Aerospace castings: How to meet their high demands?
Aerospace castings are essential components in the modern aviation and aerospace industries. They are made through casting processes and can meet high performance requirements in extreme environments. This article will explore the importance of aerospace castings, how to meet their high requirements, and important content related to future development trends.
1.Importance of aerospace castings
Aerospace castings play a vital role in the modern aviation and aerospace industries. Their importance is mainly reflected in the following aspects:
(1) Improving performance and reliability:
Precision casting technology can produce parts with complex shapes, ensure the accuracy and stability of parts, and thus improve the overall performance of aerospace vehicles.
(2) Meeting special requirements:
The aerospace field has extremely high quality requirements for castings, including high strength and corrosion resistance of materials, as well as the ability to work under extreme conditions such as high temperature and high pressure.
(3) Manufacturing of key components:
Precision castings play a key role in aerospace vehicles, such as engine impellers. The performance and reliability of these components are crucial to the working effect of aerospace vehicles.
(4) Reduce costs and improve efficiency:
Precision casting technology can reduce material waste and processing steps, reduce manufacturing costs, and improve production efficiency.
(5) Material innovation and progress:
With the increasing demand for high-performance materials, such as titanium alloys and high-temperature alloys, casting technology is also constantly improving to meet the aerospace industry’s higher requirements for material strength, fatigue life and corrosion resistance.
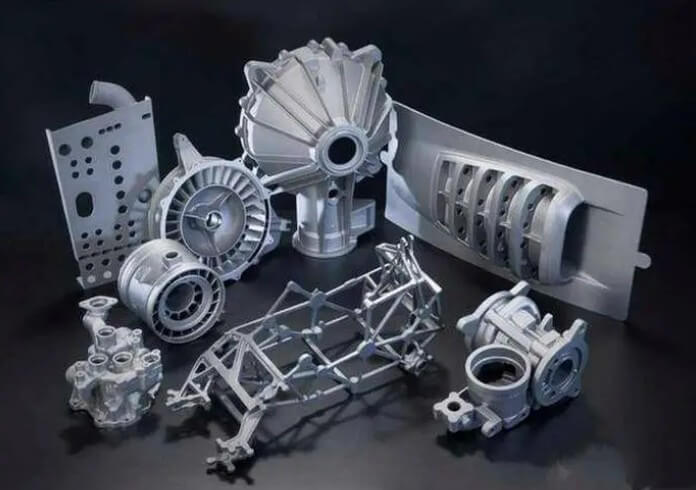
2.How to meet the high requirements of aerospace castings
The aerospace industry is one of the important symbols of modern science and technology. It has extremely high requirements for castings, mainly reflected in material properties, dimensional accuracy and surface quality. These requirements are not only to ensure the safety and reliability of aircraft, but also because the working environment of aerospace vehicles is extremely harsh and needs to withstand extreme temperatures, pressures and vibrations. Therefore, meeting these high requirements is a key challenge in the manufacture of aerospace castings.
(1) Material selection
Aerospace castings usually use high-performance alloy materials, such as titanium alloys, aluminum alloys and high-temperature alloys, and composite materials. These materials have the characteristics of high strength, low density, high temperature resistance and corrosion resistance, and can meet the requirements of use in extreme environments. For example:
1) Aluminum alloy: It has the characteristics of light weight and high strength, and is widely used in the manufacture of aircraft fuselages and wings and other structural parts.
2) Titanium alloy: It has excellent strength and corrosion resistance, and is suitable for the manufacture of engine parts and landing gear.
3) High-temperature alloy: It can maintain excellent performance in high temperature environment, and is mainly used to manufacture high-temperature engine parts.
4) Composite materials: It combines the advantages of multiple materials, has higher strength and light weight, and is gradually being used in the aerospace field.
(2) Precision casting technology
In order to meet the high-precision requirements of aerospace castings, advanced casting technology must be adopted. Precision casting technologies, such as investment casting and directional solidification technology, can achieve near-net shape, reduce subsequent processing, and improve material utilization. Investment casting can produce castings with high dimensional accuracy and smooth surface through steps such as wax mold making, shell mold preparation and high-temperature pouring. Directional solidification technology obtains castings with excellent mechanical properties by controlling the solidification process.
(3) Accuracy and roughness requirements
The dimensional accuracy of aerospace castings usually needs to reach CT5 level, that is, the tolerance level is very strict to ensure the accuracy and interchangeability of parts during assembly.
The surface roughness requirement of aerospace castings is usually below 2μm to ensure the smoothness of the part surface and reduce friction, which is crucial to improving the aerodynamic performance of the aircraft.
(4) Quality control and testing
Quality control and testing are key links in ensuring the quality of aerospace castings. During the casting process, it is necessary to strictly monitor the raw materials, smelting process, casting parameters, etc. to ensure that each link meets the standards. In addition, non-destructive testing technologies such as X-ray testing, ultrasonic testing and magnetic particle testing are also required to conduct comprehensive inspections of castings to ensure that there are no defects inside and on the surface.
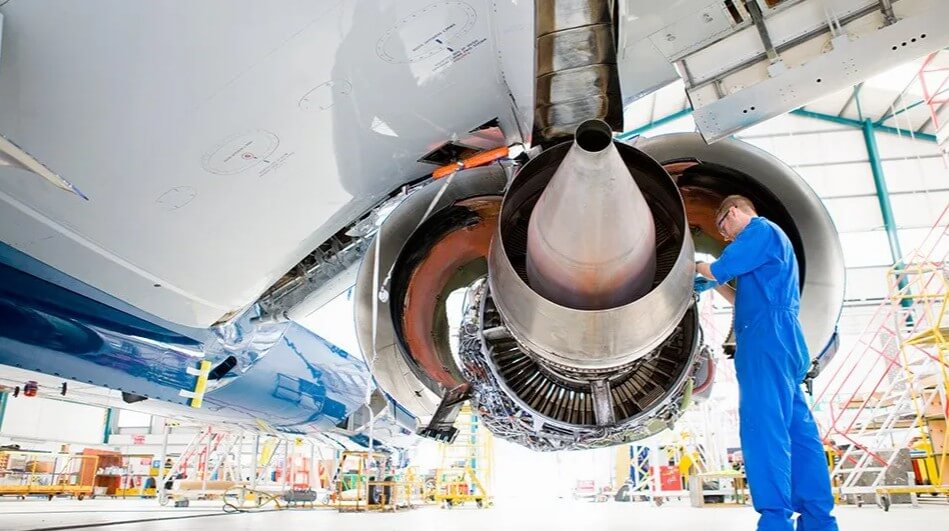
(5) Post-processing process
Post-processing process also plays an important role in improving the performance and reliability of aerospace castings. Heat treatment processes such as solution treatment, aging treatment and annealing treatment can improve the microstructure of castings and improve their mechanical properties and corrosion resistance. In addition, surface treatment technologies, such as shot peening and coating, can further improve the surface quality and fatigue resistance of castings.
(6) Digital and intelligent manufacturing
With the development of digital and intelligent manufacturing technologies, the manufacturing process of aerospace castings is also constantly transforming towards intelligence. By applying technologies such as computer-aided design (CAD), computer-aided manufacturing (CAM) and computer-aided engineering (CAE), the casting process can be optimized and simulated, the trial and error cost can be reduced, and production efficiency can be improved. At the same time, by applying technologies such as sensors, big data and artificial intelligence, real-time monitoring and intelligent control of the casting process can be achieved, further improving the quality and consistency of castings.
Summary:
Meeting the high requirements of aerospace castings is a systematic project, which requires comprehensive consideration and continuous optimization from multiple aspects such as material selection, casting technology, precision control, quality control, post-processing technology and intelligent manufacturing. Only by continuously improving the technical level and management level can high-quality and high-performance aerospace castings be produced.
3.Application of aerospace castings
(1) Aircraft engine:
The aircraft engine is the “heart” of the aerospace vehicle, and its performance is directly related to the performance and safety of the aircraft. It is widely used in aircraft engines, such as blades, turbine discs, casings and other key components.
(2) Aircraft structural parts:
Aircraft structural parts have an important impact on the safety, reliability and economy of aircraft. Its application in aircraft structural parts mainly includes landing gear, fuselage frame, engine hanger, etc.
(3) Spacecraft structural parts:
Spacecraft structural parts need to withstand extreme temperature and pressure changes. Its application in spacecraft structural parts mainly includes rocket engine casing, satellite structural parts, etc.
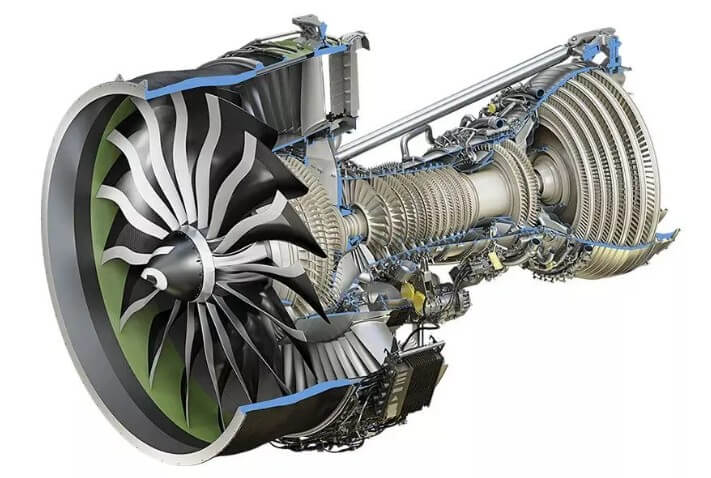
4.Future development trend of aerospace castings
(1) The market size will continue to grow
According to market research reports, the global aerospace aluminum casting market size will be approximately US$6.2 billion in 2022 and is expected to be close to US$10.3 billion by 2029. With the gradual recovery of the global economy and the increase in people’s demand for air travel, the production of aircraft will increase significantly, thereby driving the growth of the aerospace casting market.
(2) Technological innovation promotes material and process upgrades
Technological innovation is the core driving force for the development of aerospace castings. In order to meet the needs of aircraft and spacecraft for lightweight, high strength and high temperature resistance, the application of new materials and advanced manufacturing processes will become more extensive.
For example, the research and development and application of lightweight and high-strength materials such as aluminum alloys, titanium alloys and composite materials will effectively reduce the weight of aircraft and improve fuel efficiency.
In addition, the application of additive manufacturing (3D printing) technology will make the manufacturing of castings with complex structures more convenient and efficient, and further promote the development of aerospace castings towards lightweight, integrated and high performance.
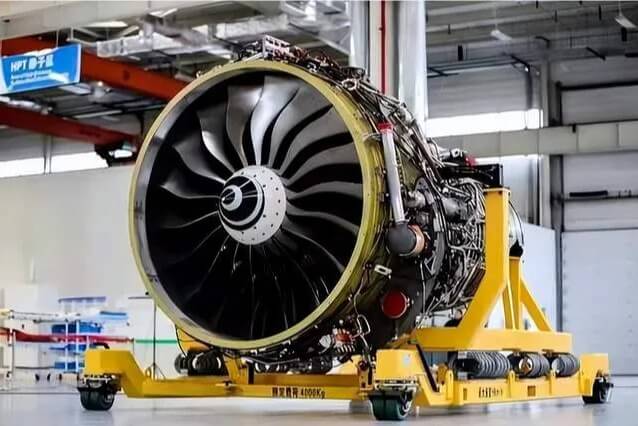
(3) The demand for customized and high-reliability fasteners will continue to grow.
The design and manufacturing of aerospace vehicles have special and high-precision requirements for fasteners, which often need to be tailor-made. With the advancement of technology and the increasing complexity of aerospace vehicles, customized demand will provide a larger market space. The research and development of high-reliability fasteners will also be an important direction in the future. These fasteners need to have high strength, high temperature resistance, vibration resistance and other characteristics to ensure the stability and safety of aerospace equipment.
(4) The importance of coordinated development of the industrial chain is increasing.
The development of the casting industry not only depends on the technological innovation and capacity improvement of a single enterprise, but also requires the coordinated cooperation of upstream and downstream of the industrial chain. From raw material supply to product design, manufacturing and after-sales service, the effective connection and cooperation of each link will greatly improve the operating efficiency and market competitiveness of the entire industry.
(5) Environmental protection and sustainability become important issues
With the increasing global attention to environmental protection and sustainable development, the foundry industry will also pay more attention to green manufacturing and environmental protection technology. For example, by optimizing production processes, reducing energy consumption and waste emissions, and improving the recycling rate of materials. In addition, the use of environmentally friendly materials and reducing carbon emissions in the production process will also become an important development direction for enterprises.
5.Summary
In summary, the aerospace casting industry will usher in a broader development space in the future,
so it is particularly important to continuously improve its technological development level to adapt to market demand.