Discussion on the types, design and processing technology optimization of machined components for chemical equipment
In the modern chemical industry, the precision, corrosion resistance and mechanical properties of machined components for chemical equipment directly affect the stability and safety of the production process. Chemical equipment usually needs to withstand high temperature, high pressure and strong corrosive environment, so its machined parts must have excellent durability and processing accuracy.
This article will conduct an in-depth analysis of the types, design principles, material selection and processing technology of machined components for chemical equipment, and explore how to optimize CNC machining technology to improve production efficiency and part quality.
1.Types of machined components for chemical equipment
There are many types of common machined parts in chemical equipment, mainly including:
(1) Pump body parts:
Such as pump housing, rotor, shaft, etc., usually used for liquid or gas transportation.
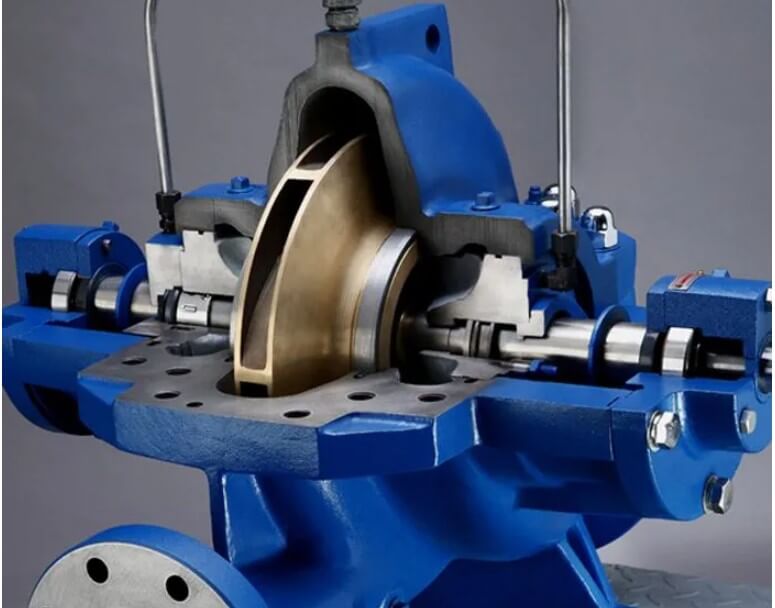
(2) Valve parts:
Such as valve body, valve cover, valve stem, valve seat, etc., commonly used in devices that control the flow of media.
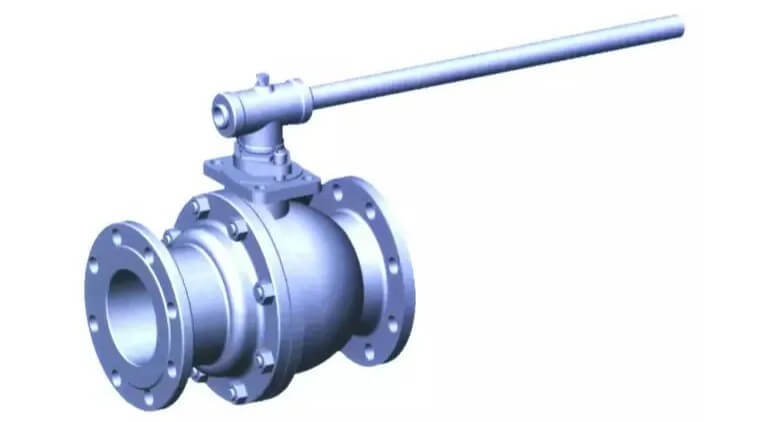
(3) Pressure vessel parts:
Such as tank body, heater, cooler, liner, etc., mainly used in high pressure environment.
(4) Heat exchanger parts:
Such as heat exchange tubes and shells, which are mainly used for heat exchange between fluids.
(5) Pipe fittings:
Such as pipe flanges, joints, tees, etc., which are used to connect and distribute fluids.
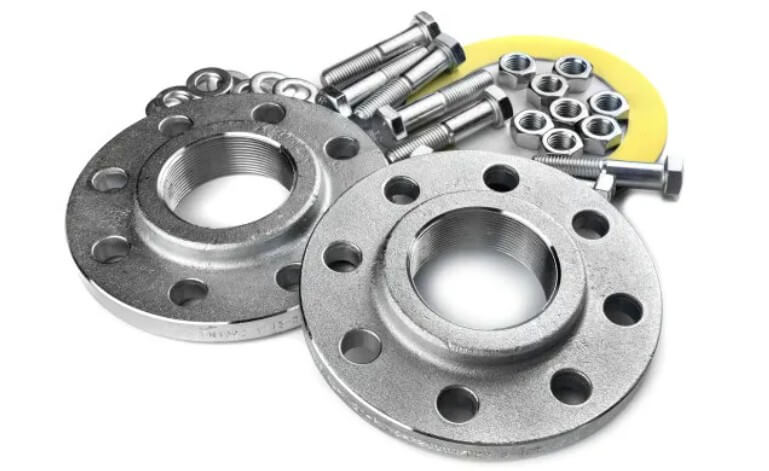
(6) Reactor parts:
Such as reactor bodies, stirring shafts, sealing devices, etc., which are containers for chemical reactions.
2.Design requirements for machined components for chemical equipment
The design of machined components for chemical equipment directly affects its function, manufacturing process and service life, and often involves the following:
(1) Functional design:
Design parts according to the use function of the equipment, such as the pump body to ensure strength and sealing, and the valve to consider the accuracy of fluid control.
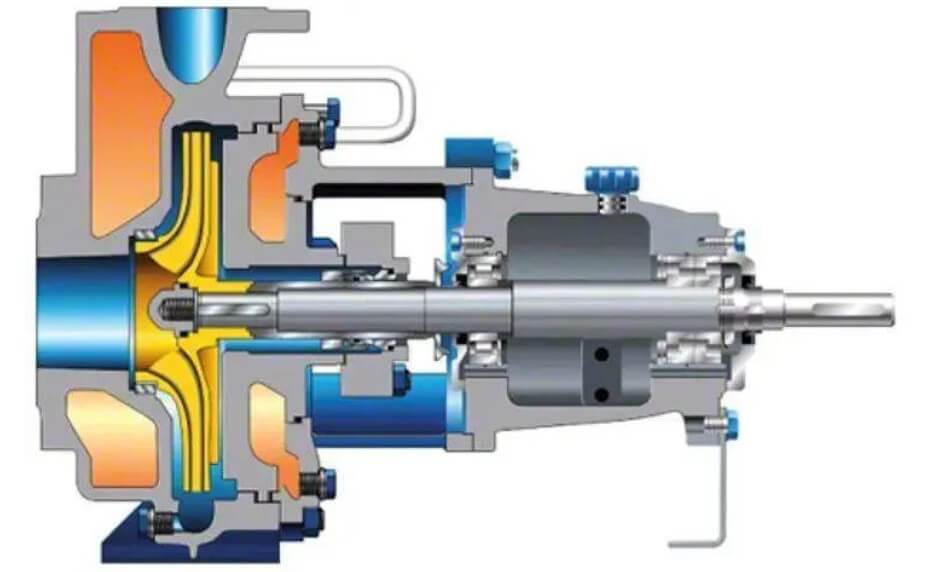
(2) Strength and stiffness analysis:
Use finite element analysis (FEA) to ensure that parts can work normally under high pressure and high temperature environments.
(3) Corrosion-resistant design:
Chemical equipment is often exposed to corrosive media, so the application of corrosion-resistant materials or coatings needs to be considered during design.
(4) Design for manufacturability:
Consider the machinability of parts, avoid overly complex geometric shapes, and reduce the difficulty of production.
(5) Design for assembly and maintenance:
Consider the ease of assembly and the feasibility of later maintenance when designing.
3.Material selection for machined components for chemical equipment
Choosing the right material is crucial for machined components for chemical equipment. Commonly used materials include:
(1) Stainless steel:
Due to its good corrosion resistance and strength, it is widely used in chemical equipment, such as pump bodies, valves, etc.
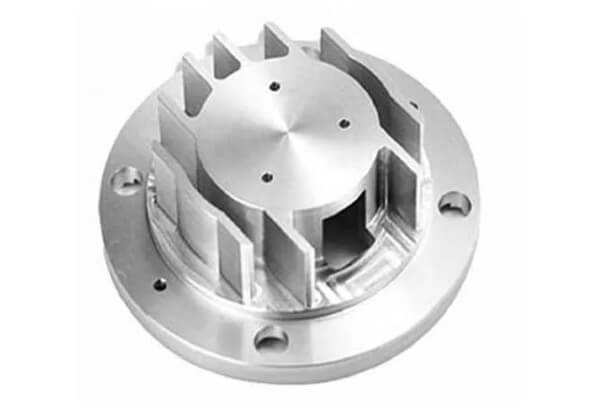
(2) Carbon steel:
Mainly used for parts with high strength requirements, often used in pressure vessels, pipelines, etc.
(3) Alloy steel:
Used for parts that withstand high temperature and pressure, such as high-temperature heat exchangers, reactors, etc.
(4) Corrosion-resistant alloys:
Such as Hastelloy and Monel alloys, often used in highly corrosive environments.
(5) Plastics and composite materials:
Used for some parts that have high corrosion requirements but do not withstand excessive pressure, or for sealing materials.
(6) Ceramic materials:
Used in some special high-temperature and high-corrosion environments, such as sealing rings, pump shafts, etc.
4.Processing technology and process of machined components for chemical equipment
The processing technology of chemical equipment parts includes the following steps:
(1) Machining:
Use traditional machining methods such as turning, milling, grinding, and drilling to make the initial shape of the parts.
(2) CNC machining:
For parts with complex shapes, use CNC machine tools for precision machining to improve machining accuracy.
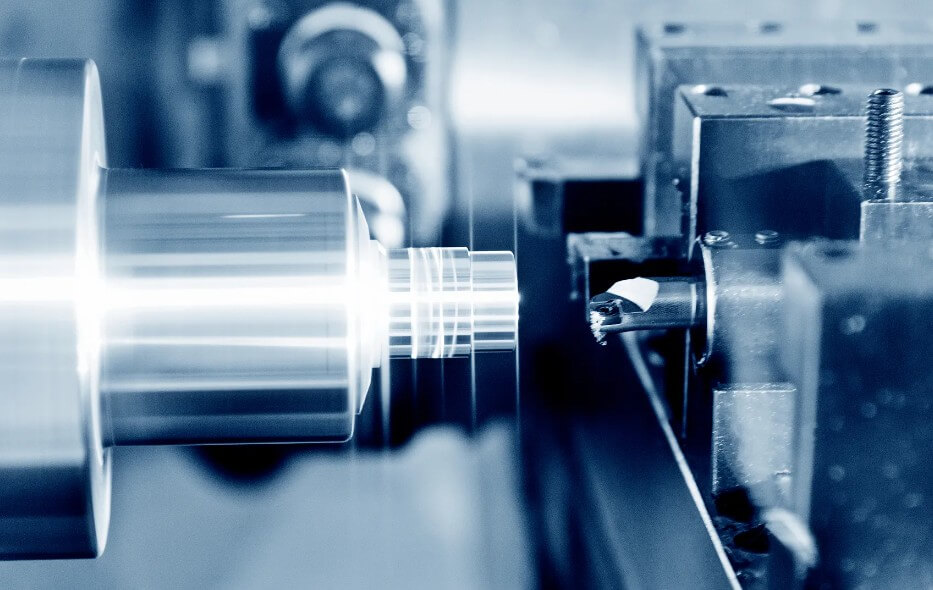
(3) Welding and assembly:
For some large parts, it may be necessary to connect multiple parts through welding processes, such as pressure vessels, reactors, etc.
(4) Heat treatment:
Through heat treatment processes such as annealing, quenching, and tempering, the hardness, strength, and wear resistance of the parts are improved.
(5) Surface treatment:
Such as spraying, plating, thermal spraying, etc., to prevent parts from rapid wear or failure due to contact with corrosive media.
(6) Precision machining and grinding:
For parts that require high precision and surface finish, such as valve seats and seals, precision machining and grinding are performed.
5.Challenges faced in machining chemical equipment parts
In the manufacturing process of machined components for chemical equipment, some challenges may be faced:
(1) Material selection and processing difficulty:
Some special materials (such as corrosion-resistant alloys, ultra-high strength steels, etc.) are difficult to process, which can easily lead to problems such as tool wear and poor processing accuracy.
(2) High precision requirements:
For some key parts (such as seals, pump shafts, etc.), high precision requirements are high, and a slight error may cause equipment failure.
(3) Processing of complex shapes:
Many parts in chemical equipment have complex shapes, especially parts with inner holes, inner grooves, inclined surfaces, etc., which are difficult to process and require highly automated CNC technology.
(4) High temperature and corrosion resistance:
Chemical equipment parts are often exposed to high temperature and corrosive environments. How to ensure the high temperature and corrosion resistance of parts is a major challenge in design and processing.
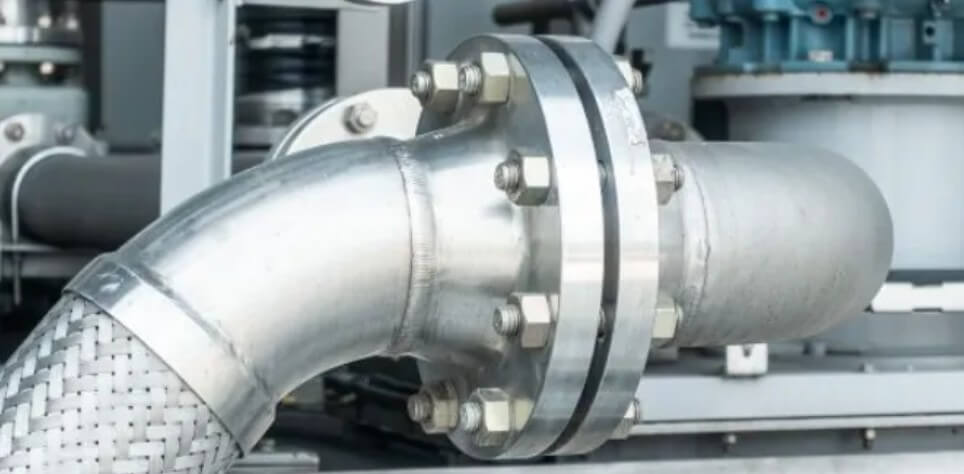
(5) Wear during long-term operation:
Equipment parts will be subject to greater wear during long-term operation. How to improve the wear resistance and life of parts and reduce the occurrence of failures has become an important issue.
6.How to optimize the manufacturing process of machined components for chemical equipment
In order to improve the processing efficiency, precision and surface quality of machined components for chemical equipment, the CNC processing process can be optimized:
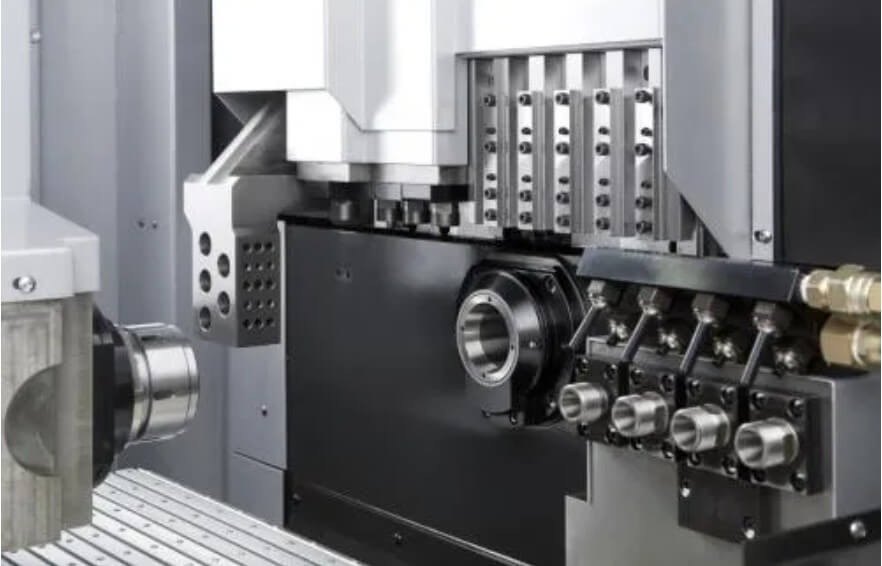
(1) Select suitable tools:
According to the material of the parts and the processing requirements, select suitable tool materials (such as carbide tools, high-speed steel tools, etc.) and tool geometry to reduce cutting force and improve processing accuracy.
(2) Optimize cutting parameters:
Reasonably select cutting speed, feed rate and cutting depth to ensure the efficiency and precision of processing, reduce tool wear and extend tool life.
(3) Use efficient cooling methods:
For materials with higher hardness or difficult cutting, high-efficiency coolants can be used to reduce temperature, reduce cutting heat and improve the surface quality and precision of parts.
(4) Refined processing path planning:
By rationally planning the tool path of CNC machine tools, redundant cutting and unnecessary idle travel can be avoided, processing time can be reduced, and processing efficiency can be improved.
(5) Application of advanced processing technology:
For example, the application of 5-axis linkage CNC technology can handle more complex part shapes, provide higher precision and better surface quality.
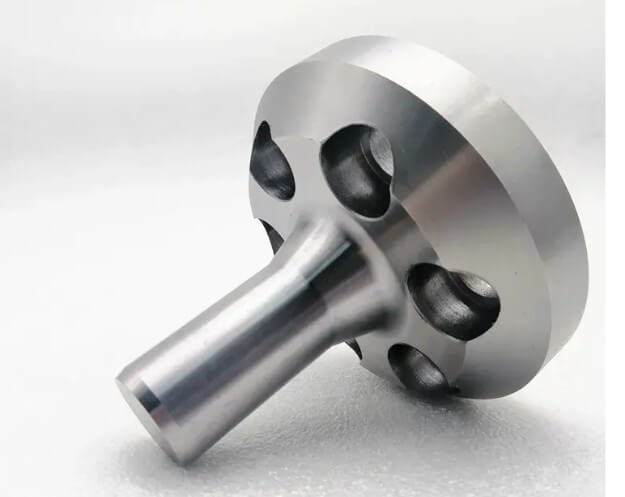
(6) Vibration and thermal deformation control:
During the processing process, controlling the vibration and thermal deformation of the machine tool can effectively ensure the processing accuracy. For example, using vibration suppression technology, thermal compensation system, etc.
(7) Automated processing and online monitoring:
By introducing automated processing systems (such as automatic loading and unloading, intelligent detection, etc.) and online monitoring systems, problems in processing can be discovered in time and adjusted in real time to improve the production efficiency and processing quality of machined components for chemical equipment.
(8) Process optimization and process parameter feedback:
By real-time monitoring and data collection of the processing process, analyzing process parameters, dynamically adjusting the cutting process, and ensuring continuous process optimization.
(9) Processing quality analysis and improvement:
Analyze the errors that occur during the processing in detail, find out the root causes, and improve the processing quality by improving the processing technology, tool selection and cutting parameters.
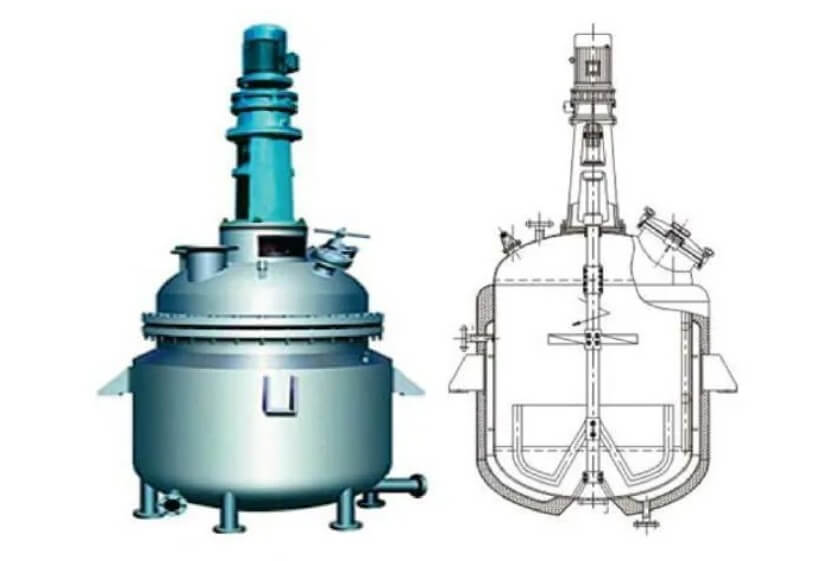
7.Summary
Chemical equipment machined components are widely used in various chemical devices, including pump bodies, valves, heat exchangers, pressure vessels and other key components. Due to the complex and changeable chemical production environment, these parts need to have high strength, corrosion resistance and high precision.
Reasonable part design, scientific material selection and advanced processing technology can ensure the stability and long-term performance of machined components for chemical equipment in high pressure, high temperature and corrosive environments.