How to choose the right stainless steel casting material: comparison between 304, 316 and other alloys
Stainless steel castings are widely used in chemical, energy, food processing, medical equipment and other fields due to their excellent corrosion resistance, strength and aesthetics. However, the performance of different stainless steel materials varies significantly, and choosing the right material is the key to ensuring that the casting meets the requirements of use.
This article will compare and analyze the common 304, 316 stainless steel and other alloys to help you choose the right material according to your specific needs.
1.The importance of stainless steel casting material selection
The material selection of stainless steel castings directly affects its performance, service life and cost. Different use environments (such as high temperature, corrosive media, high pressure, etc.) have different requirements for the corrosion resistance, strength, toughness and processing performance of the material. Therefore, understanding the characteristics of various stainless steel materials and their applicable scenarios is the basis for making the right material selection decisions.
2.Common stainless steel materials and their characteristics
(1) 304 stainless steel
1) Composition:
Contains 18% chromium and 8% nickel, which is an austenitic stainless steel.
2) Characteristics:
●Excellent corrosion resistance, suitable for most common environments.
●Good processing and welding performance.
●Relatively low cost and widely used.
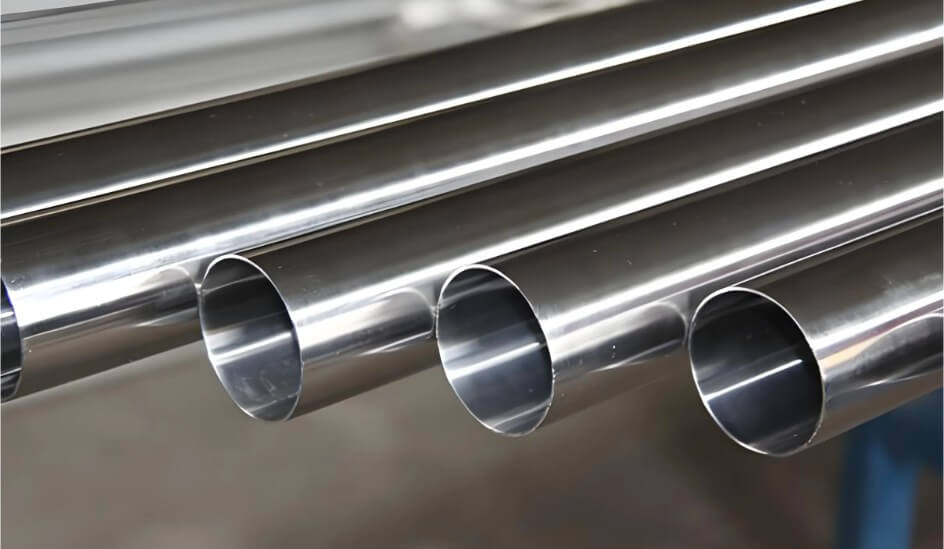
3) Disadvantages:
●Prone to pitting and stress corrosion cracking in chloride ion environment.
●General high temperature resistance, long-term use temperature should not exceed 400℃.
4) Applicable scenarios:
Food processing equipment, household appliances, architectural decoration, etc.
(2) 316 stainless steel
1) Composition:
Add 2% molybdenum on the basis of 304 to further improve corrosion resistance.
2) Characteristics:
●Excellent corrosion resistance, especially better than 304 in chloride ion environment.
●Good high temperature strength and heat resistance.
●Good processing and welding performance.
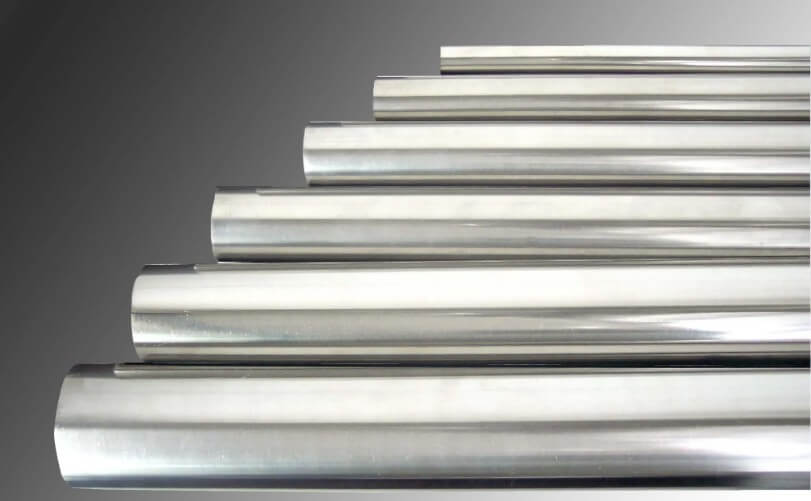
3) Disadvantages:
●High cost, about 1.5 times that of 304.
●Corrosion may still occur in strong acid or strong alkali environment.
4) Applicable scenarios:
Marine equipment, chemical equipment, medical equipment, etc.
(3) Duplex stainless steel (such as 2205)
1) Composition:
Contains 22% chromium, 5% nickel and 3% molybdenum, with both austenite and ferrite structures.
2) Characteristics:
●High strength, about twice that of 304 and 316.
●Excellent corrosion resistance, especially in chloride environments.
●Good resistance to stress corrosion cracking.
3) Disadvantages:
●High processing difficulty and poor welding performance.
●High cost, about twice that of 316.
4) Applicable scenarios:
Petrochemical, seawater desalination, pressure vessels, etc.
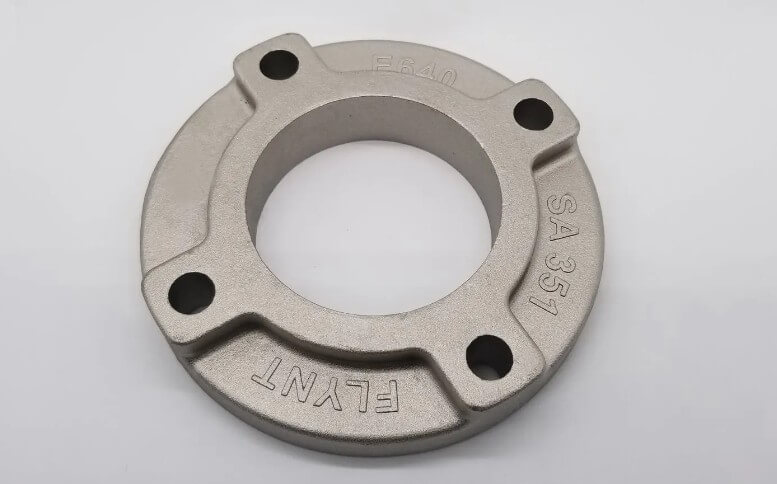
(4) Martensitic stainless steel (such as 410)
1) Composition:
Contains 12% chromium, which is a martensitic stainless steel.
2) Characteristics:
●High strength and hardness, suitable for manufacturing wear-resistant parts.
●Performance can be further improved by heat treatment.
●Low cost.
3) Disadvantages:
● Poor corrosion resistance, especially in humid or corrosive environments.
● Poor welding performance, prone to cracks.
4) Applicable scenarios:
Wear-resistant stainless steel castings such as knives, bearings, and pump shafts.
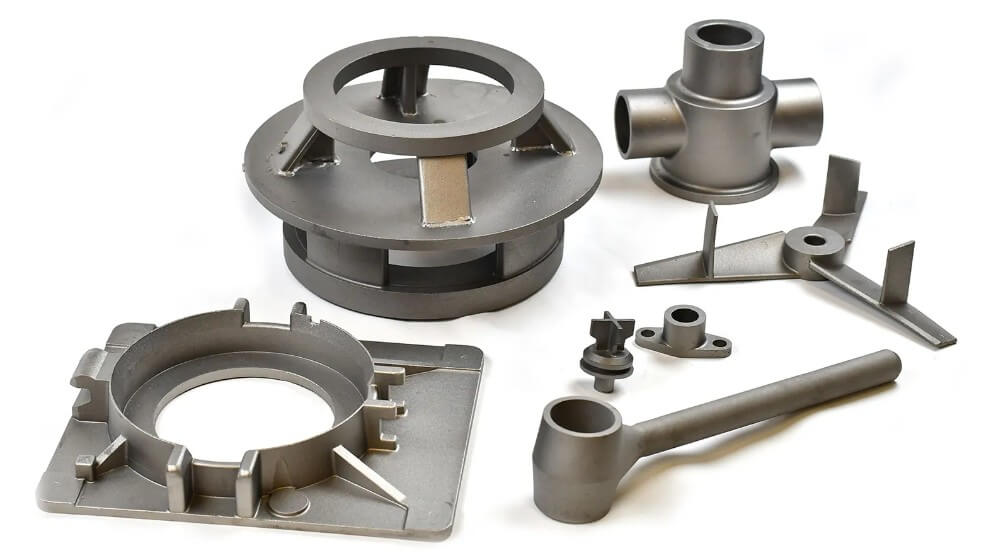
(5) Super austenitic stainless steel (such as 904L)
1) Composition:
High chromium, nickel, and molybdenum content, with added copper and other elements.
2) Characteristics:
● Excellent corrosion resistance, especially in strong acid and alkali environments.
● Good high temperature performance.
3) Disadvantages:
● Extremely high cost and difficult processing.
● Poor welding performance.
4) Applicable scenarios:
Highly corrosive environments (such as sulfuric acid and phosphoric acid equipment).
3.Material performance comparison
The following is a comparative analysis of some common stainless steel materials and properties:
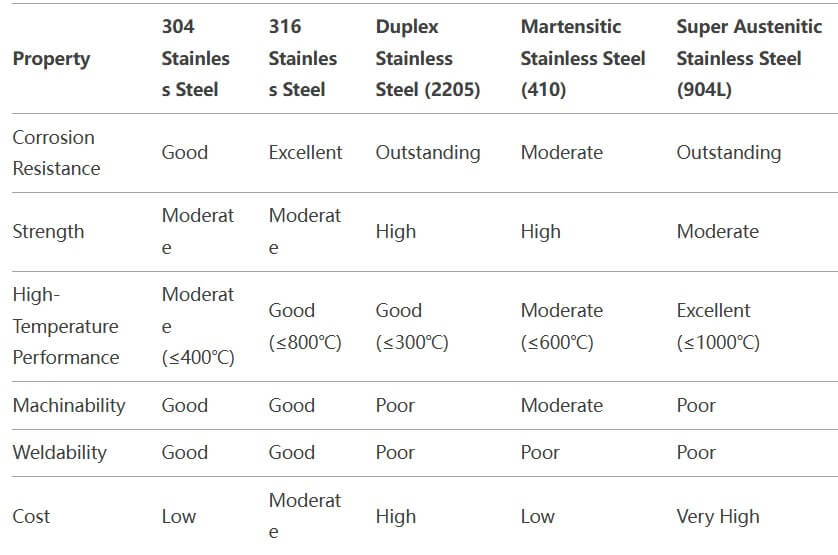
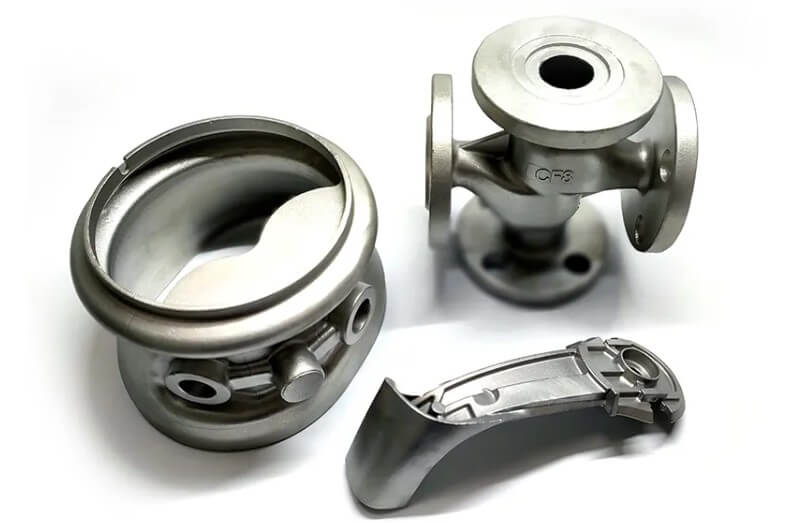
4.Material selection recommendations and application scenarios for stainless steel castings
(1) Ordinary environments (such as food processing, architectural decoration)
Recommended material: 304 stainless steel.
Reason: Low cost, corrosion resistance meets the requirements of ordinary environment, and good processing performance.
(2) Chloride ion environment (such as marine equipment, chemical equipment)
Recommended material: 316 stainless steel or duplex stainless steel.
Reason: 316 stainless steel has better corrosion resistance than 304 in chloride ion environment; duplex stainless steel performs better in extreme environment.
(3) Highly corrosive environment (such as strong acid and strong alkali equipment)
Recommended material: Super austenitic stainless steel (such as 904L).
Reason: Excellent corrosion resistance, suitable for highly corrosive media.
(4) Wear-resistant parts (such as knives, bearings)
Recommended material: Martensitic stainless steel (such as 410).
Reason: High strength and hardness, suitable for manufacturing wear-resistant parts.
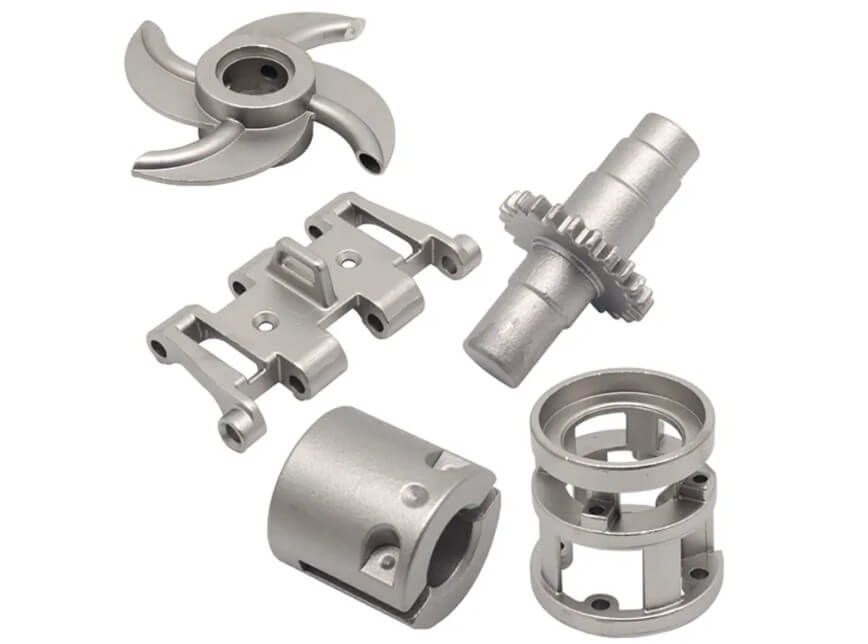
(5) High strength requirements (such as pressure vessels, structural parts)
Recommended material: Duplex stainless steel (such as 2205).
Reason: High strength, good corrosion resistance, suitable for high strength and highly corrosive environment.
5.Precautions for material selection of stainless steel castings
(1) Analysis of use environment
Clarify the use environment of stainless steel castings (such as temperature, medium, pressure, etc.) and select suitable materials.
(2) Balance between cost and performance
Try to select materials with lower cost while meeting performance requirements.
(3) Processing and welding performance
Consider the processing and welding performance of materials to avoid production difficulties caused by process problems.
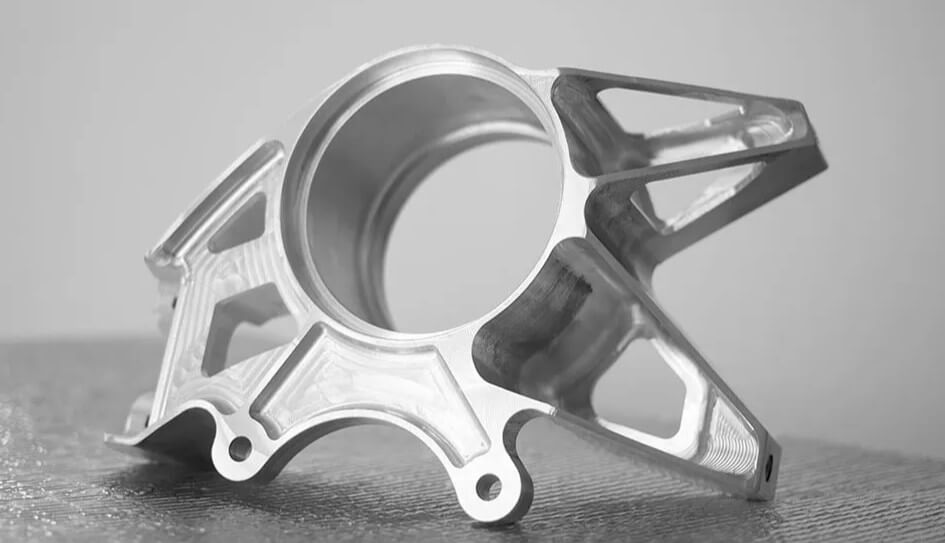
(4) Subsequent processing requirements
If stainless steel castings require heat treatment or surface treatment, select suitable materials and processes.
(5) Supply chain and inventory
Select materials with sufficient supply in the market to avoid affecting production progress due to material shortages.
6.Path to achieve customized high-quality stainless steel castings
(1) Demand analysis and design
Communicate in depth with customers to clarify the use environment, performance requirements and budget range.
Use CAD/CAE software for 3D modeling and simulation analysis to optimize the design plan.
(2) Material selection
Select suitable stainless steel materials (such as 304, 316, duplex stainless steel, etc.) according to the use environment and performance requirements.
Consider the material’s processing performance, welding performance and cost.
(3) Precision casting process
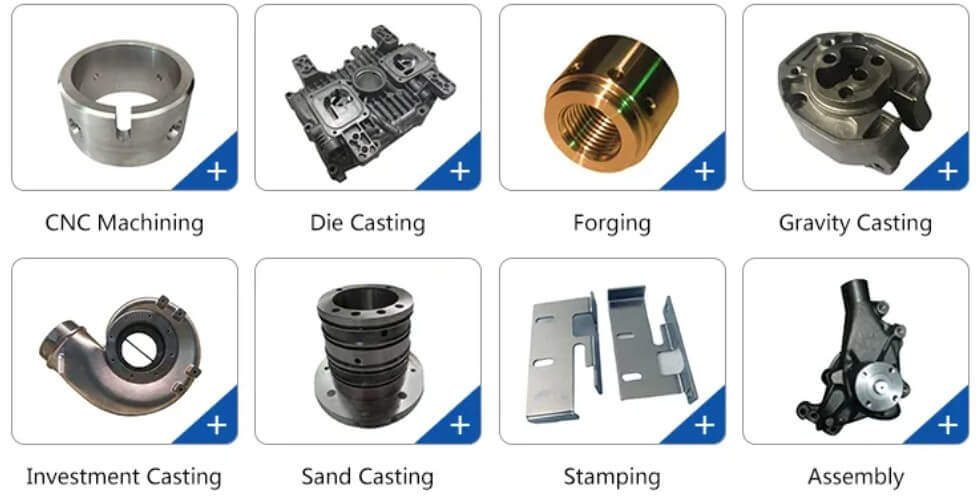
Use precision processes such as investment casting and low-pressure casting to ensure the high precision and high surface quality of stainless steel castings.
Through process optimization, reduce defects (such as pores, shrinkage) and improve the yield rate.
LVXUN Casting has rich experience in manufacturing high-quality stainless steel castings and can provide high-quality casting and machining solutions. If you need any further information or want to discuss your processing needs with us, please feel free to contact us.
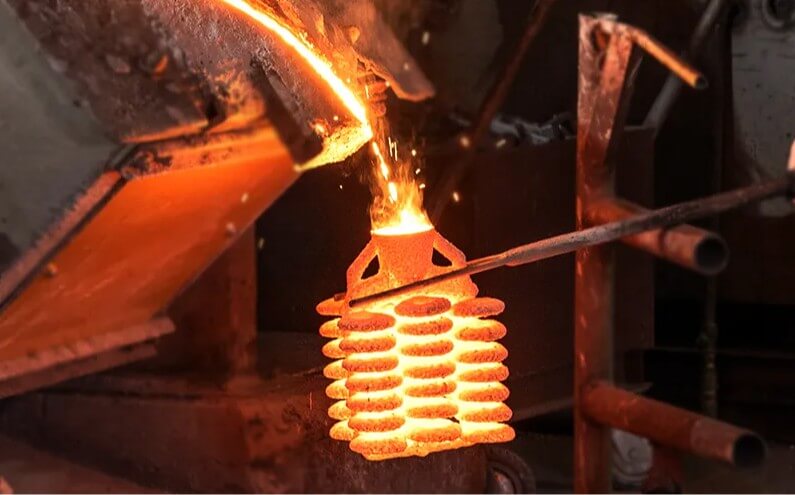
(4) Quality control and testing
Implement strict quality control during the production process to ensure that the castings meet the design requirements.
Use non-destructive testing technology (such as X-ray, ultrasonic testing) for defect detection.
(5) Subsequent processing and surface treatment
Perform subsequent processing such as heat treatment, polishing and passivation as required to improve the performance and aesthetics of the castings.
For example, the corrosion resistance of stainless steel castings can be improved by passivation treatment.
7.Summary
One of the ways to achieve customized high-quality stainless steel castings is to select the right material, which can be considered comprehensively from the perspectives of use environment, performance requirements, cost and processing performance.
What do you think?
[…] (1) Process selection for complex-shaped castings […]