Amorphous Wire Manufacturing Process: Principles, Process Methods and Optimization Guide
Amorphous wire manufacturing process is an advanced technology that combines high temperature, rapid cooling and precision control. Through this process, even micron-level metal wires with unique properties can be manufactured. These wires show great application potential in the fields of electronics, sensors and medical treatment. This article will explore in depth the principles, process methods and parameter control and optimization of amorphous wire manufacturing process.
1.Introduction to amorphous wire
(1) Definition and characteristics of amorphous wire
Amorphous wire, also known as metallic glass wire, is a material that does not have a long-range ordered structure at the atomic scale. The special structure of this material gives it many excellent properties, such as high hardness, high strength, excellent magnetic properties and corrosion resistance. These properties make amorphous wire widely used and valued in many high-tech fields.
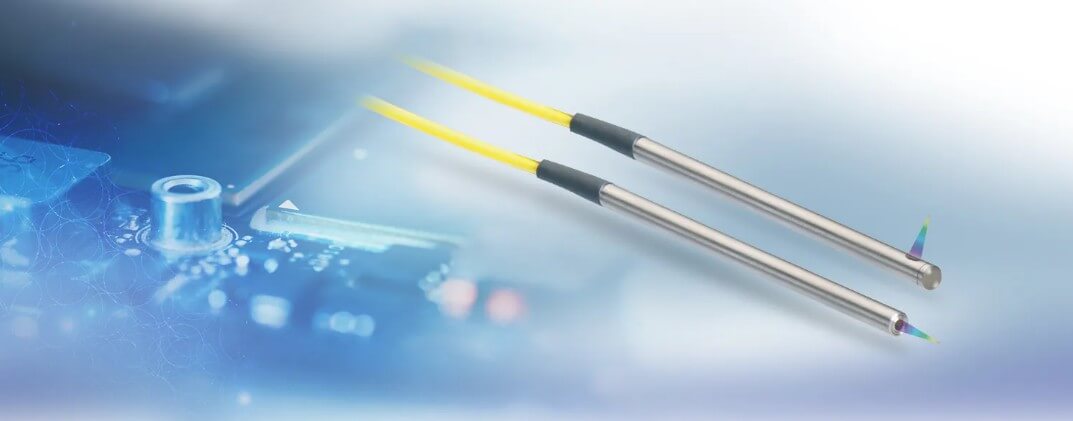
(2) Classification of amorphous wire
1) Iron-based amorphous wire:
○ High magnetic permeability: easy to magnetize, widely used in inductor components, transformers, etc.
○ Low loss: excellent performance under high frequency conditions, reducing energy loss
○ High saturation magnetic induction intensity: suitable for high-power magnetic components.
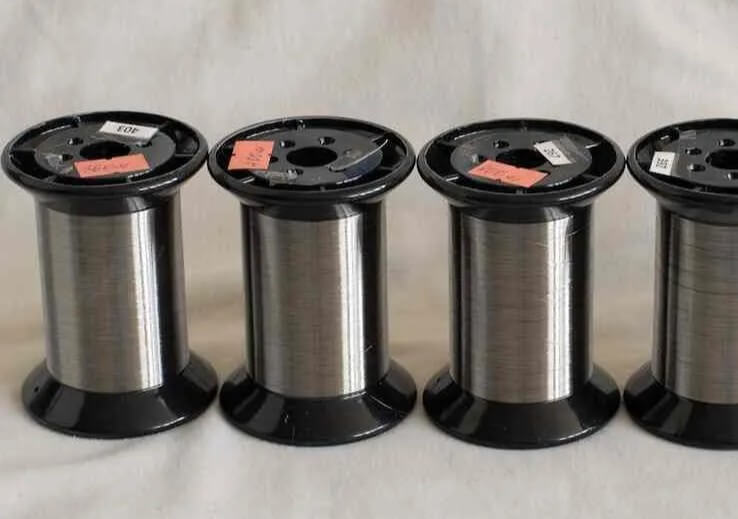
2) Cobalt-based amorphous wire:
○ Large magnetostriction coefficient: sensitive to changes in external magnetic field, suitable for magnetostrictive sensors, etc.
○ Small magnetic anisotropy: uniform magnetic properties and good stability.
○ High resistivity: reduces eddy current loss.
3) Nickel-based amorphous wire:
Good soft magnetic properties: easy to magnetize and demagnetize.
High resistivity: suitable for high-frequency applications.
Good corrosion resistance: excellent performance in harsh environments.
2.Principle of amorphous wire manufacturing process
(1) Rapid solidification technology
The amorphous wire manufacturing process mainly relies on rapid solidification technology, which cools the molten metal or alloy at an extremely fast speed so that it solidifies without enough time to form a crystal structure, thereby forming an amorphous structure. In this process, the cooling rate is the key factor, usually reaching millions of degrees per second to ensure the formation of an amorphous state. The core of this technology is to control the cooling rate to prevent atoms from having enough time to arrange into a crystal structure.
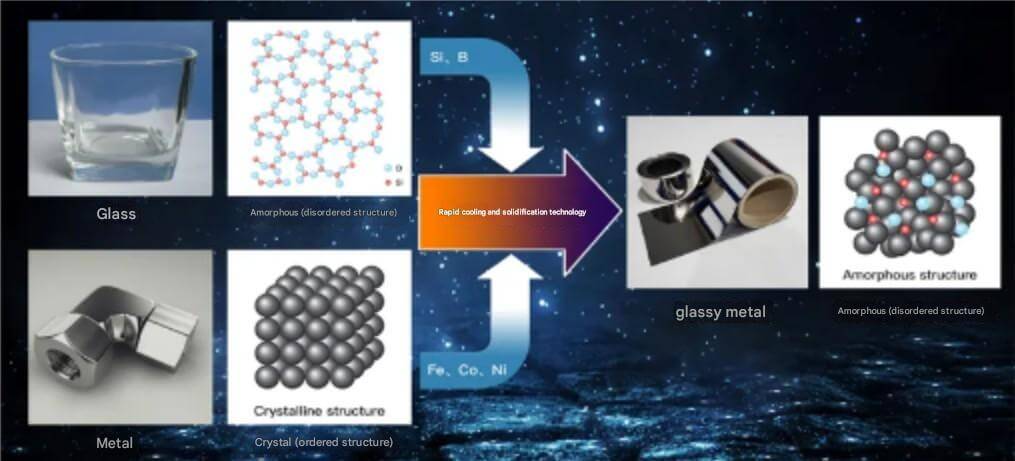
(2) Effect of cooling rate on amorphous formation
The cooling rate has a decisive influence on the formation of amorphous structure and its properties. A sufficient cooling rate can inhibit the formation and growth of crystal nuclei and ensure the formation of a completely amorphous structure. If the cooling rate is insufficient, the material may partially crystallize, affecting its properties. The cooling rate not only affects the formation of amorphous state, but also affects the microstructure and final properties of amorphous wire, such as magnetic properties, mechanical properties and chemical stability. Therefore, in the amorphous wire manufacturing process, the cooling rate must be precisely controlled.
3.Analysis of the main methods of amorphous wire manufacturing process
(1) Melt spinning method
Melt spinning method is a commonly used process method for amorphous wire manufacturing. This method ejects molten metal or alloy through a fine nozzle and rapidly cools it with a high-speed flowing cooling medium (such as water or gas) to form amorphous wire.
The advantages of this amorphous wire manufacturing process are simple equipment and easy operation, but the nozzle design and the choice of cooling medium have a significant impact on product quality. The design of the nozzle needs to ensure that the molten metal can flow out evenly and stably, while the choice of cooling medium needs to ensure that it can provide a sufficient cooling rate.

(2) Glass coating method
Glass coating method is a special amorphous wire manufacturing process that wraps the molten metal or alloy in a glass tube, and then quickly draws the glass tube and the metal inside to make it thinner at the same time, and finally forms an amorphous wire through rapid cooling. The amorphous wire made by this amorphous wire manufacturing process has a layer of glass coating on the outside, which can protect the amorphous wire from environmental influences and improve its stability and durability.
The main advantage of the glass coating method is that it can produce thin-diameter amorphous wires with excellent performance, but the process is relatively complicated and requires precise control of the drawing speed of the glass tube and the metal.
(3) Single-roll method and double-roll method
The single-roll method and double-roll method are common technologies used to manufacture amorphous thin strips. In these methods, the molten metal or alloy is sprayed onto a rapidly rotating roller and rapidly cooled to form an amorphous thin strip through contact with the roller. The single-roll method uses one roller, while the double-roll method uses two rollers. The double-roll method can more accurately control the thickness and performance of the thin strip.
The advantages of the single-roll method and the double-roll method are that they can produce amorphous thin strips on a large scale, but the equipment investment is relatively high and the control of process parameters requires strict requirements.
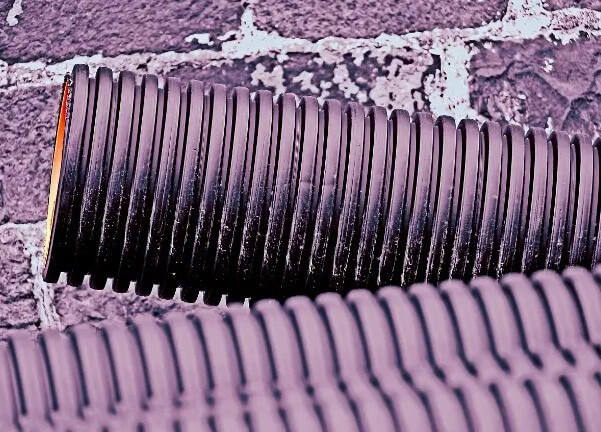
4.Control of key parameters in amorphous wire manufacturing process
(1) Material ratio and melt temperature
In the amorphous wire manufacturing process, the ratio of material components and the temperature of the melt are extremely important parameters. Different material ratios can affect the amorphous forming ability and the final performance of the product. For example, iron-based amorphous wire usually has excellent magnetic properties, while cobalt-based amorphous wire has higher hardness and wear resistance. The control of melt temperature is also very critical. Too high temperature may cause nozzle clogging, and too low temperature may affect the fluidity of the material, thereby affecting the quality of the product.
(2) Cooling rate and roller speed
The cooling rate and roller speed are key process parameters that determine the quality of amorphous wire. The cooling rate determines the formation of the amorphous structure, while the roller speed affects the thickness and performance of the thin strip. In the single-roll method and the double-roll method, the speed of the roller needs to be precisely matched with the metal flow rate of the spray to ensure the uniformity and performance of the thin strip. In addition, the optimization of the cooling rate and roller speed can be carried out through experiments and simulations to achieve the best production effect.
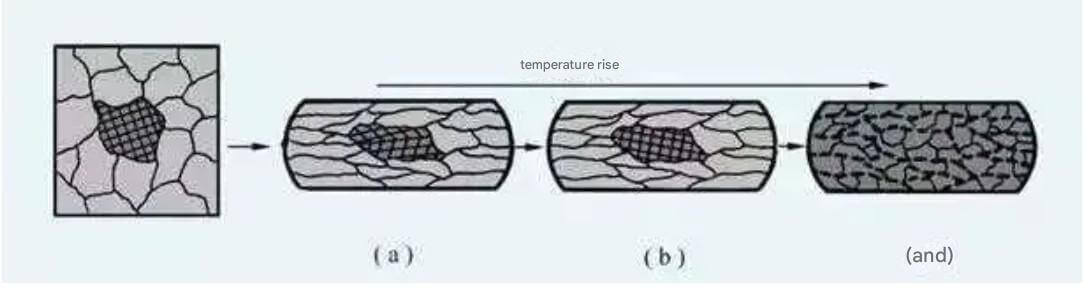
(3) Nozzle design and substrate selection
The design of the nozzle and the selection of the substrate also have an important impact on the production of amorphous wires. The shape and size of the nozzle determine the flow pattern and cooling efficiency of the molten metal, thereby affecting the quality and performance of the amorphous wire. The selection of the substrate needs to consider its thermal conductivity and surface state to ensure that it can provide sufficient cooling rate and good interface bonding. In the glass coating method, the selection of the glass tube also needs to consider its compatibility with the metal and the thermal expansion coefficient.
5.Optimization and challenges of amorphous wire manufacturing process
(1) Raw material selection and ratio optimization:
The amorphous wire manufacturing process usually adopts rapid solidification technology, and the selection and ratio of raw materials are crucial. Studies have shown that when the zirconium content in the metal composition increases from 5% to 10%, the amorphous forming ability is significantly improved.
For example, a study successfully improved the magnetic properties and mechanical strength of the product by precisely controlling the proportion of zirconium when preparing Zr-Cu-Al-Ni amorphous alloy wire.
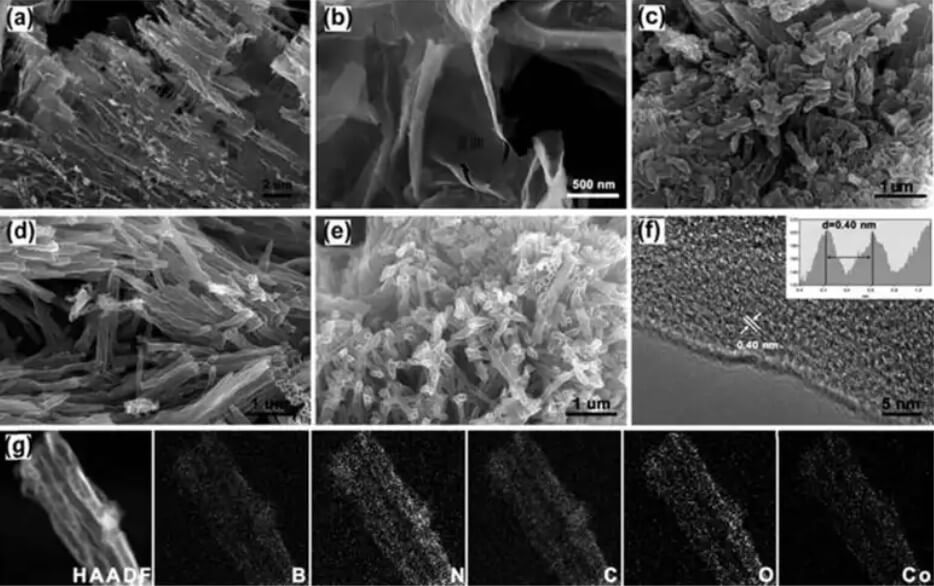
(2) Melting and casting process:
The melting temperature and time have a direct impact on the quality of amorphous wire. Data show that a uniform amorphous structure can be obtained by melting at 1550°C and holding for 30 minutes.
During the rapid cooling process, the cooling rate must reach above 105 K/s to effectively suppress the crystallization phenomenon. A production line optimized the induction melting parameters and increased the cooling rate to 108 K/s, significantly improving the yield and consistency of amorphous wire.
(3) Adjustment of spinning process parameters:
The spinning process is one of the core steps in the amorphous wire manufacturing process. The spinneret aperture, injection pressure and injection distance must all be precisely controlled. Practice shows that when the spinneret aperture is 0.5 mm, the injection pressure is 0.8 MPa and the injection distance is 20 cm, the diameter uniformity of the amorphous wire is optimal and the defect rate is reduced to less than 3%.
(4) Post-treatment process:
Post-treatment mainly includes heat treatment and surface treatment. Appropriate heat treatment can improve the mechanical properties of amorphous wire. For example, after heat treatment at 400°C for 1 hour, the hardness of amorphous wire increased by 15%.
Surface treatment can enhance its corrosion resistance. The case shows that the use of electroplating technology to form a 5 μm thick nickel coating on the surface of amorphous wire prolongs its corrosion resistance time in the salt spray test by 50%.
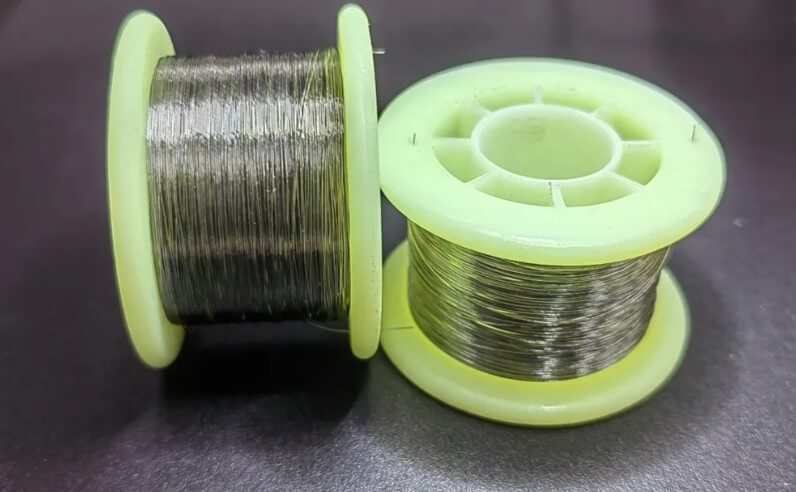
(5) Challenges faced by amorphous wire manufacturing process:
Although the above methods can significantly improve the performance of amorphous wire, the optimization of amorphous wire manufacturing process still faces many challenges, such as high equipment cost, sensitive and difficult to control process parameters. Data show that the initial investment cost of high-performance amorphous wire production equipment is 2-3 times that of traditional equipment, and slight fluctuations in process parameters may lead to huge differences in product performance.
6.Related applications of amorphous wire
(1) Power electronics field:
Amorphous wire is mainly used to make high-frequency transformers and inductors in the power electronics field. Its high magnetic permeability and low loss characteristics make the transformer highly efficient under high frequency conditions, reducing the size and weight, and is widely used in switching power supplies, inverters and other equipment.
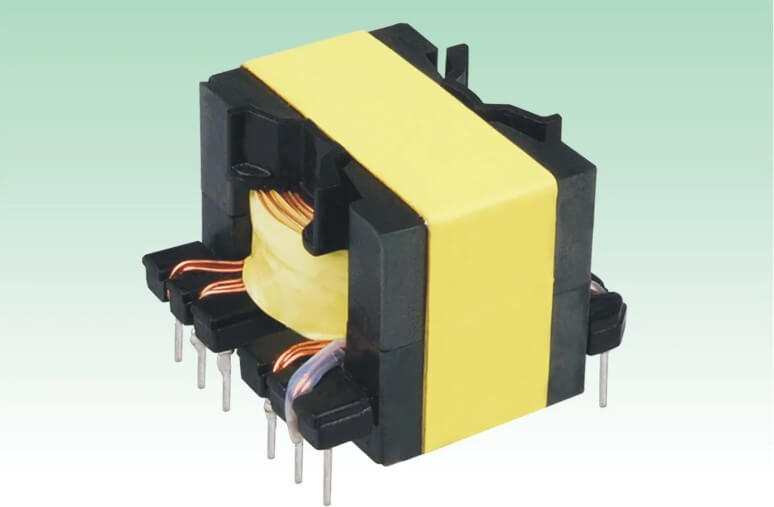
(2) Sensor field:
Because amorphous wire has a giant magneto-impedance effect, that is, its impedance value changes significantly with the external magnetic field, it is used to make high-sensitivity magnetic sensors. These sensors can be used in automotive navigation systems, current detection, non-destructive testing and other fields to provide accurate magnetic field measurements.
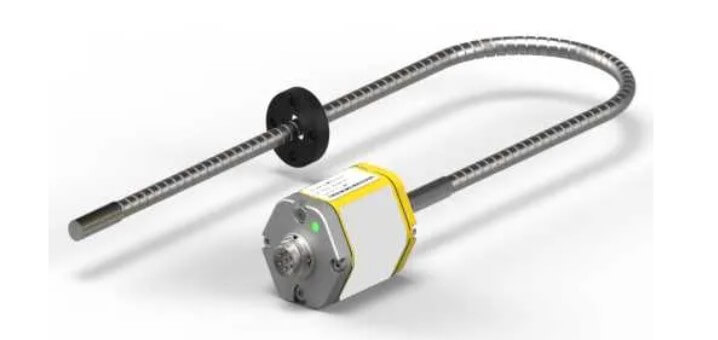
(3) Electromagnetic shielding field:
Amorphous wire materials have a good absorption effect on electromagnetic waves and can be used as electromagnetic shielding materials to effectively reduce electromagnetic interference between electronic devices. This has important applications in high-frequency electronic equipment, aerospace and military equipment.
(4) Biomedical field:
The application of amorphous wire in the biomedical field includes magnetic targeted drug delivery systems. Using its magnetic properties, amorphous wire can guide drugs to accurately reach the lesion site, improve drug efficacy and reduce side effects.
(5) Soft magnetic composite material field:
Amorphous wire can be combined with other materials to prepare soft magnetic composite materials with excellent comprehensive magnetic properties. These materials have broad application prospects in new motors, generators and other electrical equipment, and can improve equipment efficiency and performance.
7.Summary
The amorphous wire manufacturing process is a field full of challenges and opportunities. Through in-depth discussions on principles, process methods and parameter optimization, we can see that every process improvement may bring about a leap in material performance, so it is particularly important to master the amorphous wire manufacturing process.