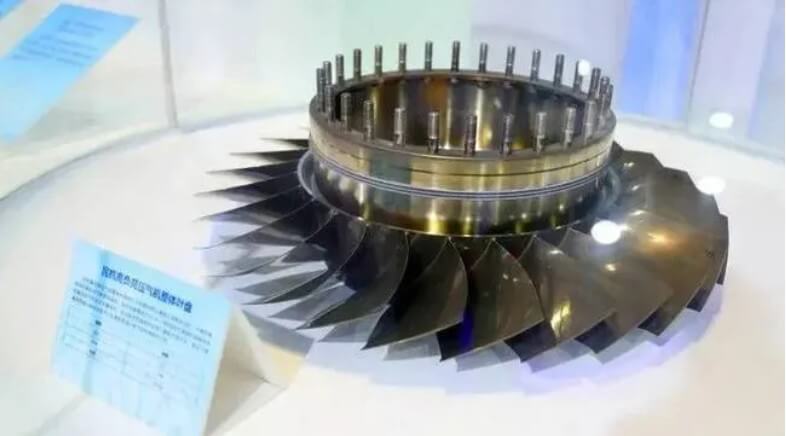
3) Combustion chamber:
The combustion chamber is another key component of the aircraft engine, which needs to withstand extremely high temperature and pressure. Investment casting can produce combustion chambers with complex structures to meet its high performance requirements.
(2) Aerospace structural parts and connecting parts
1) Frames and beams:
The frames and beams of aerospace vehicles can be investment castings. These parts require high strength and light weight. By optimizing the structural design, investment casting can integrate multiple assemblies into an integral part, reduce weight and improve structural strength.
2) Landing gear parts:
The landing gear is one of the important parts of the aircraft and needs to withstand large loads and impacts. Investment casting can produce high-strength and high-toughness landing gear parts to ensure the safe take-off and landing of the aircraft.
3) Door and window frames:
Door and window frames can also be made of investment castings. These parts require precise dimensions and good sealing performance, and investment casting can meet their manufacturing requirements.
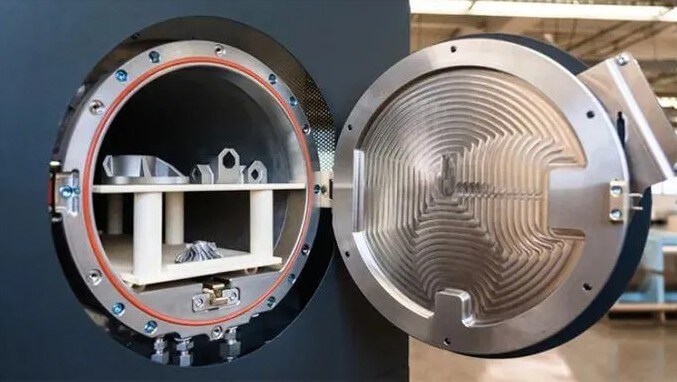
(3) Thin-walled precision parts
Investment casting can produce large, thin-walled, and complex aluminum alloy components. These components are widely used in aerospace, such as satellite structural parts and aircraft skins. Aluminum alloy precision casting technology can produce components with large outline dimensions and thin wall thickness to meet the needs of lightweight aerospace.
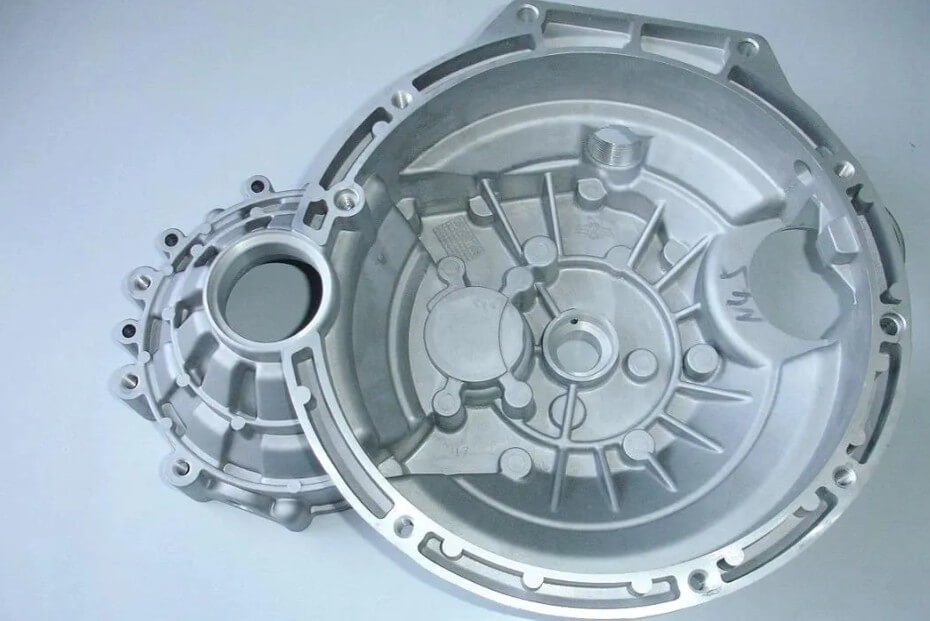
2) Titanium alloy structural parts:
Titanium alloy has high strength, low density and excellent corrosion resistance and is widely used in the aerospace field. Investment casting can produce complex titanium alloy structural parts, such as aircraft wing joints and fuselage reinforcement frames.
(4) Other key components
1) Fuel system components:
Nozzles, pump bodies and other components in the fuel system require high precision and good corrosion resistance.
Investment castings made with sophisticated processes can meet these requirements.
2) Hydraulic and pneumatic system components:
Valves, cylinders and other components in hydraulic and pneumatic systems have high requirements for dimensional accuracy and surface finish. Investment casting can produce investment castings that meet the requirements.
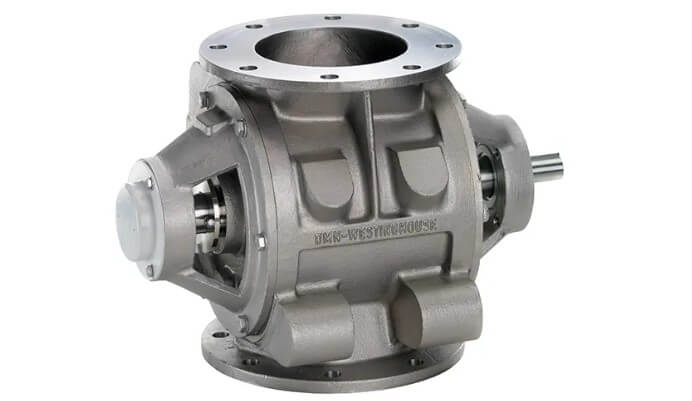
3.Strategies for optimizing investment casting production processes to meet the high requirements of the aerospace industry
In order to meet the strict requirements of this field for the dimensional accuracy, surface quality, material properties and production efficiency of investment castings, the following are optimization strategies for investment casting production processes from several aspects:
(1) Material selection and improvement:
● Select high-performance wax and refractory materials to improve the accuracy and strength of the mold shell.
● Develop new alloy materials to meet performance requirements in extreme environments, such as high temperature strength and oxidation resistance.
(2) Process parameter control:
● Accurately control the mold material temperature, pressure and cooling rate to ensure the dimensional accuracy and surface quality of the wax mold.
● Optimize the pouring system design to avoid turbulence and oxidation during the flow of molten metal and reduce defects.
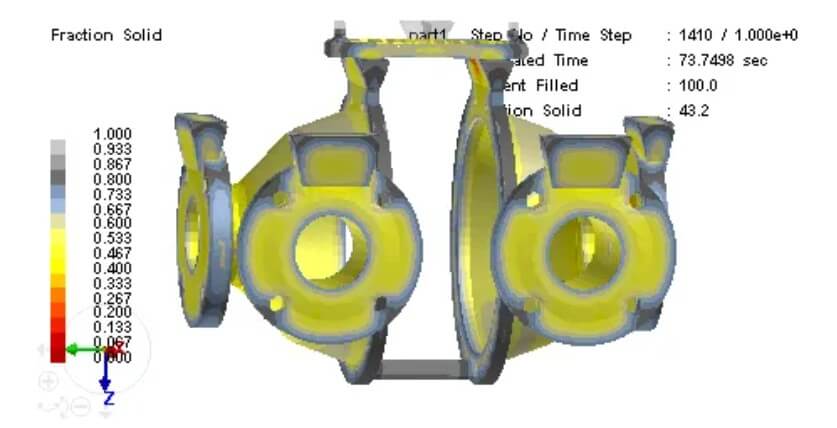
(3) Application of digital technology:
● Use CAD/CAE software to design and simulate castings and molds to predict and solve potential problems.
● Use 3D printing technology to manufacture wax molds and shells to improve production efficiency and customization capabilities.
(4) Process automation and monitoring:
● Introduce automated equipment for coating, sanding, roasting and other processes to reduce errors caused by manual operations.
● Implement an online monitoring system to monitor key parameters such as temperature and pressure during the casting process in real time to ensure process stability.
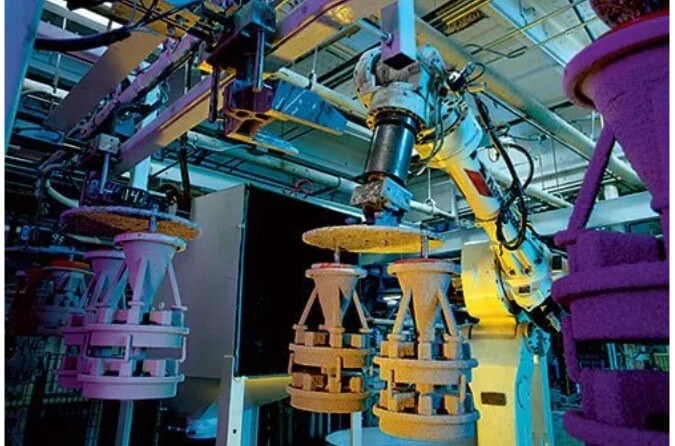
(5) Quality inspection and feedback:
● Use non-destructive testing technologies such as X-rays and CT scans to promptly detect internal defects in castings.
● Establish a complete quality feedback mechanism to continuously optimize the production process based on the test results.
Summary:
Through the implementation of the above strategies, the quality and production efficiency of investment castings can be effectively improved to meet the growing demand of the aerospace industry for high-performance, lightweight castings.
4.Conclusion
Investment casting technology has an important position and broad application prospects in the manufacturing of aerospace parts. Investment castings have significant advantages in the application of aerospace parts with complex shapes and thin-walled structures due to their high precision and high surface quality.
What do you think?
[…] the casting requires high precision and surface quality, such as aerospace, medical equipment and other fields, investment casting should be selected; if the precision and […]