Glass casting molds: design, manufacturing and maintenance process
Glass casting mold is the core component in the process of glass product molding. Its material selection, structural design and manufacturing process are extremely critical. High-quality glass casting mold can not only improve production efficiency, but also extend the service life of the mold and reduce production costs. This article will introduce in detail the material selection, design process, manufacturing process, daily maintenance and repair technology of glass casting mold, revealing its important role in the production of glass products.
1.Definition and importance of glass casting mold
Glass casting mold is a key tool for manufacturing glass products. Its design and manufacturing quality directly affects the shape, dimensional accuracy and surface quality of glass products. In modern industrial production, the excellent performance of the mold is the basis for ensuring production efficiency and product quality. Glass casting molds form various complex glass product shapes by precisely controlling the flow and cooling process of glass liquid. Therefore, the design and manufacture of molds require not only a high degree of expertise, but also precise processing technology and rich practical experience.
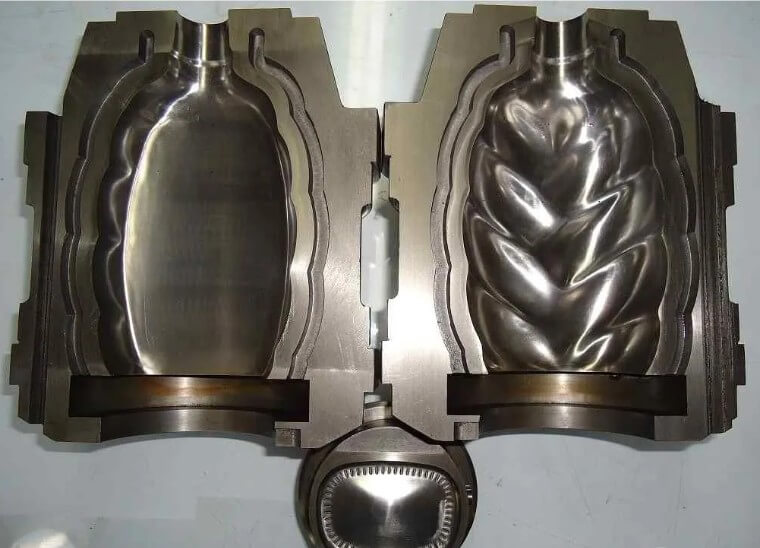
2.Application of molds in glass product production
In the production process of glass products, molds are widely used, covering a variety of fields from daily glassware to high-precision optical glass. For example, when producing glass bottles and jars, the mold determines the shape and size of the bottles and jars; when manufacturing glass plates, the mold ensures the flatness and thickness uniformity of the glass plates. In addition, the mold also plays a key role in the production of glassware. By precisely controlling the flow and cooling process of the glass liquid, glassware with complex shapes and high precision can be produced.
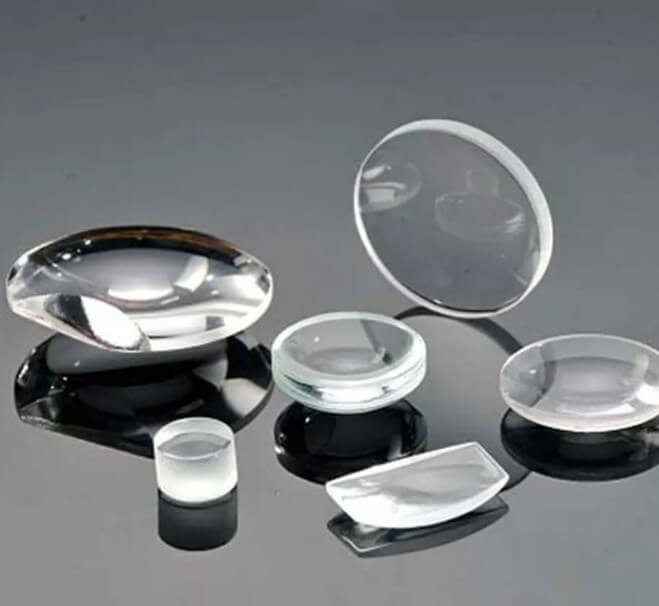
3.Material selection for glass casting molds
(1) Material requirements
Glass casting mold materials must have excellent high temperature resistance and thermal shock resistance to withstand the high temperature of the glass liquid and extreme temperature changes during the cooling process. In addition, the material should also have good corrosion resistance to resist erosion by chemicals in the glass liquid. The mechanical properties of the mold material are also one of the key factors. It needs to have sufficient strength and hardness to ensure the stability and durability of the mold in long-term use.
(2) Common material types
Common glass casting mold materials include cast iron, vermicular graphite cast iron and stainless steel. Cast iron is widely used due to its good cost-effectiveness and heat treatment performance; vermicular cast iron is suitable for the production of more complex or high-demand glass products due to its higher strength and better heat resistance; stainless steel is also used in some special occasions due to its excellent corrosion resistance.
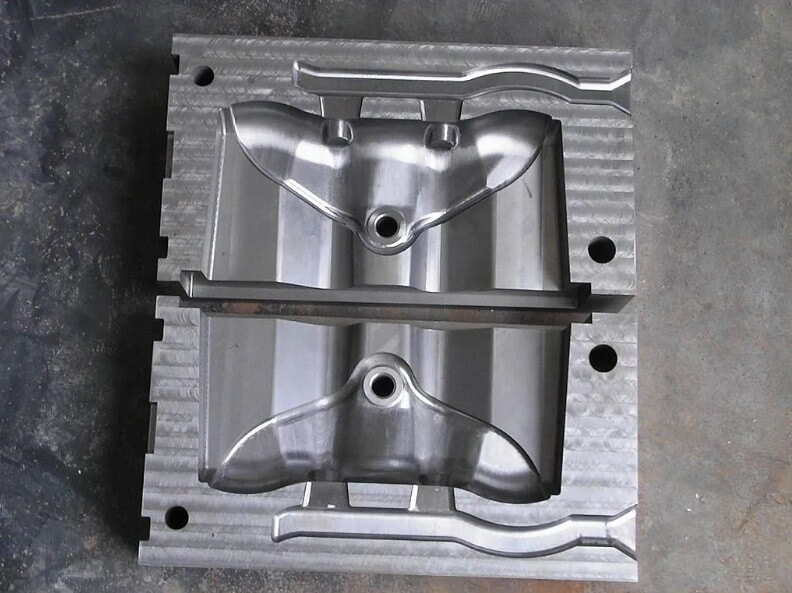
(3) Development and application of new materials
With the advancement of materials science, new mold materials are constantly emerging. For example, ceramic materials are gradually being used in the production of high-end glass products due to their extremely high temperature resistance and corrosion resistance. Composite materials combine the advantages of different materials and can provide better performance. They also show great potential in glass mold manufacturing.
Bimetallic composite materials are a type of metal material formed by layering two metal materials using their respective performance advantages. It has performance advantages that cannot be matched by a single metal, that is, it can reasonably design material combinations according to the use conditions of the workpiece, give full play to the performance characteristics of the two metals, make the parts have special properties to adapt to various harsh working conditions, and extend the service life of the parts.
4.Design technology of glass casting molds
(1) Traditional mold design method
Traditional glass casting mold design mainly relies on the designer’s experience and manual drawing. Although this method can meet basic design needs, it has the disadvantages of low efficiency and low precision when dealing with complex mold designs. Traditional design methods usually require multiple mold trials and modifications before the mold design scheme can be finally determined, which not only prolongs the production cycle but also increases production costs.
(2) Modern CAD/CAM technology
With the development of computer technology, CAD/CAM technology has become the mainstream tool for mold design. Through these technologies, designers can perform three-dimensional mold design on the computer and accurately simulate the flow and cooling process of glass liquid, thereby optimizing the mold structure. In addition, CAM technology can directly use design data for mold processing and manufacturing, improving production efficiency and mold precision. Modern CAD/CAM technology not only improves the design efficiency of glass casting molds, but also reduces the number of mold trials and modifications, thereby reducing production costs.
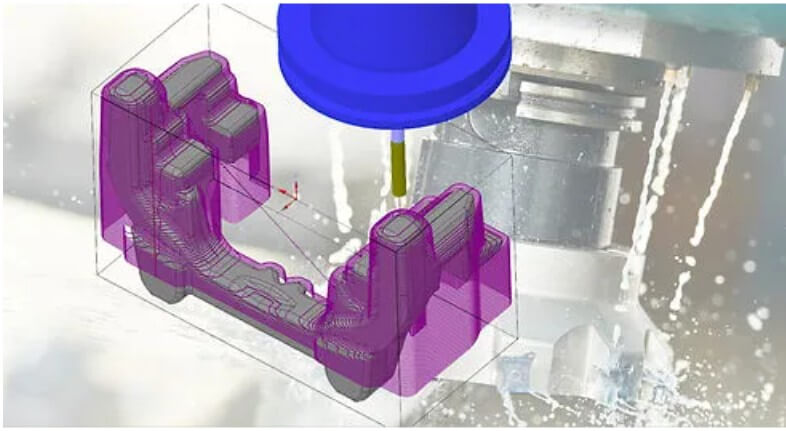
(3) Conformal cooling technology
Conformal cooling technology is a major innovation in mold design in recent years. By designing complex cooling water channels inside the mold, the coolant can be closer to the mold cavity, thereby achieving more uniform and faster cooling. This technology significantly improves the cooling efficiency of glass casting molds, shortens the production cycle, and also helps to improve the quality and consistency of glass products.
5.Manufacturing process of glass casting molds
(1) Casting process
In the manufacture of glass casting molds, commonly used casting processes include sand casting and precision casting. Sand casting is a traditional casting method suitable for making large or complex molds. Its advantages are low cost and wide adaptability, but relatively low precision and surface quality.
Precision casting can provide higher dimensional accuracy and surface finish, and is suitable for mold production with high quality requirements. Precision casting can significantly improve the accuracy and surface quality of glass casting molds by using special materials and processes, thereby meeting the high requirements of glass product production.
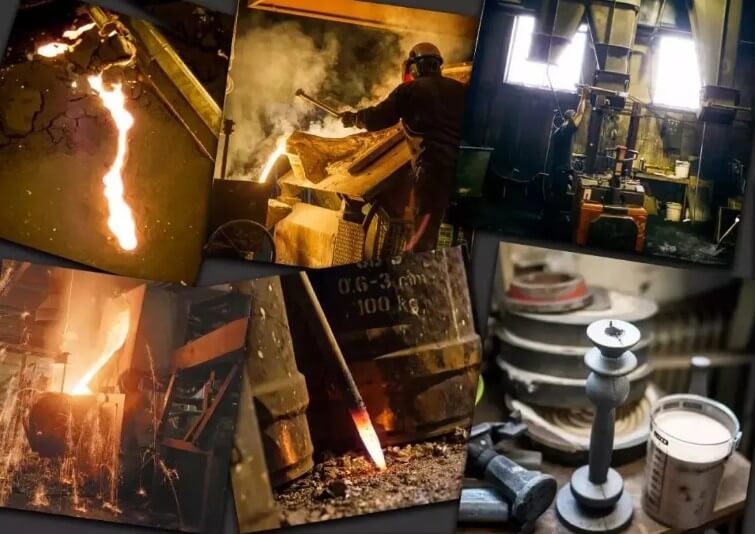
(2) Processing technology
CNC machining and EDM are commonly used precision machining technologies in mold manufacturing. CNC machining is carried out through computer-controlled machine tools and can accurately machine complex mold shapes.
EDM is suitable for machining metal materials with higher hardness, especially in the detailed machining of molds and complex cavity machining. The combined use of CNC machining and EDM can significantly improve the manufacturing accuracy and efficiency of glass casting molds and ensure the quality and production cycle of molds.
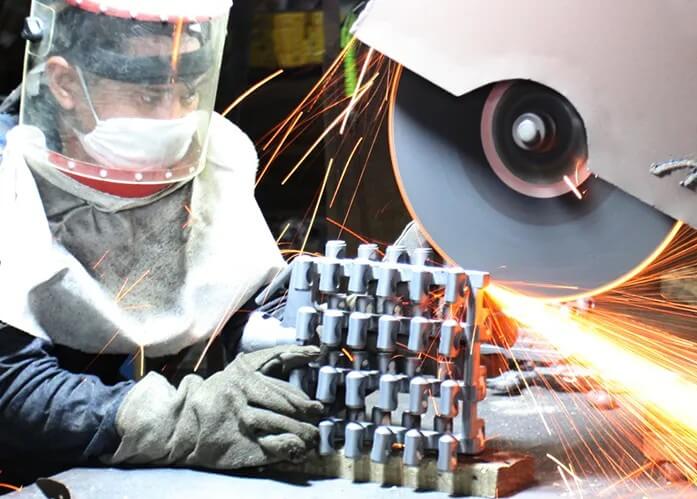
(3) Surface treatment technology
In order to improve the performance and life of the mold, surface hardening treatment and coating technology are widely used in mold manufacturing. Surface hardening treatment can enhance the hardness and wear resistance of the mold surface through physical or chemical methods.
Coating technology such as physical vapor deposition (PVD) and chemical vapor deposition (CVD) can form a thin and hard protective film on the mold surface to improve the mold’s corrosion resistance and oxidation resistance. Surface treatment technology can not only extend the service life of glass casting molds, but also improve the production efficiency and product quality of molds.
6.Use and maintenance of glass casting molds
(1) Installation and debugging of molds
The correct installation and debugging of molds are the key to ensuring the smooth progress of the production process. During the installation process, precise alignment is required to ensure the matching accuracy of the mold and mechanical equipment. During the debugging stage, it is necessary to check whether the opening and closing action of the mold, the cooling system, etc. are working normally to ensure that the mold can produce qualified glass products according to the design requirements. The installation and debugging of glass casting molds requires not only professional technicians, but also precise measuring tools and equipment to ensure the installation accuracy and debugging effect of the mold.
(2) Daily maintenance of molds
Daily maintenance is essential to keep glass casting molds in good condition and extend their service life. This includes regular cleaning of the molds, removal of residual glass and other impurities, and regular lubrication of moving parts to ensure smooth mold movement. In addition, regular performance checks should be conducted on the molds to promptly detect and repair potential problems.
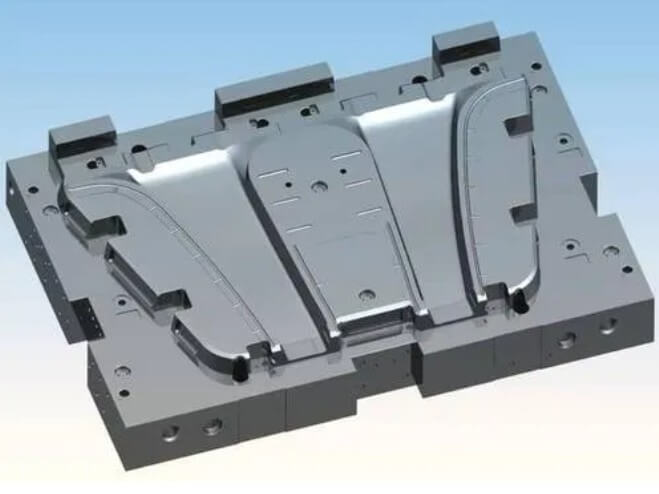
(3) Common failures and repair methods of glass casting molds
1) Cracks or breakage on the mold surface
Cause: Material fatigue, improper operation or improper maintenance.
Repair method: Stop using the mold and conduct a professional evaluation. If it can be repaired, use welding or glue repair; if it cannot be repaired, replace the corresponding parts or replace the mold as a whole.
2) Mold deformation
Cause: Long-term exposure to high temperature and high pressure, insufficient mold material strength or unreasonable cooling system design.
Repair method: Improve the cooling system, increase cooling channels or optimize cooling water distribution; for deformed molds, mechanical processing repair or heat treatment recovery can be performed.
3) Mold corrosion
Cause: Chemical substances in the glass liquid erode the mold material.
Repair method: Use corrosion-resistant materials or perform anti-corrosion treatment on the mold surface, such as nickel plating or using special coating technology.
4) Poor mold exhaust
Reason: The exhaust system is unreasonable or the exhaust hole is blocked during mold design.
Repair method: Optimize mold design, add exhaust holes or exhaust grooves; clean the exhaust holes regularly to ensure that the exhaust system is unobstructed.
5) Mold wear
Reason: Long-term use causes wear and tear due to friction between the mold surface and the glass liquid.
Repair method: Regularly inspect and maintain the mold surface, and use surface hardening treatment technology such as nitriding or chrome plating to improve wear resistance; when severely worn, the mold can be refurbished or replaced.
7.Summary
In short, the design, manufacture and maintenance of glass casting molds is a complex and delicate process that requires technical support from many aspects. Only by striving for excellence in every link can high-quality glass casting molds be manufactured to provide reliable guarantees for the production of glass products.