Effect of liquid argon stainless steel quenching on material structure and properties
The quenching treatment of stainless steel is a key process that changes its internal structure through rapid cooling, thereby improving the material’s hardness and wear resistance. As an efficient cooling medium, liquid argon is increasingly used in the quenching process of stainless steel due to its extremely low temperature and good heat conduction properties.
Therefore, the liquid argon stainless steel quenching process combines the advantages of both. It can not only significantly improve the performance of the material, but also effectively reduce the tendency of deformation and cracking during the quenching process, which is of great significance for improving product quality and reliability. This article will focus on the basic principles, process flow, effect evaluation after quenching, advantages and disadvantages, and application field analysis of liquid argon stainless steel quenching to explore the specific impact mechanism of liquid argon quenching on the structure and properties of stainless steel.
1.Definition and basic concepts of liquid argon stainless steel quenching
Liquid argon stainless steel quenching is a heat treatment process in which the stainless steel is heated to above the critical temperature, kept warm for a period of time, and then quickly immersed in liquid argon for cooling to obtain a martensite structure. Its purpose is to improve the hardness, strength and wear resistance of stainless steel while maintaining its good corrosion resistance. During the quenching process, the low temperature and rapid cooling capabilities of liquid argon can effectively inhibit the decomposition of austenite and promote the formation of martensite, thereby improving the mechanical properties of stainless steel.
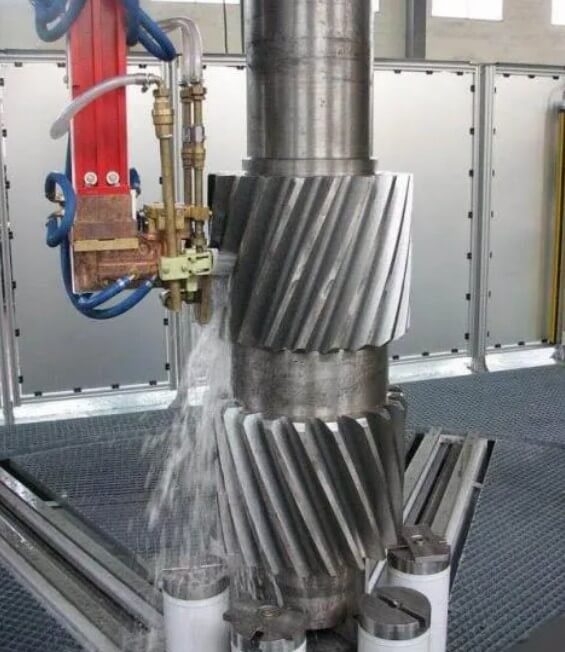
2.Basic principles of liquid argon stainless steel quenching
(1) Properties of liquid argon
Liquid argon, chemical symbol Ar, is a colorless and odorless inert gas. Under standard atmospheric pressure, the boiling point of liquid argon is -185.85°C, which is an extremely low temperature. This characteristic makes it an ideal medium for rapid cooling, which can effectively absorb heat and achieve rapid cooling of materials without chemical reaction with the material.
In addition, the good heat conduction properties of liquid argon ensure the uniformity of the cooling process, which is crucial to prevent deformation and cracks of the material during the quenching process.
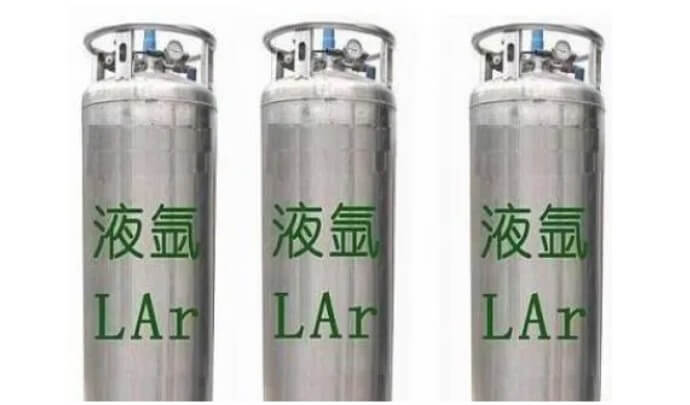
(2) Physical basis of quenching process
The liquid argon stainless steel quenching process involves heating the stainless steel to a certain temperature to transform its internal structure into austenite, and then cooling it rapidly to fix this high-temperature phase structure into martensite. This process significantly increases the hardness of the material. and intensity.
In liquid argon stainless steel quenching, the extremely low temperature of liquid argon can be used to achieve faster cooling rates than traditional quenching media such as water or oil. This rapid cooling helps form fine martensite grains, which improves the material’s mechanical properties. However, rapid cooling may also bring about greater internal stress. Therefore, tempering after quenching is essential to relieve internal stress and improve the toughness of the material.
3.Liquid argon stainless steel quenching process
The quenching process is an important means to improve the hardness, strength and wear resistance of stainless steel workpieces. Liquid argon, as a cooling medium, shows unique advantages in stainless steel quenching. The following is a detailed introduction to the quenching process of liquid argon stainless steel, including preparation before quenching, control of quenching parameters and post-quenching treatment.
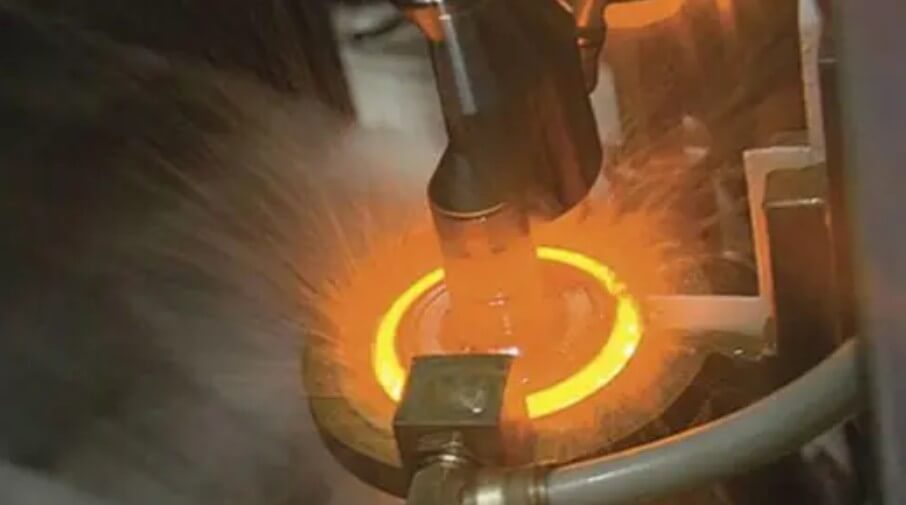
(1) Preparation before quenching
1) Material selection and inspection:
Choose the appropriate stainless steel grade according to the use needs, such as 304, 316, etc. Check the surface condition and size of the material to ensure there are no defects such as cracks and scale.
2) Preheating treatment:
Preheat stainless steel to eliminate internal stress and reduce the tendency of deformation and cracking during quenching. The preheating temperature is generally between 600-800°C, and the holding time is determined according to the material thickness.
3) Equipment preparation:
Choose a heat treatment furnace that can accurately control heating temperature and holding time, and ensure the normal operation of the liquid argon supply system. As a cooling medium, liquid argon has the advantages of fast cooling speed, good uniformity, and does not pollute the surface of the workpiece.
(2) Control of quenching parameters
1) Quenching temperature:
The quenching heating temperature of stainless steel is usually selected above Ac3 or Ac1. The specific temperature depends on the composition and structure of the steel. Hypoeutectoid steel generally chooses Ac3+30~50℃, while eutectoid steel and hypereutectoid steel choose Ac1+30~50℃. If the heating temperature is too high, it will lead to coarse grains and an increased risk of deformation and cracking, while if the temperature is too low, the ideal martensite structure cannot be obtained.
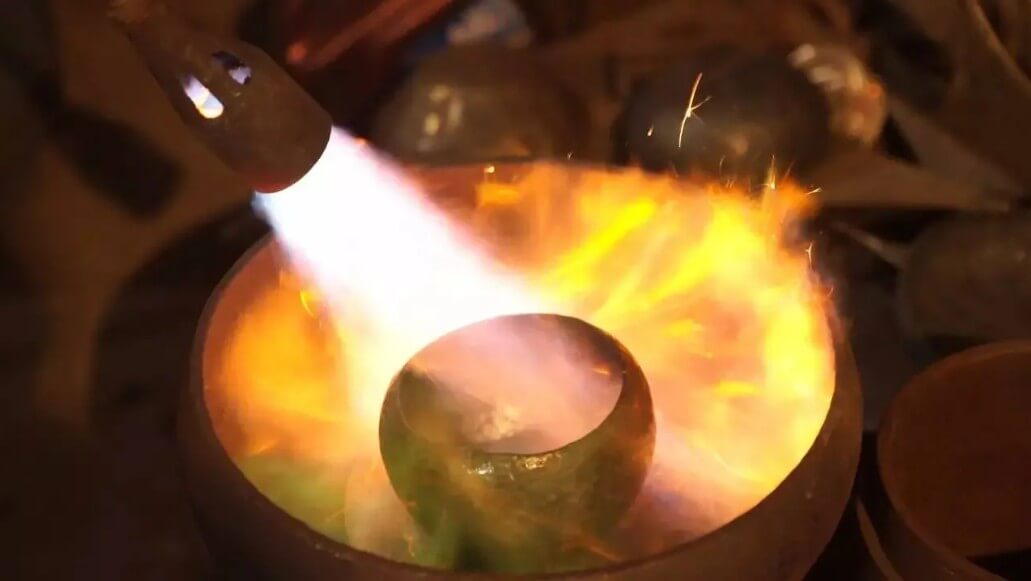
2) Keeping time:
It can be entered into the furnace at room temperature or at 300~400℃, and isothermally maintained at 550~600℃ for a period of time to ensure that the workpiece is heated evenly. The holding time should be determined according to the size of the workpiece, steel composition and heat treatment technical requirements, usually between 15 and 25 minutes.
3) Cooling speed:
Liquid argon has excellent cooling capacity as a cooling medium and is suitable for quenching stainless steel. When using liquid argon cooling, the workpiece is first rapidly cooled in liquid argon to close to the Ms point, and then immediately transferred to air for cooling to prevent cracking caused by excessive internal stress in the workpiece.
(3) Treatment after quenching
1) Tempering treatment:
Quenched stainless steel needs to be tempered to eliminate internal stress, stabilize the structure, and improve toughness. Tempering temperature and time should be determined according to the specific use requirements of the workpiece, usually between 150 and 300°C, and the holding time is 1 to 2 hours.
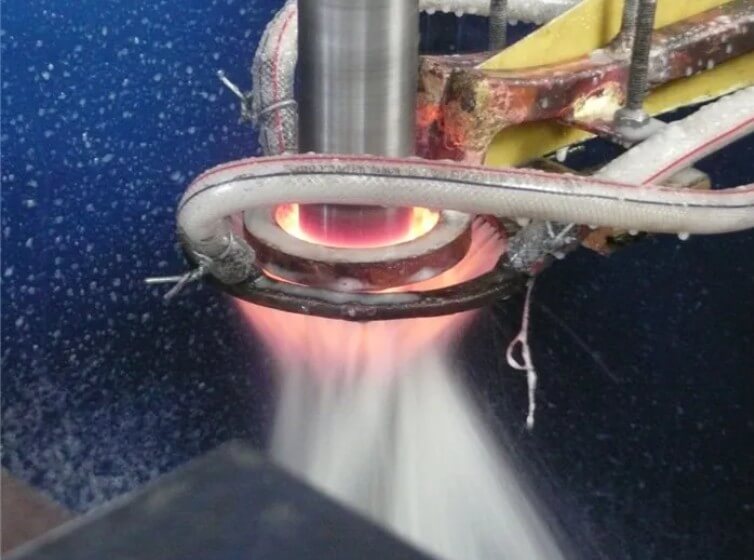
2) Cold treatment:
For high carbon and alloy steels, cold treatment is an important step. Cold treatment can make the transformation of supercooled austenite to martensite more complete, reduce the content of residual austenite, and improve the hardness and wear resistance of steel. Cold treatment is usually carried out at -70~-80℃, and the holding time is 1~2 hours.
3) Surface treatment:
There may be some scale or dirt on the surface of the workpiece after quenching and tempering, which needs to be cleaned. Cleaning methods can include mechanical grinding, pickling or sandblasting to ensure the surface finish and dimensional accuracy of the workpiece.
4) Detection:
Finally, the hardness, toughness, deformation, etc. of the quenched workpiece are tested to ensure that its performance meets the usage requirements. Commonly used detection methods include Rockwell hardness test, impact test, metallographic microscope observation, etc.
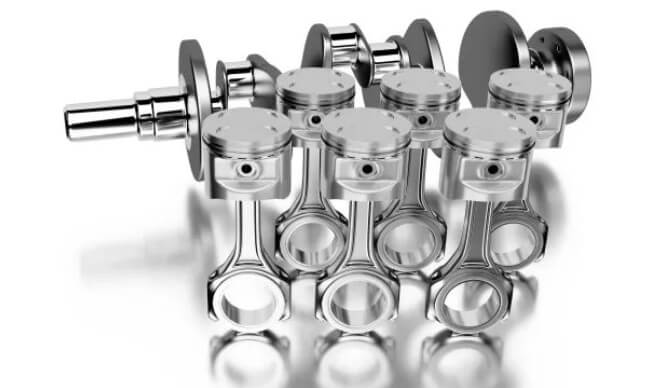
summary:
The liquid argon stainless steel quenching process can significantly improve the mechanical properties and service life of stainless steel workpieces through reasonable preparation, precise parameter control and effective post-processing, providing reliable guarantee for its application in molds, aerospace, automobiles and other fields. .
4.Evaluation of the effect of liquid argon stainless steel quenching
(1) Hardness test
Hardness testing is one of the most direct methods to evaluate the quenching effect of liquid argon stainless steel. By measuring the hardness value of the material surface, the success of the quenching process can be judged. Commonly used hardness testing methods include Rockwell hardness test, Vickers hardness test, etc.
These testing methods provide accurate hardness data to help researchers analyze and optimize the quenching process. For example, by comparing hardness values under different quenching parameters, the optimal quenching conditions can be found to improve the performance of the material.
(2) Metallographic analysis
Metallographic analysis is a method to evaluate the quenching effect of liquid argon stainless steel by observing the microstructure of the material under a microscope. Through metallographic analysis, the grain size, phase composition and organizational structure of the material can be observed to determine the quality of the quenching process.
For example, fine martensite grains and uniform microstructure usually mean good quenching results. In addition, metallographic analysis can also reveal defects that may occur during the quenching process, such as cracks and segregation, helping researchers further optimize process parameters.
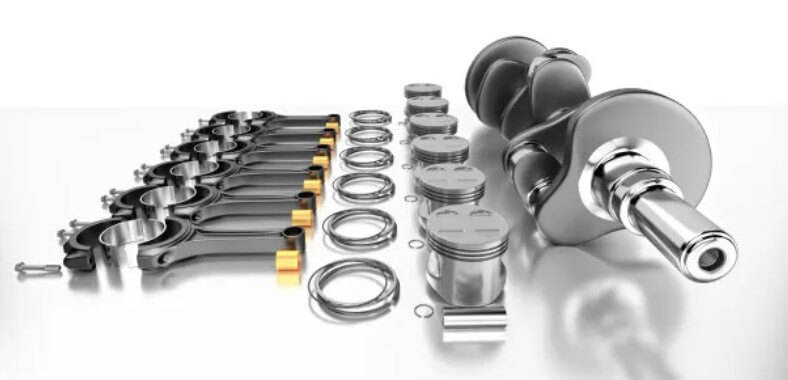
(3) Mechanical property testing
Mechanical property testing is an important means to evaluate the quenching effect of liquid argon stainless steel, including tensile testing, impact testing, etc. These tests provide key performance indicators of materials such as strength, toughness and ductility.
For example, tensile testing can measure a material’s tensile strength and yield strength, while impact testing can evaluate a material’s toughness. Through these tests, the mechanical properties of the material can be fully understood to ensure that it meets the needs of practical applications.
5.Analysis of advantages and disadvantages of liquid argon stainless steel quenching
(1) Advantages
1) Fast cooling speed:
Liquid argon has extremely low temperature and good cooling ability, which can achieve rapid cooling, help form a uniform martensite structure, and improve the hardness and strength of stainless steel.
2) Small quenching deformation:
During the liquid argon cooling process, the internal and external temperature gradient of the workpiece is small, thereby reducing thermal stress and tissue stress, and effectively reducing the risk of deformation and cracking of the workpiece.
3) Environmentally friendly and pollution-free:
Compared with traditional oil quenching and water quenching, liquid argon stainless steel quenching does not produce harmful substances, is environmentally friendly, and meets the requirements of green manufacturing.
4) Wide scope of application:
Liquid argon quenching is suitable for a variety of stainless steel materials, especially for large, complex and precise workpieces, and can maintain good quenching effects.
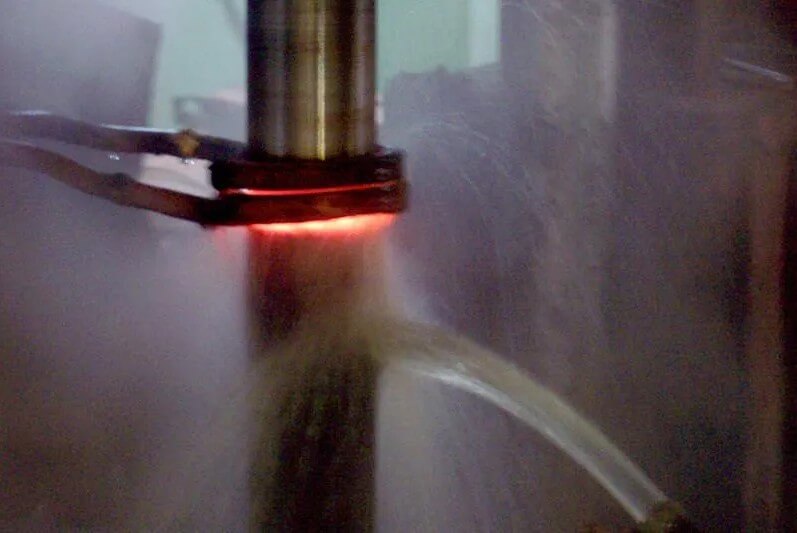
(2) Disadvantages
1) Higher cost:
As a cryogenic liquid, liquid argon has high storage, transportation and use costs, which increases the company’s production costs.
2) High operating requirements:
The low-temperature characteristics of liquid argon require high equipment and operational safety, requiring professional equipment and operators to avoid risks such as low-temperature burns.
3) The cooling speed is difficult to control:
The cooling rate of liquid argon is extremely fast. For some workpieces with thick walls or complex shapes, it is difficult to accurately control the cooling rate, which may increase internal stress and affect the performance of the workpiece.
6.Which fields require the use of liquid argon stainless steel quenching technology?
(1) Tool manufacturing industry:
Liquid argon stainless steel quenching technology is widely used in tool manufacturing. Through liquid argon quenching, the hardness and wear resistance of the tool can be significantly improved, thereby extending its service life. For example, when manufacturing high-speed steel cutting tools, liquid argon quenching can significantly improve the cutting performance of the cutting tools, reduce wear and improve production efficiency.
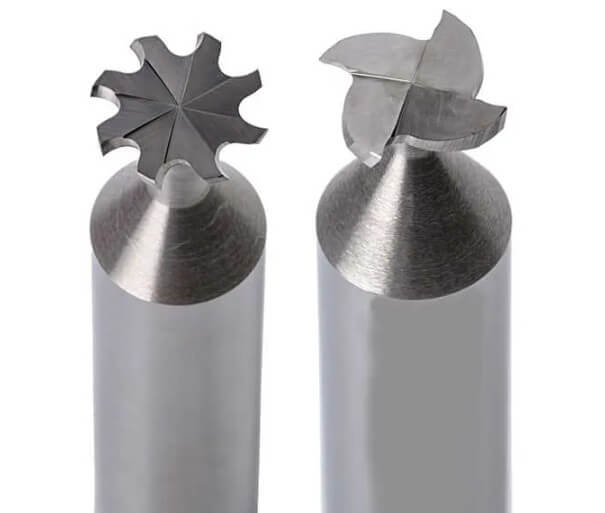
(2) Aerospace industry:
In the aerospace industry, liquid argon stainless steel quenching technology is used to manufacture high-performance stainless steel components. For example, through liquid argon quenching, the heat and corrosion resistance of engine components can be improved, thereby improving engine performance and reliability. In addition, liquid argon quenching can also be used to manufacture aircraft structural components to improve their strength and toughness and ensure flight safety.
(3) Automobile industry:
Key components such as automobile engines, transmission systems, and suspension systems require high hardness, high wear resistance, and good impact resistance. Liquid argon stainless steel quenching technology is used in the automotive industry to manufacture crankshafts, connecting rods, gears, bearings and other parts.
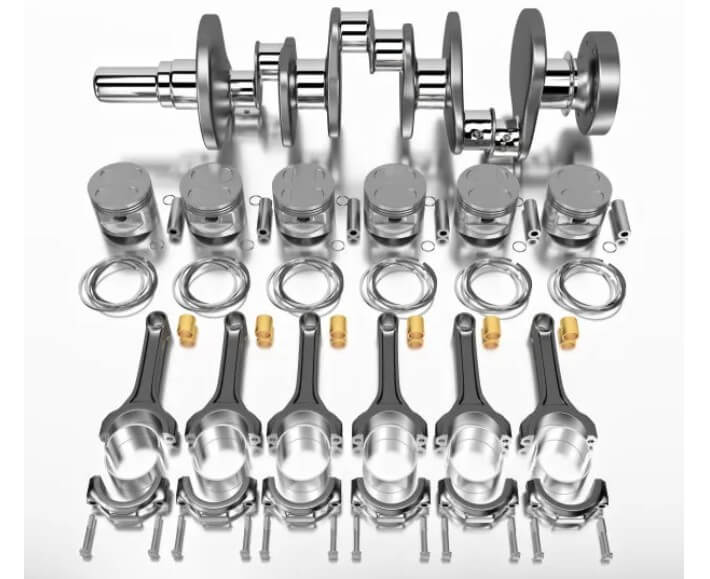
(4) Petrochemical equipment:
Petrochemical equipment often works in high temperature, high pressure, and corrosive environments, so materials need to have excellent corrosion resistance and mechanical properties. Liquid argon stainless steel quenching technology is used to manufacture key components such as oil drilling equipment, chemical reactors, and pipeline valves.
7.Summary
Liquid argon stainless steel quenching technology has shown significant advantages in improving the performance of stainless steel materials. By reasonably controlling the quenching process parameters, not only can the hardness, strength and wear resistance of the material be effectively improved, but its good corrosion resistance can also be maintained. With the continuous maturity and promotion of technology, liquid argon quenching technology will definitely open up a broader space for the application of stainless steel materials in the future.
What do you think?
[…] (1) Selection and control of cooling medium […]
[…] Quenching is a heat treatment process in which steel is heated to austenitizing temperature (generally 20℃~50℃ above Ac3 or Ac1), maintained for a certain period of time, and then cooled at a rate greater than the critical cooling rate. This process is like the “rebirth of steel”, giving it high hardness and wear resistance. The following will analyze in detail what happens when you quench and temper iron? […]
[…] basic principle of quenching heat treatment is to heat the material to above the austenitizing temperature, keep it warm for a period of time […]