High pressure die casting process applications: 5 major industry application analysis
As an indispensable part of today’s manufacturing industry, high pressure die casting process applications has been involved in all aspects of the industry, high-pressure die-casting process is with its high efficiency, precision, one-piece molding unique charm, greatly promote the transformation and upgrading of the manufacturing industry. This paper will analyze the high pressure die casting process applications of 5 industries, and detailed introduction of their application background, actual cases and application advantages.
1.High pressure die casting process principle and process characteristics overview
High pressure die casting is a kind of advanced metal molding technology, mainly used for manufacturing precision, complex metal parts. The process through the molten metal at high temperature with very high pressure into the mold cavity, so that it quickly cooled and solidified, so as to form the desired shape. This process is capable of producing parts with high dimensional accuracy and surface finish, and the following are some of the distinguishing features of the process:
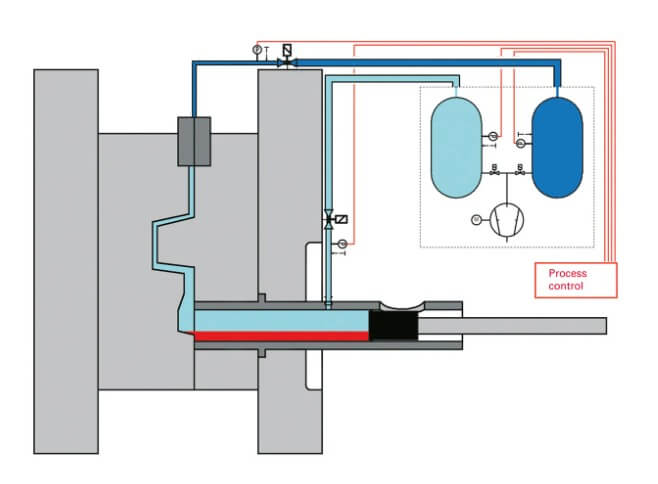
(1) high efficiency production:
High pressure die casting process, the liquid metal filling time is very short, usually in 0.01-0.2 seconds can fill the cavity, greatly improving the production efficiency.
(2) high precision and surface quality:
Due to the high pressure and high speed filling method, die casting can obtain very high dimensional accuracy and surface finish, generally up to Ra6.3 or even higher, reducing the need for subsequent processing.
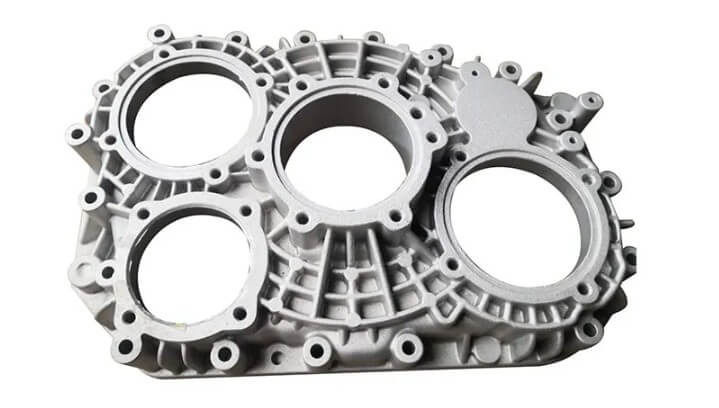
(3) Material adaptability is wide:
Commonly used die-casting materials include aluminum alloy, magnesium alloy, zinc alloy, etc., of which aluminum alloy is most widely used because of its good specific strength and corrosion resistance.
(4) complex shape molding:
High-pressure die casting can produce complex shape, thin-walled parts, to meet the needs of modern industry on lightweight and structure integration design.
2.High pressure die casting process applications — automobile industry
(1) high pressure die casting process applications background
In the automobile industry, high pressure die casting technology because it can reduce the weight of the vehicle, improve fuel efficiency and reduce production costs and has been widely valued. Along with the increasingly strict environmental protection regulations and consumers on fuel economy requirements, automobile manufacturers are more and more inclined to use lightweight materials such as aluminum alloy to replace the traditional steel materials. High-pressure die-casting technology is to achieve this goal of one of the key technologies, through high-pressure die-casting, can produce complex structure, high strength aluminum alloy parts.
(2) high pressure die casting process applications of typical parts production
1) engine parts
Cylinder block, cylinder head and crankcase: these key components need to withstand high temperature, high pressure and high strength mechanical load. Die casting process can produce parts with excellent wear resistance and heat resistance, to ensure stable engine performance.
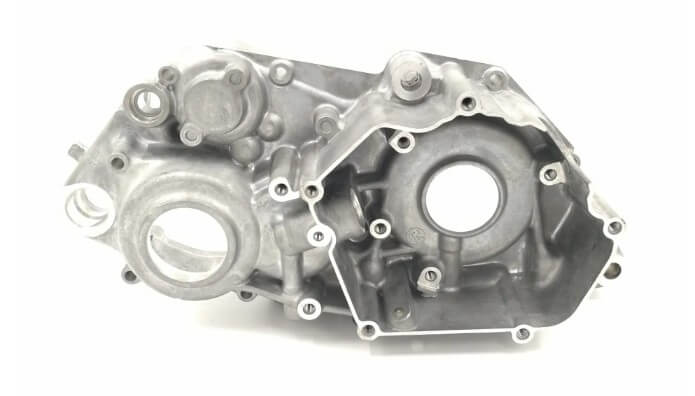
2) body parts
Wheel hubs, door frames and frames: these parts of the car’s lightweight and safety is crucial. High-pressure die-casting can produce high-strength and light weight aluminum alloy body parts, improve vehicle stability and fuel consumption performance.
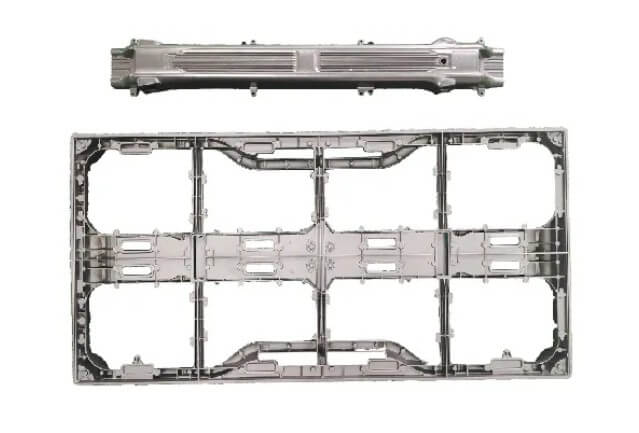
3)Chassis components
Suspension arms, axles and brake calipers: chassis components require high strength and corrosion resistance to ensure handling performance and braking safety. Die casting process can produce complex shaped parts that meet these stringent requirements.
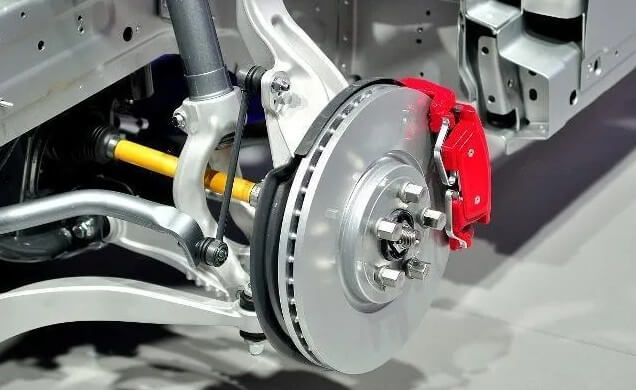
4) Interior components
Steering wheel, instrument panel and center control panel: these interior parts not only require beautiful and comfortable, but also need to have good durability and easy to clean characteristics. Die casting process can produce smooth surface, delicate details of the interior parts, enhance the driving experience.
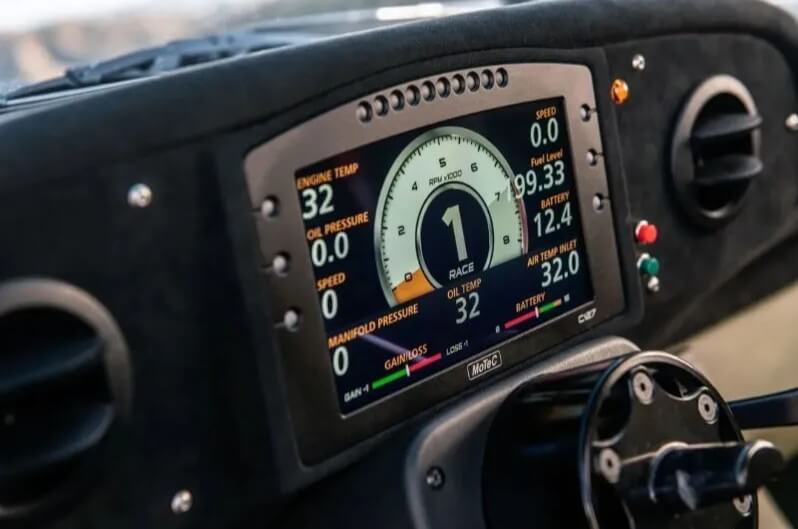
(3) high pressure die casting process applications of lightweight and environmental protection advantages
High-pressure die casting technology to automobile lightweight contribution is significant, which not only helps to reduce fuel consumption, but also can reduce the vehicle’s carbon dioxide emissions, in line with the current trend of environmental protection. For example, the application of aluminum alloy high pressure die casting in the automobile can significantly reduce the overall vehicle quality, thus improving fuel economy and range. At the same time, high pressure die casting process of high efficiency and automation degree also reduces the production process of energy consumption and waste generation, further promote the sustainable development of automobile manufacturing industry.
3.High pressure die casting process applications – 3C electronic products
(1) high pressure die casting process applications overview
In 3C (computer, communication, consumer electronics) industry, high pressure die casting technology is widely used in the production of complex structure, appearance requirements of high electronic product shell and internal structure parts. With consumers on electronic products appearance and performance requirements continue to improve, high pressure die casting technology because it can provide high precision and beautiful surface treatment and become the first choice of manufacturing these parts of the process.
(2) high pressure die casting technology application of product examples
1) cell phone frame:
Cell phone frame is to support the overall structure of the key components of the cell phone, using high-pressure die-casting technology manufacturing cell phone frame, not only the structure is strong, but also can realize the thin and light.
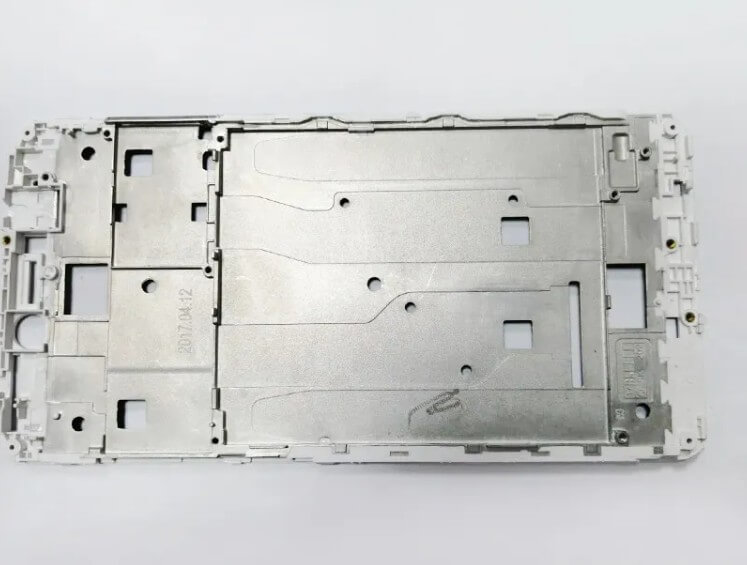
2) Laptop computer shell:
Laptop shell need to have high strength, lightweight and aesthetic degree and other characteristics. High-pressure die-casting process can produce a smooth surface, excellent texture of the notebook shell, to meet consumer demand.
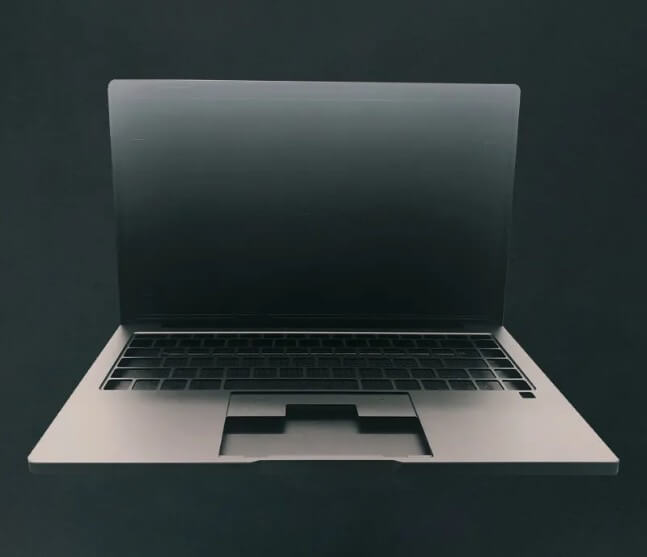
3) tablet computer backplane:
Tablet computer back plate also need to have high strength and aesthetic degree. High-pressure die-casting process can produce a complex structure, the surface of the exquisite back plate, enhance the overall texture of the product. Realize the combination of metal texture and good hand feeling.
4) digital camera shell:
Digital camera shell needs to have high precision and good protection performance. High-pressure die-casting process can produce a high-precision camera shell, to ensure that the parts of the precise coordination, while providing good shock resistance and waterproof performance.
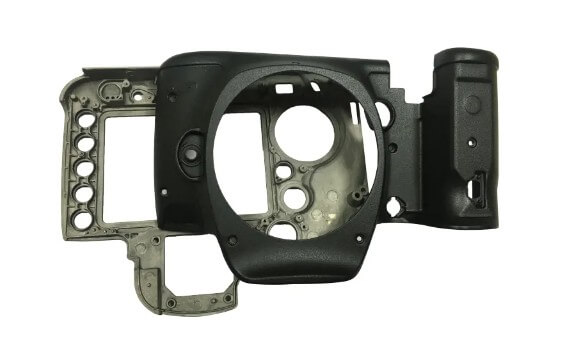
(3) high pressure die casting process applications of precision and beauty advantage
High pressure die casting process in 3C electronic products, not only ensure the precision and structural strength of the product, but also through the surface treatment technology such as sandblasting, anodizing, etc., improve the appearance of the product quality. These treatments make the product surface smoother and more delicate, which enhances the aesthetics and market competitiveness. For example, through CAE simulation simulation software optimization casting system and process parameters, can accurately predict and reduce the rolled gas, inclusions and other defects, improve the yield rate, save production costs, while ensuring that the product’s high precision and aesthetics.
4.High pressure die casting process applications – medical equipment field
(1) high pressure die casting process applications requirements
Medical device industry to product accuracy and safety has very high requirements, high pressure die casting process in this field of application gradually increased, especially in the production of surgical instrument frame and medical instrument shell and so on. These parts need to have high dimensional accuracy and good biocompatibility to ensure the safety and reliability of medical devices.
(2) high pressure die casting process applications of actual cases
1) dental implants:
High-pressure die casting can produce dental implants with high precision and excellent surface finish, such as titanium dental implants. This process ensures that the implant and the human bone good combination of degree, at the same time its high efficiency reduces the production cost.
2) Surgical instrument handles:
Surgical instrument handles produced by high-pressure die-casting process are characterized by strong structure and light weight. Aluminum alloy material through high-pressure die casting can be one-time molding complex structure, enhance the overall performance of surgical instruments.
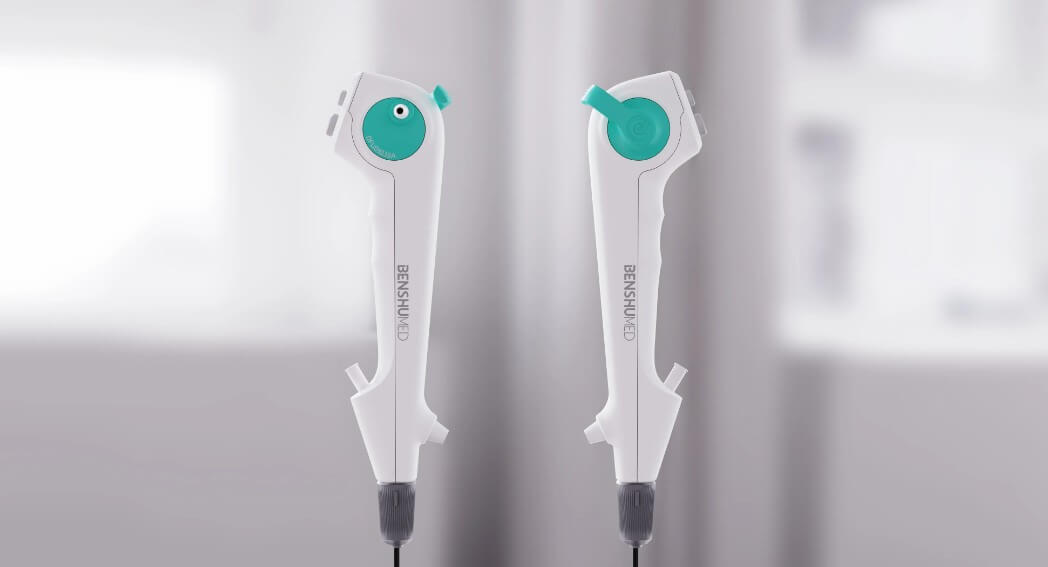
3) orthopedic fixation plate:
High-pressure die-casting process in the manufacture of orthopedic fixation plates can ensure the strength and durability of the product. The magnesium alloy material made by this process has good biocompatibility and lighter quality of the fixed plate, which helps the patient’s postoperative recovery.
4) Medical imaging equipment parts:
Such as CT machine, X-ray machine structural parts, high-pressure die-casting can produce high-precision parts to ensure the stable operation of equipment and imaging quality. The use of zinc alloy material, make parts with excellent mechanical properties and corrosion resistance.
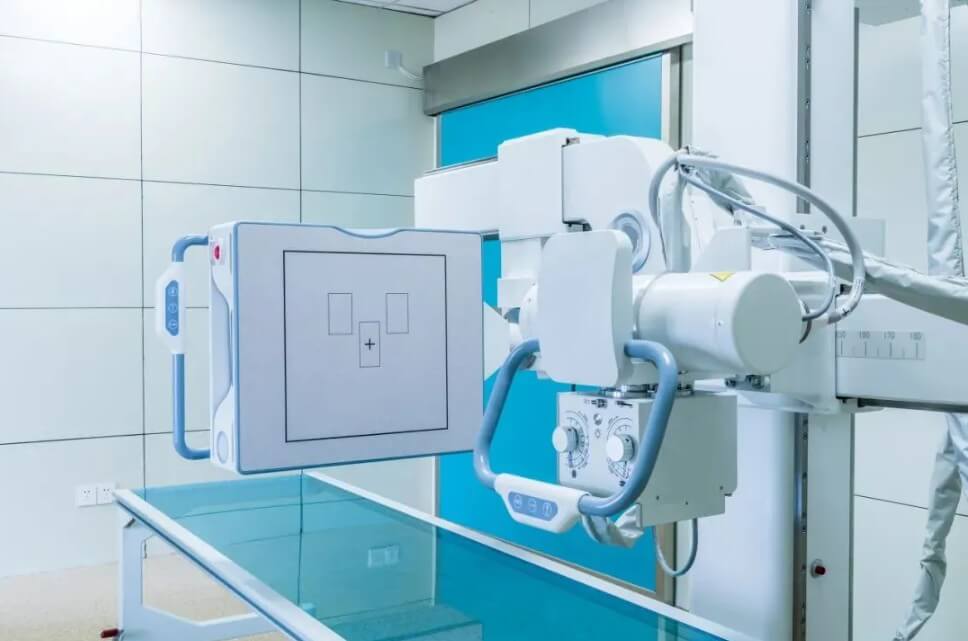
(3) high pressure die casting process applications of safety and reliability advantages
High-pressure die-casting process in the application of medical device manufacturing, not only ensure the high precision and complexity of the product, but also through the strict quality control and post-treatment process, ensure the safety and reliability of the product. For example, during the production process, the gas and impurities inside the casting are removed by vacuum die-casting technology, which improves the denseness and mechanical properties of the casting, thus ensuring the stability and safety of medical devices in the process of use. In addition, through the CAE simulation simulation software optimization process parameters, can further reduce defects, improve product quality and consistency.
5.High pressure die casting process applications – aerospace field
(1) high pressure die casting process applications needs and advantages
With the continuous development of aerospace technology, for parts and components of the performance requirements are increasingly demanding. High pressure die casting process can produce high strength, high precision parts, in the aerospace field show unique advantages.
Spacecraft need to reduce the weight to reduce the launch cost, high pressure die casting process can produce lightweight alloy parts to meet this demand. At the same time, spacecraft components need to work stably in extreme environments, the parts produced by this process have excellent heat and radiation resistance. In addition, the aerospace field to parts of the reliability requirements are very high, high pressure die casting process can realize the integration of molding, reduce assembly error, improve product consistency, reduce failure rate.
(2) high pressure die casting process applications of actual cases
1) engine blade:
High-pressure die casting can produce a complex structure, thin-walled engine blade, its high precision, smooth surface, can significantly reduce weight, improve fuel efficiency. Such as a certain type of aviation engine using aluminum alloy high-pressure die-casting blade, in the high temperature environment with excellent performance.
2) landing gear components:
Landing gear is the aviation spacecraft key safety components, high pressure die casting process can produce high strength, high toughness landing gear parts. Such as aircraft landing gear shell, support rod, etc., the use of magnesium alloy high-pressure die casting, not only reduces the weight, but also to meet the requirements of the strength and anti-fatigue properties.
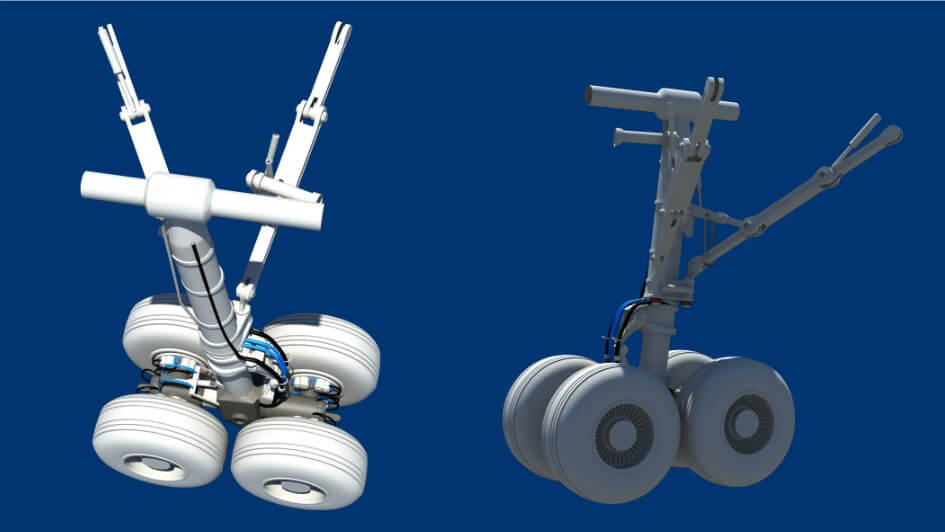
3) hatch frame:
The hatch frame requires high strength and good sealing. High-pressure die-casting process can one-time molding complex frame structure, to ensure dimensional accuracy and surface quality. Such as a certain type of airliner emergency hatch frame, using zinc alloy high pressure die casting, manufacturing cycle is short, low cost.
6.High pressure die casting process applications – home appliance field
(1) high pressure die casting process applications needs and advantages
With the continuous development of the home appliance industry, high pressure die casting process in the parts and components production in the application of the growing demand. The process can one-time molding complex structure parts, meet the home appliance product thin and light, integrated design requirements. In addition, high pressure die casting process production parts with high precision, good surface quality, strength and other characteristics, help to improve the overall performance and service life of home appliance products. In large-scale production, high-pressure die-casting process can also effectively reduce production cost and energy consumption, shorten the production cycle.
(2) high pressure die casting process applications of product examples
1) air conditioner shell:
Air conditioner indoor and outdoor machine shell usually use high pressure die casting process manufacturing. Aluminum alloy material under high pressure is injected into the mold, rapid cooling and shaping, with a smooth surface, precise size, strength and other characteristics, can effectively protect the internal components and enhance the product aesthetics.
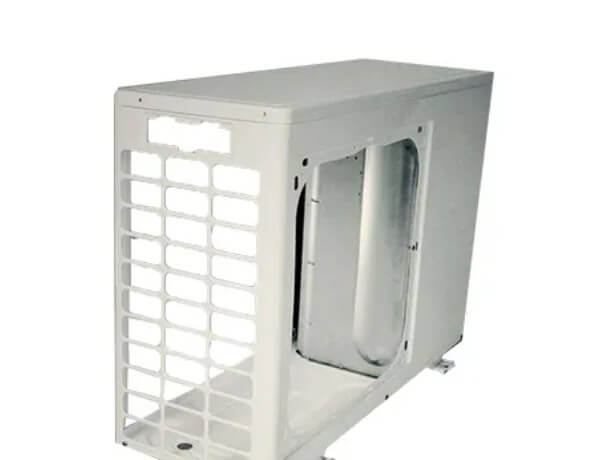
2) Washing machine inner tube:
The inner cylinder part of washing machine is also often produced by high-pressure die-casting process. Stainless steel material under high pressure to fill the mold, forming a complex structure, to ensure the durability and corrosion resistance of the inner cylinder, to meet the needs of long-term high-speed operation of the washing machine.
3) rice cooker liner:
High-pressure die-casting process can also be used to manufacture the inner liner of rice cookers. Aluminum alloy material is die-cast under high pressure to form an inner liner of uniform thickness, which not only has good thermal conductivity, but is also easy to clean and meets food safety standards.
7.Summary
High-pressure die casting process, as an advanced metal molding technology, has been widely used in many industries such as automotive, 3C electronics, medical devices, aerospace, home appliances and so on. Through high-pressure die casting technology, parts with high precision, high strength and beautiful appearance can be produced to improve the overall performance of the product and user experience.