High-performance aluminium die casting components: analysis of key factors for design optimization and strength enhancement
With the continuous advancement of modern industrial technology, aluminium die casting components have been widely used in the fields of automobiles, aerospace, electronic equipment and communications due to their light weight, high strength, good thermal conductivity and corrosion resistance.
In order to further improve the performance of aluminium die casting components, optimizing design and improving strength are particularly important. This article will deeply analyze the key factors affecting high-performance aluminium die casting components from the aspects of material selection, structural design, die-casting process and heat treatment.
1.What are the application fields of aluminium die casting components? What role do they play in them?
Aluminium die casting components are widely used in many fields due to their light weight, high strength, good corrosion resistance and good thermal conductivity. The following are their main application fields and specific functions:
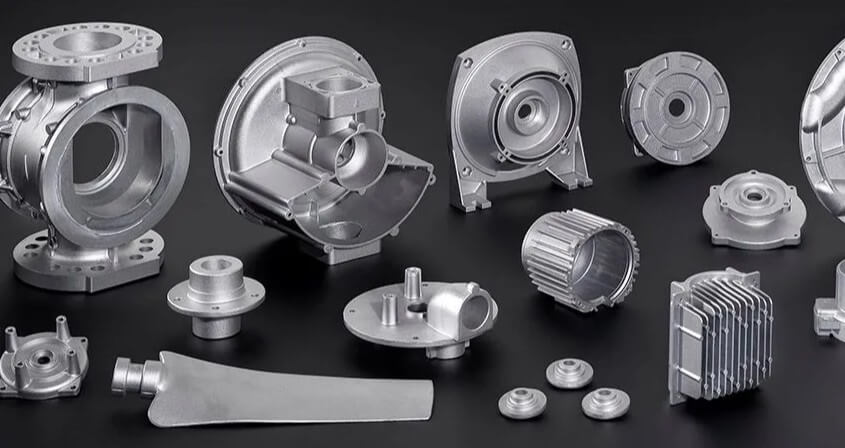
(1) Automobile industry
1) Parts:
Engine parts (such as engine block, oil pan, etc.), transmission system (such as transmission housing, clutch housing, etc.), suspension system (such as control arm, steering knuckle, etc.), chassis parts (subframe, shock tower, etc.), exterior decorative parts (front bumper, door, etc.).
2) Function:
Reduce vehicle weight, improve fuel efficiency, enhance safety performance, and improve handling stability.
(2) Electronic and communication equipment
1) Parts:
Casing, radiator, connector, socket, etc.
2) Function:
Protect electronic devices, improve equipment performance and stability, good electromagnetic shielding performance and thermal conductivity.
(3) Home appliances and electrical equipment
1) Parts:
Air conditioner casing, washing machine drum, refrigerator parts, TV bracket, etc.
2) Function:
Improve the texture and aesthetics of the product, while having good surface quality and appearance.
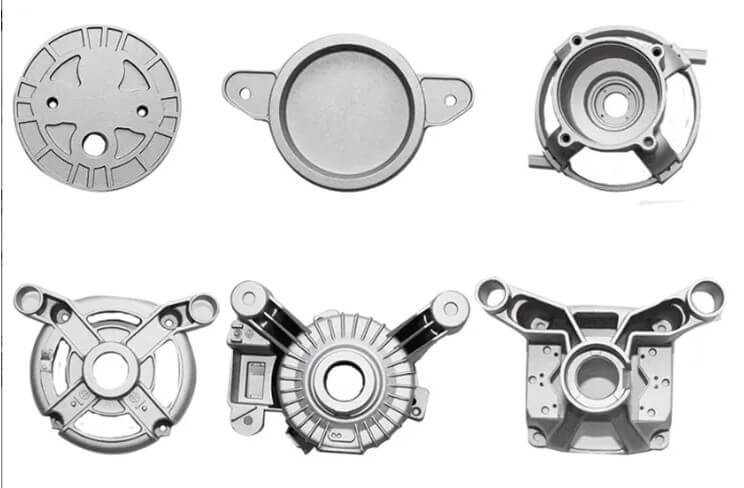
(4) Aerospace
1) Parts:
Structural parts of aircraft and spacecraft.
2) Function:
Meet the requirements of high strength and lightweight, good corrosion resistance and easy processing.
(5) Engineering machinery
1) Parts:
Structural parts of heavy equipment such as excavators and bulldozers.
2) Function:
Improve the strength and durability of the equipment, and meet environmental protection and safety requirements.
(6) Construction and decoration fields
1) Parts:
Window frames, door and window accessories, interior decoration parts, etc.
2) Function:
Lightweight and weather-resistant, meeting the strength and aesthetic requirements of construction and decoration materials.
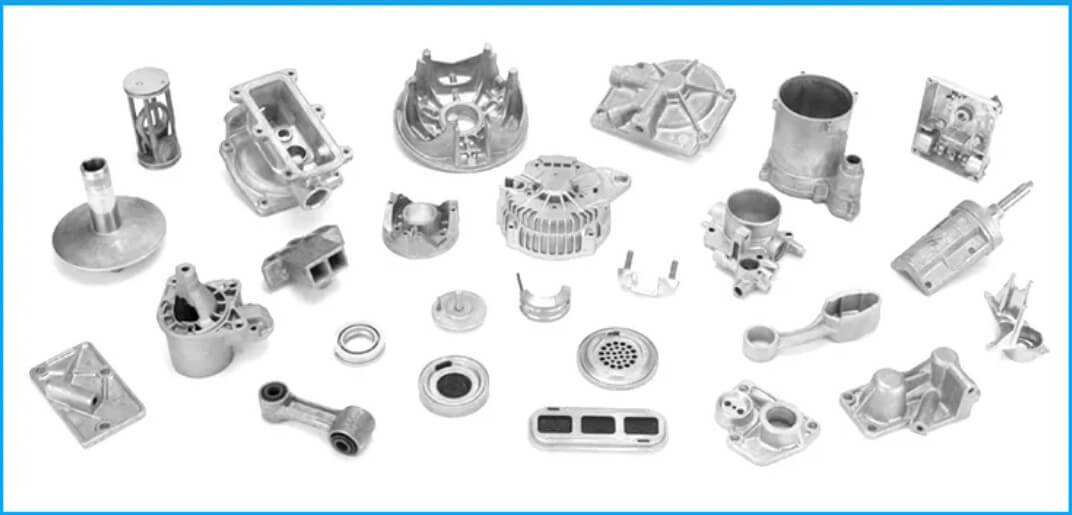
Summary:
The above lists some of the main application areas of aluminium die casting components, which can be seen as a wide variety. Because of this, it is crucial to improve the performance of its parts. This can not only extend the service life of the product, but also improve the safety and reliability of the product, and meet the evolving industrial needs and technical standards. The following will analyze in detail the key factors that create high-performance aluminium die casting components.
2.Material selection: Laying the foundation for performance
The performance of high-performance aluminium die casting components depends first on the selected aluminum alloy material. There are many types of aluminum alloys, and different alloy compositions have a significant impact on their mechanical properties and processing properties. The following are several commonly used high-performance aluminum alloys and their characteristics:
(1) Al-Si alloys:
It has good casting properties and thermal cracking resistance, and is suitable for manufacturing parts with complex shapes. By adding appropriate amounts of Mg and Cu, its strength and toughness can be significantly improved.
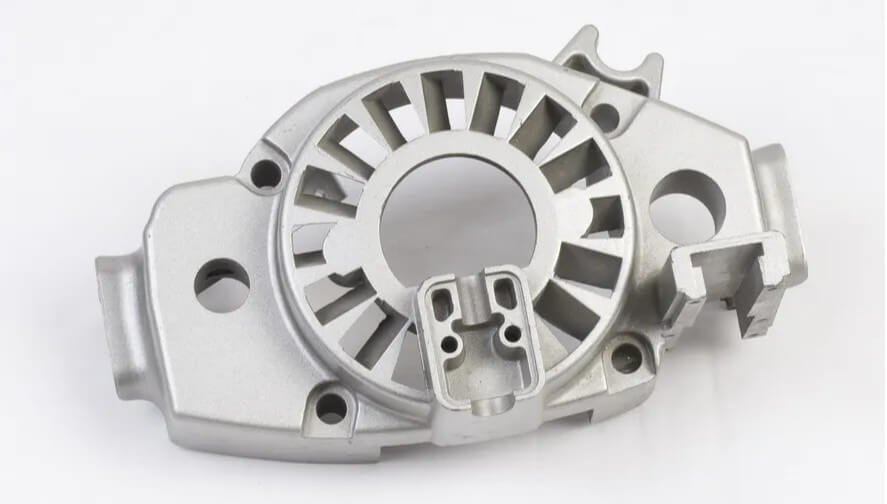
(2) Al-Mg alloys:
They have excellent corrosion resistance and medium strength, and are suitable for parts with high corrosion resistance requirements. However, their casting performance is relatively poor, which needs to be compensated by optimizing the casting process.
(3) Al-Zn alloys:
They have high strength and good plasticity, but poor corrosion resistance. By adding appropriate amounts of Mg and Cu, their strength and corrosion resistance can be further improved, making them suitable for manufacturing high-strength structural parts.
When selecting aluminum alloy materials, the most suitable alloy material should be selected based on the use environment and performance requirements of the parts, taking into account factors such as mechanical properties, casting properties, corrosion resistance and cost.
3.Structural design of aluminium die casting components: optimizing mechanical properties
Reasonable structural design is the key to improving the strength of aluminium die casting components. The following are several key factors for optimizing structural design:
(1) Wall thickness design:
Too thick a wall will increase material consumption and production costs, and may also cause defects such as shrinkage cavities and shrinkage. Too thin a wall will affect the strength and stiffness of the parts. Therefore, the wall thickness should be reasonably designed according to the stress conditions and functional requirements of the components, and the wall thickness should be kept uniform as much as possible.
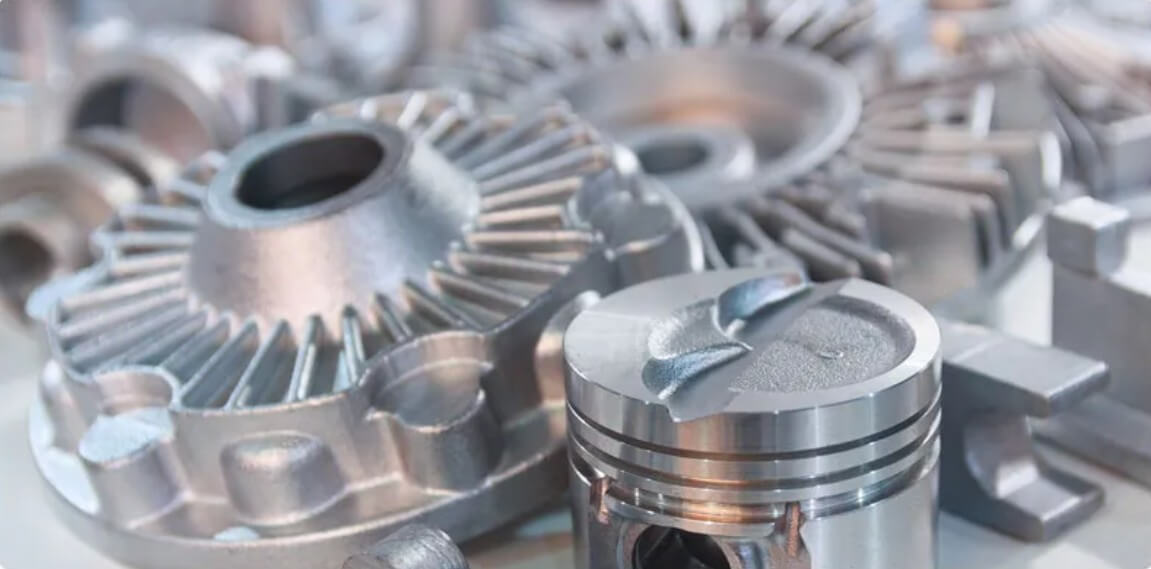
(2) Fillet and transition design:
In structural design, sharp edges and mutations should be avoided, and fillet and transition design should be adopted to reduce stress concentration and improve the fatigue resistance of components.
(3) Rib design:
Reasonable arrangement of ribs can significantly improve the stiffness and strength of components while reducing weight. The thickness and height of the ribs should be optimized according to the stress conditions of the components.
(4) Hole and slot design:
The location, size and shape of holes and slots have a significant impact on the strength and stiffness of components. When designing, holes and slots should be avoided as much as possible in high stress areas, and appropriate reinforcement measures should be taken.
4.Die casting process: ensure stable quality
The die casting process is an important factor affecting the performance of aluminum die casting components. The following are several key process parameters and their effects on component performance:
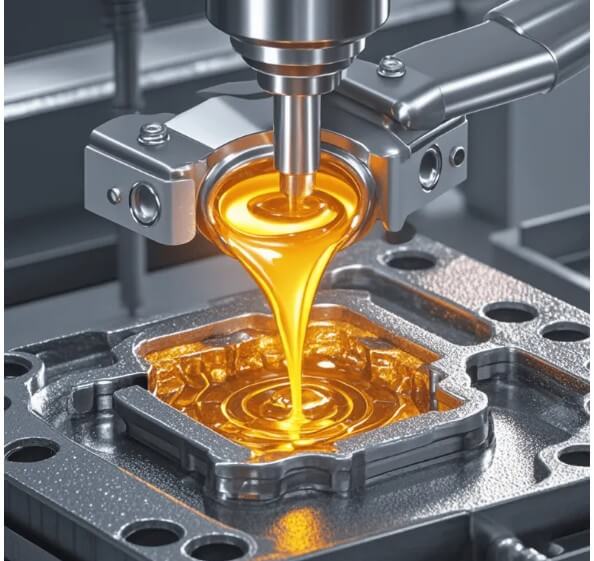
(1) Die casting temperature:
If the die-casting temperature is too high, it will lead to coarse grains and reduce the mechanical properties of the component; if the die-casting temperature is too low, it may cause defects such as poor filling and cold shut. Therefore, the die-casting temperature should be reasonably selected according to the characteristics of the aluminum alloy material and the structural characteristics of the component.
(2) Injection speed:
The injection speed determines the flow speed of the molten metal in the mold cavity. Too high an injection speed may cause gas entrainment and turbulence, resulting in defects such as pores and oxide inclusions; too low an injection speed may lead to insufficient filling. Therefore, the injection speed should be reasonably adjusted according to the structural complexity and wall thickness of the component.
(3) Holding time and pressure:
The holding time and pressure determine the density and mechanical properties of the component. Too short a holding time or insufficient pressure may lead to defects such as shrinkage and shrinkage; too long a holding time or too high a pressure may lead to internal stress and deformation. Therefore, the holding time and pressure should be reasonably selected according to the structural characteristics and wall thickness of the component.
5.Heat treatment: improving mechanical properties
Heat treatment is an important means to improve the mechanical properties of aluminium die casting components. The following are several commonly used heat treatment methods and their effects on part performance:
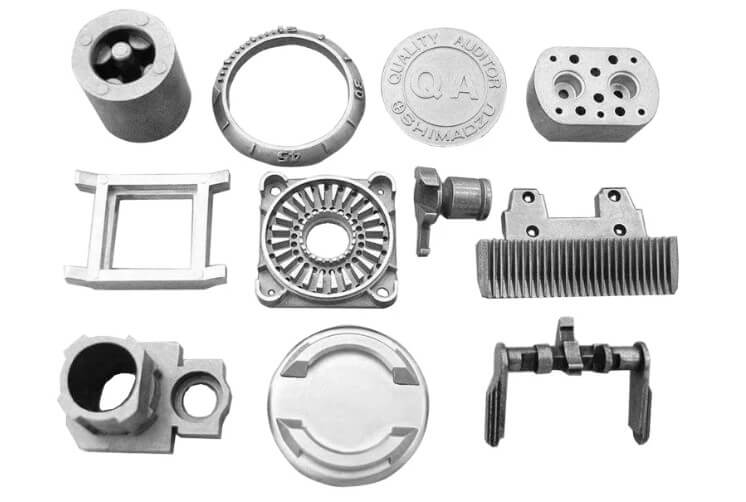
(1) Solution treatment:
The aluminium die casting components are heated to the solution temperature, kept at the temperature for a certain period of time, and then cooled rapidly to allow the alloy elements to fully dissolve into the matrix to form a supersaturated solid solution. Solution treatment can significantly improve the strength and hardness of the parts.
(2) Aging treatment:
The parts after solution treatment are placed at room temperature or low temperature for a period of time to decompose the supersaturated solid solution and precipitate the strengthening phase, further improving the strength and hardness of the parts. The time and temperature of aging treatment should be selected according to the characteristics and performance requirements of the alloy material.
(3) Regression treatment:
The parts after aging treatment are heated to the regression temperature, kept at the temperature for a certain period of time, and then cooled rapidly to allow the strengthening phase to dissolve into the matrix again and restore the plasticity and toughness of the parts. Regression treatment is often used for parts that require multiple deformations.
6.Surface treatment of aluminium die casting components: enhancing corrosion resistance and aesthetics
Surface treatment can not only enhance the corrosion resistance of aluminium die casting components, but also improve their aesthetics and wear resistance. The following are several commonly used surface treatment methods:
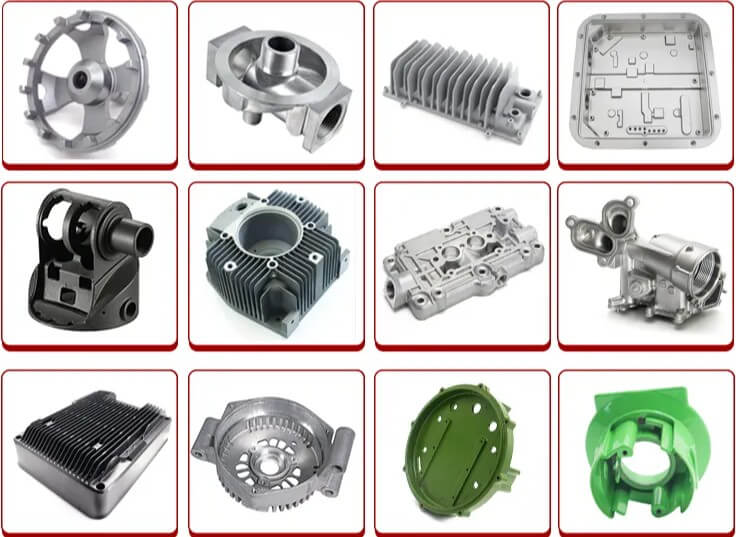
(1) Anodizing:
A dense oxide film is formed on the aluminum surface through electrolysis, which significantly improves the corrosion resistance and wear resistance of the parts. The color of the anodized film can be adjusted as needed and has good decorative properties.
(2) Electroplating:
Electroplasticizing a layer of metal, such as zinc, nickel or chromium, on the aluminum surface can further improve the corrosion resistance and wear resistance of the parts. The thickness and performance of the electroplating layer should be selected according to the use environment and performance requirements of the parts.
(3) Spraying:
Spraying a layer of organic coating, such as paint or powder coating, on the aluminum surface can significantly improve the corrosion resistance and aesthetics of the parts. The thickness and performance of the spray coating should be selected according to the use environment and decorative requirements of the parts.
7.Summary
In summary, the optimization design and strength improvement of high-performance aluminium die casting components is a systematic project, which requires comprehensive consideration and optimization from multiple aspects such as material selection, structural design, die-casting process and heat treatment. Through scientific and reasonable design and manufacturing, aluminium die casting components with excellent performance and stable quality can be produced to meet the diverse needs of modern industry.