Performance analysis of alloy die casting materials: how to choose the most suitable die-casting material
Alloy die casting is a metal forming process widely used in modern manufacturing. It injects molten metal into the mold cavity under high pressure and quickly cools and solidifies to form parts of the required shape and size. Selecting the right alloy die casting material is crucial to ensuring product quality, production efficiency and economic benefits.
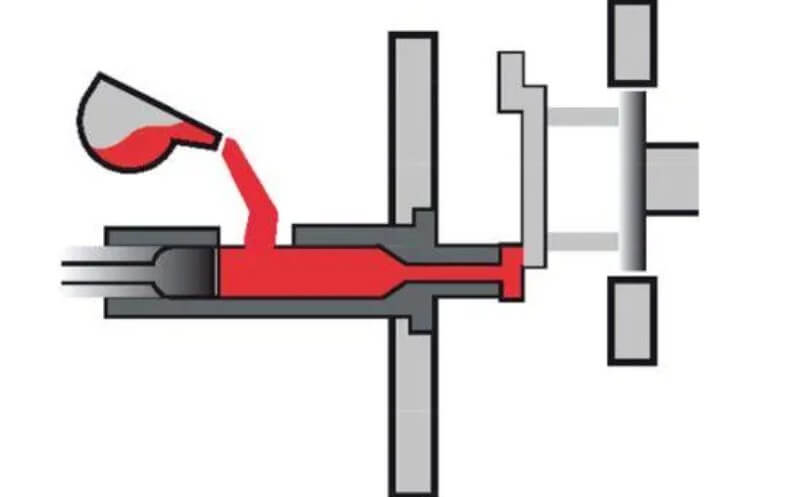
This article will analyze in detail the performance characteristics of three commonly used die-casting materials in alloy die casting: aluminum alloy, zinc alloy and magnesium alloy, and explore how to choose the most suitable die-casting material according to specific needs.
1.Alloy die casting material: aluminum alloy
Aluminum alloy is one of the most widely used alloy die casting materials. Its unique properties make it occupy an important position in the automotive, aerospace, motorcycle and electronics industries.
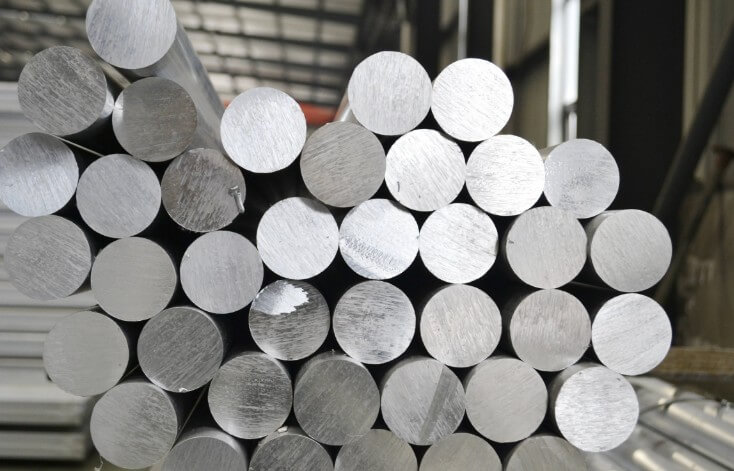
(1) Performance characteristics
1) Lightweight and high strength:
The density of aluminum alloy is about one-third of that of steel, but its specific strength and specific stiffness are higher, which makes it an ideal choice for reducing product weight.
2) Good thermal conductivity and electrical conductivity:
Aluminum alloy has excellent thermal and electrical conductivity and is suitable for manufacturing products that require good heat dissipation or electrical conductivity.
3) Good anti-oxidation and corrosion performance:
A dense aluminum oxide film is easily formed on the aluminum surface, which can effectively prevent further oxidation and has good corrosion resistance.
4) Excellent die-casting performance:
Aluminum alloy has good fluidity, simple die-casting process, good forming and cutting performance, excellent mechanical properties and corrosion resistance, and is the most promising alloy die casting material to replace steel castings.
5) Stable high and low temperature performance:
Aluminum alloy maintains good mechanical properties in both high and low temperature environments and is suitable for extreme conditions.
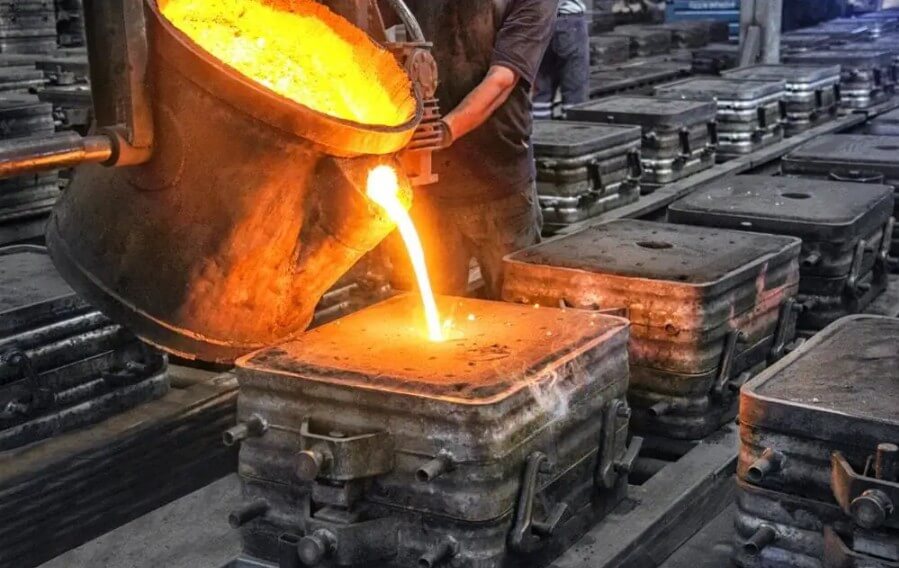
(2) Commonly used aluminum alloy grades
1) ADC12:
It has good fluidity and corrosion resistance and is suitable for the manufacture of complex structural parts and body shells.
2) A380:
It has high strength and heat resistance and is widely used in automotive parts and mechanical structural parts.
3) A360:
It has good mechanical properties and surface quality and is commonly used in the automotive industry and the manufacture of structural parts.
4) YL113:
High strength and easy processing, low cost, suitable for aerospace and automobile engine fields.
(3) Scope of application
Aluminum alloy is suitable for manufacturing parts with complex structure, light weight and high strength requirements, such as automobile engine block, cylinder head, wheel hub, aerospace structural parts, electronic product housing, etc.
2.Alloy die casting material: zinc alloy
Zinc alloy occupies an important position in the die-casting industry due to its low cost, good plasticity and fast forming speed.
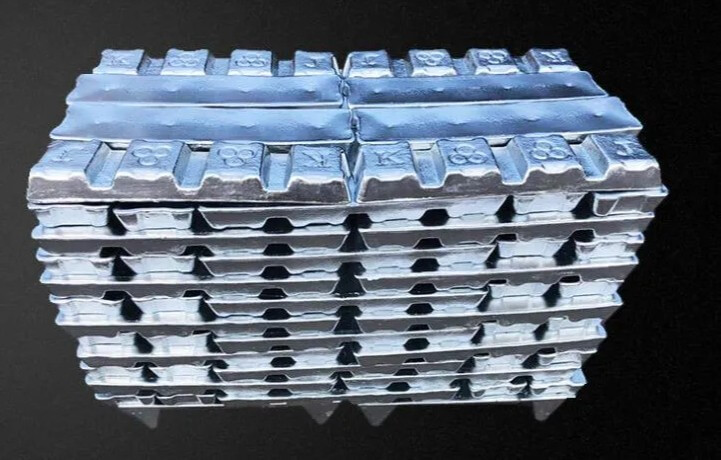
(1) Performance characteristics
1) Low cost:
Zinc alloy is relatively cheap and suitable for mass production.
2) Good formability:
Zinc alloy has good fluidity and is easy to form parts with complex shapes.
3) Good mechanical properties:
Zinc alloy has certain strength and hardness and can meet general use requirements.
4) Easy to process:
Zinc alloy has good cutting performance and is suitable for various mechanical processing.
5) Good wear resistance:
Zinc alloy has certain wear resistance and can extend the service life of the mold.
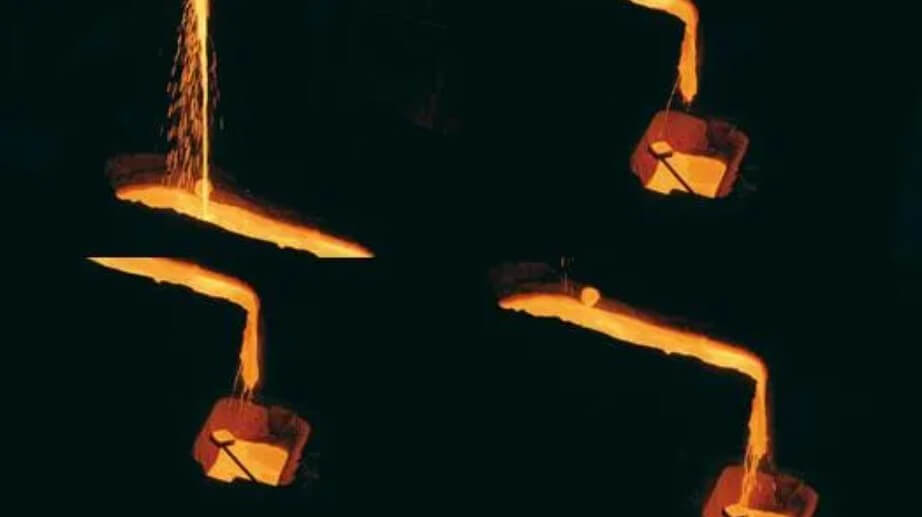
(2) Common zinc alloy grades
1) Zamak3:
It has good fluidity and mechanical properties, and is suitable for manufacturing toys and lamps that do not require high strength.
2) Zamak5:
It has excellent fluidity and mechanical properties, and is used in castings that require strength, such as automotive parts and electromechanical parts.
3) ZA8:
It has good fluidity and dimensional stability, and is suitable for die-casting small-sized and high-precision workpieces.
4) Superloy:
It has the best fluidity and is suitable for die-casting thin-walled, large-sized, high-precision, and complex-shaped workpieces.
(3) Scope of application
Zinc alloy is suitable for manufacturing parts with low weight requirements, complex shapes, and large batches, such as toys, decorative parts, and lamp housings.
3.Alloy die casting materials: magnesium alloy
Magnesium alloy is the lightest metal structural material with excellent shock absorption, thermal conductivity, and electromagnetic shielding properties. In recent years, it has been widely used in aerospace, automotive, electronics and other industries.
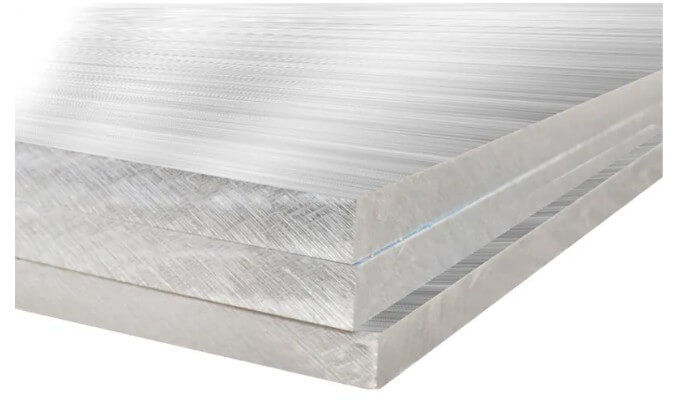
(1) Performance characteristics
1) Lightweight:
The density of magnesium alloy is about two-thirds of that of aluminum alloy and one-quarter of that of steel, making it the lightest metal structural material.
2) Good shock absorption:
Magnesium alloy has good shock absorption performance and is suitable for manufacturing parts that require shock absorption.
3) Excellent thermal conductivity:
The thermal conductivity of magnesium alloy is better than that of aluminum alloy and zinc alloy, and is suitable for manufacturing products that require good heat dissipation performance.
4) Good electromagnetic shielding performance:
Magnesium alloy has good electromagnetic shielding performance and is suitable for manufacturing electronic product housings.
5) Good formability:
Magnesium alloy has good fluidity and is easy to form parts with complex shapes.
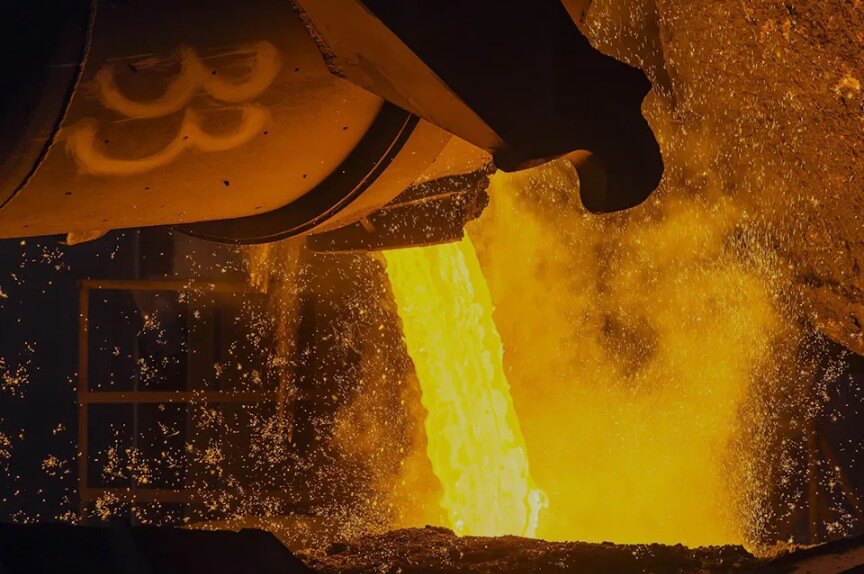
(2) Common magnesium alloy grades
1) AZ91D:
It has good mechanical properties and casting properties and is widely used in automobiles and electronic products.
2) AM60B:
It has good toughness and impact resistance and is often used to manufacture structural parts that require high safety.
3) AS41B:
With high strength and heat resistance, it is suitable for mechanical parts working in high temperature environments.
(3) Scope of application
Magnesium alloy is suitable for manufacturing parts with extremely high weight requirements, high shock absorption requirements, and good heat dissipation performance, such as laptop computer shells, mobile phone shells, car steering wheels, etc.
4.How to choose the most suitable alloy die casting material
The following factors need to be considered comprehensively when choosing the appropriate alloy die casting material:
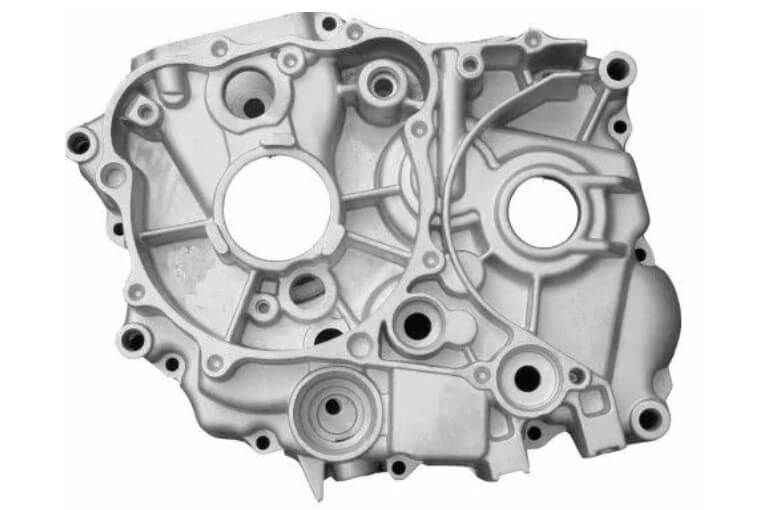
(1) Product performance
1) Strength requirements:
If the product requires higher strength, aluminum alloy or magnesium alloy can be selected. Aluminum alloy has higher strength and is suitable for manufacturing parts with complex structures; magnesium alloy has slightly lower strength than aluminum alloy, but is lighter in weight and is suitable for manufacturing parts with extremely high weight requirements.
2) Heat resistance requirements:
If the product needs to work in a high temperature environment, aluminum alloy or magnesium alloy can be selected. Both materials have good heat resistance and can maintain good mechanical properties at high temperatures.
3) Conductivity requirements:
If the product requires good conductivity, aluminum alloy can be selected. The conductivity of aluminum alloy is better than that of zinc alloy and magnesium alloy.
(2) Shock absorption requirements:
If the product requires good shock absorption performance, magnesium alloy can be selected. The shock absorption performance of magnesium alloy is better than that of aluminum alloy and zinc alloy.
(3) Process performance
1) Fluidity:
Zinc alloy has the best fluidity and is easy to form parts with complex shapes; aluminum alloy and magnesium alloy have the second best fluidity, but can also meet the general alloy die casting requirements.
2) Cutting performance:
Aluminum alloy and zinc alloy have good cutting performance and are easy to perform various mechanical processing; magnesium alloy has slightly worse cutting performance, but can also be processed by selecting appropriate processing parameters.
(4) Production conditions
1) Production batch:
If the product is mass-produced, aluminum alloy or zinc alloy can be selected. The casting process of these two alloy die casting materials is simple, the forming speed is fast, and they are suitable for mass production.
2) Mold life:
Aluminum alloy and magnesium alloy have a longer mold life and are suitable for long-term production; zinc alloy has a relatively short mold life, but the cost is lower, which is suitable for short-term or small and medium-sized batch production.
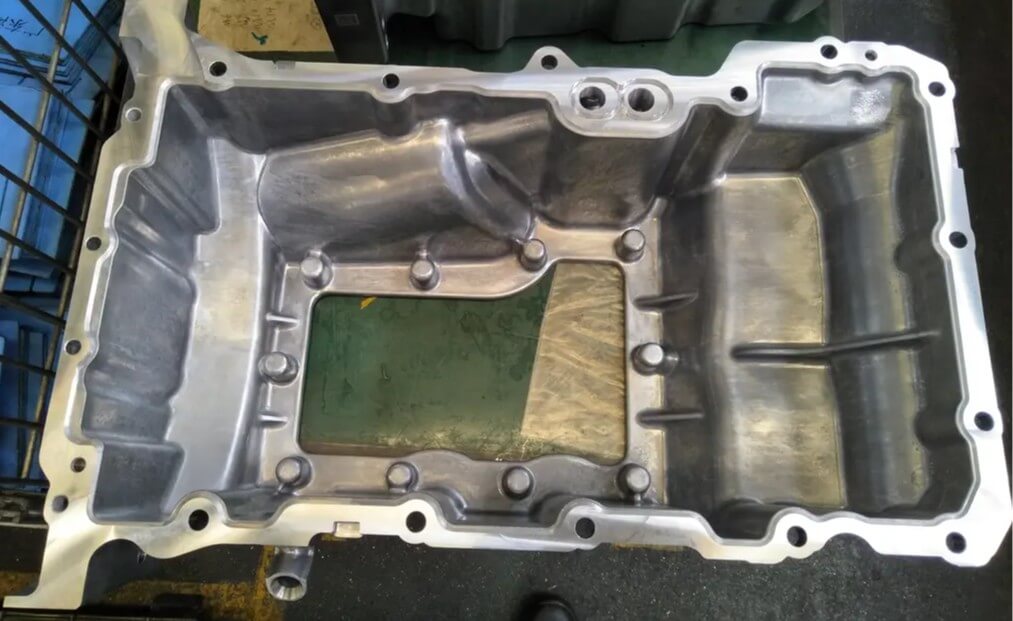
(5) Economy
1) Material cost:
Zinc alloy has the lowest cost and is suitable for projects with limited budgets; aluminum alloy has moderate cost and is widely used in various industries; magnesium alloy has the highest cost, but has excellent performance and is suitable for high-end products.
2) Processing cost:
The processing cost of aluminum alloy and magnesium alloy is high, requiring higher processing equipment and processes; zinc alloy has lower processing cost and is easy to process.
5.Summary
Selecting the right alloy die casting material is the key to ensuring product quality and production efficiency. Aluminum alloy, zinc alloy and magnesium alloy each have their own unique performance characteristics and are suitable for different application scenarios.
When selecting alloy die casting materials, it is necessary to comprehensively consider factors such as product performance, process performance, production conditions and economy, and select the most suitable material to achieve the best production effect and economic benefits.