Material selection and process key points analysis of steel investment casting
Investment casting, also known as lost wax casting, is an advanced casting technology that can produce high-precision, complex-shaped castings.
The steel investment casting process is complex, and the entire process involves the selection and application of multiple materials.Material selection and process control are key factors in ensuring the quality of steel investment castings.
This article will conduct a detailed analysis from the aspects of wax pattern materials, shell materials, steel selection and process key points.
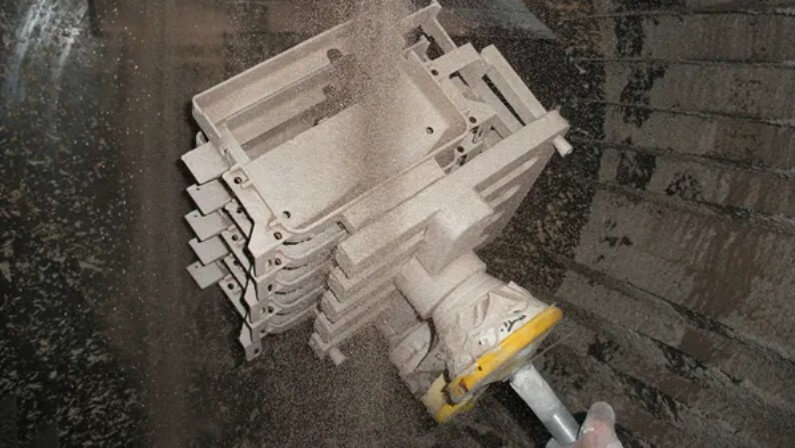
1.Selection of wax pattern materials in steel investment casting
Wax pattern is a key component in the steel investment casting process, and its performance directly affects the dimensional accuracy and surface quality of the casting. Commonly used wax pattern materials include wax-based pattern materials and resin-based pattern materials.
(1) Wax-based pattern materials
Wax-based pattern materials are mainly composed of paraffin wax, ozokerite wax, fatty acid wax and ester wax. Wax-based pattern materials have good fluidity and formability and are suitable for making wax patterns with complex shapes. However, wax-based pattern materials have low strength and heat resistance and are easy to deform.
(2) Resin-based mold materials
Resin-based mold materials are mainly composed of rosin, polyethylene and polystyrene. Resin-based mold materials have high strength and heat resistance and are suitable for making large and complex wax molds. However, resin-based mold materials are expensive and have poor processing performance.
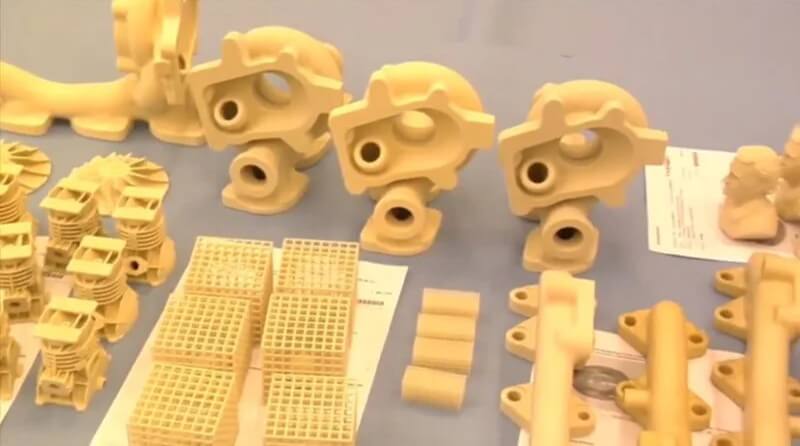
2.Selection of mold shell materials in steel investment casting
The mold shell is an important component in the steel investment casting process. Commonly used mold shell materials include refractory materials and binders.
(1) Refractory materials
Refractory materials mainly include silica sand, zircon sand, bauxite and mullite.
Silica sand has good heat resistance and chemical stability and is suitable for making mold shells for small and medium-sized castings;
Zircon sand has high refractoriness and thermal shock resistance and is suitable for making mold shells for large and high-precision castings;
Bauxite and mullite have high strength and high temperature resistance and are suitable for making mold shells for high-temperature alloy castings.
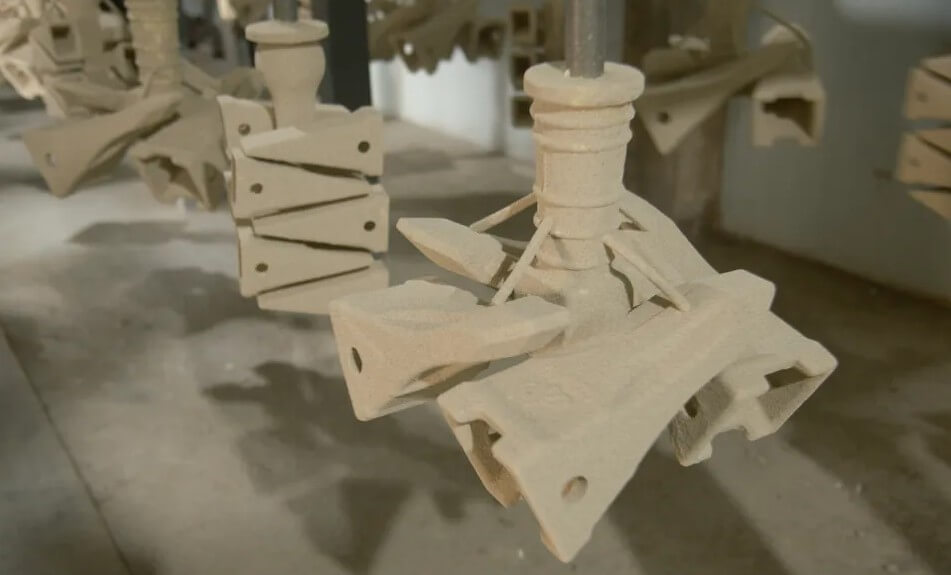
(2) Binders
Binders mainly include water glass, silica sol and ethyl silicate.
Water glass has good bonding properties and low cost, but the strength of the mold shell is low;
Silica sol has high bonding strength and good heat resistance, and is suitable for manufacturing mold shells for high-precision castings;
Ethyl silicate has excellent bonding properties and high-temperature stability, and is suitable for manufacturing mold shells for large and high-precision castings.
3.Steel selection in steel investment casting
In steel investment casting, it is crucial to select the right steel. Different steels have different mechanical properties, heat resistance and corrosion resistance, and are suitable for different application scenarios.
(1) Carbon steel
Carbon steel is one of the most commonly used casting steels, with good mechanical properties and processing properties. According to the carbon content, carbon steel can be divided into low carbon steel, medium carbon steel and high carbon steel.
Low carbon steel has good plasticity and is suitable for manufacturing castings with complex shapes; medium carbon steel has high strength and hardness and is suitable for manufacturing parts with medium loads; high carbon steel has high hardness and wear resistance, but poor plasticity and weldability.
(2) Alloy steel
Alloy steel improves the mechanical properties, heat resistance and corrosion resistance of steel by adding alloying elements (such as chromium, nickel, molybdenum, etc.). Common alloy steels include stainless steel, heat-resistant steel and tool steel.
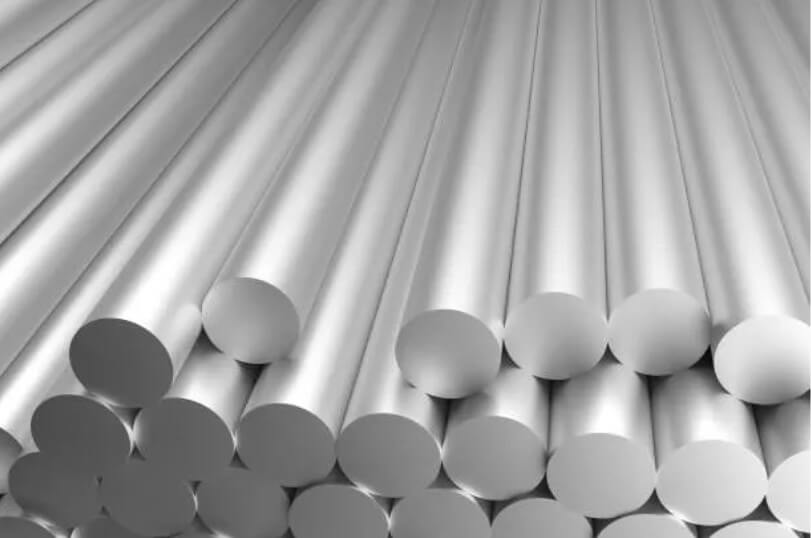
1) Stainless steel:
It has excellent corrosion resistance and is widely used in chemical, food and medical equipment fields. Commonly used stainless steels include austenitic stainless steel (such as 304, 316) and martensitic stainless steel (such as 420).
2) Heat-resistant steel:
It has good oxidation resistance and creep resistance under high temperature environment and is often used in high-temperature components such as steam turbines and gas turbines. Common heat-resistant steels include chromium-molybdenum steel and nickel-based alloys.
3) Tool steel:
It has high hardness, high wear resistance and good toughness, and is suitable for manufacturing cutting tools and molds. Commonly used tool steels include high-speed steel and cold-working die steel.
(3) Special steel
Special steel includes electrical steel, magnetic steel, etc., which have special physical and chemical properties and are suitable for specific application fields. For example, electrical steel has good magnetic properties and is widely used in electrical equipment such as motors and transformers.
4.Key points of steel investment casting process
Based on the above, the material has been selected according to the needs, and the next step is specific production and manufacturing. The process of steel investment casting includes wax pattern manufacturing, shell manufacturing, dewaxing, roasting and pouring, and each link has its key points.
(1) Wax pattern manufacturing
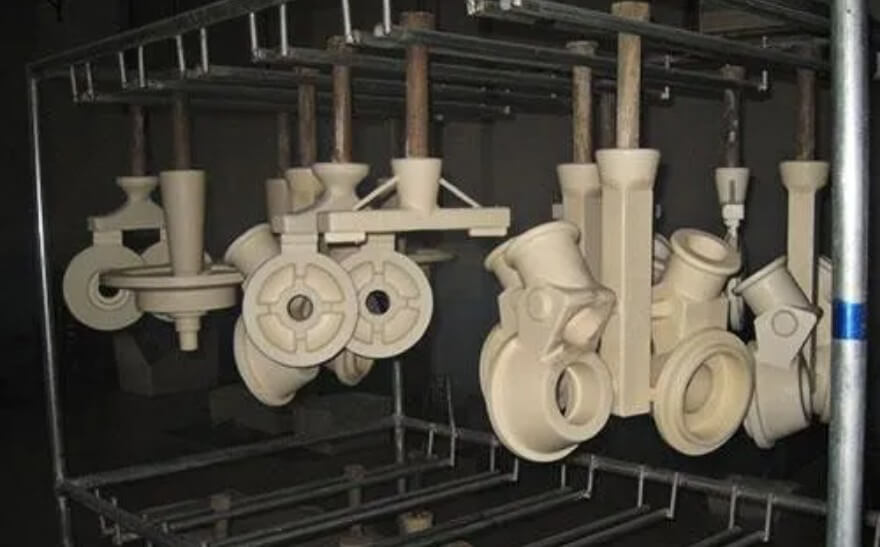
1) Press design:
The press must have high dimensional accuracy and small surface roughness value to ensure the quality of the wax pattern.
2) Wax pattern pressing:
The molten wax material is pressed into the press, taken out after condensation, and a single wax pattern is obtained after trimming and inspection.
3) Combined wax pattern:
The single wax pattern is welded to the pre-made wax common pouring system to form a mold group.
(2) Shell manufacturing
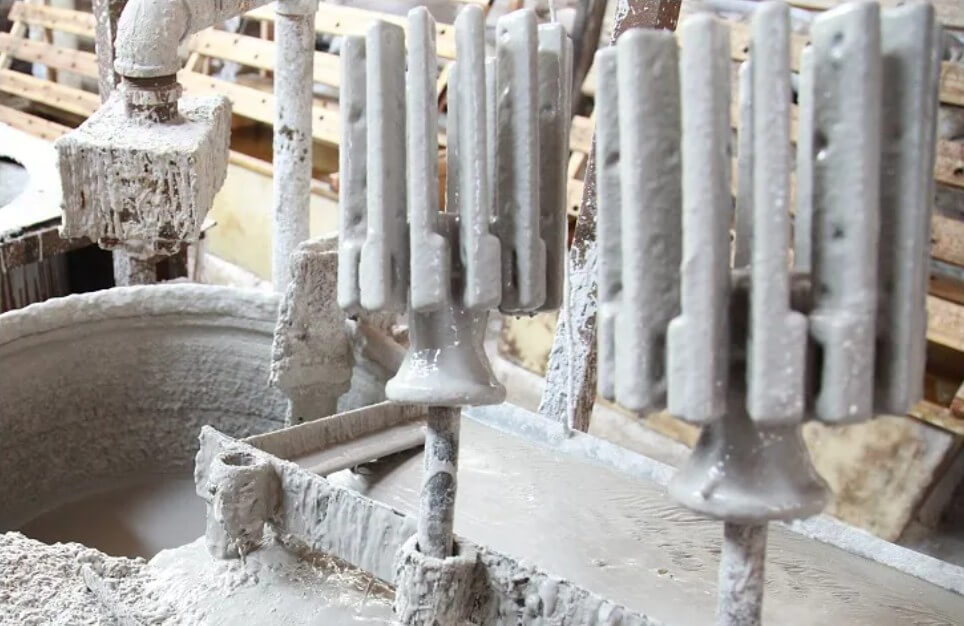
1) Coating and sanding:
The surface of the wax pattern is coated with refractory material and sand is sprinkled to form a shell.
2) Drying and hardening:
The shell must be dried and hardened to improve its strength and heat resistance.
3) Dewaxing:
Put the shell in hot water to melt the wax mold and flow out to obtain a hollow shell.
(3) Firing
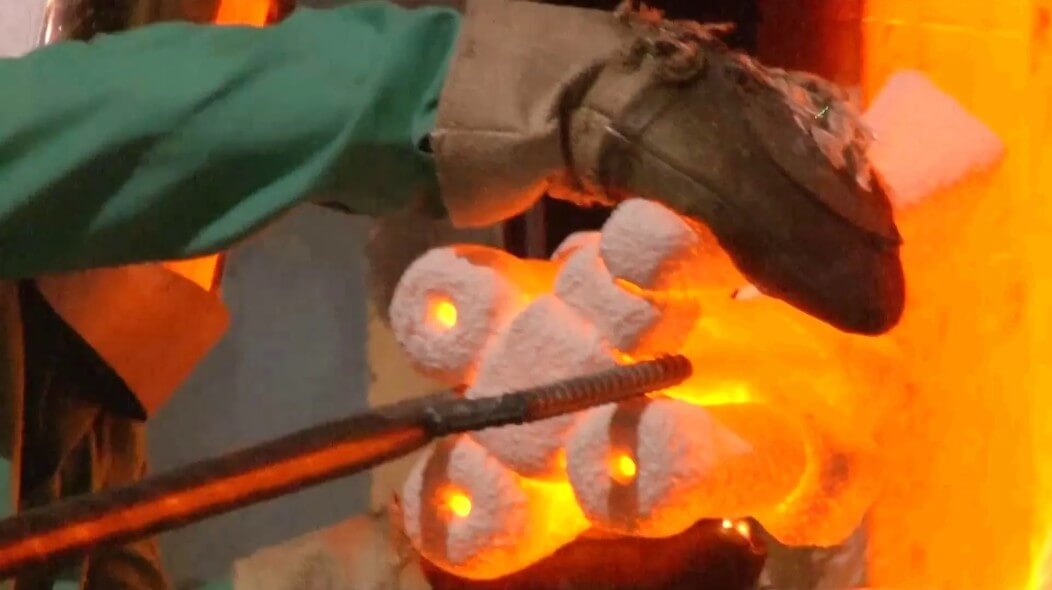
1) High temperature Firing:
The shell is baked at high temperature to remove residual wax and moisture and improve the strength and air permeability of the shell.
2) Temperature control:
The Firing temperature and time must be strictly controlled to prevent the shell from deforming or cracking.
(4) Molten steel pouring
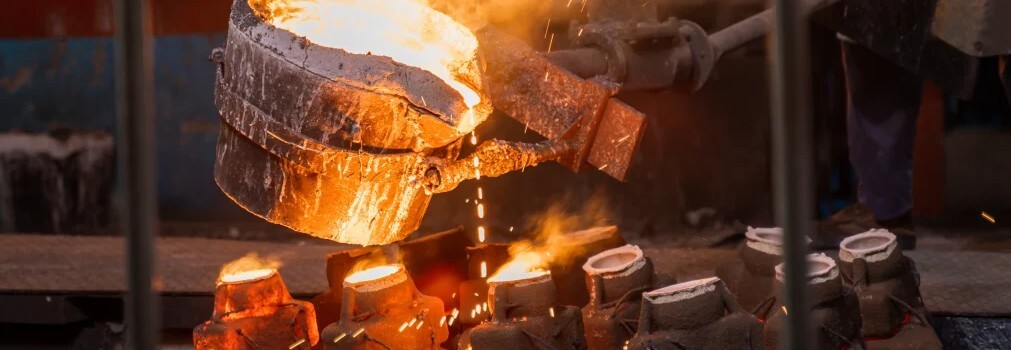
1) Pouring temperature:
According to the type of steel and the shape of the casting, select the appropriate pouring temperature to ensure the filling capacity and solidification quality of the casting.
2) Pouring speed:
Control the pouring speed to prevent the shell from deforming or cracking, and avoid defects such as pores and slag inclusions.
(5) Cleaning
1) Sand removal and cleaning:
After the casting is condensed, destroy the mold, remove the pouring system, clean the burrs and thoroughly clean the casting.
2) Heat treatment:
Heat treatment is performed as needed to improve the mechanical properties and organizational structure of the casting.
5.Quality control of steel investment casting
In the process of steel investment casting, quality control is the key to ensuring the quality of castings. Quality control includes raw material inspection, process parameter control, casting inspection and other links.
(1) Raw material inspection
Strictly inspect steel, wax pattern materials and shell materials to ensure that they meet the technical requirements.
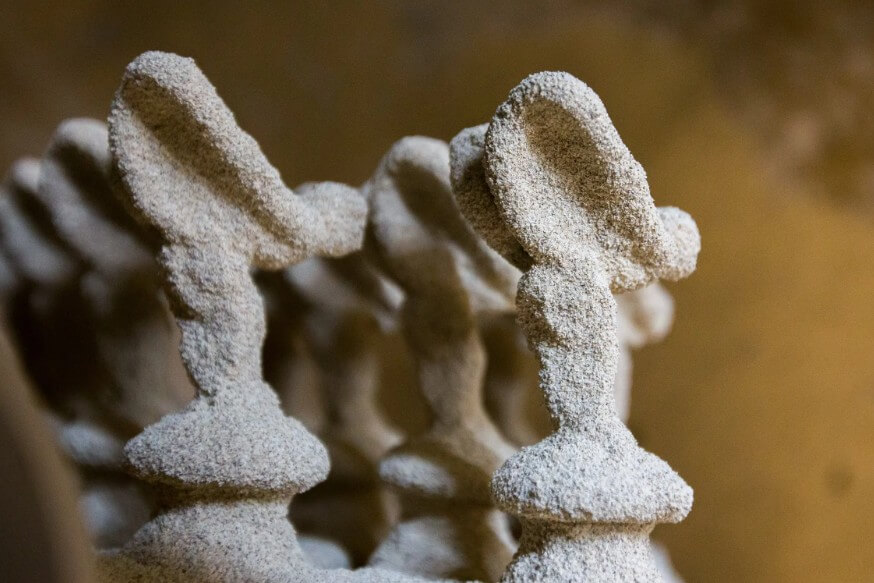
(2) Process parameter control
Strictly control the process parameters such as wax pattern manufacturing, shell manufacturing, roasting and pouring to ensure the quality of each link.
(3) Casting inspection
Inspect the castings for dimensional accuracy, surface quality, mechanical properties and chemical composition to ensure that they meet the design requirements.
6.Conclusion
Steel investment casting is a high-precision and high-efficiency casting technology. In steel investment casting, by rationally selecting steel, wax pattern materials and shell materials and strictly controlling process parameters, the dimensional accuracy, surface quality and mechanical properties of castings can be effectively improved to meet the needs of different application fields.