Aluminum engine block castings: a classic example of lightweighting in the modern automobile industry
In the modern automobile industry, lightweighting has become a key factor in improving fuel efficiency, reducing emissions and enhancing vehicle performance.
As a representative of lightweighting technology, aluminum engine blocks occupy an important position in automobile engine manufacturing with their excellent performance. This article will elaborate on the advantages, manufacturing process and other aspects of aluminum engine block castings.
1.Advantages of aluminum engine block castings
(1) Significant lightweighting effect
The density of aluminum is about one-third of that of steel. Using aluminum cylinder blocks can significantly reduce the weight of the engine. Reducing the weight of the engine not only helps to improve the acceleration performance and handling flexibility of the vehicle, but also effectively reduces the fuel consumption and carbon dioxide emissions of the vehicle.
Research shows that for every 10% weight reduction of a car, fuel efficiency can be increased by 6% to 8%. Therefore, aluminum engine blocks have significant advantages in energy saving and emission reduction.
(2) Good thermal conductivity
The thermal conductivity of aluminum is about three times that of steel, which makes the aluminum cylinder block have a faster heat dissipation speed. Good thermal conductivity helps keep the engine within a suitable operating temperature range and improves the reliability and durability of the engine.
At the same time, rapid heat dissipation can also reduce the heat loss of the engine, improve thermal efficiency, and further improve fuel economy.
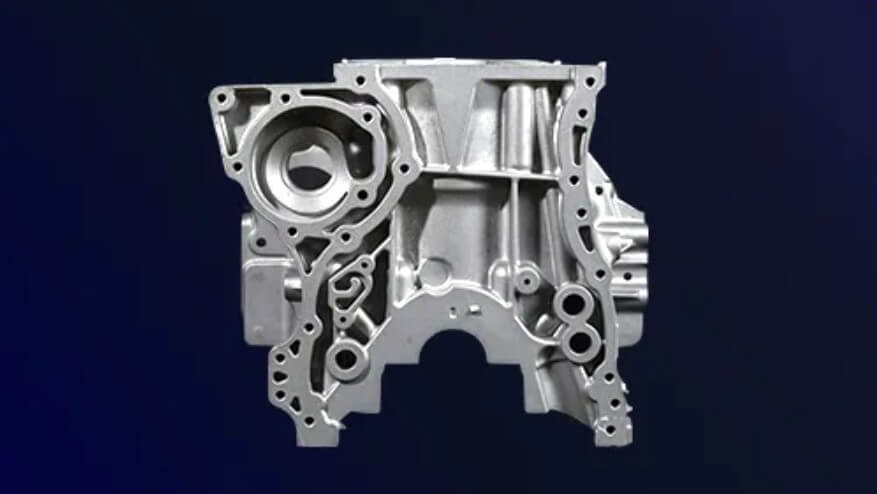
(3) Excellent corrosion resistance
Aluminum has good corrosion resistance in the atmosphere, and a dense oxide film will naturally form on its surface, which effectively prevents the erosion of corrosive media. In contrast, steel is prone to rust in a humid environment and requires additional anti-corrosion treatment.
The corrosion resistance of the aluminum engine block not only extends the service life of the engine, but also reduces maintenance costs.
(4) Good machinability and recyclability
Aluminum has good machinability and can be processed through a variety of processes such as casting and machining to meet the needs of different engine designs.
In addition, aluminum is a recyclable material with a high recycling rate and low impact on the environment. The use of aluminum engine blocks is in line with the concept of sustainable development.
2.Application of aluminum alloy materials in engine cylinder blocks
(1) Common types of aluminum alloys
The aluminum alloy materials used for engine cylinder blocks mainly include Al-Si series, Al-Cu series and Al-Mg series. Among them, Al-Si series aluminum alloys are widely used in the manufacture of automobile engine cylinder blocks due to their good casting performance and wear resistance. For example, ZL104 alloy is widely used in the production of aluminum engine blocks at home and abroad.
(2) Selection criteria of aluminum alloys
When selecting aluminum alloy materials suitable for engine blocks, factors such as mechanical properties, heat resistance, wear resistance and cost should be considered. In addition, the machinability and recyclability of the alloy are also important considerations. For example, when selecting aluminum alloy materials, it is necessary to consider their performance at high temperatures, as well as their fluidity and formability during casting and processing.
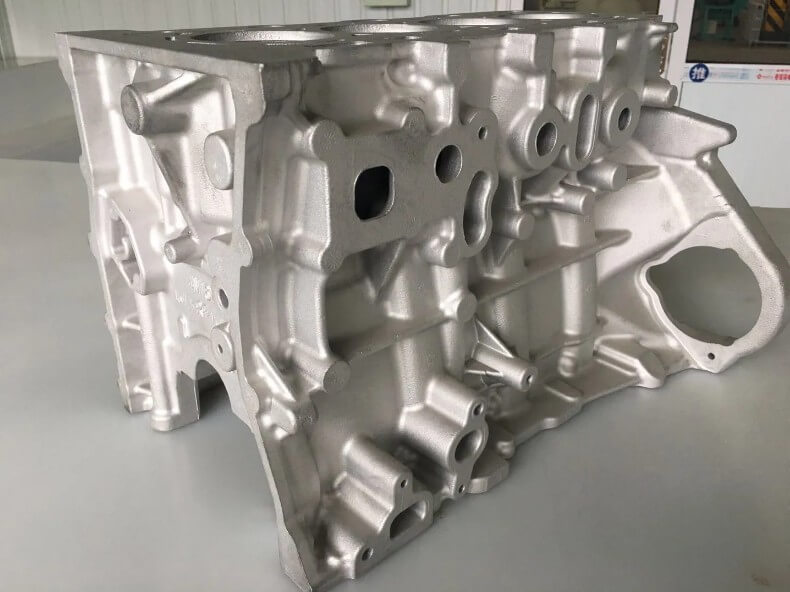
3.Manufacturing process and advantages of aluminum aluminum engine block castings
As the core component of the engine, the cylinder block has a direct impact on the performance and reliability of the engine. The following are the principles and advantages of three commonly used aluminum engine block manufacturing processes, including low-pressure casting technology, metal mold gravity casting and die casting technology.
(1) Low-pressure casting technology
1) Process principle
Low-pressure casting is to introduce dry compressed air into a sealed crucible. Under the action of gas pressure, the liquid metal rises along the riser and enters the mold cavity smoothly through the gate. The gas pressure on the liquid surface in the crucible is maintained until the casting is completely solidified. Then the liquid surface pressure is released, and the unsolidified metal liquid flows back to the crucible. Finally, the mold is opened and the casting is ejected.
2) Process advantages
● Smooth filling:
The metal liquid fills the mold at a lower pressure, and the speed is controllable, which reduces pores and slag inclusion defects and improves the quality of the casting.
● Good shrinkage compensation effect:
Continuous pressurization during solidification is conducive to shrinkage compensation of the casting, reduces shrinkage cavities and shrinkage, and improves the density and mechanical properties of the casting.
● High process yield:
The utilization rate of the metal liquid is high, which reduces metal waste.
● Wide application range:
Applicable to various alloys, especially aluminum alloys, and widely used in the production of complex castings such as automobile wheels and aluminum engine blocks.
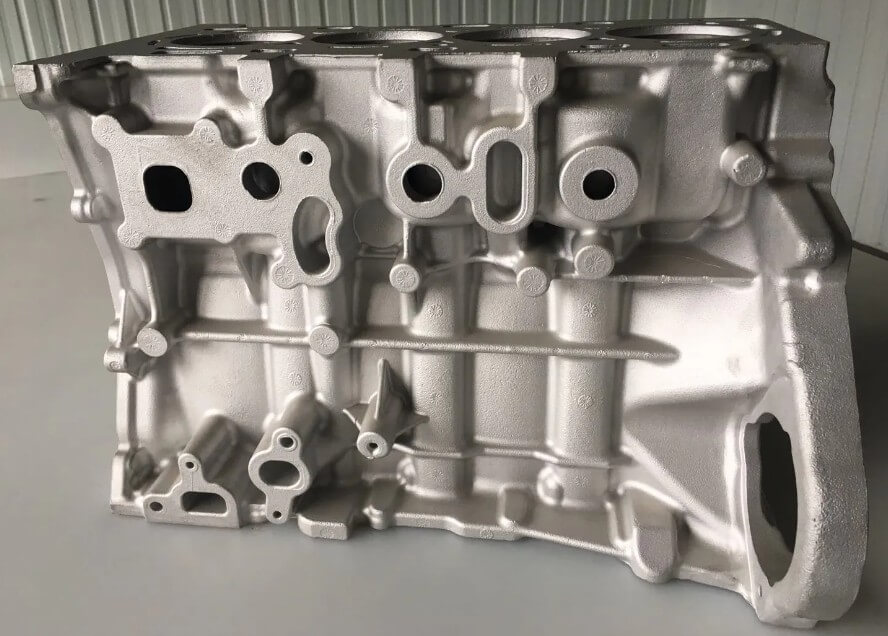
(2) Metal mold gravity casting
1) Process principle
Metal mold gravity casting is to pour aluminum molten metal into the preheated metal mold cavity, use gravity to fill the mold cavity with molten metal, and cool and solidify in the mold cavity to form a casting.
2) Process advantages
● High casting precision:
The thermal conductivity of the metal mold is high, the cooling rate is fast, and the dimensional accuracy and surface quality of the casting are better than sand casting.
● High production efficiency:
The metal mold can be reused, the production cycle is short, and it is suitable for mass production.
● Good mechanical properties of the casting:
The cooling rate of the metal mold is fast, the grain of the casting is refined, and the mechanical properties are better than sand casting.
● Simple process:
No complex molds and equipment are required, and the investment cost is low.
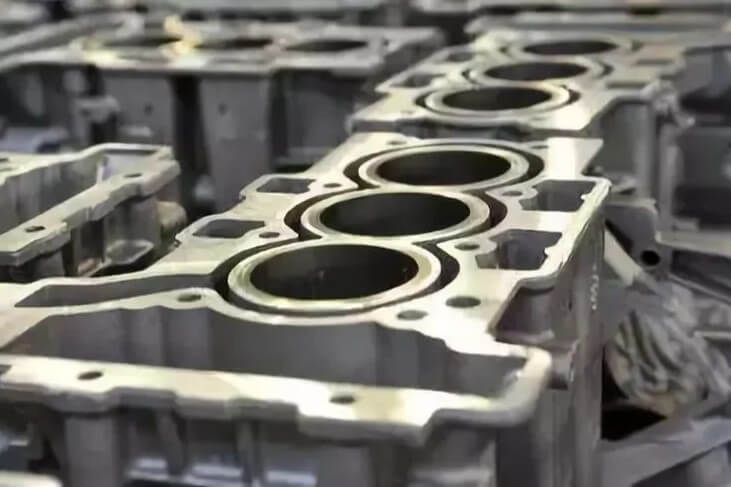
(3) Die-casting process
1) Process principle
Die-casting is to quickly press molten aluminum metal into the metal mold cavity under high pressure, and cool and solidify under pressure to form a casting.
2) Process advantages
● High production efficiency:
The die-casting speed is fast, the molding cycle is short, and it is suitable for mass production.
● High casting precision:
The dimensional accuracy and surface quality of die-castings are very high, which can meet the requirements of less cutting or no cutting.
● Complex casting structure:
It can produce castings with complex shapes and thin walls to meet various structural design requirements.
● Excellent mechanical properties:
The structure of die-castings is dense, and the mechanical properties are better than other casting methods.
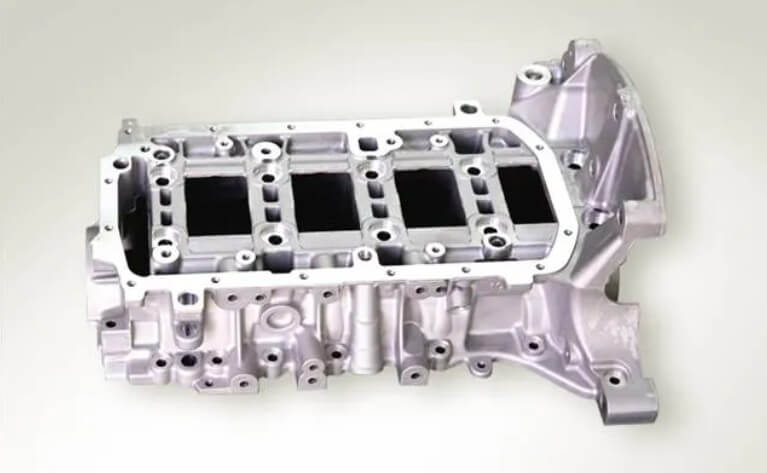
4.Technical challenges and solutions for aluminum engine block
(1) Shrinkage and pore problems
Shrinkage and pores are common problems in aluminum engine block castings. These defects will affect the structural integrity and mechanical properties of the castings.
To solve these problems, the casting process parameters can be optimized, such as controlling the pouring speed and temperature, and using high-quality aluminum alloy raw materials. In addition, post-treatment processes such as heat treatment can also help reduce these defects.
For example, in the production process of aluminum alloy cylinder heads, the quality of castings can be significantly improved by controlling the gas content and temperature of the aluminum liquid.
(2) Heat treatment process
Heat treatment is one of the key processes to improve the performance of aluminum engine blocks. Through proper heat treatment, the microstructure of the alloy can be improved, and its mechanical properties and heat resistance can be improved.
For example, the T6 heat treatment process is commonly used for Al-Si aluminum alloys. Through solution treatment and aging treatment, the strength and hardness of the alloy can be significantly improved.
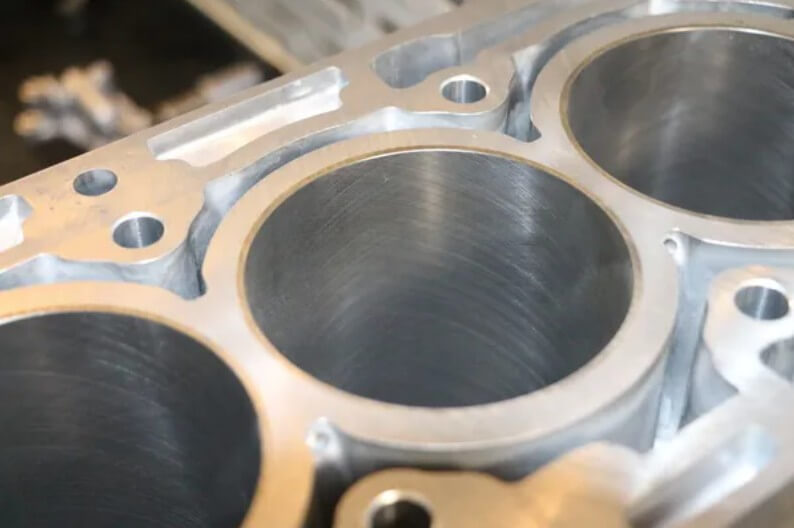
(3) Surface treatment technology
In order to improve the wear resistance and corrosion resistance of aluminum engine blocks, surface treatment technologies such as physical vapor deposition (PVD) and hard chrome plating are widely used. These technologies can significantly enhance the surface performance of the cylinder block without adding too much weight.
For example, the application of hard chrome plating on engine parts effectively improves the durability and reliability of aluminum cylinder blocks.
5.Summary
In short, aluminum engine block castings have been widely used in the modern automobile industry due to the advantages of aluminum materials such as lightweight, good thermal conductivity, corrosion resistance, machinability and recyclability, as well as the advantages of high casting precision, high production efficiency, ability to meet complex structures and good casting mechanical properties.
What do you think?
[…] with aluminum alloy engine blocks, cast iron engine blocks are significantly heavier, which increases the weight of the vehicle, […]
[…] alloy is about 2.7 g/cm³, which is much lower than the 7.8 g/cm³ of cast iron. Therefore, aluminum alloy engine blocks are […]