Aluminum based castings in the automotive sector: the best choice for lightweight design and manufacturing
In recent years, the global automotive industry is moving towards lightweight, high efficiency and low emissions.
Under this trend, the application of lightweight and high-strength materials has become the key, and “aluminum based castings in the automotive sector” has gradually become an important choice in automobile manufacturing due to its advantages such as high strength, low density and strong corrosion resistance.
At present, aluminum alloy materials have been widely used in key components such as automobile engines, chassis, and bodies. Compared with traditional steel materials, aluminum alloys can achieve a weight reduction of more than 30% while ensuring safety and reliability. Therefore, in-depth research on the material optimization, manufacturing process and performance optimization of “aluminum based castings in the automotive sector” is of great significance to promoting the development of the automotive industry.
1.Overview of aluminum based castings in the automotive sector
(1) The meaning of aluminum-based
“Aluminum-based” refers to a matrix material with aluminum (Al) as the main element.
In castings in the automotive field, aluminum-based materials usually refer to aluminum alloys, that is, other alloying elements (such as silicon, copper, magnesium, zinc, etc.) are added to pure aluminum to improve its performance.
Aluminum-based materials can also include aluminum-based composite materials, that is, adding reinforcing phases (such as carbon fiber, ceramic particles, etc.) to the aluminum alloy matrix to further improve strength, wear resistance and other properties.
(2) The difference between aluminum alloy and aluminum-based
Aluminum alloy is a type of aluminum-based material, which is an alloy composed of aluminum and other metal elements.
The scope of aluminum-based is wider. In addition to aluminum alloys, it also includes other materials with aluminum as the matrix, such as aluminum-based composite materials.
(3) Characteristics of aluminum based castings in the automotive sector
In the automotive field, aluminum-based castings usually use aluminum alloys because aluminum alloys have the following advantages:
1) Lightweight: Aluminum alloys have low density, which can significantly reduce the weight of the car, reduce fuel consumption and emissions.
2) Good casting performance: Aluminum alloys have good fluidity and are suitable for manufacturing castings with complex shapes.
3) Good mechanical properties: By adjusting the alloy composition and heat treatment process, high-strength and high-toughness castings can be obtained.
4) Corrosion resistance: A dense oxide film will form on the surface of aluminum alloys, which has good corrosion resistance.
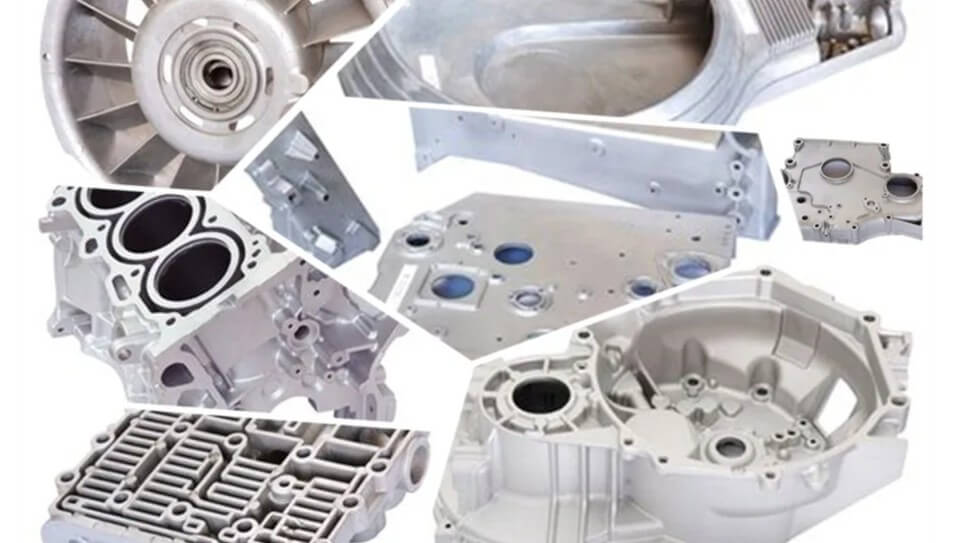
(4) Commonly used aluminum alloys in the automotive field
The following aluminum alloys are commonly used in aluminum based castings in the automotive sector:
1) Aluminum-silicon alloys (such as A356, A380): have good casting properties and mechanical properties, and are commonly used in engine blocks, gearbox housings, etc.
2) Aluminum-magnesium alloys: have high strength and corrosion resistance, and are commonly used in body structural parts.
3) Aluminum-copper alloys: have high strength and heat resistance, and are commonly used in high-temperature parts.
(5) Application of aluminum-based composite materials
In some high-performance automotive parts, aluminum-based composite materials may be used, for example:
1) Aluminum-based silicon carbide composite materials: used to manufacture high-performance brake discs, engine pistons, etc.
2) Aluminum-based carbon fiber composite materials: used to manufacture lightweight body structural parts.
2.Main application scenarios of aluminum based castings in the automotive sector
“Aluminum based castings in the automotive sector” are widely used in the following key components:
(1) Power system components
1) Engine block: Aluminum alloy materials are lighter and dissipate heat faster.
2) Engine cylinder head: reduce weight and improve heat resistance.
3) Piston: reduce inertia and improve fuel efficiency.
4) Intake manifold: optimize airflow and improve power performance.
5) Turbocharger housing: resist high temperature and high pressure and improve supercharging efficiency.
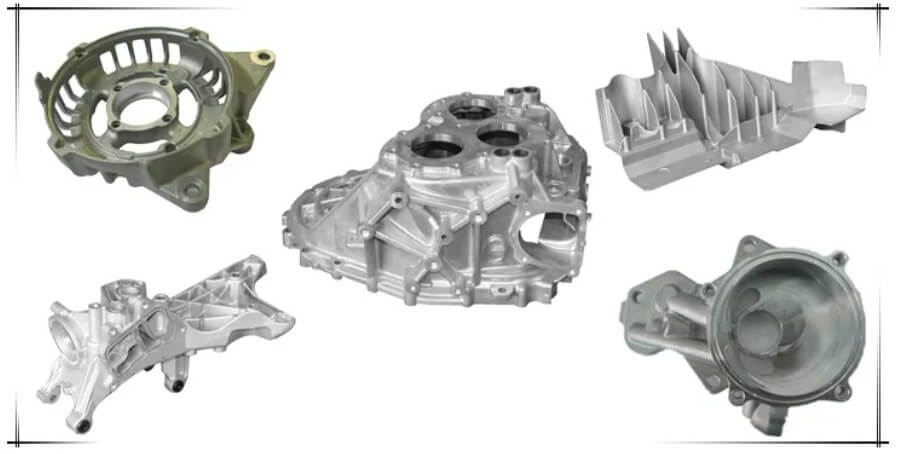
(2) Chassis and suspension system
1) Subframe: reduce weight and improve handling.
2) Control arm: enhance durability and optimize suspension response.
3) Steering knuckle: reduce unsprung mass and improve stability.
4) Wheel hub: lighter and more corrosion-resistant, improve fuel economy.
5) Anti-roll bar: optimize bending stiffness and improve handling performance.
(3) Body structure
1) Front and rear anti-collision beams: lightweight and improve collision energy absorption capacity.
2) Door internal support: enhance side impact safety.
3) A/B/C pillar reinforcement: improve body rigidity and safety.
4) Engine hood: reduce weight and reduce pedestrian collision damage.
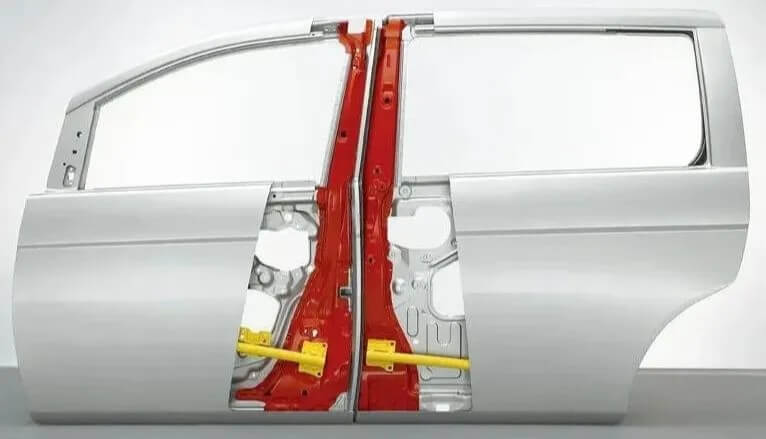
(4) Special parts for electric vehicles
1) Battery housing: light and corrosion-resistant, improve heat dissipation.
2) Motor housing: high thermal conductivity, protect the motor.
3) Inverter housing: fast heat dissipation, improve system stability.
(5) Gearbox and transmission system
1) Gearbox housing: lightweight, improve heat dissipation.
2) Differential housing: reduce weight and improve stability.
3) Clutch housing: high temperature resistance, improve power transmission efficiency.
3.Overview of aluminum based casting manufacturing process in the automotive field
“Aluminum based castings in the automotive sector” mainly adopt the following advanced manufacturing processes to meet the requirements of strength, precision and durability in different application scenarios.
(1) High-pressure casting
1) Process characteristics:
The aluminum alloy melt is pressed into the metal mold with high pressure and high speed, and quickly cooled and formed.
Suitable for mass production of thin-walled complex parts, such as gearbox housings, engine cylinders, etc.
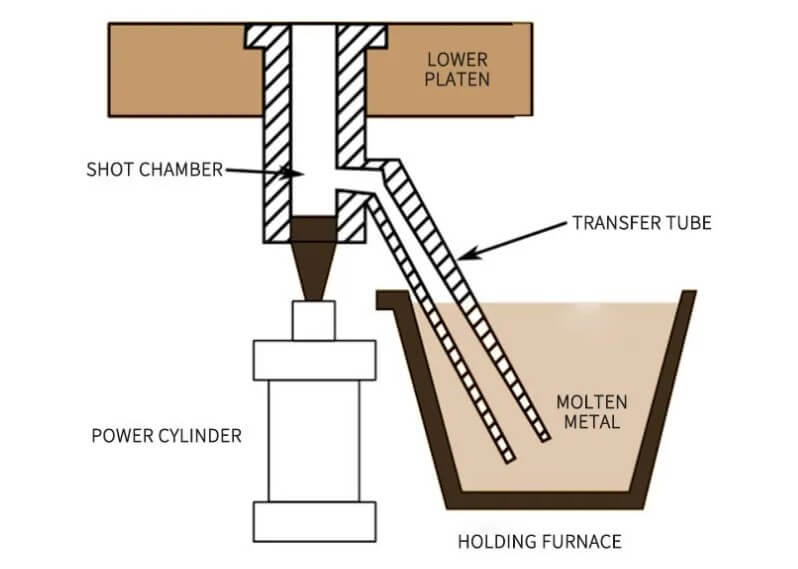
2) Advantages:
High production efficiency, automation and precision control can be achieved.
Good surface quality of castings and high dimensional accuracy.
3) Disadvantages:
Porosity, shrinkage and other defects are prone to occur, affecting mechanical properties.
Due to the fast cooling rate, the alloy structure is coarse, resulting in low ductility.
(2) Low-pressure casting
1) Process characteristics:
The molten aluminum liquid is slowly injected into the mold cavity through low pressure to reduce turbulence and improve the quality of castings.
Suitable for manufacturing high-strength and high-density parts, such as wheels, suspension system components, etc.
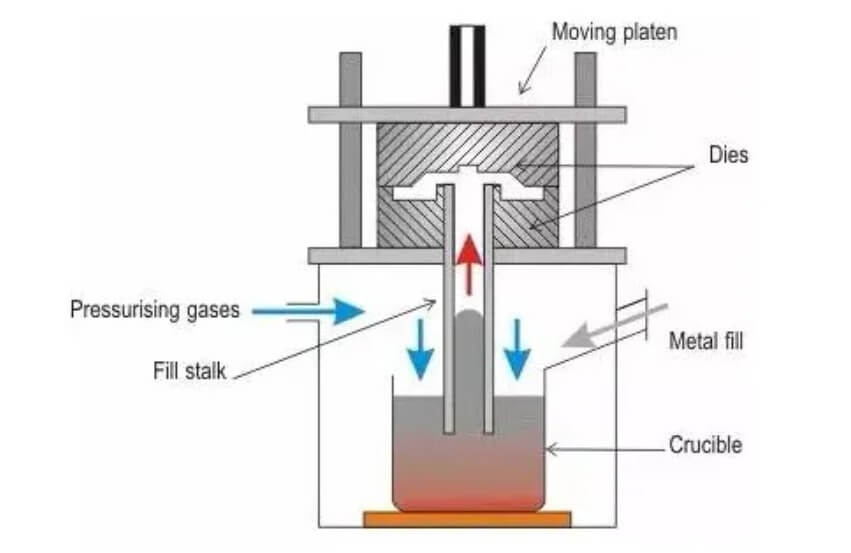
2) Advantages:
Low porosity and high material strength.
Suitable for medium-volume production with high yield rate.
3) Disadvantages:
The production efficiency is lower than that of high-pressure casting, and it is not suitable for ultra-large-scale production.
High requirements for molds and relatively high costs.
(3) Gravity casting
1) Process characteristics:
Relying on gravity to naturally fill the mold, suitable for large-volume, thick-walled structural parts, such as engine blocks and cylinder heads.

2) Advantages:
Dense structure, high strength, and excellent wear resistance.
Suitable for parts under high temperature conditions, such as engine components.
3) Disadvantages:
Low production efficiency, not suitable for large-scale automated production.
The mold service life is relatively short and requires regular maintenance.
(4) Precision casting
1) Process characteristics:
Adopting investment casting technology, complex-shaped parts can be manufactured, suitable for high-end automotive parts, such as turbocharger housings.
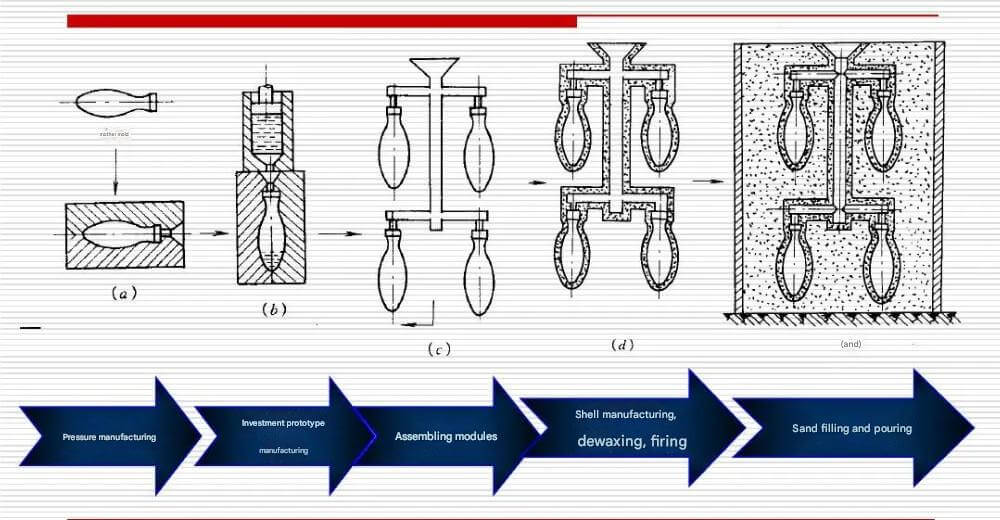
2) Advantages:
High precision, can produce complex-shaped parts.
Excellent mechanical properties, suitable for aluminum-based castings in the high-demand automotive field.
3) Disadvantages:
High production cost and long cycle.
Not suitable for mass production.
4.Structural optimization design of aluminum based castings in the automotive sector
In order to improve the performance of “aluminum based castings in the automotive sector”, structural optimization design is crucial, which is mainly reflected in the following aspects:
(1) Lightweight optimization
1) Topological optimization:
Use CAE (computer-aided engineering) technology to analyze the stress conditions, remove excess materials, and reduce weight to the greatest extent while ensuring strength.
2) Wall thickness optimization:
Reduce unnecessary thick parts and improve material utilization, such as optimizing the wall thickness design of engine cylinder block and suspension control arm.
3) Integrated design:
By reducing the number of parts, multiple functional components are integrated into one, such as the integration of battery housing and structural parts, to improve overall strength and reduce weight.
(2) Heat dissipation performance optimization
1) Increase heat dissipation rib design:
Optimize the distribution of heat dissipation ribs on components such as battery housing and engine cylinder head to improve heat dissipation efficiency.
2) Optimize material thermal conductivity:
Use high thermal conductivity aluminum alloy to improve heat transfer efficiency and prevent local overheating, such as applied to motor housing and inverter housing.
3) Hollow design:
For non-stressed areas, hollow structures are used to improve air flow and promote heat dissipation, such as the ventilation hole design of brake discs.
(3) Strength and durability optimization
1) Strengthen key stress areas:
Add ribs in high stress areas (such as steering knuckles and subframe connections) to improve fatigue resistance.
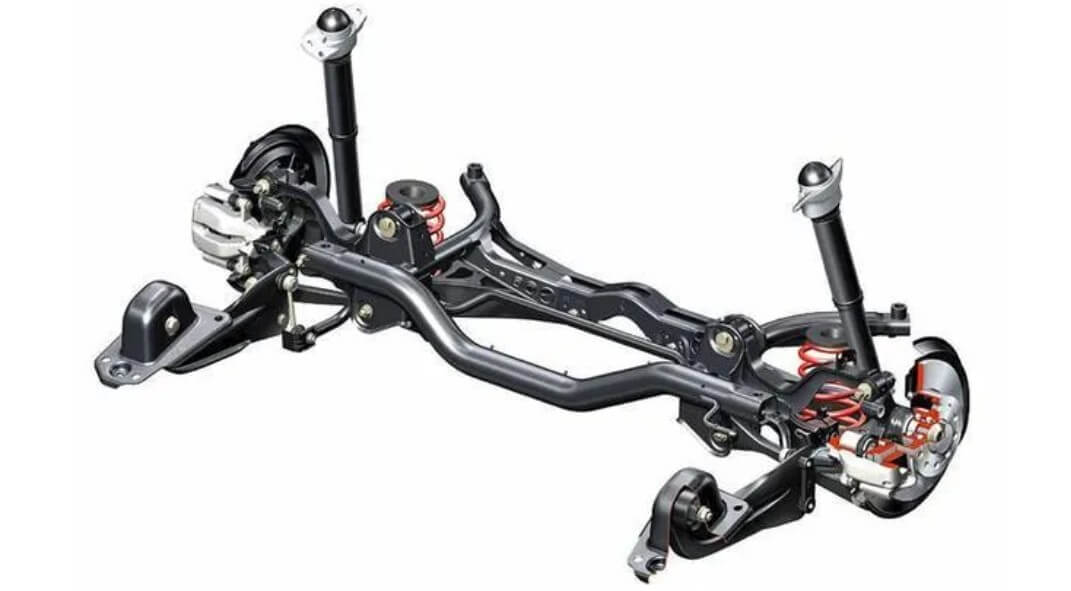
2) Material microstructure optimization:
Through heat treatment and alloy element adjustment, durability is improved and the risk of fracture is reduced.
3) Optimize welding and connection methods:
Use stir friction welding, bolt connection and other methods to improve structural strength and reduce stress concentration.
5.Manufacturing process control of aluminum based castings in the automotive sector
In order to ensure the product quality of “aluminum based castings in the automotive sector”, manufacturing process control is particularly critical, mainly including the following aspects:
(1) Dimensional accuracy control
1) Optimize casting parameters:
Precisely control the pouring temperature and pressure, reduce cold shrinkage and deformation, and improve dimensional stability.
2) Improve mold accuracy:
Use high-precision CNC processing molds to ensure the dimensional consistency of castings.
3) Automated testing:
Use three-dimensional coordinate measuring machine (CMM) for quality inspection to improve product qualification rate.
(2) Surface quality optimization
1) Deburring and polishing:
Use mechanical or chemical deburring process to improve surface finish and reduce stress concentration.
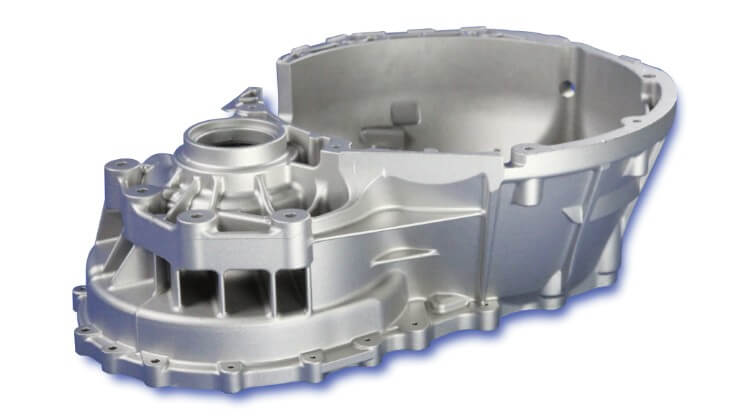
2) Sandblasting and shot peening:
Enhance surface hardness and increase fatigue life. Widely used in parts such as wheels and gearbox housings.
3) Anti-corrosion coating:
Add oxidation or coating treatment to body structural parts and chassis parts to improve corrosion resistance.
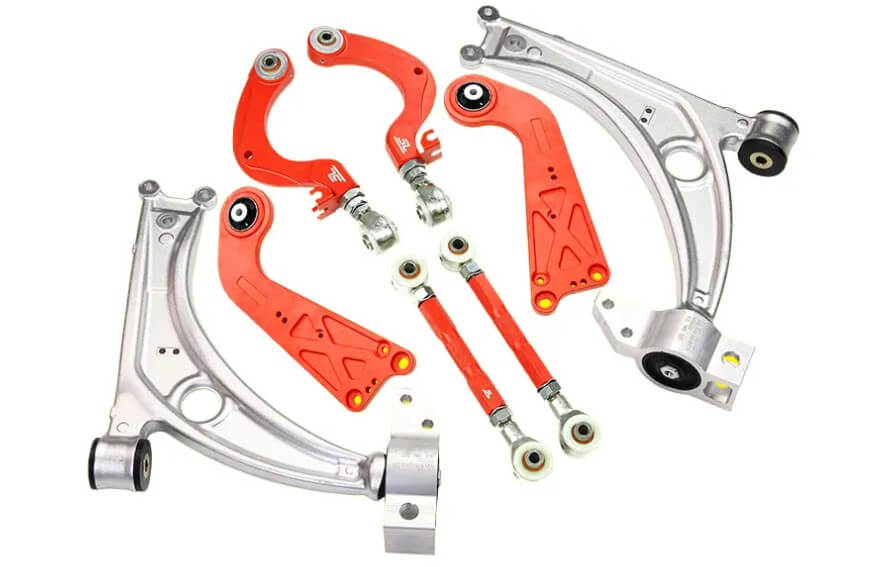
(3) Internal defect control
1) Vacuum casting technology:
Reduce pores and increase casting density. Suitable for parts with high strength requirements.
2) X-ray detection:
Used to check internal shrinkage holes and cracks to improve product reliability.
3) Friction stir welding (FSW):
Used for aluminum alloy welding, reducing pores and improving connection strength.
6.Summary
Aluminum based castings in the automotive sector play an irreplaceable role in automobile lightweighting. With the optimization of materials, continuous progress in manufacturing processes and in-depth development of structural optimization design, aluminum alloy castings will play a more important role in the future automotive industry.