Comprehensive Study on Aluminum Casting Deck Frame: Advantages, Design, Manufacturing and Application
Aluminum alloy has been widely used in many industrial fields due to its excellent properties such as light weight, high strength and corrosion resistance.
Among them, the use of aluminum casting deck frames is increasing in structures such as ships, bridges, mechanical equipment, etc. that need to bear large loads. The aluminum casting process can not only optimize the material properties, but also improve the stability and service life of the overall structure.
This paper will conduct an in-depth discussion on the material properties, main advantages, manufacturing process, structural design and application fields of aluminum casting deck frames to fully demonstrate the engineering value of aluminum casting deck frames.
1.Material properties of aluminum casting deck frames
The material selection of aluminum casting deck frames has an important influence on its strength, corrosion resistance, machinability and service life. At present, there are three common types of aluminum alloy materials: 5083, 6061 and 7075. They have their own characteristics and can be used in different application scenarios.
(1) 5083 aluminum alloy
● Mainly used in the shipbuilding industry, due to its excellent corrosion resistance, it is suitable for environments with long-term contact with seawater.
●It has high strength and good weldability, but cannot be further strengthened by heat treatment, and can only rely on cold processing to improve performance.
(2) 6061 aluminum alloy
●It is suitable for structures that require high strength and good processing performance, such as bridges, mechanical equipment, etc.
●It can improve strength through heat treatment, has good corrosion resistance and fatigue resistance, and is suitable for high-strength lightweight structure applications.
(3) 7075 aluminum alloy
●Its strength is close to that of some steels, so it is suitable for high-load-bearing deck frames.
●Due to its relatively weak corrosion resistance, surface treatment (such as anodizing, spraying) is usually required to enhance corrosion resistance.
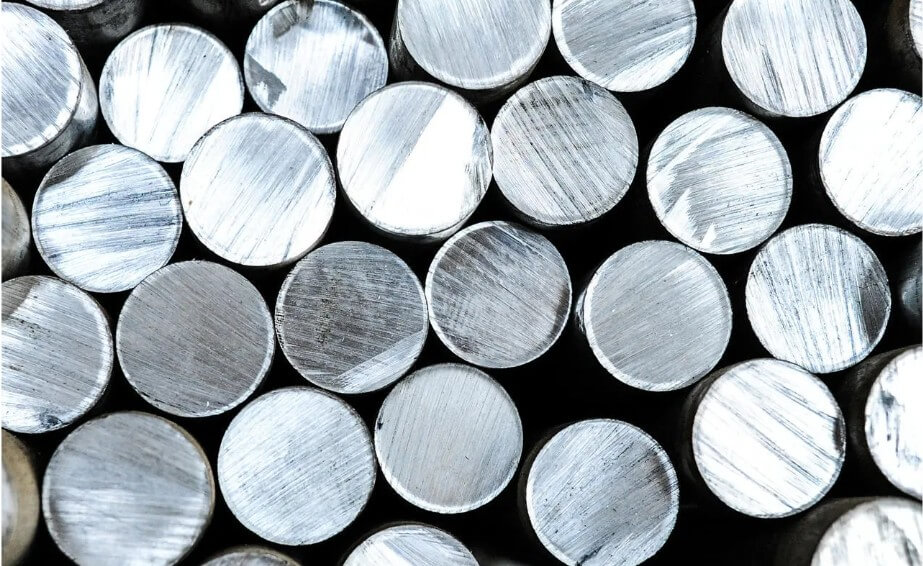
Summary:
The selection of aluminum alloys needs to comprehensively consider the structural load requirements, environmental adaptability, manufacturing process and maintenance requirements to ensure that the cast deck frame has good performance.
2.Main advantages of aluminum casting deck frame
Due to its unique material properties and advanced manufacturing process, aluminum casting deck frame has obvious advantages in many fields:
(1) Lightweight design, improving fuel economy
● The density of aluminum alloy is only 1/3 of that of steel, which can significantly reduce the weight of the structure while ensuring strength.
● In the shipbuilding industry, lighter deck frames can reduce fuel consumption and increase the cargo capacity of ships.
(2) High strength and good fatigue resistance
● Modern aluminum casting technology can optimize structural strength while reducing weight to meet high load requirements.
● Heat-treated aluminum alloy has excellent fatigue resistance and is suitable for deck structures subjected to long-term stress.
(3) Excellent corrosion resistance and reduced maintenance costs
● Deck frames made of 5083 or 6061 aluminum alloy can resist seawater corrosion and do not require frequent coating protection.
● Good corrosion resistance reduces maintenance frequency and cost and increases the service life of the structure.
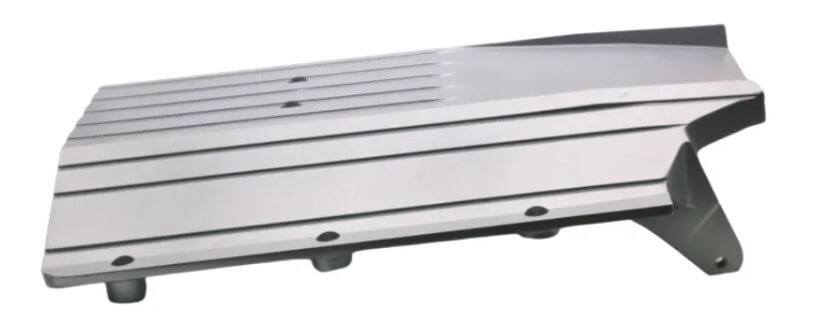
(4) Convenient manufacturing and processing
● Aluminum alloy has good machinability and can realize complex structural design through casting, welding, machining and other methods.
● Modern casting technology enables aluminum alloy frames to be formed in one step, reducing subsequent processing and improving production efficiency.
3.Structural design and optimization of aluminum casting deck frames
(1) Load calculation and force analysis
● In actual use, aluminum casting deck frames need to withstand different types of loads, such as static loads, dynamic loads, impact loads, etc., so detailed force analysis must be performed to ensure their safety.
● Finite element analysis (FEA) is used to simulate stress distribution under different working conditions, identify possible weak points, and optimize the design to improve the reliability of the overall structure.
(2) Lightweight and structural optimization design strategy
● Lightweight design not only helps to reduce material consumption, but also reduces transportation and installation costs. Therefore, it is extremely important in the fields of ships, bridges, mechanical equipment, etc.
● Through topological optimization, redundant materials can be removed while maintaining the necessary strength and stiffness, thereby reducing structural weight and improving load-bearing capacity.
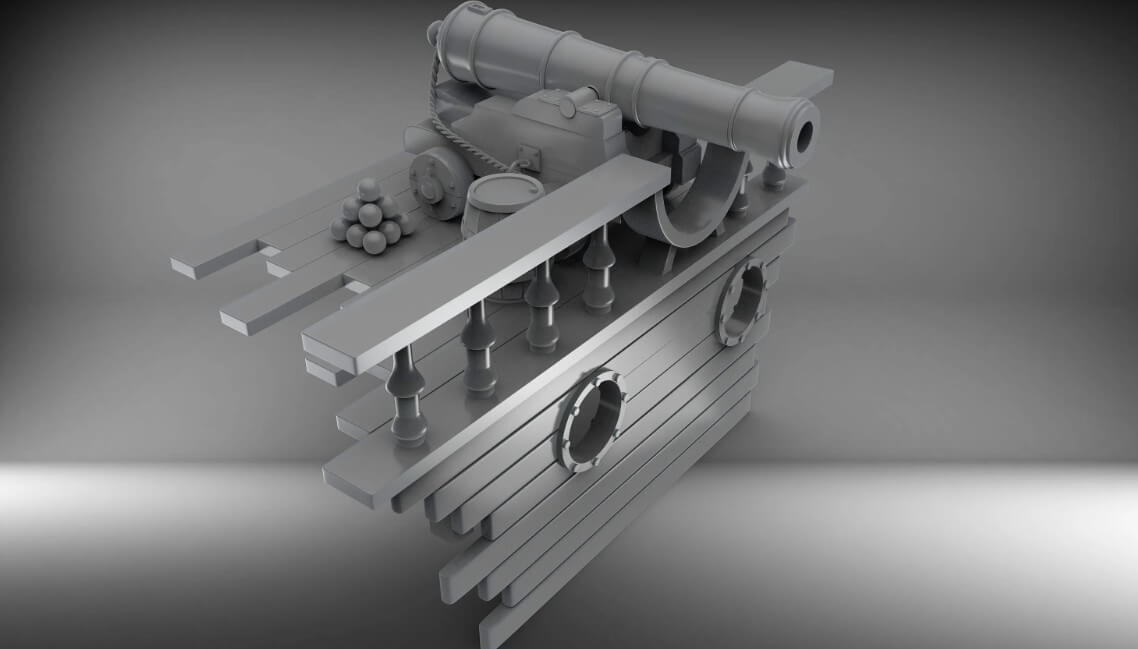
(3) Influence of welding, riveting and bolting methods
● The choice of connection method will affect the overall stiffness, fatigue resistance and maintenance convenience of the aluminum cast deck frame.
● Welding connections provide good sealing, but may cause a decrease in the strength of the local heat-affected zone; riveting and bolting connections It is easier to maintain and disassemble, and is suitable for replaceable structural parts.
(4) Application of computer-aided design (CAD) and simulation (FEA) in optimization
● Modern engineering design widely uses CAD technology for modeling, and combines FEA analysis to optimize the structure.
● By simulating different load conditions, designers can quickly adjust the frame shape and material distribution, thereby reducing test costs and improving design efficiency.
● In addition, the combination of 3D printing and rapid prototyping technology enables the design scheme to be converted into actual products more quickly, providing more optimization possibilities for the casting process.
4.Manufacturing process of aluminum casting deck frame
The choice of casting method directly affects the mechanical properties, structural accuracy and production cost of aluminum casting deck frame. Different casting methods are suitable for different types of deck frames. The process characteristics and applicable scenarios are as follows:
(1) Gravity casting
● This method relies on gravity to naturally flow molten aluminum into the mold. It is suitable for castings with thicker walls and relatively simple shapes, such as the main structure of a large deck frame.
● Due to the slow cooling, the internal structure of the casting is more uniform and has better fatigue resistance, but defects such as shrinkage cavities may occur, so a reasonable design of the shrinkage compensation system is required.
● The production cost of this process is relatively low and it is suitable for medium and low batch production.
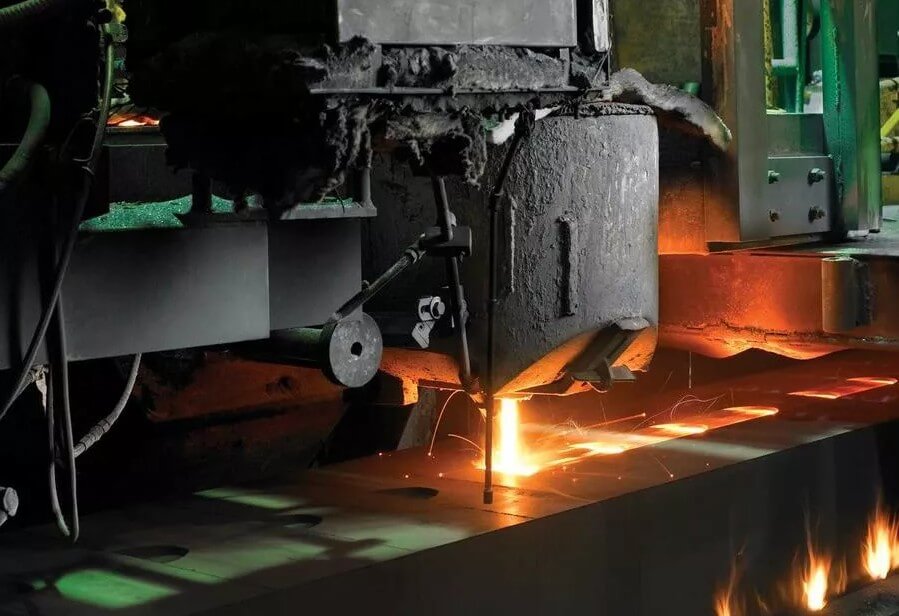
(2) Low-pressure casting
● Low-pressure gas is used to slowly inject aluminum liquid into the mold to form a denser internal structure of the casting, thereby improving strength and durability.
● This method is suitable for small and medium-sized deck frame parts with higher requirements, such as complex support structures or connectors with large loads.
● The molding precision of low-pressure casting The degree of gravity is high and the material utilization rate is high, but the equipment investment is large, which is suitable for mass production.
(3) High-pressure casting
●Through high-pressure rapid filling of the mold, thin-walled and complex-shaped castings can be produced, greatly improving production efficiency.
●This method is suitable for aluminum casting deck frame parts with lightweight and high-precision requirements, such as skeleton structures for high-speed ships or high-end industrial equipment.
●Due to the fast filling speed of aluminum liquid, the casting may have porosity problems, so subsequent heat treatment or machining is usually required to improve performance.
Summary:
In summary, gravity casting is suitable for large-size, low-cost frames, low-pressure casting is suitable for high-strength, dense structure parts, and high-pressure casting can be used for high-precision, lightweight applications. The specific choice needs to be considered comprehensively based on structural requirements, production batch and economy.
5.Common defects and preventive measures in the casting process
During the manufacturing process, aluminum cast deck frames may have defects such as pores, shrinkage cavities, cracks, and inclusions. These defects will affect the mechanical properties and service life of the castings, so reasonable preventive measures need to be taken:
(1) Porosity:
● Air may be drawn into the aluminum liquid during the pouring process, resulting in the formation of pores inside the casting.
● Optimizing the pouring system, controlling the pouring speed, and improving the degassing treatment effect can reduce the formation of pores.
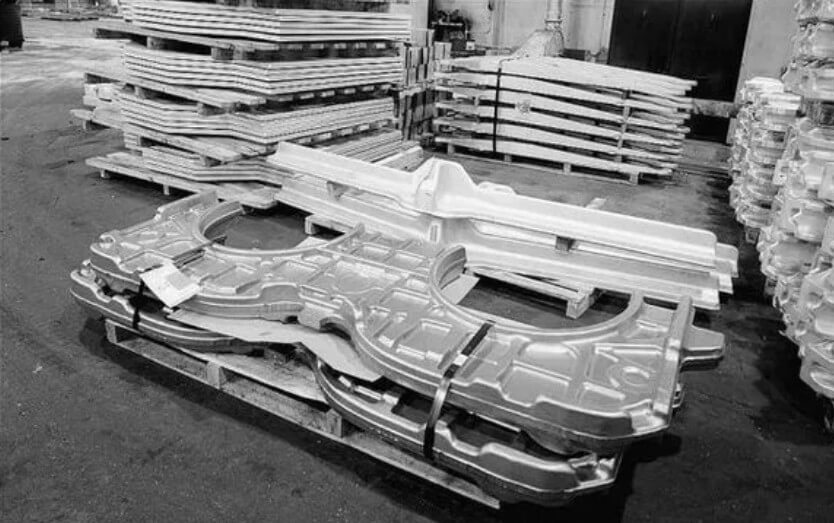
(2) Shrinkage:
● The volume of aluminum liquid shrinks during the cooling process, which may cause local formation of pores in the casting.
● Reasonable design of the shrinkage feeding system, adjustment of the cooling rate, and the use of reasonable risers and chillers can effectively reduce shrinkage defects.
(3) Cracks:
● Thermal stress or uneven cooling may cause cracks in the casting.
● Optimizing the casting temperature, reducing the cooling rate, and using appropriate heat treatment processes can reduce the occurrence of cracks.
(4) Inclusions:
● Oxides or impurities may be mixed into the casting process, affecting the quality of the casting.
● By strictly controlling the melting environment, using refining agents to remove impurities, and optimizing the filtration system, the inclusion content can be effectively reduced and the purity of the casting can be improved.
6.Effect of heat treatment on the mechanical properties of aluminum alloys
Heat treatment can significantly improve the strength, hardness, toughness and corrosion resistance of aluminum alloys, making them more suitable for high-strength load-bearing structures. The effects of different heat treatment methods on the performance of aluminum casting deck frames are as follows:
(1) T6 treatment (solution treatment + aging)
● The alloy elements are evenly distributed through high-temperature solution treatment, and then artificial aging is performed to improve hardness and strength.
● Applicable to 6061 and 7075 aluminum alloys, it can improve tensile strength and yield strength, making the frame more resistant to fatigue and impact.
(2) Annealing treatment
● Mainly used to eliminate residual stress in the casting process, improve the toughness and plasticity of the material, and enhance processing performance.
● Suitable for aluminum alloy frames that require subsequent welding or machining, which can reduce the risk of cracking and deformation.
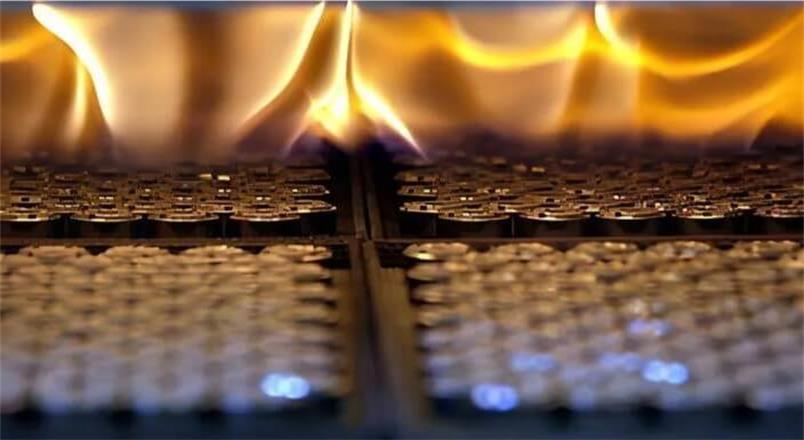
(3) Aging hardening
● Suitable for aluminum alloys that can be strengthened by heat treatment, such as 6061 and 7075, which can improve the fatigue resistance of the material and make the frame more durable.
● Through natural aging or artificial aging, the precipitation phase is evenly distributed, thereby enhancing the overall mechanical properties.
Summary:
By rationally selecting the heat treatment process, the comprehensive performance of the aluminum casting deck frame can be optimized to ensure that it has a good service life and safety under different environmental and load conditions.
7.Application of aluminum casting deck frames
(1) Application in ship structures
● Aluminum casting deck frames are widely used in the deck load-bearing structure and cabin support frame of ships, which can effectively reduce the weight of the hull and improve fuel economy.
● Due to the excellent corrosion resistance of aluminum alloys, these frames are particularly suitable for seawater environments, which can reduce long-term maintenance costs and increase service life.
● Combined with modern welding technology and modular manufacturing processes, aluminum casting deck frames can be assembled more quickly and efficiently, shortening the ship construction cycle.
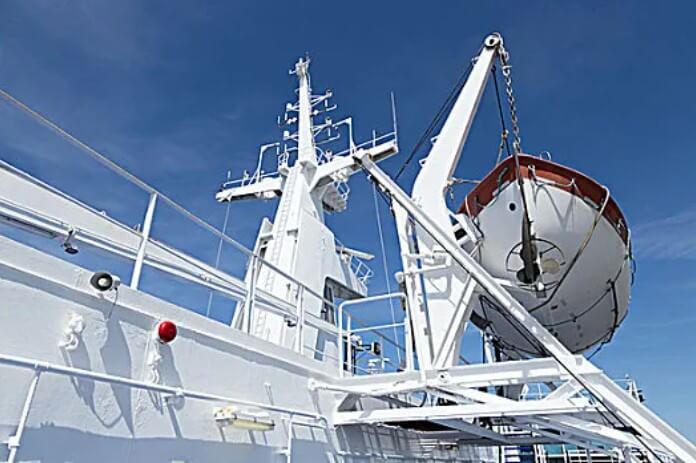
(2) Structural support in bridges and offshore platforms
Aluminum casting deck frames are widely used in structures such as offshore drilling platforms and floating bridges. Their lightweight characteristics help reduce foundation loads and improve overall stability.
In high humidity and high salinity environments, traditional steel structures are susceptible to corrosion, while aluminum alloy frames can maintain a longer service life and reduce maintenance frequency.
(3) Load-bearing frames in industrial equipment and machinery manufacturing
● Many automated production lines and heavy machinery equipment use cast aluminum frames to ensure that the structure is light and strong, and easy to install and adjust.
● Because aluminum alloys are easy to process, more complex and higher-precision load-bearing structures can be manufactured to meet the needs of modern industrial manufacturing.
(4) Applications in other large-scale structural projects
● In the fields of aerospace, rail transportation, etc., aluminum cast deck frames are used to manufacture high-performance support structures, such as aircraft floor frames and high-speed train car frames.
● These frames not only need to withstand high mechanical loads, but also need to have good fatigue resistance to meet the requirements of long-term, high-intensity operation.
8.Summary
In summary, it can be seen that the advantages of aluminum casting deck frames are not only reflected in material properties, but also in their design flexibility and manufacturing efficiency. Through a comprehensive discussion of advantages, design, manufacturing and applications, it can be clearly seen that aluminum casting deck frames are important and practical in modern engineering.