Aluminum Extrusion Die: Design and Optimization Guide
In the design and manufacturing process of aluminum extrusion dies, there are several key factors that cannot be ignored. The selection of materials, the design of the structure, the determination of the processing technology, etc. all directly affect the performance and service life of the die. This article will start from the above perspectives and comprehensively analyze the design and optimization process of aluminum extrusion dies.
1.Importance and application of aluminum extrusion dies
As a key component in the production of aluminum profiles, the design and manufacturing quality of aluminum extrusion dies directly affect the product quality and production efficiency of aluminum. In modern industry, aluminum profiles are widely used in construction, aviation, automobiles, electronics and other fields due to their advantages such as light weight, high strength and good machinability. With the advancement of industrial technology and the diversification of market demand, the design and manufacturing technology of aluminum extrusion dies are also constantly developing to meet the production requirements of higher precision and higher efficiency.
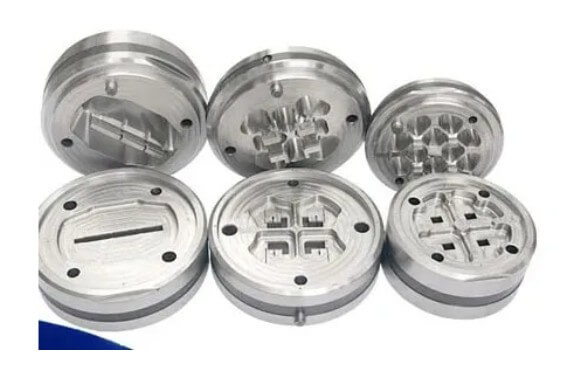
2.Application advantages of aluminum extrusion dies
(1) Aluminum profile extrusion molding:
Aluminum extrusion dies are mainly used to extrude aluminum alloy materials into aluminum profiles of various required shapes, such as aluminum door and window frames for construction, aluminum frames for industry, etc.
(2) Improve production efficiency:
By replacing the mold, aluminum products of different shapes and sizes can be produced quickly, greatly shortening the production preparation time and improving production flexibility.
(3) Optimize material properties:
During the extrusion process, the aluminum alloy material is treated with high temperature and high pressure, its internal structure is optimized, and the mechanical properties and surface quality are significantly improved.
(4) Reduce processing procedures
The extruded aluminum profiles have high dimensional accuracy and good surface roughness. They can usually be used directly without additional machining, which reduces production costs.
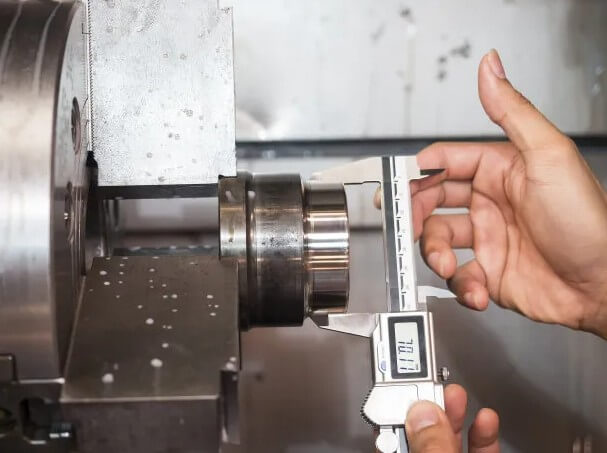
(5) Adapt to complex designs:
Aluminum extrusion dies can produce aluminum profiles with complex cross-sectional shapes to meet diverse design requirements, such as hollow, porous, thin-walled and other structures.
(6) Reduce production energy consumption:
Compared with traditional forging and rolling processes, aluminum extrusion dies have more advantages in equipment investment and energy consumption, which helps enterprises save energy and reduce emissions.
3.Basic requirements and challenges of aluminum extrusion die design
The design of aluminum extrusion dies faces many challenges, mainly including the selection of die materials, structural design, processing technology, heat treatment, etc. The mold material needs to have high temperature strength and wear resistance to withstand the high temperature and high pressure during the extrusion process. The structural design needs to ensure the uniformity of metal flow and the dimensional accuracy of the product. In addition, the manufacturing process and heat treatment of the mold have a direct impact on the performance and life of the mold. Therefore, how to improve the performance and life of the mold by optimizing the design and manufacturing process is a problem in the design of aluminum extrusion dies.
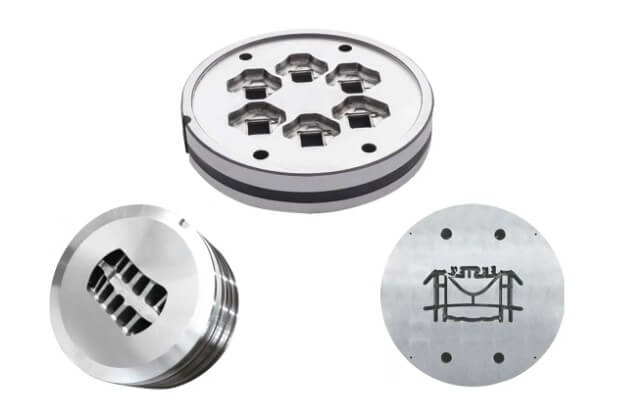
4.Design elements of Aluminum Extrusion Dies
(1) Selection of mold materials
The selection of mold materials is one of the key factors in the design of aluminum extrusion dies. Commonly used mold materials include H13 steel, etc.
1) H13 mold steel:
H13 steel is a commonly used hot working mold steel with good hardness, wear resistance and heat resistance, suitable for aluminum alloy die casting molds. It can maintain good mechanical properties at high temperatures and is suitable for makingaluminum extrusion dies with complex shapes.
2) Tungsten steel:
Tungsten steel has a high melting point and high strength, which is very suitable for the working environment of aluminum extrusion dies under high temperature and high pressure. Its excellent thermal stability ensures that the mold can still maintain accuracy and performance after long-term use.
3) 3Cr2W8V steel:
This steel is often used in aluminum alloy die casting molds due to its excellent thermal strength and thermal stability. 3Cr2W8V steel can withstand high pressure and high temperature and is suitable for the production of large and complex aluminum extrusions.
4) LG mold steel:
LG mold steel is known for its high toughness and hardness of up to HRC56-58, while maintaining excellent crack resistance. It is suitable for cold extrusion aluminum molds and can effectively prevent molds from cracking under high pressure and extend the service life of the mold.
5) High chromium and high molybdenum materials such as DAC55, 8418, and DIEVAR:
These materials contain a higher molybdenum content and have better heat resistance and thermal stability. They are suitable for high temperature and complex structure aluminum alloy die-casting molds and can significantly extend the life of the mold.
(2) Basic structure of aluminum extrusion dies
Aluminum extrusion dies usually consist of three parts: positive mold, mold pad and mold sleeve. Among them, the positive mold is the core part of the mold, which directly determines the shape and size of the aluminum profile. The structure of the positive mold mainly includes the following key parts:
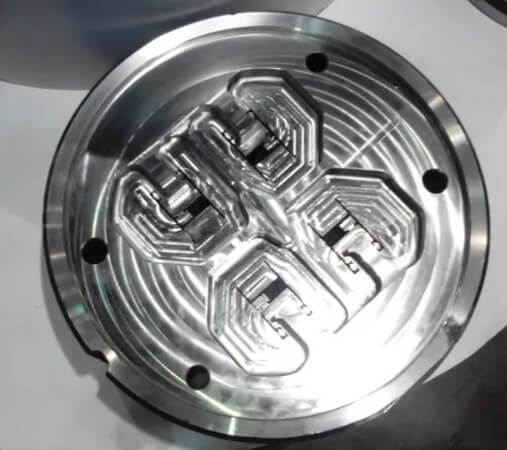
1) Working belt:
The working belt is perpendicular to the working end face of the mold to form the shape of the aluminum profile. The length of the working belt needs to be moderate. If it is too short, the aluminum profile size will be unstable. If it is too long, it will increase metal friction and extrusion force, which will easily lead to metal bonding.
2) Empty knife:
The empty knife is the main channel for the aluminum profile to pass through, which ensures the quality of the aluminum and the life of the mold. The design of the empty knife structure needs to take into account the wall thickness and shape of the aluminum profile to ensure smooth passage.
3) Guide plate (groove):
The guide plate sets the transition shape between the aluminum bar and the aluminum product, which helps to reduce the deformation process. A reasonably designed guide plate can improve the forming quality of the aluminum profile.
4) Diverter hole:
The diverter hole is the channel for aluminum to pass through the mold hole. Its shape, cross-sectional size, number and arrangement directly affect the quality of extrusion molding, extrusion force and mold life. Generally, the number of diverter holes should be as small as possible to reduce welding lines, increase the area of diverter holes and reduce extrusion force.
5) Diverter bridge:
The width of the diverter bridge is related to the mold strength and metal flow. Reasonable design of the diverter bridge can improve the uniformity of metal flow.
6) Mold core:
The mold core determines the size and shape of the inner cavity of the aluminum profile.
7) Welding chamber:
The welding chamber is where the metal gathers and welds. Its design height has an important influence on the metal welding effect and the stability of the mold core.
(3) Key points of aluminum extrusion mold design
1) Working belt design:
The length of the working belt should be determined according to the wall thickness difference of the profile and the distance from the center. For aluminum profiles with complex cross-sections, the design of the working belt needs to comprehensively consider the situation where the mold hole is covered by the diverter bridge.
2) Diverter ratio and extrusion ratio:
The diverter ratio is the ratio of the cross-sectional area of the diverter hole to the cross-sectional area of the profile, and the extrusion ratio is the ratio of the cross-sectional area of the extrusion barrel to the cross-sectional area of the profile. These two parameters directly affect the extrusion resistance, molding quality and welding quality. Reasonable selection of the diverter ratio and extrusion ratio can improve production efficiency and product quality.
3) Reasonable adjustment of aluminum metal flow rate:
In order to ensure that every mass point on the cross section of the aluminum profile flows out of the die hole at the same speed, the flow rate of aluminum metal needs to be reasonably adjusted. Multi-hole symmetrical arrangement should be used in the design of extrusion dies as much as possible, and working belts of different lengths should be designed according to the shape, wall thickness, circumference and distance from the center of the extrusion cylinder of the aluminum profile.
4) Die strength verification:
In die design, die strength is a very important issue. Shear strength, bending strength and compression strength verification are required to ensure that the die can work stably under harsh working conditions.
5) Empty knife structure and die hole size:
The structure of the cantilever support of the die hole working belt outlet needs to be reasonably designed to ensure the quality of the aluminum profile and the life of the die. Different empty knife structures should be used for aluminum profiles with different wall thicknesses.
5.Aluminum extrusion die manufacturing technology
(1) Application of CAD/CAE technology in aluminum extrusion die design
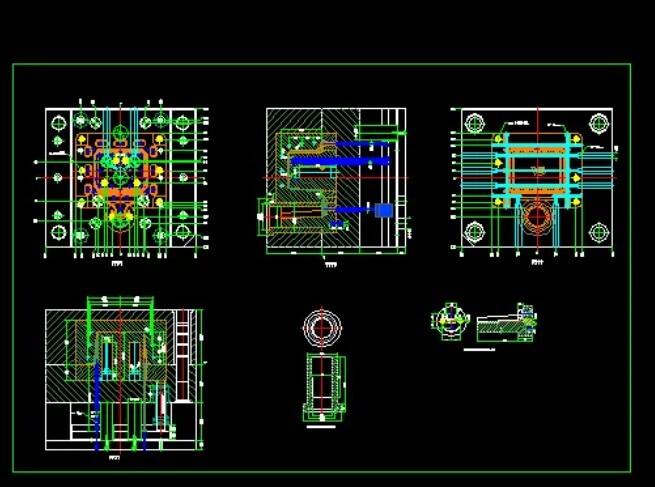
1) 3D modeling and assembly:
Through CAD technology, designers can create a 3D model of the aluminum extrusion die in the computer, perform virtual assembly, check the interference between components, and optimize the die structure.
2) Optimization design:
Combined with CAE technology, finite element analysis is performed on the die to predict the stress and strain distribution of the die during the extrusion process, optimize the shape and size of the die, and improve the service life of the die.
3) Process parameter simulation:
Use CAE software to simulate process parameters such as temperature field and velocity field during the extrusion process to help engineers select appropriate process parameters, reduce the number of mold trials, and reduce production costs.
4) Defect prediction and control:
Through numerical simulation, defects that may occur during the extrusion process, such as cracks and twisting, are predicted, and the design scheme is optimized in advance to improve the product qualification rate.
(2) Processing and manufacturing technology of aluminum extrusion dies
1) Material selection and preliminary processing:
Aluminum extrusion dies are usually made of high-strength and heat-resistant alloy steel. First, the material is cut and blanked according to the design drawings, and then the mold is preliminarily shaped through mechanical processing steps such as rough turning and fine turning.
2) Heat treatment process:
In order to improve the hardness, wear resistance and service life of the mold, heat treatment processes such as quenching and tempering are required. During the treatment process, the heating temperature and insulation time must be strictly controlled to ensure that the mold obtains ideal mechanical properties.
3) Precision machining:
The mold is further precision-machined using high-precision equipment such as CNC machining centers and wire-cut equipment. This stage mainly processes the working belt and cavity of the mold to ensure that its dimensional accuracy and surface roughness meet the requirements.
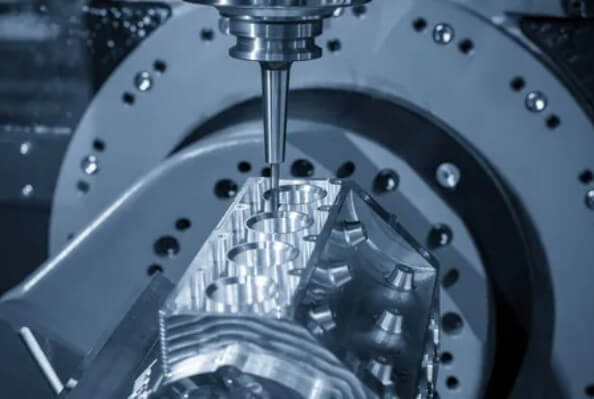
4) EDM and wire cutting:
Through EDM and wire cutting technology, the mold is processed with fine structures such as mold holes and complex contours. These technologies can achieve high-precision processing effects and meet the complex shape requirements of aluminum extrusion dies.
5) Surface treatment:
In order to improve the wear resistance and corrosion resistance of the mold, surface treatment such as nitriding and chrome plating is performed. This step can extend the service life of the mold and ensure the surface quality of the extruded aluminum profile.
6) Quality inspection and mold trial:
Carry out a comprehensive quality inspection on the mold, including size inspection, surface quality inspection and performance inspection. After passing the mold trial, make necessary adjustments and mold repairs according to the mold trial results to ensure that the mold meets production requirements.
6.Summary
Through a comprehensive analysis of the design, manufacturing and application advantages of aluminum extrusion dies, it can be seen that the optimization and innovation of mold design are the key to improving the quality and production efficiency of aluminum profile products. With the continuous advancement of technology, the design and manufacturing of aluminum extrusion dies will become more intelligent and efficient, providing strong support for the development of the aluminum extrusion industry.
What do you think?
[…] and certain mechanical properties. This process is similar to the process of squeezing toothpaste. Aluminum extrusion dies are a common application and are widely used in the manufacture of various aluminum profiles, such […]