How to choose a suitable process for casting stainless steel: from complex parts to mass production
The choice of casting stainless steel process directly affects the quality, cost and production efficiency of the casting. Different casting processes are suitable for stainless steel castings of different shapes, sizes and batches.
Starting from the needs of complex parts to mass production, this article will compare and analyze several major casting stainless steel processes to help you choose the most suitable process solution.
1.Characteristics of stainless steel materials
(1) Strong corrosion resistance:
Stainless steel has very strong anti-oxidation and anti-corrosion properties, especially in special environments such as chemicals and oceans.
(2) Good mechanical properties:
It has high strength, hardness and wear resistance and can be used to manufacture parts that withstand large loads and friction.
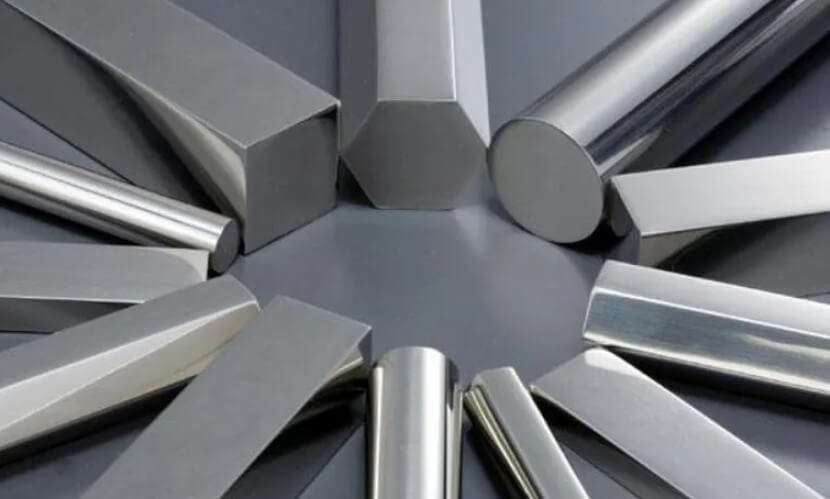
(3) Difficulty in forming:
Stainless steel has a high melting point and is prone to defects such as pores and cracks during casting, so it has high requirements for casting technology.
2.Process principles and common types of casting stainless steel
Casting stainless steel is a process in which molten stainless steel is injected into a mold and cooled to form the desired shape. Common casting stainless steel processes include sand casting, investment casting, centrifugal casting, low-pressure casting and die casting. Each process has its own unique advantages and scope of application. When choosing, it is necessary to comprehensively consider the complexity of the casting, batch size, cost budget and quality requirements.
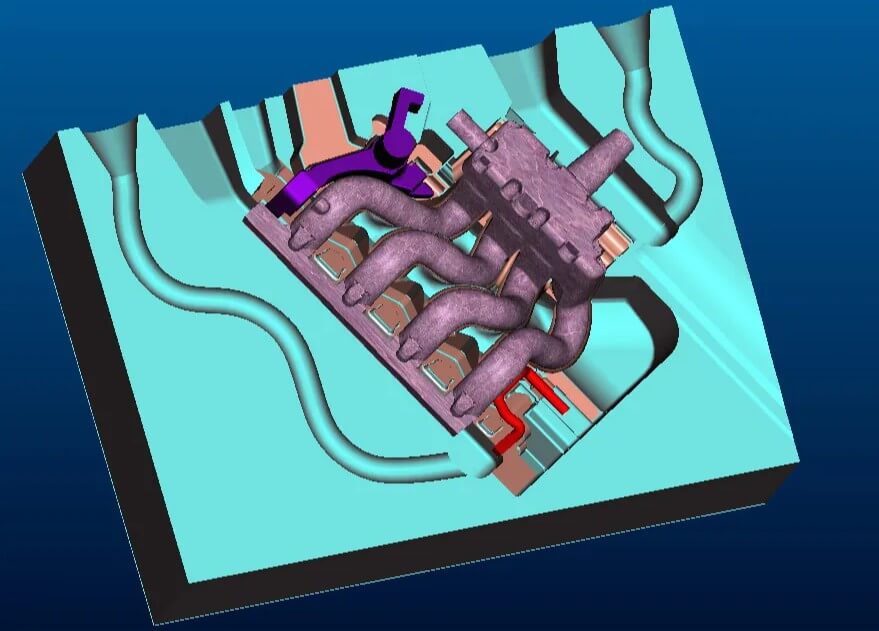
3.Introduction to the main casting stainless steel processes: their respective characteristics and applicable scenarios
(1) Sand casting
1) Process characteristics:
Sand casting is the most traditional casting method. It uses sand molds as mold materials. It has low cost and strong adaptability and is suitable for the production of large castings.
2) Advantages:
The mold is simple to make and is suitable for single-piece or small-batch production; it can cast large and complex-shaped castings.
3) Disadvantages:
The surface roughness is high and the dimensional accuracy is low; the production efficiency is low and it is not suitable for mass production.
4) Applicable scenarios:
Large stainless steel castings (such as valves, pump bodies) or single-piece custom production.
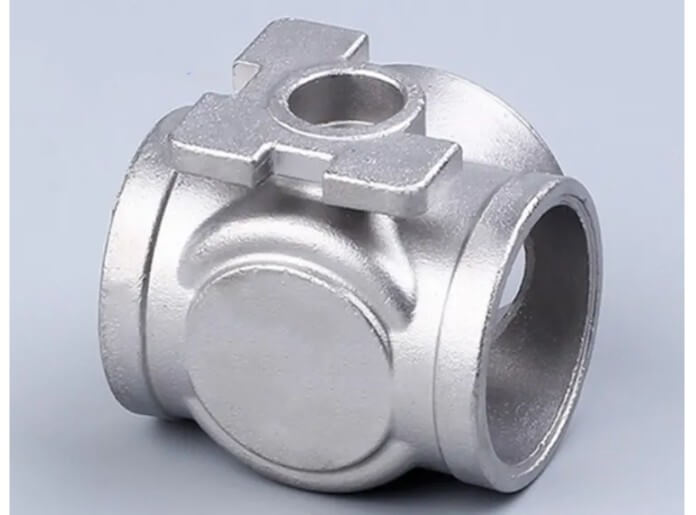
(2) Investment casting (lost wax casting)
1) Process characteristics:
Investment casting uses wax molds to make precision molds, which is suitable for producing high-precision, complex-shaped castings.
2) Advantages:
The casting has a high surface finish and high dimensional accuracy; it can produce extremely complex-shaped castings.
3) Disadvantages:
The process is complex and the cost is high; the production cycle is long.
4) Applicable scenarios:
Precision stainless steel castings (such as aerospace parts, medical devices).
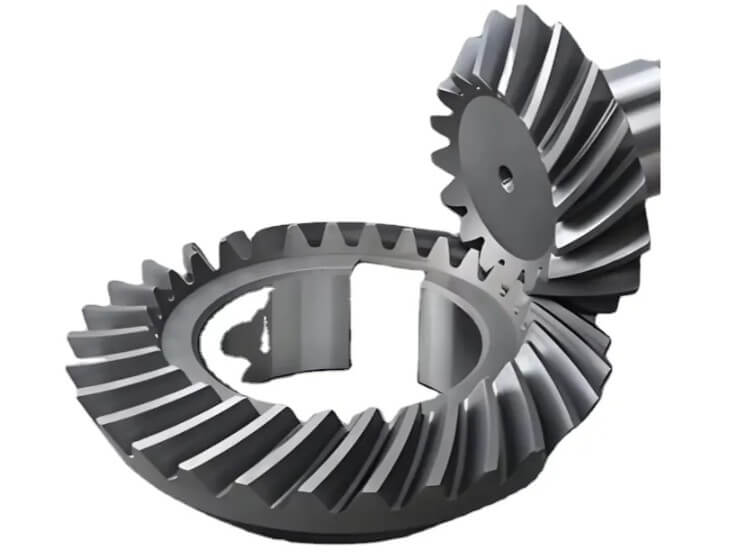
(3) Centrifugal casting
1) Process characteristics:
Centrifugal casting uses a rotating mold to shape the molten metal under the action of centrifugal force, which is suitable for producing tubular or annular castings.
2) Advantages:
The casting has high density and good mechanical properties; it is suitable for producing symmetrical-shaped castings.
3) Disadvantages:
The equipment cost is high; the shape is limited, and it is not suitable for complex parts.
4) Applicable scenarios:
Symmetrical castings such as stainless steel pipe fittings and bearing rings.

(4) Low-pressure casting
1) Process characteristics:
Low-pressure casting uses air pressure to press molten metal into the mold, which is suitable for the production of thin-walled, high-precision castings.
2) Advantages:
Castings have stable quality and high surface finish; suitable for the production of thin-walled complex parts.
3) Disadvantages:
Large equipment investment; high mold cost.
4) Applicable scenarios:
Thin-walled stainless steel castings (such as automotive parts and shell parts).
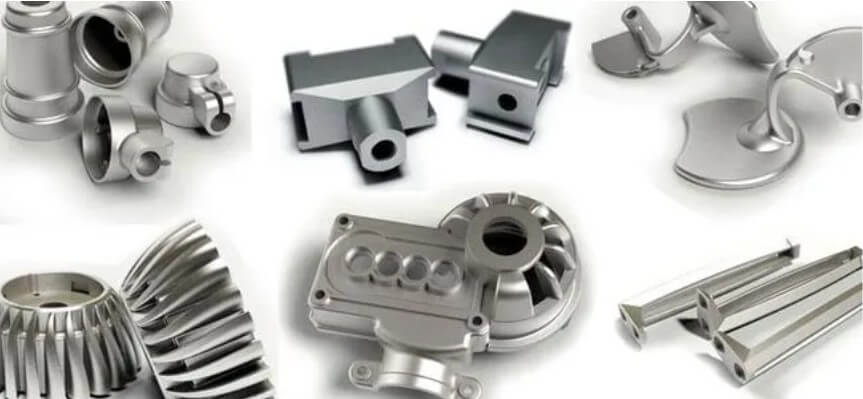
(5) Die casting
1) Process characteristics:
Die casting uses high pressure to inject molten metal into the mold, which is suitable for mass production of small precision castings.
2) Advantages:
High production efficiency, suitable for mass production; high casting dimensional accuracy.
3) Disadvantages:
High equipment cost; not suitable for the production of large castings.
4) Applicable scenarios:
Small stainless steel precision castings (such as electronic components and hardware accessories).
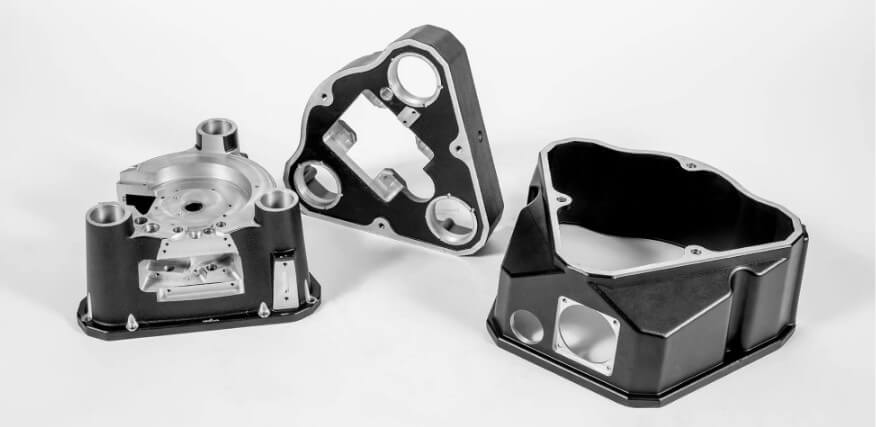
4.Process selection for casting stainless steel from complex parts to mass production
(1) Process selection for complex-shaped castings
Recommended processes:
Investment casting, low-pressure casting.
Reason:
Investment casting is suitable for the production of high-precision, complex-shaped castings, such as aerospace parts; low-pressure casting is suitable for thin-walled complex parts, such as automotive parts.
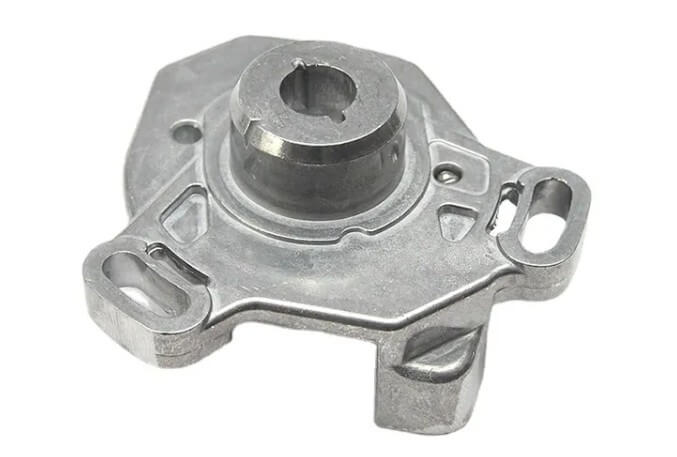
(2) Process selection for large castings
Recommended process:
Sand casting.
Reason:
Sand casting has low cost and strong adaptability, and is suitable for the production of large stainless steel castings, such as valves and pump bodies.
(3) Process selection for mass production
Recommended processes:
Die casting, low-pressure casting.
Reason:
Die casting is suitable for mass production of small precision castings with high efficiency; low-pressure casting is suitable for medium-volume production of high-quality castings.
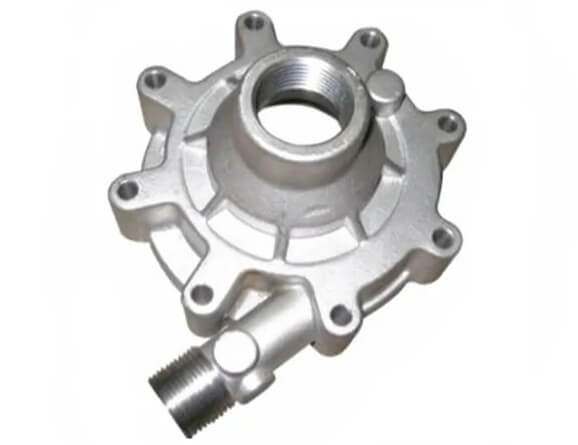
(4) Process selection for symmetrical-shaped castings
Recommended process:
Centrifugal casting.
Reason:
Centrifugal casting is suitable for producing tubular or annular castings, such as stainless steel pipe fittings and bearing rings.
5.Comprehensive considerations for the selection of casting stainless steel process
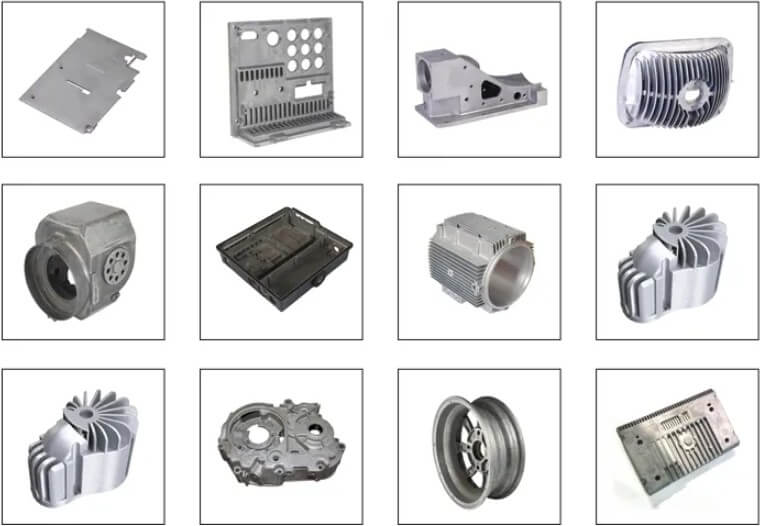
(1) Casting shape and complexity
Complex shape castings are preferably investment casting or low-pressure casting; simple shape castings can be selected from sand casting or centrifugal casting.
(2) Batch size
Sand casting or investment casting can be selected for single-piece or small batch production; die casting or low-pressure casting is preferred for large-scale production.
(3) Cost budget
When the budget is limited, sand casting is an economical choice; when the budget is sufficient, investment casting or low-pressure casting can be selected to improve quality.
(4) Quality requirements
Castings with high precision and high surface quality requirements should choose investment casting or low-pressure casting; castings with general quality requirements can choose sand casting.
(5) Production cycle
Sand casting or die casting can be selected for urgent orders; investment casting can be selected for orders with low production cycle requirements.
6.Analysis of practical application cases of casting stainless steel parts
(1) Case 1: Aerospace parts
Requirements: high precision and complex shapes.
Process selection: investment casting.
Application: high dimensional accuracy and good surface finish of castings, meeting the high standards of the aerospace field.
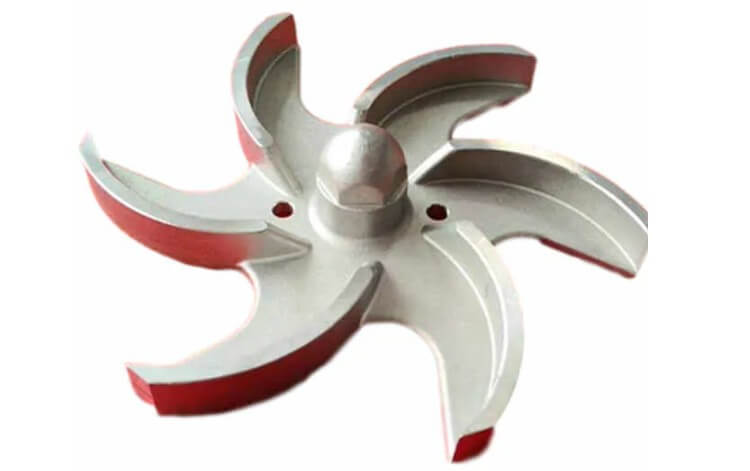
(2) Case 2: Automotive parts
Requirements: thin wall and medium batch.
Process selection: low pressure casting.
Application: stable casting quality and high production efficiency, meeting the batch requirements of the automotive industry.

(3) Case 3: Electronic components
Requirements: lightweight, precise shape and large-scale production
Process selection: die casting.
Application: high precision, smooth appearance and compact structure of castings, maintaining stability and efficiency in large-scale production.
7.Summary
Selecting a suitable casting stainless steel process requires comprehensive consideration of the shape, batch, cost and quality requirements of the casting.
For complex-shaped castings, investment casting and low-pressure casting are ideal choices;
For large castings, sand casting is more advantageous;
For mass production, die casting and low-pressure casting can meet the needs of efficient production.
By selecting the right process, the quality of casting stainless steel parts can be significantly improved, production costs can be reduced, and the needs of different industries can be met.