Application of high-performance ASM Al-Si alloys casts by die casting in the automotive industry
With the continuous development of the automotive industry, the performance requirements for automotive parts are increasing.
High-performance ASM Al-Si alloys casts by die casting have been widely used in the automotive industry due to their excellent mechanical properties and good casting processability. This article will elaborate on the application, manufacturing process and related process parameter settings of high-performance ASM Al-Si alloys casts by die casting in the automotive industry from multiple aspects.
1.Characteristics of high-performance ASM Al-Si alloy
High-performance ASM Al-Si alloy is an alloy material based on aluminum with silicon as the main alloying element. It has the following significant characteristics:
(1) Good mechanical properties:
By adjusting the silicon content and the ratio of other alloying elements, alloy materials with different strengths and toughness can be obtained to meet the use requirements of various automotive parts.
(2) Excellent casting performance:
The alloy has good fluidity and can fill complex mold cavities to produce complex-shaped die castings with fewer casting defects.
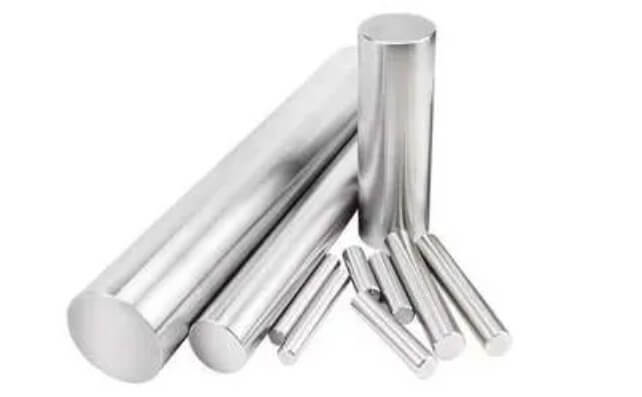
Good thermal conductivity: Aluminum-silicon alloy has good thermal conductivity, which helps to dissipate heat from automotive parts and improve the service life and reliability of parts.
(3) Lower density:
Compared with traditional steel materials, aluminum-silicon alloy has a lower density, which helps to reduce the weight of the entire vehicle, improve fuel economy and reduce emissions.
(4) Good corrosion resistance:
A dense oxide film can be formed on the surface of aluminum-silicon alloy, which has good corrosion resistance and can maintain good performance in harsh environments.
2.Application areas of high-performance ASM Al-Si alloys casts by die casting in the automotive industry
(1) Engine system
1) Cylinder block:
High-performance ASM Al-Si alloys casts by die casting can be used to manufacture engine cylinder blocks. Compared with traditional cast iron cylinder blocks, aluminum-silicon alloy cylinder blocks have the advantages of light weight and good heat dissipation performance, which helps to improve the thermal efficiency of the engine and reduce fuel consumption.
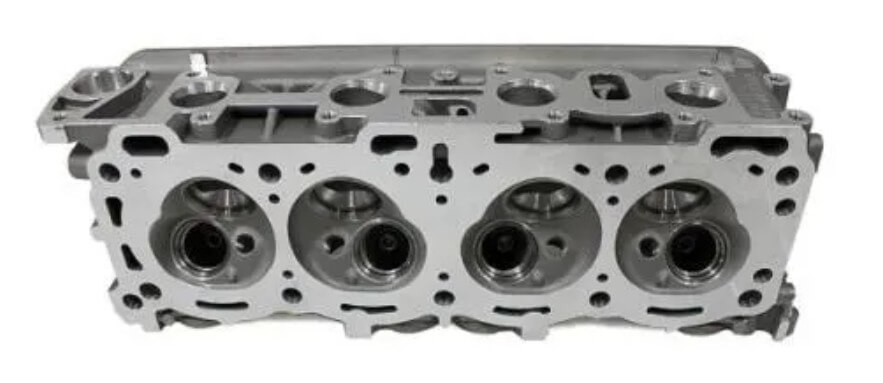
2) Cylinder head:
Aluminum-silicon alloy cylinder head has good thermal conductivity, which can quickly dissipate the heat generated by engine combustion, reduce the operating temperature of the engine, and improve the reliability and durability of the engine.
3) Intake manifold:
The aluminum-silicon alloy intake manifold is light in weight and has good thermal conductivity, which can improve the intake efficiency and the power performance of the engine.
(2) Transmission system
1) Transmission housing:
High-performance ASM Al-Si alloys casts by die casting can be used to manufacture transmission housings. The aluminum-silicon alloy transmission housing has good strength and rigidity, can withstand large torque and vibration, and is light in weight, which helps to improve the fuel economy of the vehicle.
2) Differential housing:
The aluminum-silicon alloy differential housing has excellent corrosion resistance and good casting performance, which can meet the manufacturing requirements of complex structures and improve the reliability and service life of the differential.
(3) Chassis system
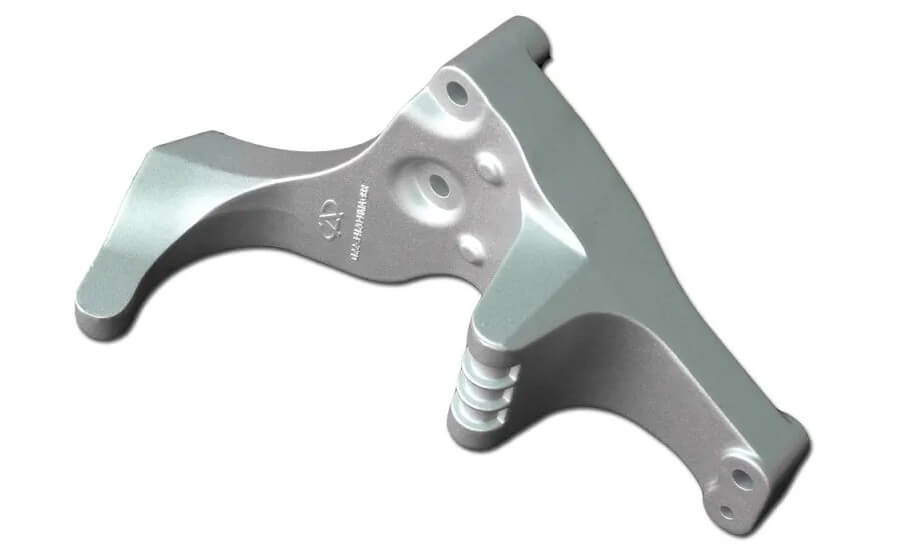
1) Steering knuckle:
The aluminum-silicon alloy steering knuckle is light in weight and high in strength, which can improve the vehicle’s handling performance and driving stability. At the same time, the aluminum-silicon alloy steering knuckle has good casting processability, and can produce steering knuckles with complex shapes to meet the needs of different models.
2) Control arm:
High-performance ASM Al-Si alloys casts by die casting can be used to manufacture control arms. Aluminum-silicon alloy control arms have good strength and toughness, can withstand large loads, and improve the performance of the vehicle’s suspension system.
(4) Body structure
1) Door frame:
Aluminum-silicon alloy door frames are light in weight and high in strength, which can improve the rigidity and safety of the vehicle body. At the same time, the manufacturing process of aluminum-silicon alloy door frames is simple and the cost is low.
2) Roof frame:
Aluminum-silicon alloy roof frames have good corrosion resistance and beautiful appearance, which can improve the overall quality of the vehicle body.
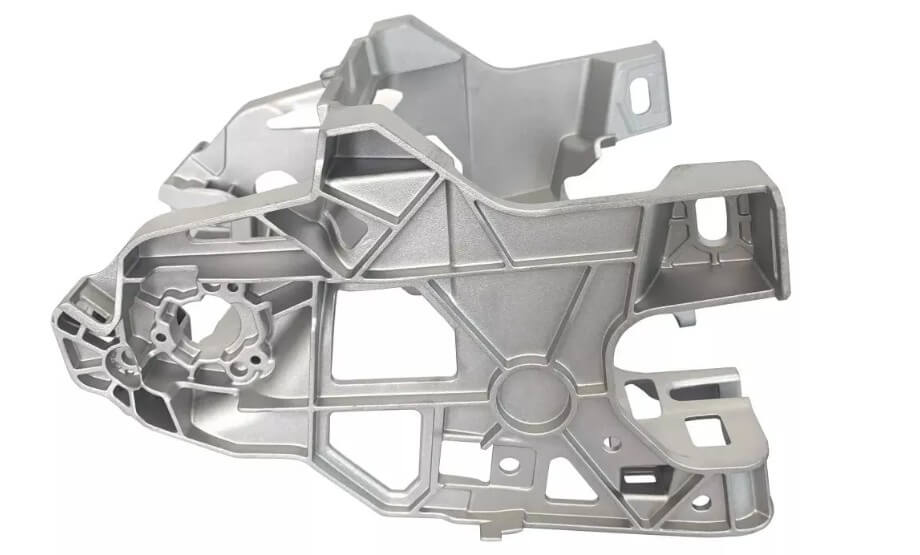
3.Manufacturing process of high-performance ASM Al-Si alloys casts by die casting
(1) Raw material preparation
Select high-purity aluminum and silicon as the main raw materials and prepare them in a specific proportion to ensure that the alloy has excellent mechanical properties and casting properties.
Carry out strict quality inspection of raw materials to prevent impurities from affecting the quality of castings.
(2) Melting
Melting is carried out under inert gas protection or vacuum environment to avoid oxidation and air inhalation of the alloy liquid.
Precisely control the melting temperature, usually between 680-800°C, to ensure uniform alloy composition.
(3) Preparation of die casting mold
Use high-strength and high-heat-resistant mold steel to make die casting molds, and perform heat treatment to improve the service life of the mold.
Preheat the mold, the preheating temperature is generally between 180-300°C to reduce thermal shock and prevent mold cracking.
(4) Die casting
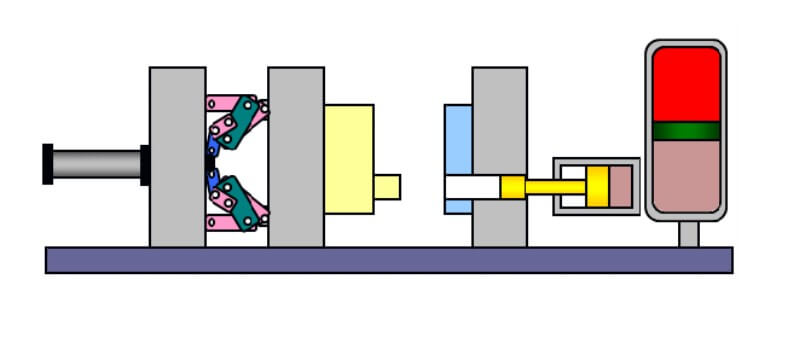
Inject the smelted alloy liquid into the barrel of the die casting machine and quickly fill the mold cavity under high pressure.
During the die casting process, control the filling speed, pressure and time to ensure that the casting has a dense structure and is free of defects such as pores and shrinkage holes.
(5) Cooling and demolding
The casting is demolded after cooling to an appropriate temperature in the mold. Control the cooling speed to prevent deformation and cracking of the casting.
After demolding, clean the casting to remove flash, burrs, etc.
(6) Heat treatment
Solution treatment and aging treatment are performed on ASM Al-Si alloys casts by die casting to improve their mechanical properties and dimensional stability.
The solution treatment temperature is generally 520-550°C, and the holding time is determined according to the thickness of the casting;
The aging treatment temperature is generally 150-180°C, and the holding time is generally several hours.
(7) Quality inspection
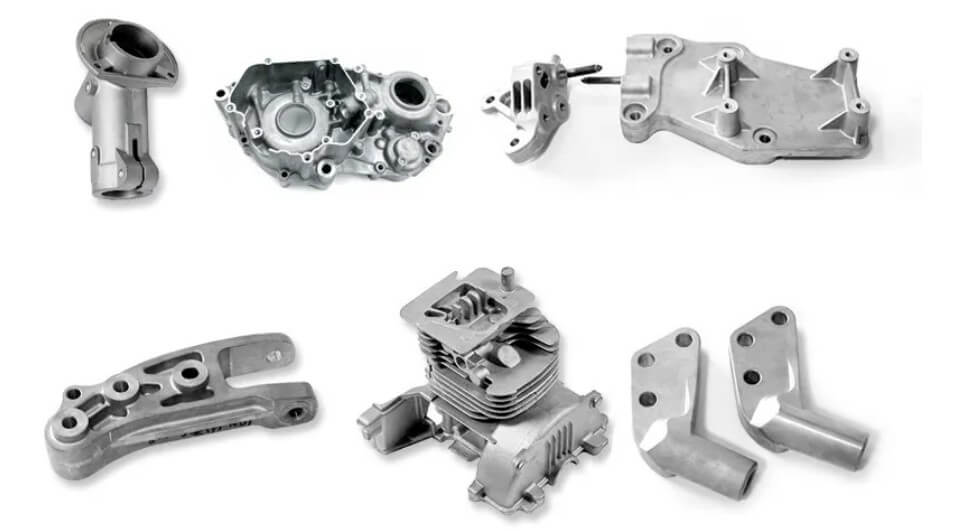
The internal quality of the casting is inspected by X-ray flaw detection, ultrasonic testing and other methods to ensure that there are no internal defects.
The dimensional accuracy, surface quality, mechanical properties, etc. of ASM Al-Si alloys casts by die casting are inspected to meet the design requirements.
4.Case analysis: Optimizing process parameters to improve the quality of ASM Al-Si alloys casts by die casting
(1) Case background
A certain automobile parts manufacturer uses ASM Al-Si alloy to produce a certain type of engine cylinder head. During the production process, it was found that ASM Al-Si alloys casts by die casting had defects such as cold shut, undercasting, and cracks, which seriously affected product quality and production efficiency.
(2) Problem Analysis
●Through a comprehensive inspection and analysis of the production process and equipment, the following problems were found:
1) The alloy melting temperature control is not accurate, and there is a large temperature fluctuation.
2) The injection speed and pressure selection are unreasonable, resulting in incomplete metal liquid filling.
3) The mold temperature control is unstable, and the temperature in some areas is too high or too low.
4) The holding time and cooling time are improperly set, resulting in shrinkage holes, shrinkage and other defects inside the die casting.
(3) Optimization measures
●In response to the above problems, the following optimization measures were taken:
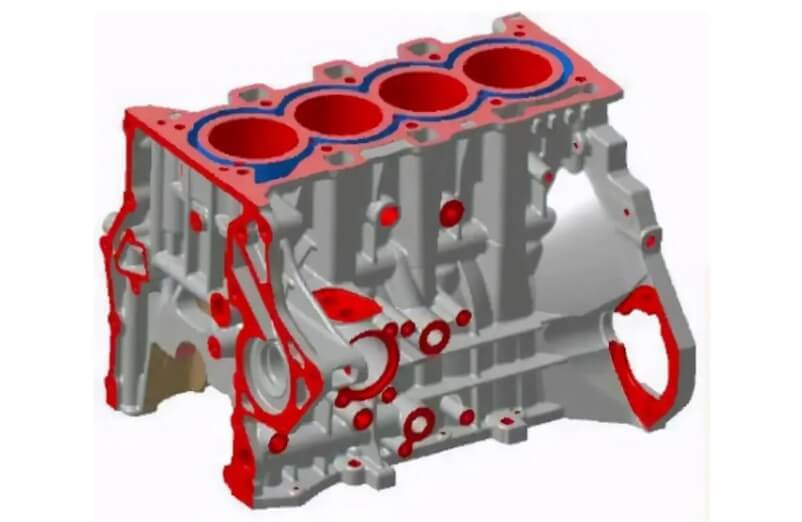
1) Replace advanced melting equipment and regularly calibrate the temperature of the melting furnace to ensure that the alloy melting temperature is stable between 680-750℃.
2) According to the structure and wall thickness of the die casting, readjust the injection speed and pressure to ensure that the metal liquid can smoothly fill the mold.
3) Use a mold temperature control system to accurately control the mold temperature to ensure that the mold temperature is stable between 180-250℃.
4) According to the structure and wall thickness of the die casting, readjust the holding time and cooling time to ensure that the internal structure of the die casting is dense and defect-free.
5.Conclusion
High-performance ASM Al-Si alloys casts by die casting have broad application prospects in the automotive industry. By optimizing the alloy composition and manufacturing process, ASM Al-Si alloys casts by die casting with excellent performance, light weight and low cost can be produced to meet the various needs of the automotive industry for parts.