Overview and Application of Hydraulic Precision Machined Parts
Hydraulic precision machined parts are core components in hydraulic systems and play an important role in aerospace, automobile manufacturing, engineering machinery and industrial automation.
The machining accuracy of these parts directly affects the sealing, stability and efficiency of the hydraulic system, so the requirements for the manufacturing process are extremely strict.
High-quality hydraulic precision parts can not only improve equipment performance, but also reduce maintenance costs and energy consumption. This article will discuss the role, classification, manufacturing process, material selection and application scenarios of hydraulic precision machined parts.
1.The role of hydraulic systems and precision machined parts
(1) The importance of hydraulic systems in industrial manufacturing
Hydraulic systems are a type of power transmission and control system widely used in industrial manufacturing. They rely on the pressure of liquid media to transmit energy and can achieve efficient and precise mechanical movement. Its main advantages include:
1) High power density:
Hydraulic systems can transmit high power in a small volume, which is very suitable for space-constrained application scenarios.
2) Precise control:
Control flow and pressure through hydraulic valves to achieve high-precision execution.
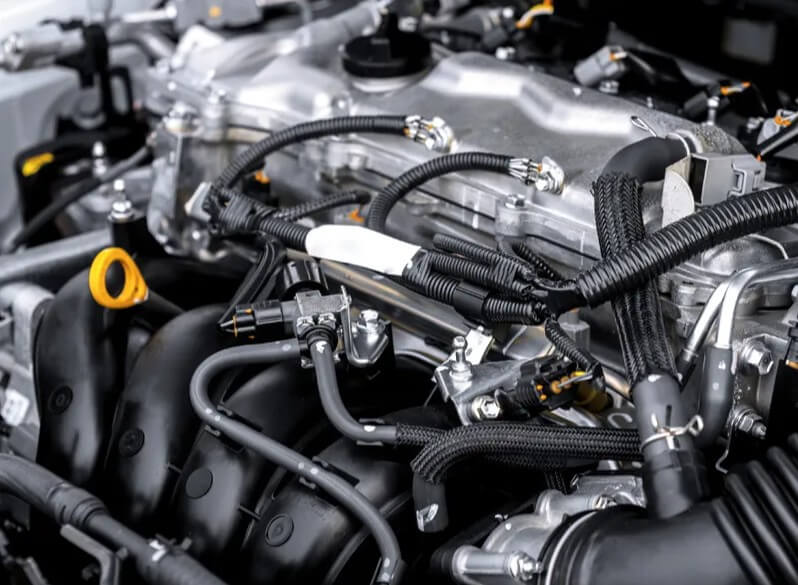
3) Stability and adaptability:
Hydraulic systems can operate in harsh environments and adapt to complex working conditions such as high temperature, high pressure, and strong vibration.
4) Automation integration:
Modern hydraulic systems can be combined with electronic control technology to achieve intelligent and automated operation and improve production efficiency.
(2) The core role of precision machined parts
Hydraulic precision machined parts play a vital role in hydraulic systems. Their main functions include:
1) Ensure sealing and stability:
Hydraulic precision machined parts can reduce leakage and improve the overall stability of the hydraulic system.
2) Improve durability and reliability:
Parts made of high-quality materials and precision manufacturing processes have a longer service life and reduce failure rates.
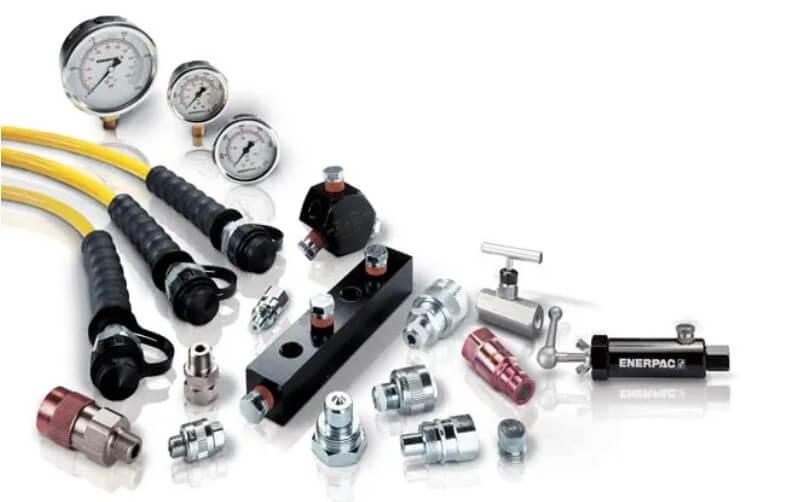
3) Optimize power transmission and energy efficiency:
Precision-made valve bodies, pistons and other parts can reduce fluid resistance and improve system energy efficiency.
4) Suitable for high-end manufacturing needs:
For example, aerospace and high-precision automation equipment have extremely high requirements for hydraulic parts, which must reach micron or even nanometer precision.
2.Classification of hydraulic precision machined parts
There are many types of hydraulic precision machined parts, which can be divided into the following categories according to their functions and uses:
(1) Hydraulic valve parts
1) Direction control valve:
Used to change the direction of fluid flow and control the on/off state of the hydraulic system, such as solenoid reversing valve, manual reversing valve, etc.
2) Flow control valve:
Used to adjust the liquid flow to meet different load requirements, such as throttle valve, speed control valve, etc.
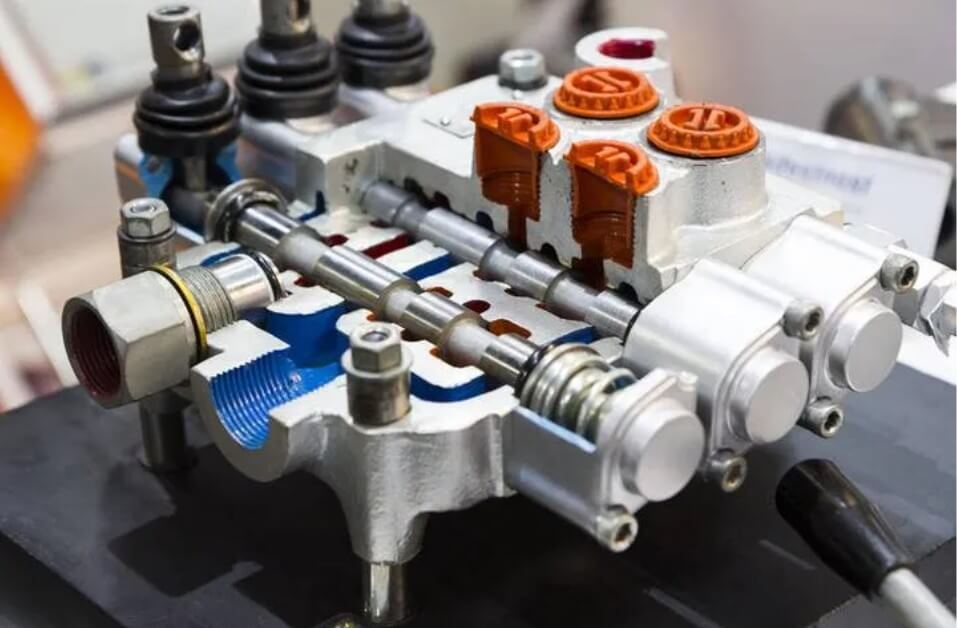
3) Pressure control valve:
Maintain stable system pressure and prevent pressure overload or fluctuation, such as overflow valve, pressure reducing valve, etc.
(2) Hydraulic pump parts
1) Plunger:
The key part of the plunger pump requires extremely high wear resistance and sealing to ensure stable pressure output.
2) Gear:
The core component of the gear pump adopts high-precision processing technology to reduce energy loss and improve transmission efficiency.
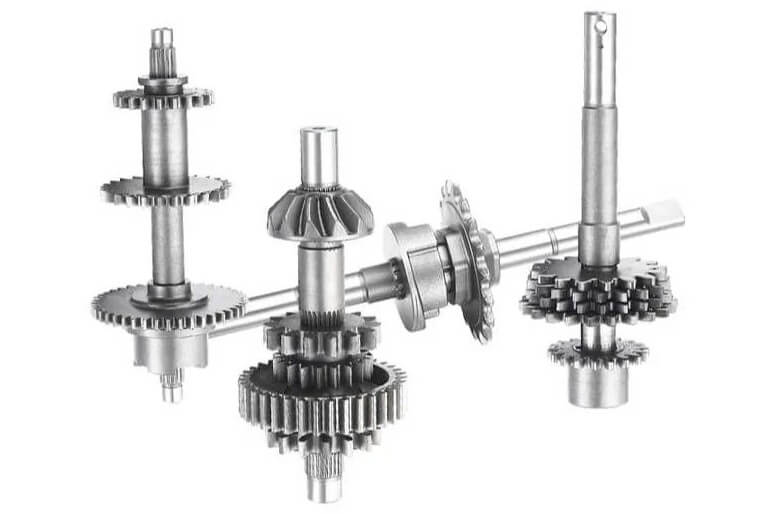
3) Blade:
An important component of the vane pump, it needs to ensure good dynamic balance and wear resistance to extend the service life.
(3) Hydraulic cylinder parts
1) Piston:
Determines the sealing and movement accuracy of the hydraulic cylinder, usually made of high-strength alloy steel or ceramic materials.
2) Cylinder body:
The main component that bears the hydraulic pressure needs to be deep-hole processed and precision honed to ensure a high-precision inner wall.
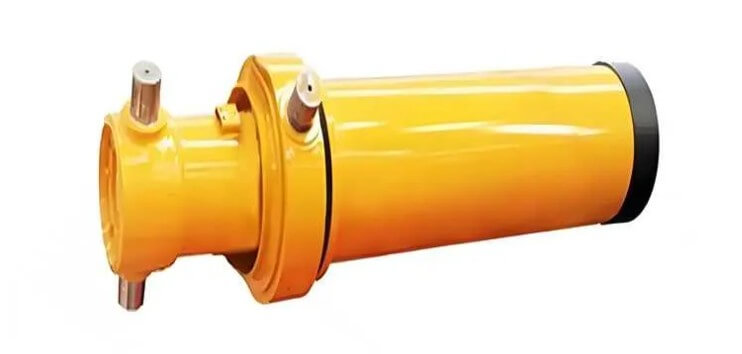
3) Cylinder head:
Ensures piston sealing to prevent hydraulic oil leakage, and connects the cylinder body with other structural parts.
(4) Connections and seals
1) Joint:
Connects different hydraulic components and needs to have high strength and shock resistance to prevent hydraulic oil leakage.
2) Sealing ring:
Fluororubber, polytetrafluoroethylene and other materials are often used to ensure reliable sealing under high temperature and high pressure conditions.
3.Manufacturing process of hydraulic precision machined parts
(1) Material preparation
Select high-strength and wear-resistant materials such as alloy steel, stainless steel or special aluminum alloy.
(2) Rough machining
Use turning, milling and other machining processes to remove excess materials and form a preliminary structure.
(3) Precision machining
Use high-precision CNC machine tools, grinding, honing and other technologies to ensure that hydraulic precision machined parts reach micron-level tolerances.
In the deep hole machining process, in order to ensure the straightness and surface quality of the hole, gun drilling, deep hole drilling or internal hole honing processes are usually used to reduce the aperture error and improve the fluid stability inside the hydraulic cylinder and valve body.
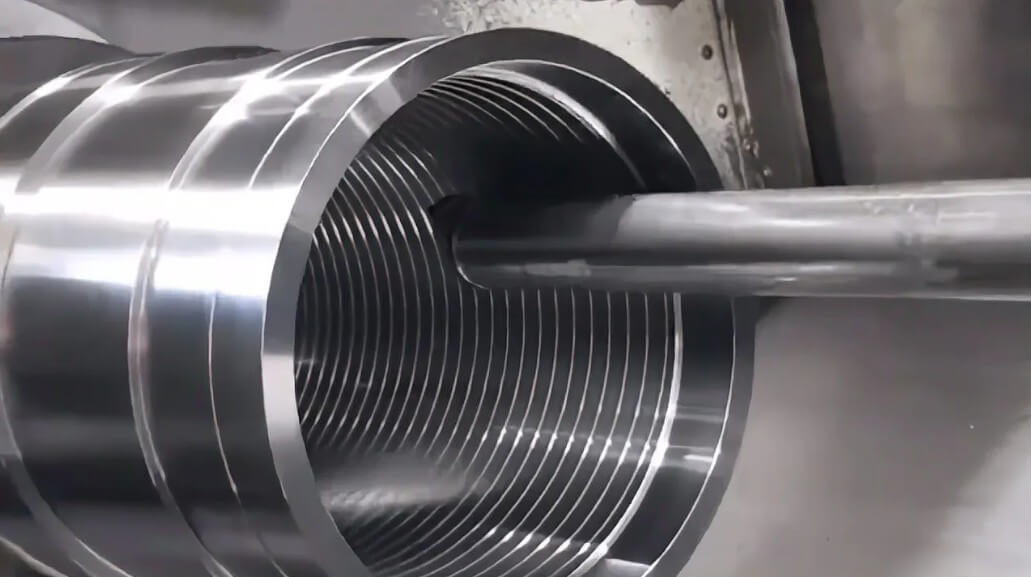
(4) Control of inner surface roughness
The inner surface roughness of hydraulic parts directly affects the sealing and fluid dynamic performance of the hydraulic system. Through high-precision grinding, honing and super-finishing technology, the smoothness of the inner wall of the part is ensured, making the fluid flow smoother and reducing energy loss.
For key components, such as the inner wall of the hydraulic cylinder and the contact surface of the valve core, ultra-precision honing and polishing are usually used to meet strict surface roughness requirements (such as Ra ≤ 0.2μm).
(5) Heat treatment and surface treatment
Heat treatment (such as quenching, tempering, nitriding): Enhance material hardness and wear resistance.
Surface treatment (such as chrome plating, electroplating): improve corrosion resistance and reduce friction loss.
(6) Selection of processing equipment and tools
Select high-precision CNC machine tools, such as five-axis CNC machining centers, to improve the accuracy and consistency of part processing.
For deep hole processing, use a dedicated deep hole drilling machine and select suitable carbide drill bits to ensure processing quality.
In the process of precision grinding and honing, use ultra-hard material tools (such as CBN tools, diamond tools) to improve the surface quality and dimensional accuracy of hydraulic precision machined parts.
4.Material selection for hydraulic precision machined parts
The material selection of hydraulic precision machined parts is crucial, and factors such as wear resistance, corrosion resistance, mechanical strength and weight must be considered. The main materials include:
(1) High-strength alloy steel (42CrMo, 20CrMnTi)
Suitable for high-pressure load-bearing parts, with excellent fatigue strength and wear resistance.
After heat treatment, its hardness and durability can be further improved.
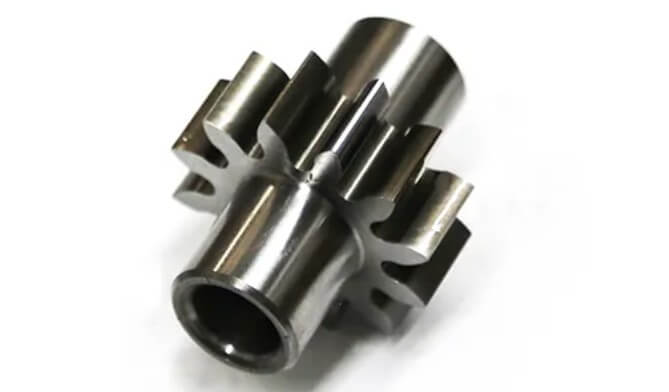
(2) Stainless steel (304, 316L)
Suitable for humid and highly corrosive environments, such as marine engineering and chemical equipment.
Excellent corrosion resistance, extending the service life of the hydraulic system.
(3) Aluminum alloy (7075-T6)
Suitable for lightweight requirements, such as aerospace and mobile hydraulic equipment.
Has both high strength and good oxidation resistance.
(4) Engineering ceramics (zirconia, silicon carbide)
Suitable for ultra-high wear resistance and high temperature conditions, such as high-end hydraulic valve cores or seals.
Has extremely low friction coefficient, improving system efficiency.
5.Application areas of hydraulic precision machined parts
Hydraulic precision machined parts are widely used in multiple industries, mainly including:
(1) Aerospace
Precision control valves and hydraulic pumps for aircraft landing gear hydraulic systems.
Precision hydraulic actuators in spacecraft attitude control systems.
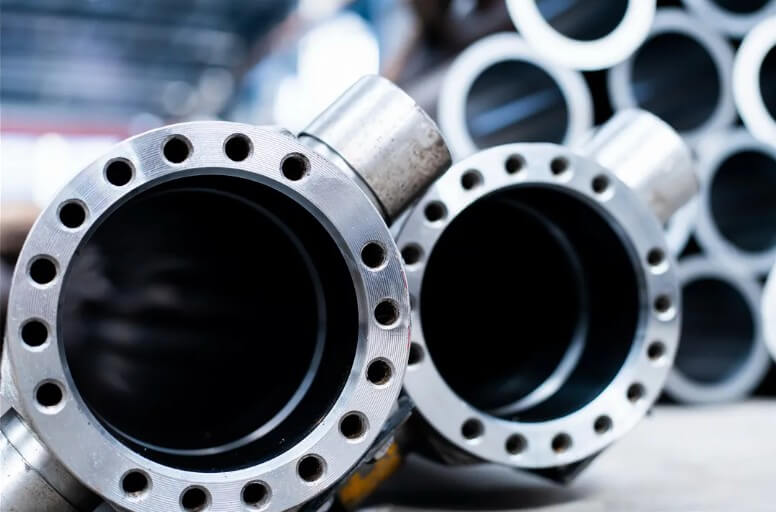
(2) Automobile manufacturing
Key parts of hydraulic brake systems, such as pistons and seals.
Hydraulic control unit in transmission, improving shifting smoothness and efficiency.
(3) Engineering machinery
Hydraulic cylinders and hydraulic pumps for large equipment such as excavators and loaders.
High-pressure hydraulic transmission systems in tunnel boring machines and mining machinery.
(4) Industrial automation
Hydraulic fixtures for CNC machine tools, improving processing accuracy and efficiency.
Robot joint drive hydraulic actuator system, achieving high-precision motion control.
(5) Marine and oil production
Hydraulic control system for submarine pipeline laying equipment.
High-pressure hydraulic actuators for oil drilling platforms, improving operation stability.
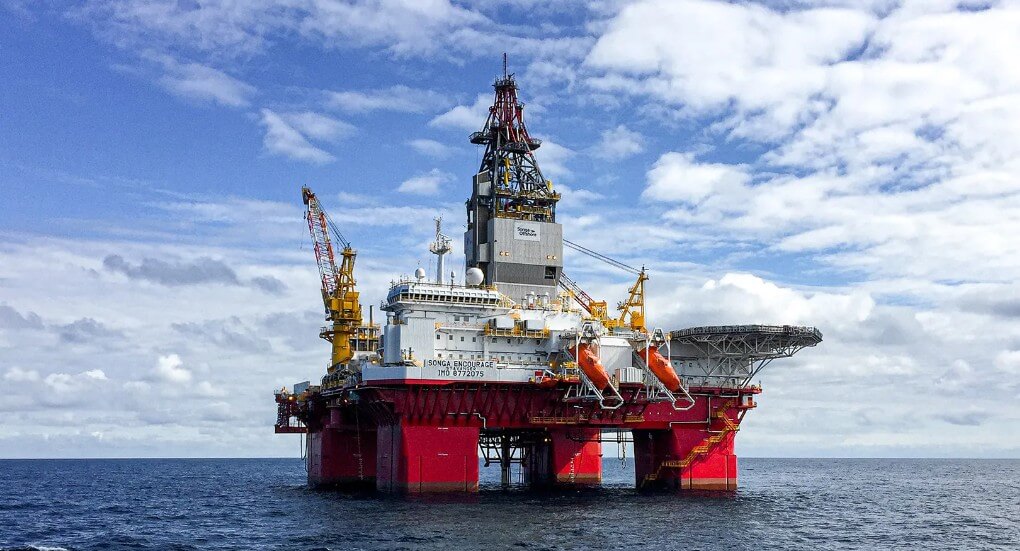
6.Summary
The application of hydraulic precision machined parts covers a variety of industries such as aerospace, automobile manufacturing, engineering machinery, industrial automation, marine and oil production. Their high precision and durability provide a guarantee for the stable operation of hydraulic systems. These parts play an important role in reducing system leakage, improving energy efficiency and extending equipment life, and have become an indispensable core component of modern industry.
What do you think?
[…] Use high-precision CNC machine tools to process key components such as throttles and valve cores to ensure smooth flow channels, […]