The perfect combination of fabrication and quenching: creating high-performance metal workpieces
Fabrication and quenching technology plays an indispensable role in industrial production. Manufacturing technology involves the process of converting raw materials into final products through various processing methods, while quenching technology is an important heat treatment process that changes the physical and chemical properties of materials through rapid cooling to improve their hardness and durability. The combination of fabrication and quenching technologies plays a vital role in improving product performance and extending their service life.
This paper aims to comprehensively explore the basic principles, application areas and interaction between fabrication and quenching technology. The following is a detailed analysis:
1.Overview of fabrication technology
(1) Traditional fabrication technology
Traditional fabrication technology mainly includes forging, casting and cutting processes.
Forging is a process that deforms metal by applying external force to change its physical properties. It is often used to manufacture mechanical parts and tools.
Casting is a method of pouring liquid metal into a mold and cooling and solidifying it to form the desired shape. It is suitable for producing parts with complex shapes.
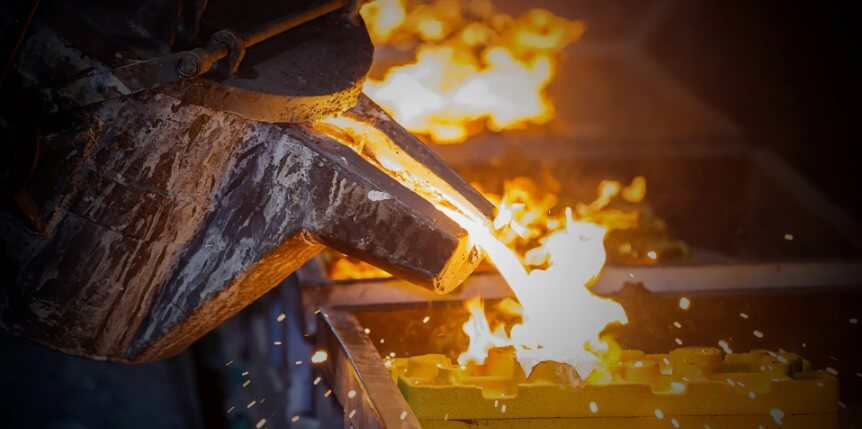
Cutting is a processing method that removes material by a tool to obtain precise size and shape. It is widely used in the field of mechanical processing.
(2) Modern fabrication technology
With the development of science and technology, modern fabrication technologies such as additive manufacturing and high-precision machining have gradually become an important part of the manufacturing industry.
Additive manufacturing, also known as 3D printing, is a technology that builds objects by stacking materials layer by layer. It is characterized by high efficiency, flexibility and high material utilization.
High-precision machining technology achieves micron-level machining accuracy through high-precision machine tools and advanced control technology, and is suitable for manufacturing high-precision parts and equipment.
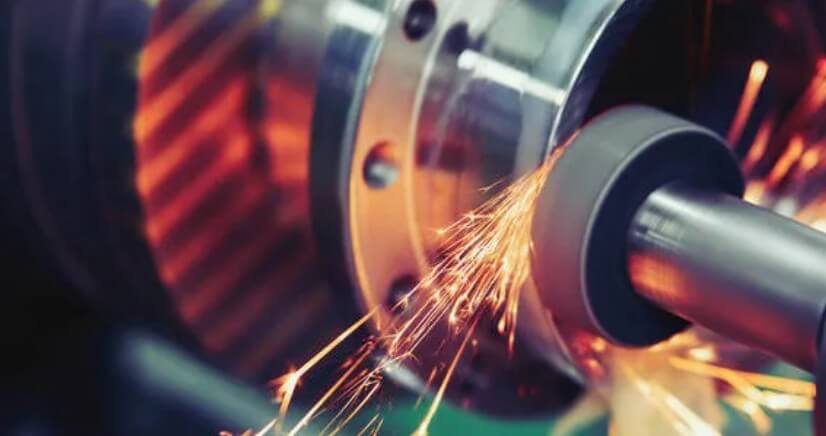
2.Principle and classification of quenching process
(1) Quenching principle
Quenching is a heat treatment process in which a metal is heated to a certain temperature, kept warm for a period of time, and then rapidly cooled. Its purpose is to improve the hardness, strength and wear resistance of the metal by changing its internal structure.
During the heating process, the atomic movement inside the metal intensifies and the structure changes; in the rapid cooling process, the atoms do not have time to rearrange themselves, forming hard and brittle structures such as martensite, thereby improving the performance of the metal.
(2) Quenching classification
According to different cooling media and cooling speeds, quenching processes can be divided into many types. Water quenching is one of the most common quenching methods. It has the advantages of fast cooling speed and low cost. It can obtain higher hardness and strength, but it is easy to cause deformation and cracking of the workpiece. It is suitable for carbon steel and low alloy steel.
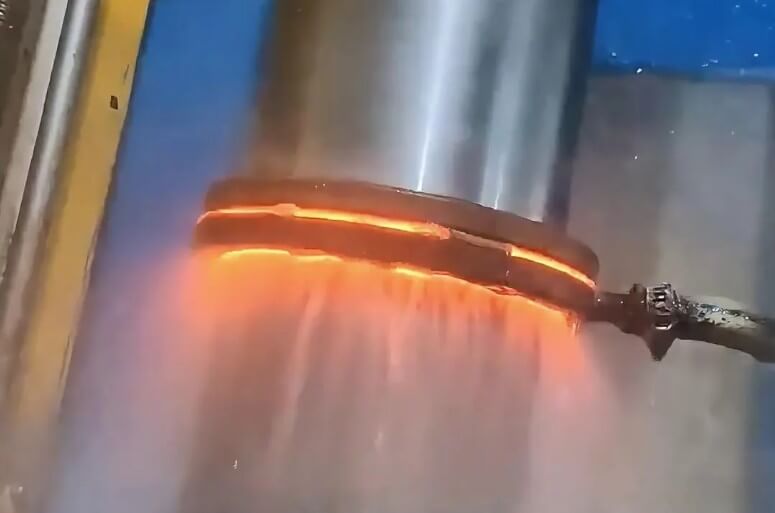
Oil quenching is relatively mild and has a slower cooling speed. It can reduce the risk of quenching cracks. It is suitable for high alloy steel and tool steel as well as some workpieces with high deformation requirements.
Gas quenching achieves precise cooling speed control by controlling the flow rate and temperature of the gas. It is suitable for heat treatment of special materials or high-precision parts, such as high-performance alloys in the aerospace field.
3.Close connection between fabrication and quenching
(1) The influence of manufacturing process on quenching
The choice of manufacturing process and processing quality directly affect the quenching effect. For example, in the machining process, if the surface roughness of the workpiece is too high, it is easy to cause stress concentration during quenching, increasing the risk of deformation and cracking of the workpiece. Therefore, in the manufacturing process, it is necessary to strictly control the processing quality to provide good conditions for the quenching process.
(2) The role of quenching in promoting manufacturing processes
The importance of quenching technology in modern manufacturing is self-evident. Its role in promoting manufacturing processes is mainly reflected in the following aspects:
1) Improving the mechanical properties of materials:
Quenching treatment can significantly improve the hardness, strength and wear resistance of metals, thereby extending the service life of products and improving their reliability.
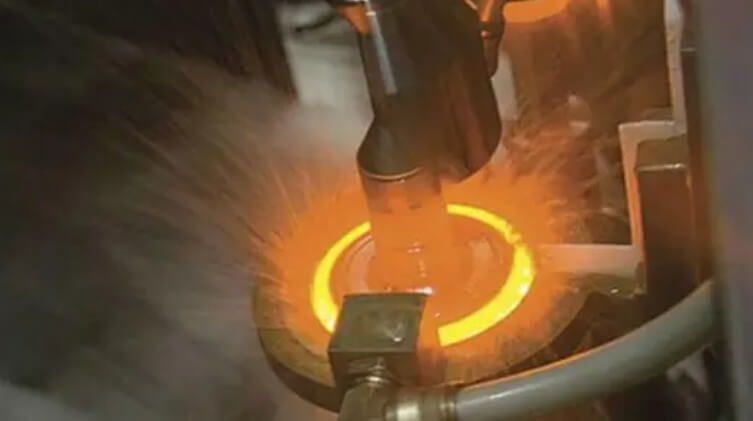
2) Expanding the application range of materials:
The quenching process enables metal materials with originally poor performance to obtain excellent mechanical properties through heat treatment, thereby expanding their application range. For example, some low-alloy steels can obtain similar performance to high-alloy steels through quenching treatment, reducing production costs.
3) Optimizing product design:
The quenching process can be combined with other manufacturing processes such as casting and cutting to form a comprehensive manufacturing solution. By rationally designing the process flow, the structure and performance of the product can be optimized and production efficiency can be improved.
4) Promoting the development of new materials:
With the advancement of science and technology, the requirements for material performance are becoming higher and higher. As an important means of modifying metal materials, quenching technology has promoted the research and development of new materials. For example, the emergence of some new high-temperature alloys is inseparable from the support of heat treatment processes such as quenching.
Fabrication and quenching are two closely related links in industrial production. Manufacturing gives metal shape, while quenching gives metal properties.
4.Fabrication and quenching: The process of quenching technology and its application in modern manufacturing
The core of the quenching process is to change the internal microstructure of the metal through high-temperature heating and rapid cooling. Specifically, the quenching process mainly includes the following steps:
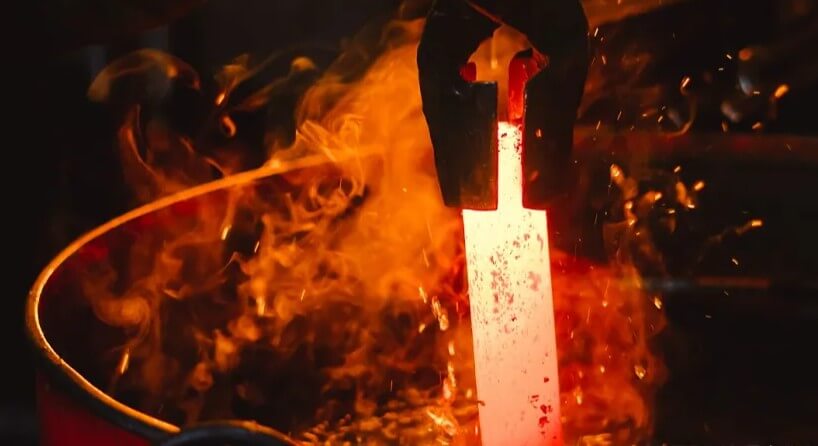
(1) Heating:
Heat the metal workpiece to above the critical temperature so that its internal structure is transformed into austenite. Austenite is a high-temperature phase with good plasticity and toughness.
(2) Insulation:
Keep above the critical temperature for a certain period of time to ensure that the internal structure of the metal workpiece is completely transformed into austenite.
(3) Cooling:
The heated metal workpiece is quickly placed in a coolant to cool it quickly. The faster the cooling rate, the faster the rate of transformation of austenite to martensite, thereby obtaining a metal structure with high hardness and high strength.
(4) Tempering:
Although the hardness of the quenched metal increases, its brittleness also increases. In order to reduce brittleness and improve toughness, tempering treatment is usually required. Tempering is the process of heating and keeping the quenched metal at a temperature below the critical temperature and then cooling it to room temperature.
In modern manufacturing, quenching technology has been widely used. From the production of automotive parts, aerospace medicine to molds, cutting tools, etc., fabrication and quenching technology are indispensable.
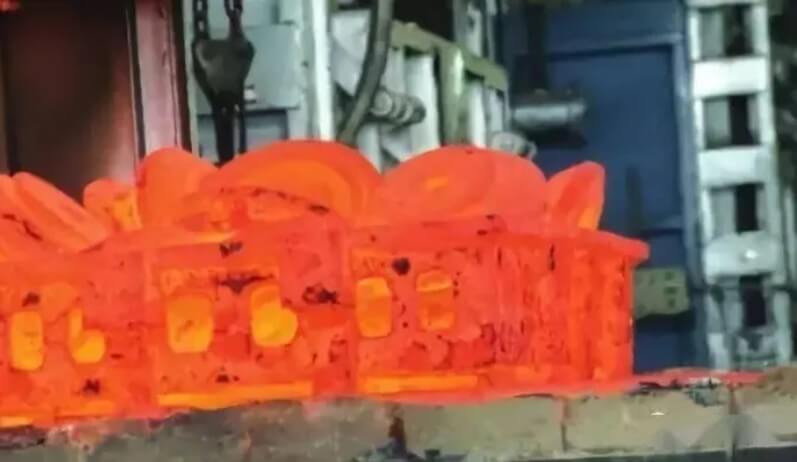
5.Fabrication and quenching: Examples of quenching applications in manufacturing
(1) Tool manufacturing
As an important tool in the manufacturing industry, the performance of cutting tools directly affects processing efficiency and product quality. In tool manufacturing, quenching technology is widely used. Through reasonable quenching treatment, the hardness of the tool can reach HRC60 or above, with excellent wear resistance and cutting performance.
For example, after high-temperature quenching and multiple tempering treatments, high-speed steel cutting tools not only have high hardness but also good toughness, which can meet the needs of high-speed cutting.
(2) Mold manufacturing
Molds are indispensable tools in industrial production. Their service life and precision have an important impact on product quality and production efficiency. Quenching technology also plays an important role in mold manufacturing. Through quenching treatment, the hardness and wear resistance of the mold can be improved and its service life can be extended.
For example, after low-temperature quenching and deep cryogenic treatment, the hardness of cold working die steel can reach HRC62 or above, which can meet the needs of high-strength stamping and forming processing.
(3) Automobile parts manufacturing
The manufacturing of automobile parts has very high requirements on the performance and precision of materials. Quenching technology is widely used in automobile parts manufacturing.
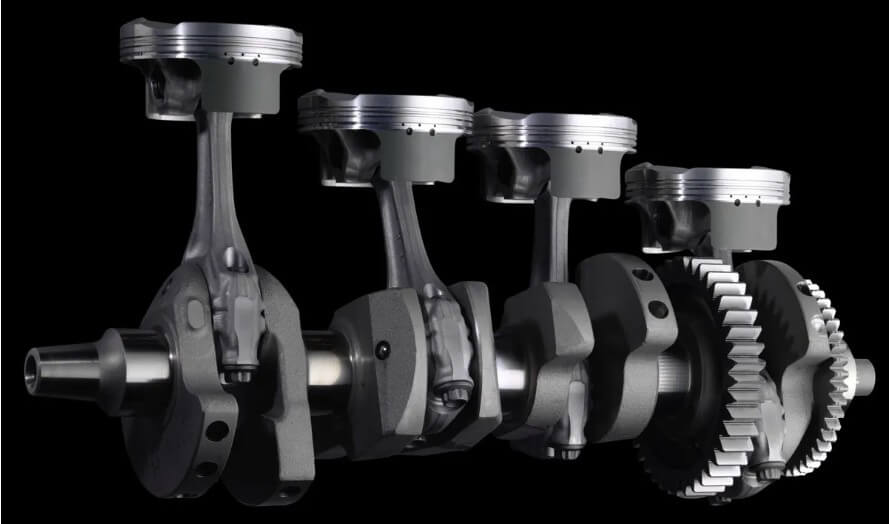
For example, after quenching treatment, the crankshaft and connecting rod of the automobile engine can improve their strength and fatigue life to ensure the stable operation of the engine; after quenching and tempering treatment, the springs in the automobile suspension system have good elasticity and toughness, which can provide a comfortable driving experience.
6.Summary
In the processing of metal materials, fabrication and quenching technology do not exist in isolation. The synergistic effect between the two can give full play to the potential of metals. Therefore, in order to create high-performance metal workpieces, the perfect combination of fabrication and quenching is crucial. The two complement each other and jointly determine the final performance of the workpiece.