Aluminum alloy casting: categories, advantages and disadvantages, applications
Aluminum alloy casting is a metal forming technology widely used in modern industry, and is favored for its light weight, high strength and good corrosion resistance. With the development of China’s manufacturing industry, the demand for aluminum alloys and aluminum alloy castings is increasing, which will also drive the development of the aluminum alloy casting industry.
This article will first take you to understand the following concepts and working principles of casting, and then deeply analyze the aluminum alloy casting process, advantages and disadvantages of aluminum alloy casting, and the application fields of aluminum alloy casting.
1.What is casting?
Casting is a technology that pours, cools, and solidifies liquid metal into parts of the desired shape, and is widely used in the manufacture of various metal products. The casting process involves multiple key steps, from the structure and properties of liquid metal to the laws of crystallization and solidification, to the working principles of different casting methods, each step plays a decisive role in the quality of the final casting.
2.Aluminum alloy casting process
Currently, aluminum alloy casting processes are roughly divided into two types: gravity casting and pressure casting.
Pressure casting is divided into high-pressure casting and low-pressure casting
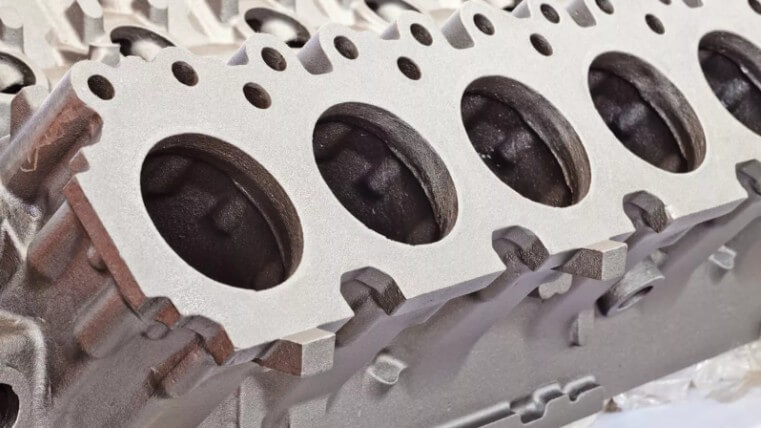
(1) Gravity casting
1) The concept of gravity casting
Gravity casting refers to the process of injecting aluminum liquid into a mold by gravity under the action of the earth’s gravity. In a broad sense, gravity casting is divided into: sand casting, metal mold (steel mold) casting, lost foam casting, etc.; in a narrow sense, gravity casting refers specifically to metal mold casting.
2) The characteristics of aluminum alloy gravity castings are:
①. The surface finish of the product is not high, and pits are easily generated after shot blasting.
②. There are few pores inside the aluminum casting, and heat treatment can be performed.
③. The product has low density and slightly poor strength, but high elongation.
④. The mold cost is low and the mold service life is long.
⑤. The production efficiency is low, which increases the production cost.
⑥. The process is relatively simple and is not suitable for the production of thin-walled parts.
⑦. Low-fluidity special aluminum alloys can be used.
3) What products can choose gravity casting?
The casting process to be selected for product processing is mainly based on the wall thickness of the workpiece. When the wall thickness of the product is greater than 8mm, die casting will cause many pores to exist in the wall. Therefore, products with thicker walls can be completed by gravity casting.
(2) High-pressure casting
1) Concept of high-pressure casting
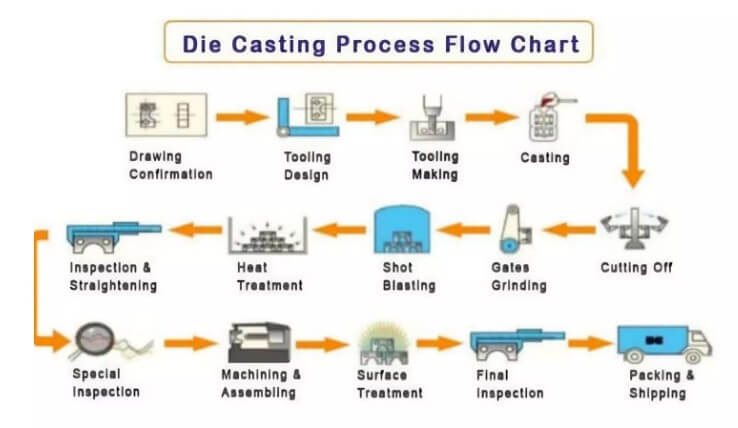
High-pressure casting is what we usually call die casting. The aluminum liquid is poured into the pressure chamber, and the pressure fills the mold cavity at a high speed, and the aluminum liquid solidifies under pressure to form an aluminum casting.
2) Characteristics of aluminum alloy high-pressure castings are:
①. The surface finish of the product is good, generally up to Ra6.3 or even Ra1.6.
②. Usually not heat-treatable.
③. The product has high air tightness, high casting strength and surface hardness, but low elongation, and excessive wall thickness is prone to pores.
④. The mold cost is high and the service life is short.
⑤. High production efficiency.
⑥. Thin-walled parts can be produced with small processing allowance.
⑦. Special aluminum alloys cannot be used.
(3) Low-pressure casting
1) Working principle of low-pressure casting
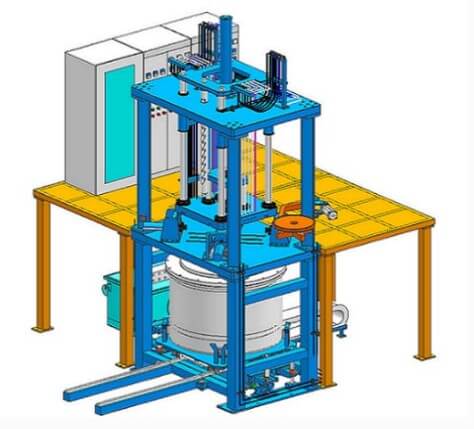
Dry compressed air is introduced into a sealed crucible (or sealed tank). Under the action of gas pressure, the molten metal rises along the riser into the straight runner and smoothly enters the mold cavity through the inner runner, and maintains the gas pressure on the liquid surface in the crucible. Until the casting is completely solidified. Then the gas pressure on the liquid surface is released, so that the unsolidified molten metal in the riser flows back to the crucible. The mold is opened again and the aluminum alloy casting parts are taken out.
2) Characteristics of aluminum alloy low-pressure castings are:
①. The surface of the product is stronger than that of the die casting and stronger than that of the gravity casting.
②. There are few pores inside the aluminum casting and heat treatment can be performed.
③. The product has high air tightness, and the strength and surface hardness of the casting are higher than those of the die casting, but the elongation is lower than that of the gravity casting.
④. The mold cost is low and the service life is low.
⑤. The production efficiency is lower than that of the gravity casting and much lower than that of the die casting.
⑥. The process is complex and is used to produce high-requirement, high-quality castings.
⑦. Low-fluidity special aluminum alloys can be used.
3.Advantages and disadvantages of aluminum alloy casting
The advantages of aluminum alloy casting are mainly reflected in the following aspects:
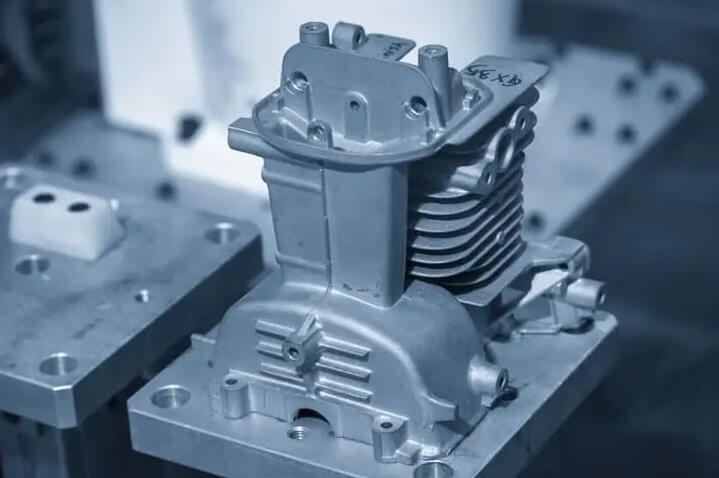
(1) Lightweight and high strength:
The density of aluminum alloy is low, about 2.7g/cm³, which makes the casting light and has high strength and hardness. This feature makes it widely used in aerospace, automobile manufacturing and other fields, which can effectively reduce product weight and improve fuel efficiency.
(2) Good corrosion resistance:
Aluminum alloys show excellent corrosion resistance in atmospheric and seawater environments, reducing maintenance costs and extending the service life of products.
(3) Good forming performance:
Aluminum alloys have good plasticity and fluidity, and can produce complex-shaped casting blanks through casting processes, which improves production efficiency and reduces machining production costs.
(4) High production efficiency:
The aluminum alloy casting process is simple and has high production efficiency. For example, pressure casting equipment can quickly produce a large number of castings and is suitable for large-scale production.
(5) High material utilization:
The waste generated during the aluminum alloy casting process is small, and the material utilization rate is high. At the same time, the casting has precise dimensions and good surface finish, which reduces the workload of subsequent machining.
The shortcomings of aluminum alloy casting are mainly reflected in the following aspects:
(1) Oxidation slag:
During the casting process, aluminum alloy is prone to produce oxidation slag, which affects the quality and performance of the casting.
(2) Porosity and shrinkage:
Aluminum alloy liquid is prone to form pores and shrinkage during the solidification process, resulting in defects inside the casting, affecting its strength and durability.
(3) Cracks:
During the cooling process, aluminum alloy castings are prone to cracks due to stress concentration, especially for castings with complex shapes.
(4) Cost issues:
Although the raw materials and equipment costs of aluminum alloy casting are relatively low, some high-performance aluminum alloy materials and advanced casting equipment are relatively expensive, which increases the production cost.
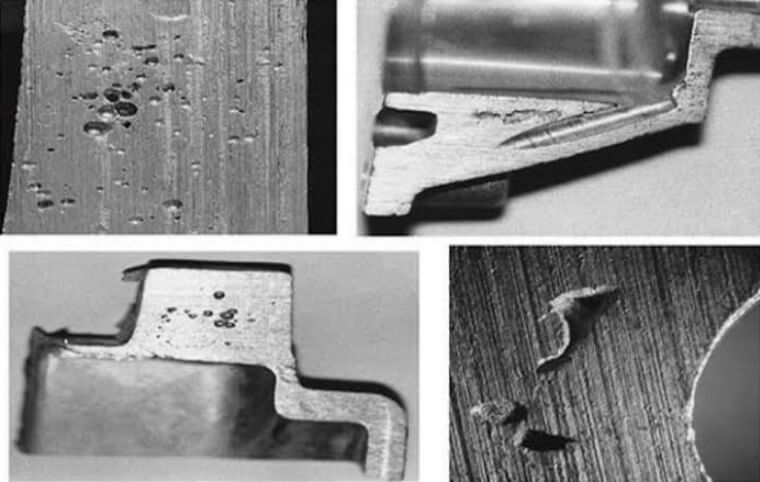
Therefore, aluminum alloy casting has significant advantages such as light weight, high strength, corrosion resistance, and high production efficiency, but it also has defects such as oxidation slag, pores, cracks, and cost issues. In practical applications, it is necessary to weigh the advantages and disadvantages according to specific needs, and take corresponding measures to reduce the impact of defects.
4.Application fields of aluminum alloy casting
Aluminum alloy casting is an important metal processing technology, which is widely used in various industrial fields. The following are several common aluminum alloy application fields:
(1) Aerospace field:
Aluminum alloy castings are used to manufacture aircraft beams, turbine blades, pump bodies, pylons, hubs, intake lips and engine casings, etc. Its light weight and high strength greatly improve the performance of aircraft.
(2) Automobile industry:
Aluminum alloy castings are used in automobile manufacturing to produce cylinder heads, gearboxes, pistons, hubs and steering booster housings, etc., which not only reduces the weight of the vehicle, but also improves fuel efficiency.
(3) Mechanical engineering field:
Aluminum alloys are often used to manufacture high temperature and corrosion resistant mechanical parts, such as petrochemical equipment, automotive parts and heat treatment equipment, etc., to maintain stable performance and long service life in harsh working environments.
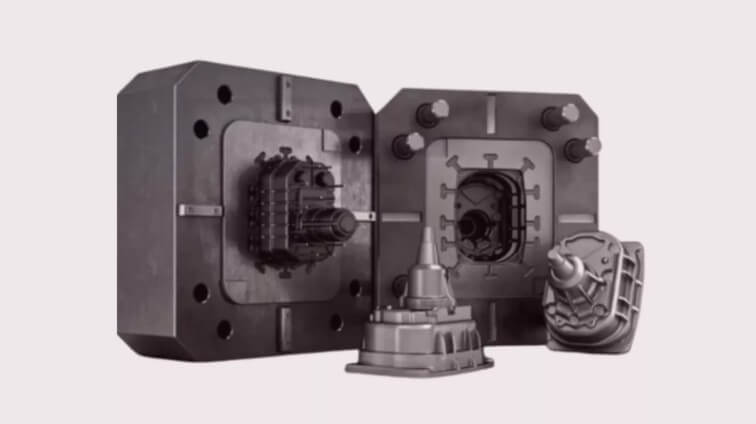
5.Summary
In short, aluminum alloy casting parts, with their unique advantages, occupy an important position in modern industry. With the continuous advancement of science and technology, the aluminum alloy casting process will be further improved, and its application field will be further expanded, injecting new vitality into the development of various industries.