Analysis and prevention measures of defects in investment castings
Investment casting, also known as lost wax casting, is an advanced casting process with high precision and low cutting, which is widely used in aerospace, automobile, medical equipment and other fields.
Although investment castings have the advantages of high dimensional accuracy and good surface quality, various defects will occur in castings due to the influence of various factors in the actual production process, affecting the quality and performance of castings. This article will analyze in detail the common defect types, causes and corresponding prevention measures of investment castings.
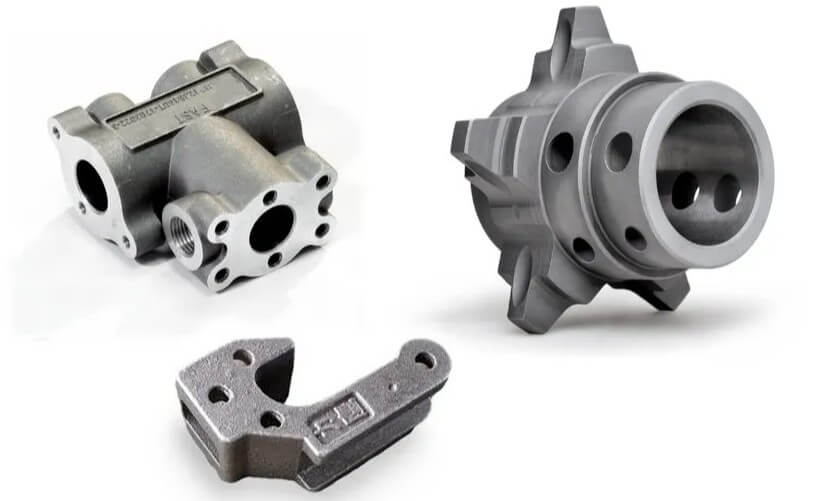
1.Common defect types and causes of investment castings
(1) Shrinkage and shrinkage
Shrinkage and shrinkage are common defects in investment castings, mainly due to the failure to replenish the volume shrinkage of molten metal during solidification. Shrinkage usually appears as round or elliptical holes inside or on the surface of the casting, while shrinkage appears as scattered small pores.
1) Causes:
● Irrational design of the pouring system leads to uneven filling of the molten metal.
● The casting has a complex structure, uneven thickness and inconsistent cooling rate.
● The mold shell is not strong enough, and it deforms or cracks at high temperatures.
2) Preventive measures:
● Optimize the design of the pouring system to ensure that the molten metal can fill the mold sequentially and smoothly.
● Reasonably design the casting structure to avoid a large difference in thickness, and increase process shrinkage measures when necessary.
● Improve the strength and high temperature resistance of the mold shell to ensure that it does not deform or crack at high temperatures.
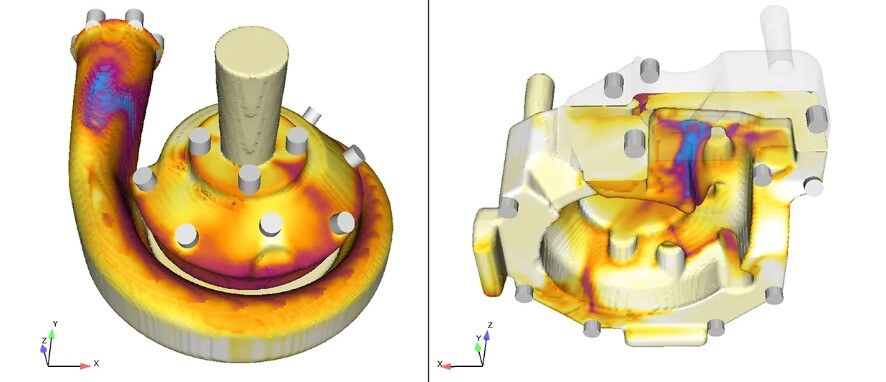
(2) Cracks
Cracks are one of the more serious defects in investment castings. According to the causes and forms, they can be divided into hot cracks and cold cracks. Hot cracks usually occur during the solidification process of the casting, while cold cracks occur after the casting cools to room temperature.
1) Causes:
● Hot cracks are mainly caused by the internal stress generated during the solidification of the molten metal exceeding the tensile strength of the material.
● Cold cracks may be caused by the casting cooling too fast, or the material contains more harmful elements (such as sulfur, phosphorus, etc.), resulting in a decrease in the toughness of the material.
● The casting structure design is unreasonable, and there are stress concentration sites such as sharp corners and sudden changes in thickness.
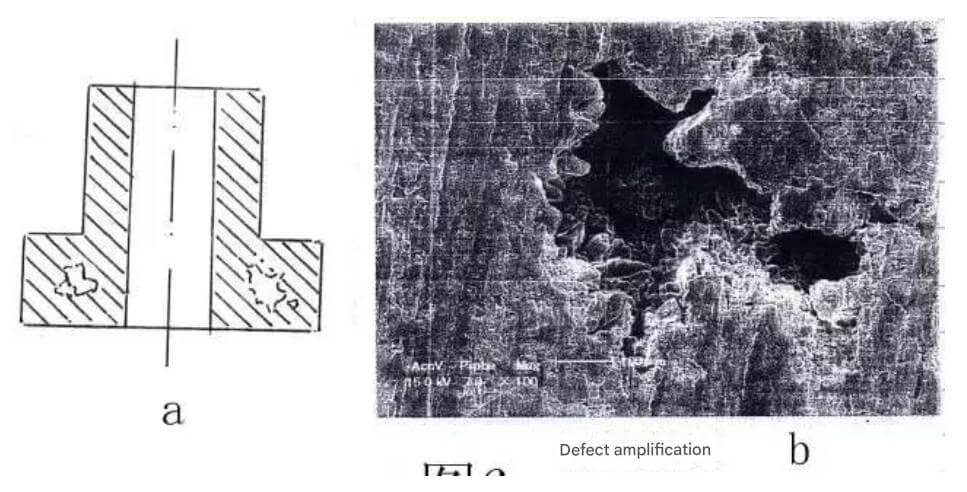
2) Prevention and control measures:
● Control the chemical composition of the molten metal, reduce the content of harmful elements, and improve the crack resistance of the material.
● Optimize the structural design of the investment casting to avoid stress concentration sites such as sharp corners and sudden changes in thickness.
● Control the cooling rate to avoid excessive cooling, and perform slow cooling treatment when necessary.
● Strengthen the strength and stability of the shell to reduce thermal stress.
(3) Surface defects
The surface defects of investment castings mainly include surface roughness, oxidation decarburization, rat tail, depression, sand inclusion, etc. These defects not only affect the appearance quality of the casting, but also may affect its performance.
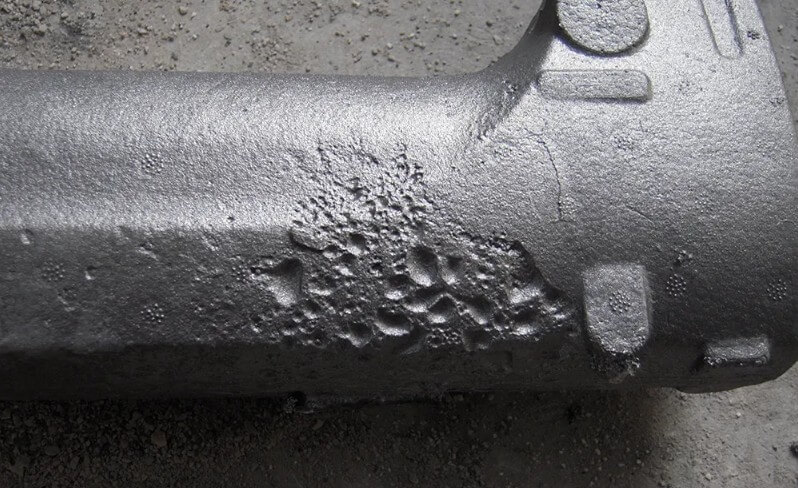
1) Causes:
● The surface quality of the shell is poor, with sand particles, impurities, etc.
● The pouring temperature is too high or too low, resulting in insufficient or excessive reaction between the molten metal and the shell.
● Improper selection of shell material or unreasonable shell making process.
2) Preventive measures:
● Improve the surface quality of the shell to ensure it is smooth and clean.
● Control the pouring temperature to ensure that the molten metal reacts fully and not excessively with the shell.
● Rationally select the shell material and optimize the shell making process to ensure the quality of the shell.
(4) Internal defects
The internal defects of investment castings mainly include pores, slag holes, etc. These defects will reduce the mechanical properties of the castings, especially the impact toughness and fatigue strength.
1) Causes:
● The molten metal contains gas or impurities, which are not discharged in time.
● The pouring system is not designed properly, resulting in gas or impurities being drawn into the molten metal during the filling process.
● The shell is not vented smoothly, resulting in the inability to discharge gas.
2) Preventive measures:
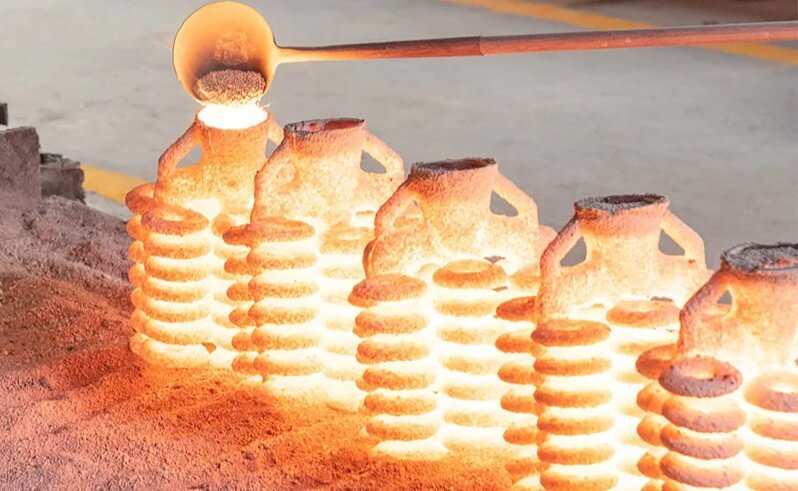
● Strengthen the refining treatment of the molten metal to reduce the gas and impurity content.
● Optimize the pouring system design to avoid gas or impurities being drawn into the molten metal during the filling process.
● Ensure smooth venting of the shell to avoid gas retention.
2.Prevention and control measures for defects in investment castings
(1) Optimize the design of the pouring system
● Reasonable pouring system design can avoid turbulence and splashing of the molten metal during the filling process, and reduce oxidation and slag inclusion defects. Ensure that the layout of the ingates, runners and sprues is reasonable to avoid dead corners or sharp changes in the flow of the molten metal.
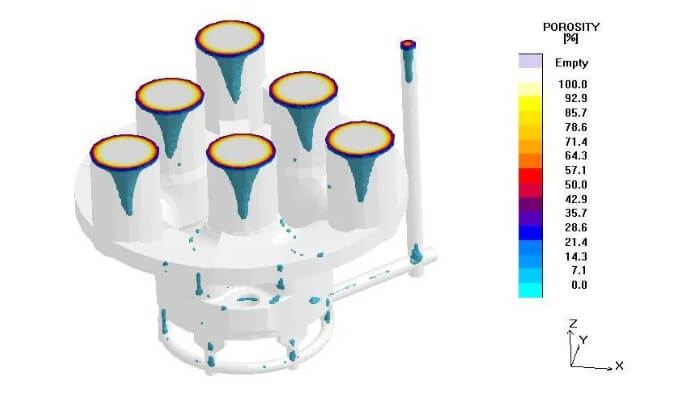
● Using an inclined pouring method can help the floating and discharge of gases and inclusions, and reduce the formation of pores and slag inclusions.
(2) Increase the mold preheating temperature
● Ensure that the mold is preheated to an appropriate temperature to prevent the molten metal from cooling too quickly and reduce the formation of pores and shrinkage cavities. The preheating temperature should be adjusted according to the specific material and casting structure, and is usually controlled between 150-250℃.
● Use appropriate coatings to improve the exhaust performance of the mold and prevent gas accumulation in the cavity to form pores.
(3) Control the pouring temperature and speed
● Reasonable pouring temperature can ensure the fluidity of the molten metal and reduce cold shut and undercasting defects. Too high a temperature can easily lead to sand sticking and shrinkage, while too low a temperature can easily lead to cold shut and insufficient pouring.
● Control the pouring speed to avoid being too fast or too slow. Too fast a pouring speed can easily lead to turbulence and slag inclusions, while too slow a pouring speed can easily lead to cold shuts.
(4) Select appropriate investment castings materials and coatings
● Select high-quality raw materials and mold materials to reduce pyrolysis residues and reduce the probability of slag inclusions and pores.
● Use high-performance coatings with good refractoriness, density and strength to prevent molten metal from penetrating into the sand and forming sand sticking defects.
(5) Use advanced technology and equipment
With the continuous development of science and technology, investment casting technology is also constantly improving. The use of advanced technology and equipment can effectively improve the quality of investment castings and reduce the scrap rate. For example:
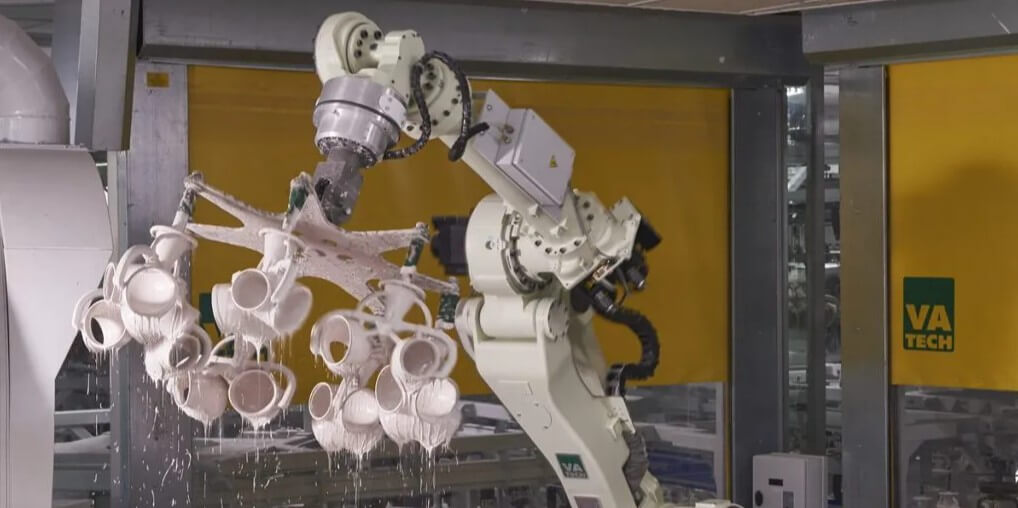
● Use computer simulation technology to simulate and analyze the pouring process and optimize the pouring system design.
● Use vacuum pouring technology to reduce the involvement of gas and impurities and improve the internal quality of castings.
● Adopt automated shell making equipment to improve shell making efficiency and shell quality.
3.Conclusion
The generation of defects in investment castings is a complex process involving multiple links and factors. Only by deeply analyzing the causes of defects and taking effective preventive measures can we
Continuously improve the technical level of investment casting process, thereby improving casting quality, reducing production costs, and improving the competitiveness of enterprises.
What do you think?
[…] investment casting does not require a parting surface, thus avoiding the dimensional error and surface defects caused by the parting […]
[…] Investment castings have high dimensional accuracy and low surface roughness. The general accuracy can reach CT4-6 and the surface roughness can reach Ra25-6.3μm. […]