Analysis of Quenching Heat Treatment Microstructure and Its Effects
Quenching is an important heat treatment method that heats the material to above the critical temperature by rapid cooling, thereby changing its microstructure and significantly affecting the mechanical properties of the material.
The following will discuss in detail the formation process of quenching heat treatment microstructure, common microstructure types and their effects on material properties.
1.Basic principles of quenching heat treatment
The basic principle of quenching heat treatment is to heat the material to above the austenitizing temperature, keep it warm for a period of time to make the material completely austenitized, and then cool it rapidly so that the austenite has no time to decompose and directly transforms into martensite. The key to this process is that the cooling rate must be greater than the critical cooling rate to avoid the decomposition of austenite into other microstructures, such as pearlite or bainite.
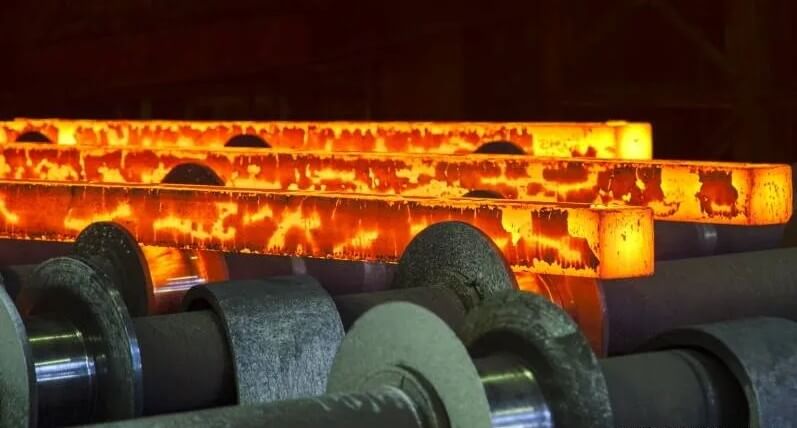
2.Formation process of quenching heat treatment microstructure
(1) Austenitization:
Austenitization is the first step in the quenching process, which involves heating the steel to above the critical temperature, usually between 727°C and 912°C, depending on the chemical composition of the steel. During this process, the ferrite and cementite in the steel are transformed into a uniform austenite structure. Austenite is a solid solution of carbon in γ-iron with good plasticity and toughness.
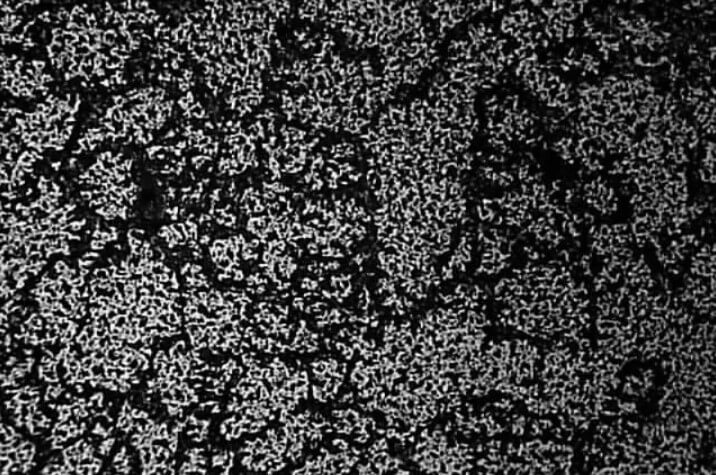
(2) Cooling transformation:
When austenite is cooled rapidly, because the cooling rate is greater than the critical cooling rate, austenite does not have time to decompose into pearlite or bainite through diffusion-type phase transformation, but directly transforms into martensite. Martensite is a structure with high hardness and high strength, but its plasticity is poor.
(3) Residual austenite:
During the actual quenching process, due to uneven cooling rate or the influence of material composition, part of the austenite may not be completely transformed into martensite, but remain to form residual austenite. The presence of residual austenite will reduce the hardness and strength of the material, but can improve the toughness of the material.
3.Common quenching heat treatment microstructure
(1) Martensite:
Martensite is the most common quenching heat treatment microstructure with high hardness and high strength. The morphology of martensite mainly includes lath and needle. Lath martensite has good plasticity and toughness, while needle martensite has higher hardness but poor toughness.
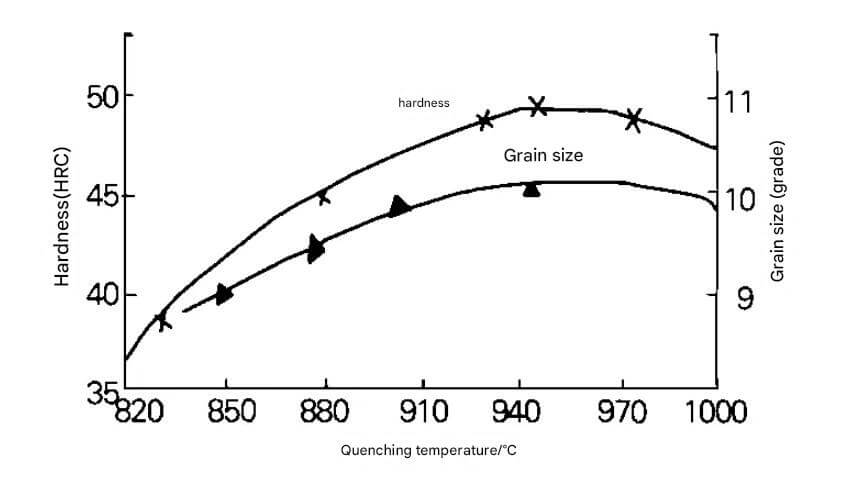
The structure of 27simn steel after quenching at 930℃ (a) Optical microscope photo ×400 (b)
(2) Bainite:
Bainite is a structure between pearlite and martensite with medium hardness and strength. The formation temperature of bainite is between pearlite and martensite, and it is easy to form when the cooling rate is slow. Bainite structure can improve the toughness and wear resistance of the material.
(3) Pearlite:
Pearlite is a lamellar structure composed of ferrite and cementite, with low hardness but good plasticity and toughness. The formation temperature of pearlite is low, and it is easy to form when the cooling rate is slow. During quenching, if the cooling rate is insufficient, austenite may decompose into pearlite.
(4) Retained austenite:
As mentioned above, retained austenite is austenite that fails to completely transform into martensite during quenching. The amount of retained austenite depends on factors such as material composition, cooling rate and quenching process.
4.Effect of quenching heat treatment microstructure on material properties
(1) Hardness:
The martensitic structure has high hardness, so the hardness of the material is significantly improved after quenching. The hardness of martensite depends on its carbon content and morphology. High carbon martensite has higher hardness but poorer toughness.
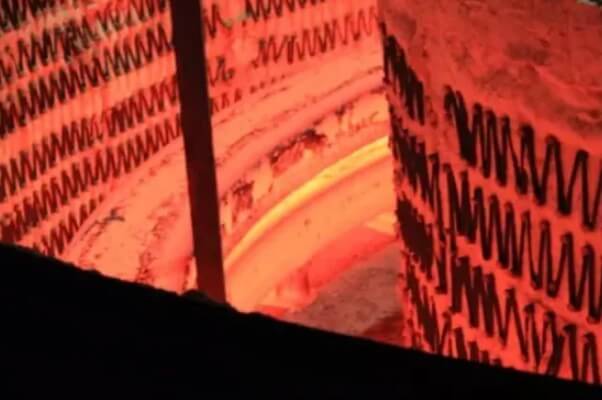
(2) Strength:
The strength of the material is also significantly improved after quenching, mainly due to the high strength of the martensitic structure. The strength of martensite depends on its carbon content and dislocation density. High carbon martensite has higher strength.
(3) Toughness:
The toughness of the material will decrease after quenching, mainly due to the low plasticity of the martensitic structure. However, an appropriate amount of residual austenite can improve the toughness of the material. In addition, lath martensite has good toughness, so in some applications, a good balance of strength and toughness can be obtained by controlling the quenching process.
(4) Wear resistance:
The high hardness of the martensitic structure makes it have good wear resistance. In addition, the bainitic structure also has certain wear resistance, so in some applications that require wear resistance, an appropriate quenching process can be selected to obtain the bainitic structure.
5.Factors affecting the quenching heat treatment microstructure
(1) Material composition:
The composition of the material has a significant effect on the quenching heat treatment microstructure. Carbon content is an important factor affecting the formation of martensite. High carbon steel is easy to form high hardness martensite after quenching. In addition, alloying elements will also affect the formation of quenching heat treatment microstructure. For example, elements such as chromium, molybdenum, and vanadium can improve the hardenability of steel.
(2) Heating temperature and time:
The heating temperature and time determine the degree of austenitization. If the heating temperature is insufficient or the time is too short, the austenitization is insufficient, which will affect the structure after quenching. On the contrary, if the heating temperature is too high or the time is too long, it may cause grain coarsening and reduce the performance of the material.
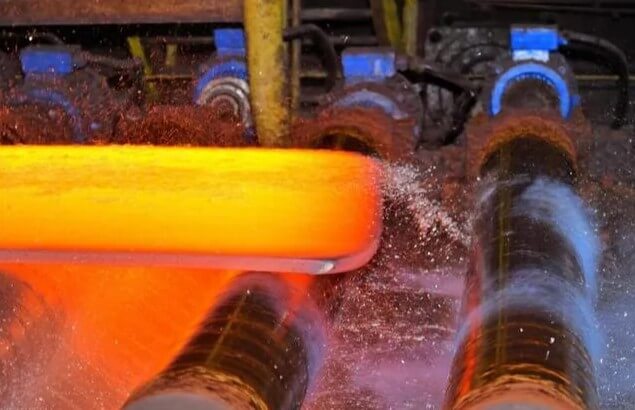
(3) Cooling rate:
The cooling rate is the key factor in determining the quenching heat treatment microstructure. The cooling rate must be greater than the critical cooling rate to avoid the decomposition of austenite into pearlite or bainite. The faster the cooling rate, the more martensite is formed and the higher the hardness.
(4) Quenching medium:
The choice of quenching medium has a direct impact on the cooling rate. Commonly used quenching media include water, oil, and salt water. Water has the fastest cooling rate, but it is easy to cause material deformation and cracking; oil has a slower cooling rate, but it can reduce the risk of deformation and cracking.
6.Application of quenching process
(1) Tool steel:
Tool steel usually requires high hardness and high wear resistance, so quenching treatment is often used. By controlling the quenching process, a high-hardness martensitic structure can be obtained to increase the service life of the tool.
(2) Bearing steel:
Bearing steel requires high hardness and high fatigue strength, so quenching treatment is also often used. The martensitic structure formed after quenching can improve the bearing capacity and service life of the bearing.
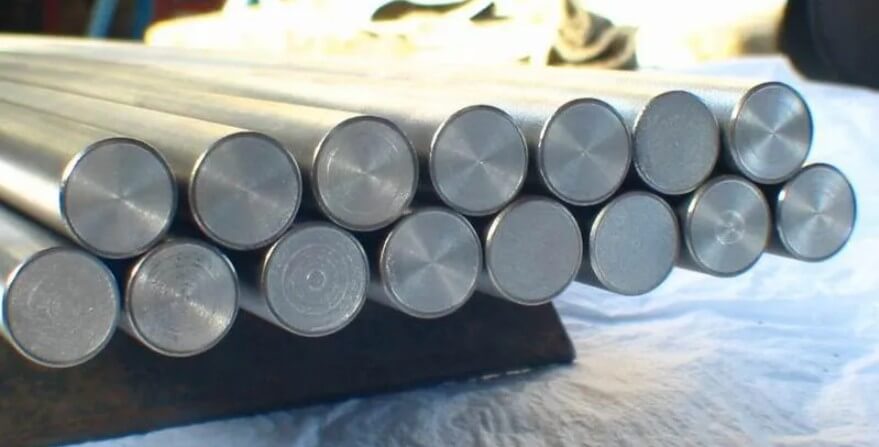
(3) Mold steel:
Mold steel requires high hardness, high strength and high wear resistance, so quenching treatment is also often used. By controlling the quenching process, a quenching heat treatment microstructure with good comprehensive performance can be obtained.
(4) Structural steel:
Some structural steels also need to be quenched to improve their strength and hardness to meet specific use requirements.
7.Conclusion
Quenching heat treatment is an important material modification method. By controlling factors such as heating temperature, holding time, cooling rate and quenching medium, different quenching heat treatment microstructure can be obtained, which significantly affects the mechanical properties of the material.
Understanding the formation process of quenching heat treatment microstructure and its influence on material properties is of great significance for the rational selection of materials and the formulation of heat treatment processes. In practical applications, the appropriate quenching process should be selected according to the specific use requirements to obtain the best performance combination.