Aluminium die casting components: detailed explanation of manufacturing process and technological innovation
Aluminium die casting components have a wide range of applications, covering multiple industries such as automobiles, electronics, aerospace, and machinery.
The reason why aluminium die casting components are widely used is mainly due to two reasons: First, the advantages of die-casting technology can produce complex parts with high precision and high efficiency to meet the needs of mass production;
Second, aluminum alloys are lightweight, corrosion-resistant and have good mechanical properties, which are suitable for industries such as automobiles and aviation that require high strength and durability. These advantages make aluminium die casting components an ideal choice for many industries.
This article will discuss in detail the application, manufacturing process, and key technological innovation of aluminium die casting components to provide information for people in related industries.
1.Classification and application of aluminium die casting components
(1) Automobile industry
● Engine block, gearbox housing:
Aluminum die-casting technology can provide high-strength and lightweight solutions to meet the needs of automobile power systems.
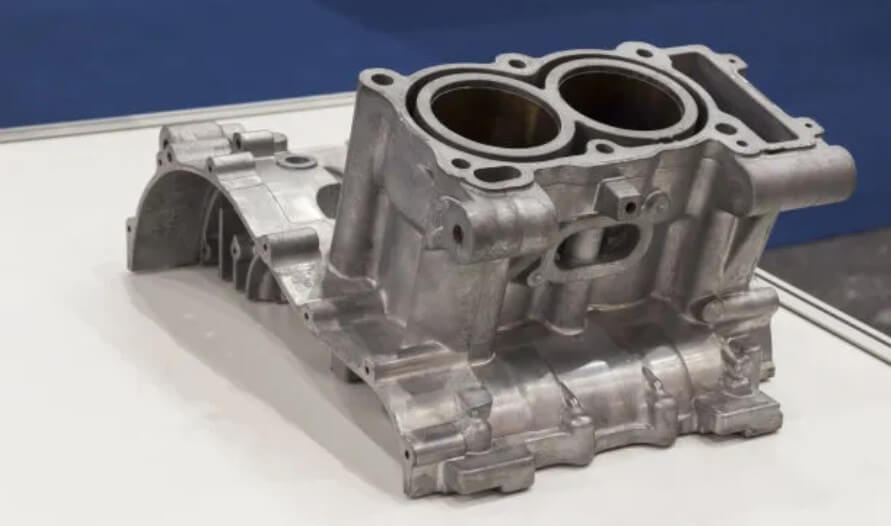
● Wheel hub, suspension bracket:
Aluminium die casting components are widely used in automobile chassis systems, improving vehicle handling and fuel economy.
● Body structural parts (integrated die-casting technology, such as Giga Casting):
Integrated die-casting technology improves production efficiency and reduces body weight by reducing the number of parts.
(2) Electronics industry
● Radiators, mobile phone cases, 5G base station heat dissipation components:
Aluminum die-casting components play an important role in electronic equipment. Their high thermal conductivity and lightweight characteristics meet the needs of the electronics industry.
(3) Aerospace
● Lightweight structural parts, high-strength brackets:
The application of aluminum die-casting technology in the aerospace field has significantly reduced the weight of aircraft and improved fuel efficiency and flight performance.
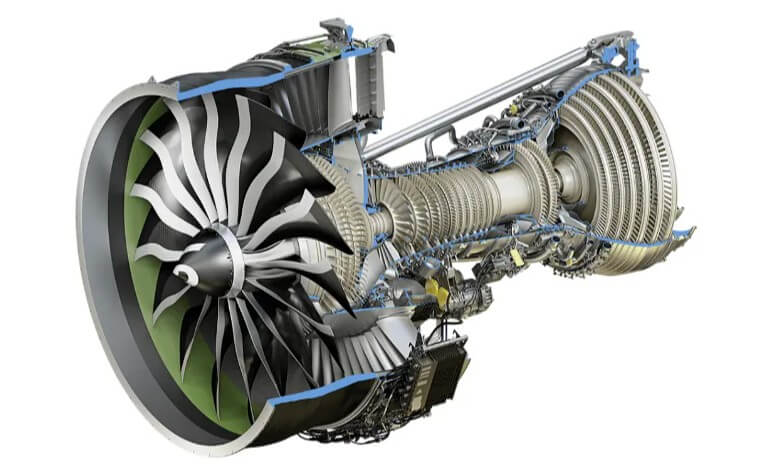
(4) General machinery and tools
● Power tool housings, industrial pump housings, valve bodies:
Aluminum die-casting components are widely used in the general machinery and tool industry, providing high strength and corrosion resistance.
2.Detailed explanation of the manufacturing process of aluminium die casting components
(1) Mold design and manufacturing
1) Mold flow analysis:
By simulating the flow of molten metal in the mold, the mold design is optimized and defects are reduced.
2) 3D printing-assisted design:
3D printing technology shortens the mold development cycle and improves design flexibility.
3) Cooling system:
Optimize the layout of cooling water channels, improve cooling efficiency, and prevent deformation.
(2) Alloy smelting and refining
1) Alloy selection:
Select suitable aluminum alloy materials according to the application scenario to meet different performance requirements.
2) Smelting process:
Control the temperature at 650-720℃ to ensure uniform melting of the alloy.
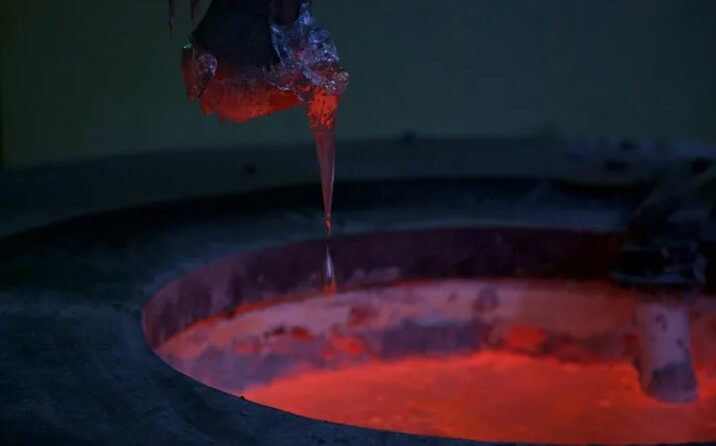
3) Refining treatment:
Use degassing and slag removal technology to improve the purity of the alloy and reduce inclusions.
(3) Die casting (detailed analysis and process control points)
1) Mold closing:
● The two halves of the mold (fixed mold and movable mold) are closed under the action of the die casting machine to form a closed cavity.
● During the mold closing process, it is necessary to ensure the accuracy and sealing of the mold to avoid metal leakage or flash.
2) Injection:
● Molten metal is rapidly injected into the mold cavity under high pressure through the injection system of the die casting machine (including the injection cylinder and the injection punch).
● The injection speed and time need to be precisely controlled to ensure that the metal can fully fill every corner of the cavity while avoiding turbulence and air entrainment.
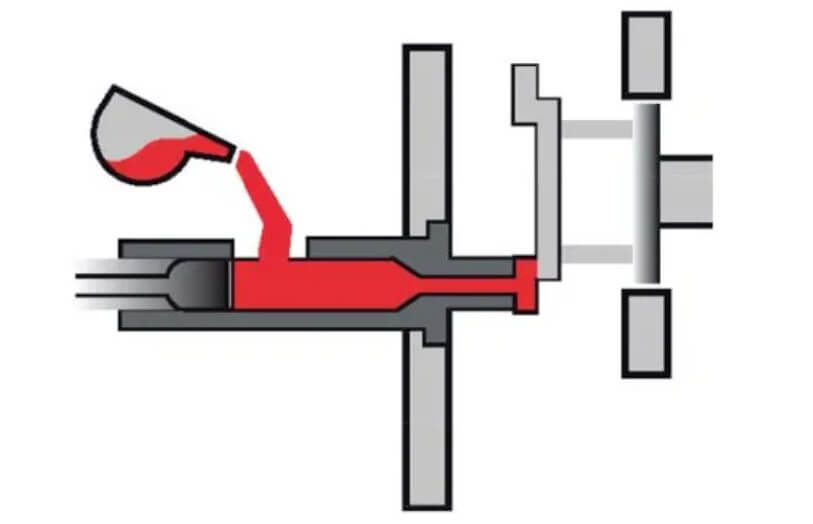
3) Holding pressure:
● After the metal fills the cavity, the die casting machine continues to maintain a certain pressure (holding pressure stage) to ensure that the metal can fully compensate for shrinkage during the cooling process and reduce shrinkage and shrinkage defects.
● Holding pressure time and pressure need to be optimized according to the product shape and material properties.
(4) Cooling and mold opening
1) Cooling:
● The metal cools rapidly in the mold to form a solid part. The cooling time depends on the thickness of the product and the design of the mold cooling system.
● During the cooling process, it is necessary to ensure that the metal cools evenly to avoid deformation and internal stress concentration.
2) Mold opening:
● After cooling is completed, the two halves of the mold are opened by the die casting machine.
● The ejector mechanism (such as ejector pin or ejector plate) pushes the molded part out of the mold to complete demolding.
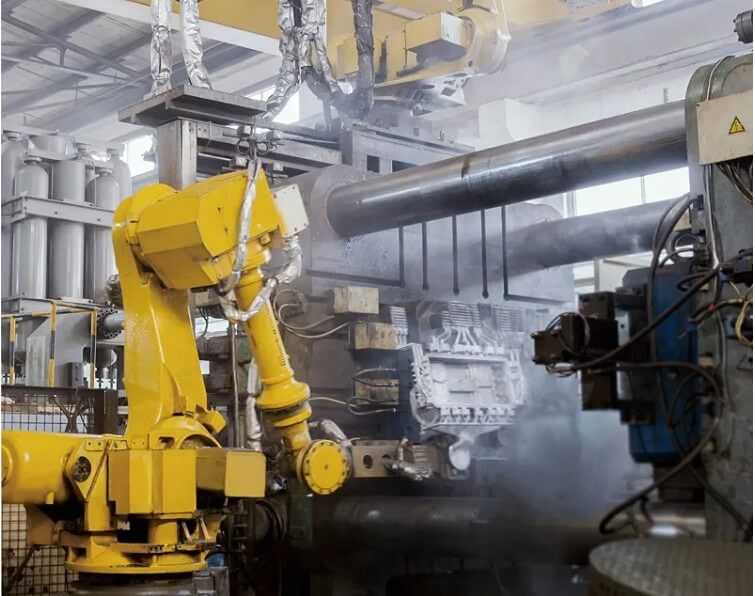
(5) Post-processing and finishing
1) Deburring and polishing:
Remove burrs and improve surface finish.
2) Machining:
CNC machining improves dimensional accuracy and meets assembly requirements.
3) Surface treatment:
Anodizing, electroplating, etc., to improve corrosion resistance.
3.Key parameters of die casting
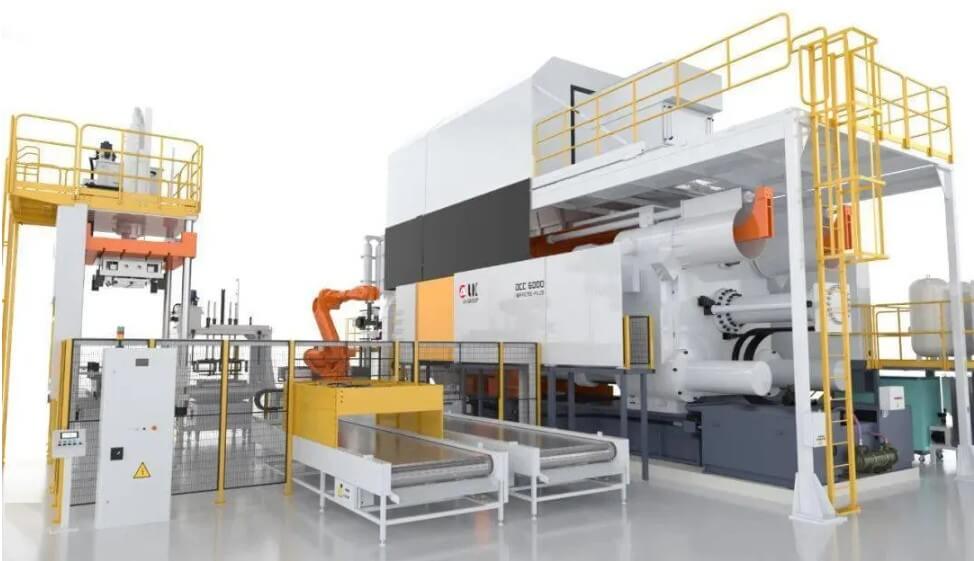
(1) Injection pressure:
Usually 100-150 MPa to ensure that the metal fills the cavity quickly.
(2) Injection speed:
High-speed injection can reduce the metal solidification time, but too high a speed may cause turbulence and air entrainment.
(3) Mold temperature:
The mold temperature needs to be controlled within an appropriate range (usually 150-250℃) to ensure metal fluidity and cooling efficiency.
(4) Cooling time:
Determined according to product thickness and material properties, usually between a few seconds and tens of seconds.
4.Advantages and challenges of die casting
(1) Advantages:
● High production efficiency, suitable for mass production.
● Aluminium die casting components have high dimensional accuracy and good surface quality.
● Ability to produce parts with complex shapes.
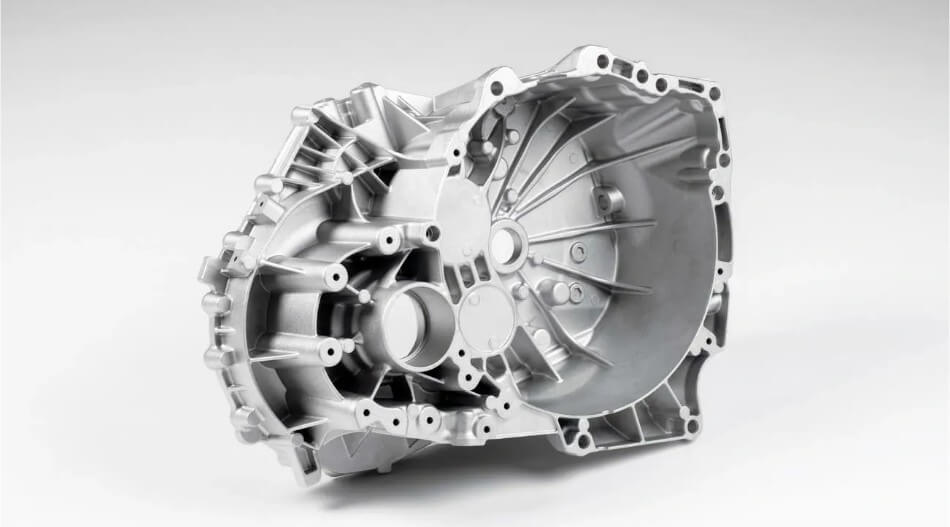
(2) Challenges:
● Internal defects such as pores and shrinkage cavities are prone to occur.
● High mold cost and long development cycle.
● High requirements for control of process parameters.
5.Key technological innovations in manufacturing aluminium die casting components
(1) Comparison between high pressure die casting (HPDC) and low pressure die casting (LPDC)
Suitable for mass production, can provide high precision and high strength.
● Low pressure die casting:
Suitable for parts with complex shapes, can reduce pores and defects.
(2) Application of vacuum die casting technology
● Reducing pores:
Reduce pores through vacuum environment and improve product strength.
● Improve strength:
Vacuum die-casting technology is particularly suitable for parts with extremely high strength requirements.
(3) Application of 3D printing in mold manufacturing
● Shorten the development cycle:
3D printing technology can quickly manufacture complex molds and shorten the development cycle.
● Improve design flexibility:
3D printing technology provides higher flexibility for mold design.
(4) Application of CNC machining technology
CNC machining technology plays an important role in the post-processing of aluminium die casting components, especially in the manufacture of high-precision parts.
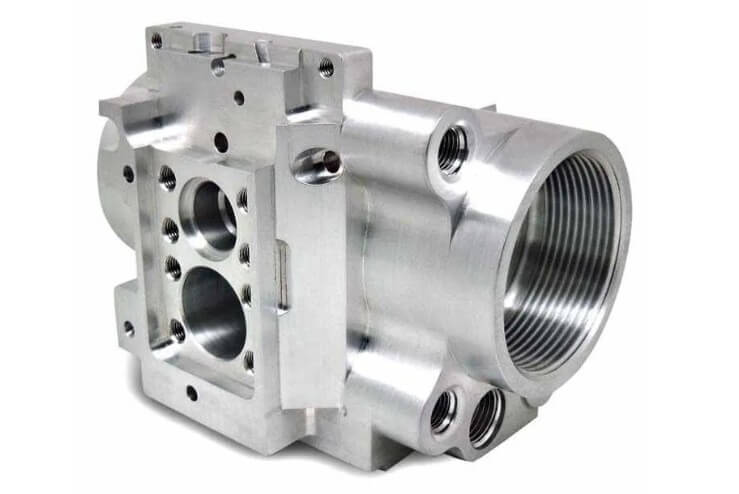
● Improve dimensional accuracy:
CNC machining can perform precision machining on parts after die-casting to ensure that their dimensional accuracy meets design requirements.
● Complex shape machining:
CNC technology can process parts with complex shapes to meet diverse product requirements.
● Improve surface quality:
Through CNC machining, the surface finish and consistency of the parts can be further improved.
● Automation integration:
CNC machining equipment can be seamlessly integrated with automated production lines to achieve full process automation from die-casting to machining and improve production efficiency.
(5) Intelligent manufacturing and automation
● Robotic picking:
Automated production lines improve production efficiency and reduce manual intervention.
● Intelligent monitoring:
Ensure product quality by real-time monitoring of key parameters in the production process.
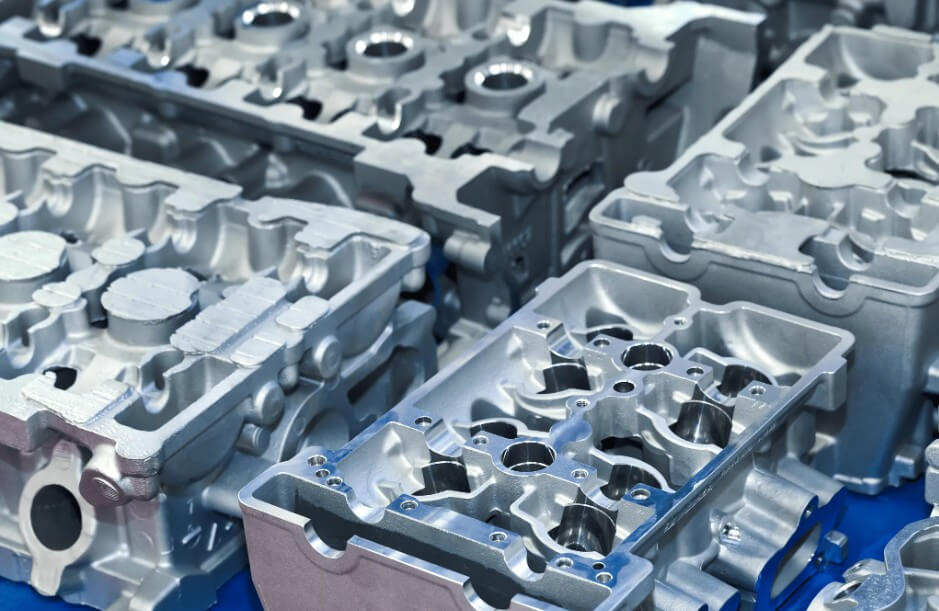
5.Quality control and inspection technology for aluminium die casting components
(1) Common defects and solutions
● Porosity, cold shut, shrinkage, inclusions:
These defects can be effectively reduced by optimizing mold design and improving smelting and casting processes.
(2) Quality inspection methods
● X-ray inspection: Detect pores and inclusions inside the product.
● CT scanning: Provide three-dimensional images to comprehensively inspect the internal structure of the product.
● Ultrasonic inspection: Detect defects and cracks inside the product.
(3) Surface treatment and corrosion resistance improvement
● Spraying, electrophoresis, anodizing:
Improve the corrosion resistance and appearance quality of the product and extend the service life of the product.
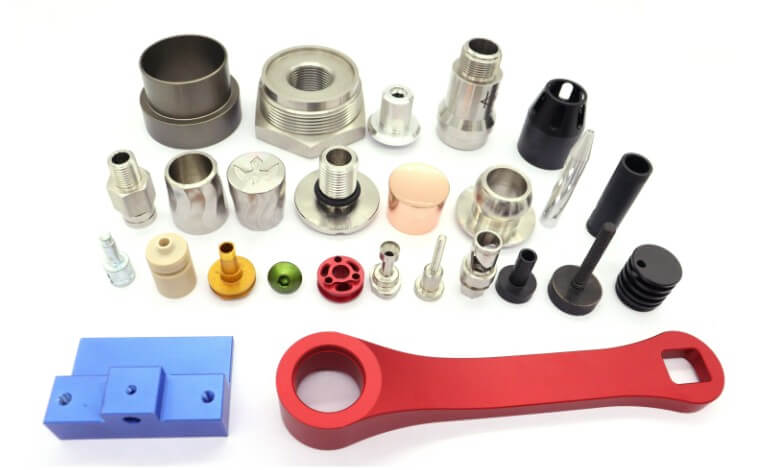
6.The market demand for aluminium die casting components will continue to grow
(1) The growing demand for aluminium die casting components in electric vehicles
● Battery housing, lightweight body structure:
With the rapid development of the electric vehicle market, the demand for aluminium die casting components continues to grow.
(2) Lightweight trend
● The demand for lightweight materials in the automotive industry and aerospace drives the development of aluminum die-casting technology.
(3) The rise of integrated die-casting technology
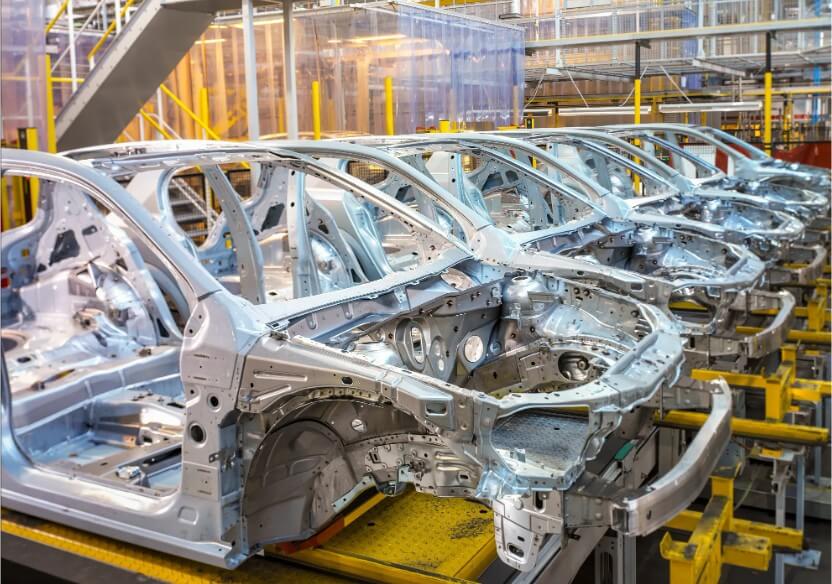
● Reducing the number of parts:
Integrated die-casting technology improves production efficiency by reducing the number of parts.
● Improving production efficiency:
Integrated die-casting technology is particularly suitable for large-scale production.
(4) Application of high-performance aluminum alloys
New aluminum alloys with higher temperature resistance and fatigue resistance will promote the development of aluminium die casting components in machinery, oil and gas (such as the demand for high-performance parts in the oil and gas industry), aerospace and other fields, such as the widespread application of Al-Cu-Mg alloys.
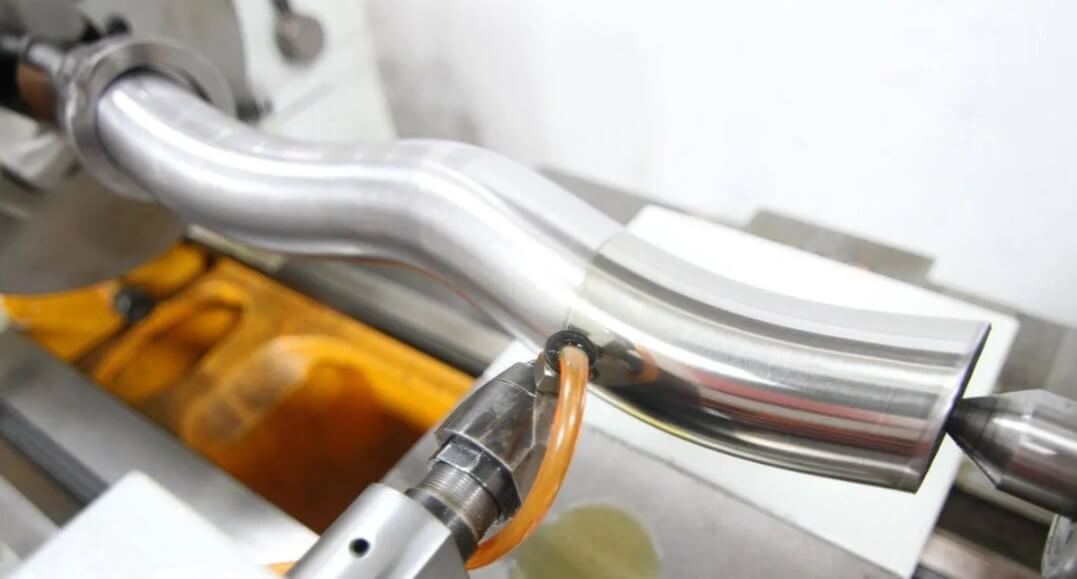
7.Summary
The importance of aluminium die casting components in various industries is self-evident, and the advancement of its manufacturing technology has promoted the continuous improvement of product performance. In the future, with the rapid development of the electric vehicle market, the demand for lightweight materials in the automotive industry and aerospace, the rise of integrated die-casting technology and the application of high-performance aluminum alloys, the aluminum die-casting industry will usher in a broader development prospect.
What do you think?
[…] Good surface quality of castings and high dimensional accuracy. […]
[…] precision casting technology, such as investment casting, gravity casting, low-pressure casting, die casting (widely used in aluminum metal materials), etc., to ensure the high quality and complex shape of the […]