A356T6 aluminum castings: characteristics, applications and production process optimization
A356T6 aluminum castings occupy an important position in modern industry due to their excellent performance, especially in the fields of automobiles, aerospace and other fields. This article will explore in depth the characteristics, application fields, production processes and technical control, quality control and performance optimization of A356T6 aluminum castings, as well as common problems and solutions.
1.Basic information introduction of A356T6 aluminum castings
A356T6 aluminum castings are a type of component made of A356 aluminum alloy through a casting process, which is widely used in many important industrial fields, including automobiles, aerospace and military industries. A356 aluminum alloy is considered to be one of the preferred materials for high-end aluminum alloy castings due to its excellent mechanical properties, processing properties and corrosion resistance. A356 aluminum alloy is alloyed by adding elements such as silicon and magnesium to form a material with high strength and good plasticity. In addition, after the T6 heat treatment process, the mechanical properties of A356 aluminum alloy are further improved, making it perform well in a variety of applications.
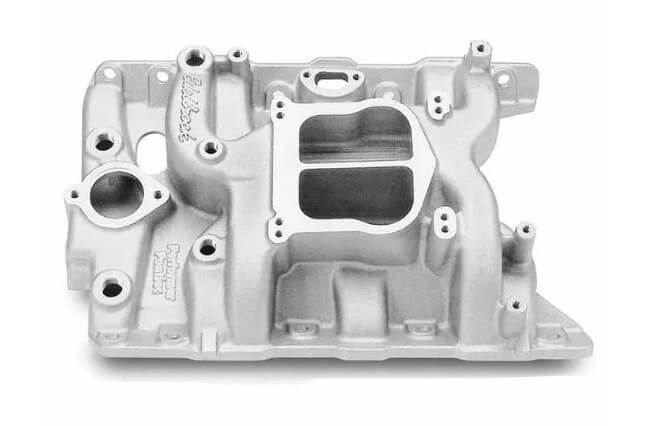
2.Analysis of the importance of A356T6 aluminum castings
The importance of A356T6 aluminum castings lies in their wide application prospects and ever-increasing performance requirements. With the continuous advancement of modern industrial technology, the requirements for material performance are becoming higher and higher, especially in terms of lightweight, high strength and high durability. In the automotive industry, lightweight is the key to improving fuel efficiency and reducing emissions, while in the aerospace field, lightweight and high-strength materials are an important factor in improving flight performance and fuel efficiency. Therefore, in-depth understanding of the characteristics of A356T6 aluminum castings and optimization of their production processes are of great significance to promoting the development of related industries.
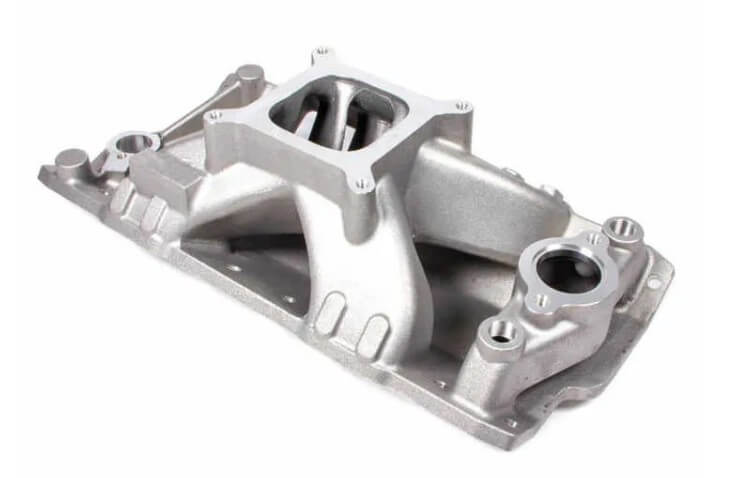
3.Analysis of A356 aluminum alloy characteristics and T6 heat treatment process
(1) Chemical composition and role of alloying elements
The main alloying elements of A356 aluminum alloy include silicon and magnesium, of which the silicon content is usually between 6.5% and 7.5%, and the magnesium content is between 0.25% and 0.45%. The addition of silicon improves the fluidity and wear resistance of the alloy, making it more suitable for casting processes; the addition of magnesium significantly improves the strength and toughness of the alloy. In addition, the addition of trace elements such as titanium and iron also plays a key role. Titanium can refine the grain structure and improve the mechanical properties of the material; iron is controlled at a low level to avoid adverse effects on the toughness and corrosion resistance of the alloy.
(2) Mechanical properties
After T6 heat treatment (solid solution treatment and artificial aging), A356 aluminum alloy shows excellent mechanical properties. Its tensile strength can reach more than 310MPa, its yield strength is about 275MPa, and its elongation can be maintained above 8%. This alloy not only has high strength, but also has good plasticity and toughness, which can meet various demanding application requirements. In terms of hardness, A356 aluminum alloy also performs well, and its hardness value is usually above HB95, which makes it have significant advantages in wear resistance and fatigue resistance.
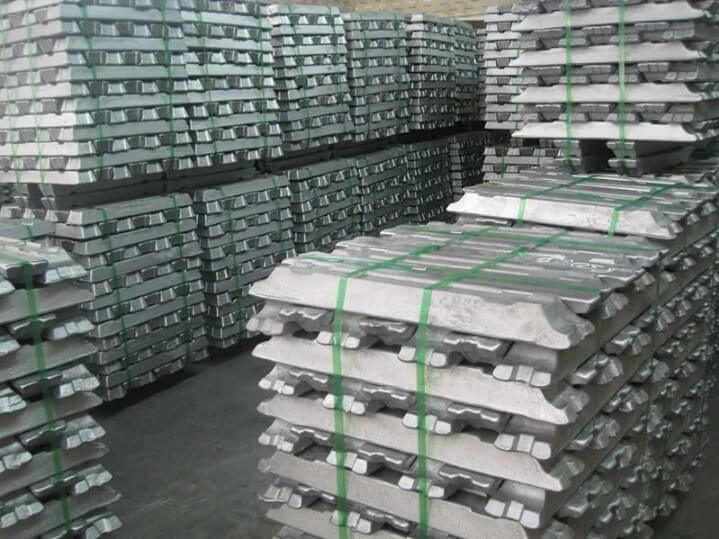
(3) Heat treatment effect
T6 heat treatment process is an important step in optimizing the performance of A356 aluminum alloy. During the solution treatment process, the alloy is heated to a certain temperature and maintained for a period of time to fully dissolve the alloying elements in the aluminum matrix. The subsequent quenching treatment rapidly cools the alloy to fix the supersaturated solid solution state.
Finally, through artificial aging treatment, the alloy elements are precipitated in the form of fine precipitates, which significantly enhances the strength and hardness of the alloy. In this process, the change in microstructure plays a decisive role in improving the performance of the alloy. The fine precipitates can effectively hinder the movement of dislocations, thereby improving the strength of the material.
4.Application fields of A356T6 aluminum castings
(1) Automobile industry
In the automobile industry, A356T6 aluminum castings are widely used in the manufacture of important components such as engine parts, gearbox housings, and wheels due to their excellent lightweight and high strength properties. The use of A356T6 aluminum castings can not only reduce the overall weight of the vehicle and improve fuel efficiency, but also enhance the safety and performance of the vehicle. For example, the use of aluminum wheels not only reduces the non-suspension mass and improves the handling and comfort of the vehicle, but also prolongs the service life of the tires and brake systems due to their good heat dissipation performance.
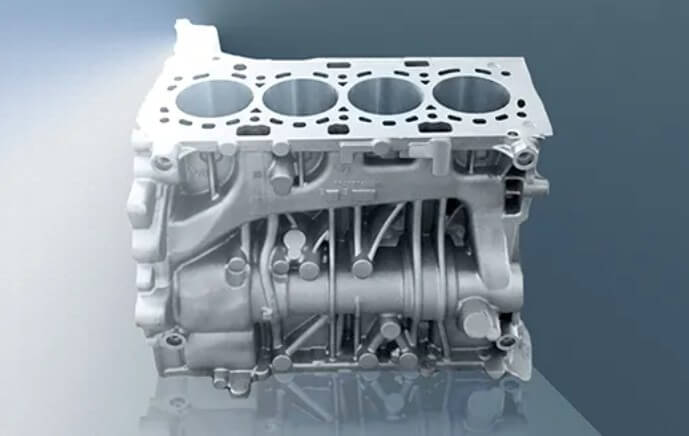
(2) Aerospace
The aerospace field has extremely strict requirements on materials. A356T6 aluminum castings have been widely used in this field due to their light weight and high strength. Aerospace components need to withstand extreme temperatures and pressures, and A356T6 aluminum castings can meet these stringent requirements. For example, A356T6 aluminum castings are used to manufacture aircraft structural parts, engine parts and other key components, which not only reduces the weight of the aircraft and improves fuel efficiency, but also enhances the safety and reliability of the aircraft.
(3) Applications in other industries
In addition to the automotive and aerospace fields, A356T6 aluminum castings have also found wide application in many other industries. For example, in the motorcycle and bicycle manufacturing industry, A356T6 aluminum castings are used to manufacture key components such as frames and wheels, improving the safety and performance of vehicles. In the manufacture of industrial equipment and mechanical parts, A356T6 aluminum castings are also widely used to manufacture various high-precision and high-reliability parts due to their excellent mechanical properties and corrosion resistance.
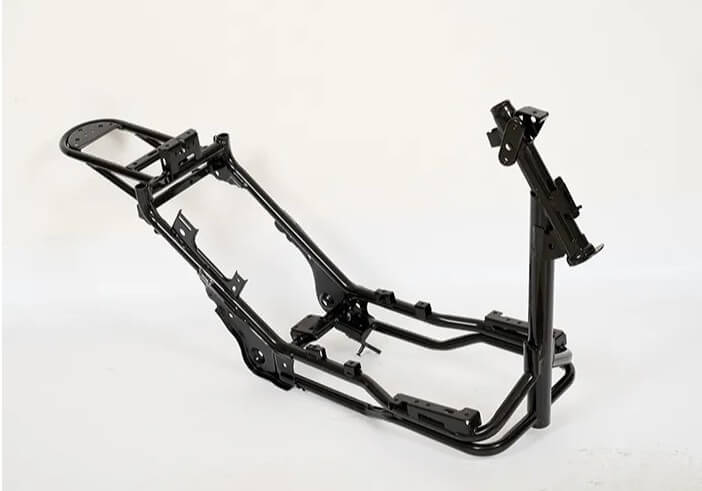
5.Production process and technical control of A356T6 aluminum castings
(1) Casting process selection
A356T6 aluminum castings are mainly produced by gravity casting and low-pressure casting. Gravity casting is one of the most commonly used methods. It is simple to operate, low-cost and suitable for mass production. However, gravity casting is prone to defects such as pores and shrinkage, which affect the quality of the castings. Low-pressure casting applies low pressure in the mold to slowly fill the mold with molten aluminum, which can effectively reduce pores and shrinkage and improve the density and surface quality of the castings. Low-pressure casting is particularly suitable for producing castings with complex structures and large wall thickness differences.
(2) Melting and casting process control
In the production process of A356T6 aluminum castings, the control of the melting and casting process is the key to ensuring the quality of the castings. First, the selection and preparation of raw materials are crucial. It is necessary to ensure that the alloy composition meets the standards and avoid excessive impurity content. Second, the melting temperature and time need to be strictly controlled to ensure that the alloy elements are fully dissolved and evenly distributed. During the smelting process, a rotary argon refining device is usually used for degassing to remove gas and non-metallic inclusions in the aluminum liquid and improve the purity of the alloy.
(3) Post-processing process
The post-processing process after casting is equally important, mainly including cleaning and surface treatment. The cleaning process needs to remove the oxide scale and burrs on the surface of the casting to ensure a smooth surface. Surface treatment can improve the corrosion resistance and aesthetics of A356T6 aluminum castings through methods such as sandblasting and anodizing.
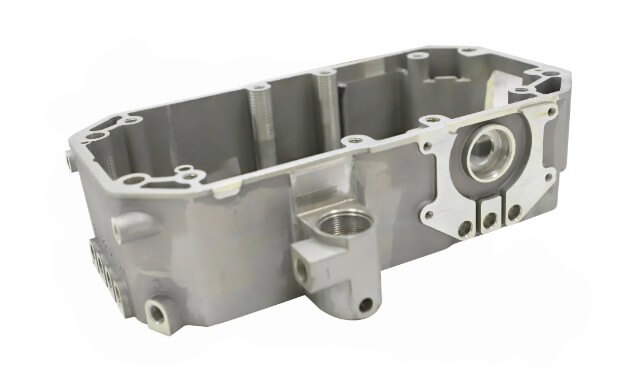
6.Quality control and performance optimization of A356T6 aluminum castings
(1) Control of chemical composition
Precise control of the chemical composition of A356T6 aluminum castings is the basis for its performance optimization. During the production process, alloying elements such as silicon and magnesium need to be added in strict accordance with the standards, and the content of trace elements such as titanium and iron needs to be controlled. Through scientific composition design, the mechanical properties and corrosion resistance of the alloy can be effectively improved. For example, the appropriate addition of rare earth elements can refine the grains and improve the mechanical properties and heat resistance of the alloy.
(2) Process parameter optimization
Casting speed and cooling rate are important factors affecting the quality of A356T6 aluminum castings. Reasonable casting speed can ensure that the aluminum liquid fills the mold evenly and avoids defects. Appropriate cooling rate helps to control the grain size and distribution of precipitation phase and improve the mechanical properties of the alloy. In actual production, the casting and cooling process can be optimized by adjusting parameters such as mold temperature and cooling medium flow rate.
(3) Quality inspection standards and methods
The quality inspection of A356T6 aluminum castings needs to follow international standards such as ASTM and BSEN. Common inspection methods include mechanical property testing, metallographic microscope observation, X-ray inspection, non-destructive testing, etc. Through systematic quality inspection, the internal quality and surface quality of the casting can be ensured to meet the needs of various applications.
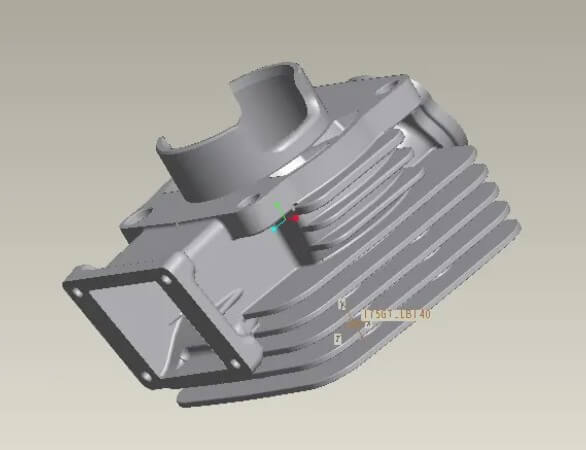
7.Common problems and solutions of A356T6 aluminum castings
A356T6 aluminum castings are widely used in industry and manufacturing due to their excellent mechanical properties and corrosion resistance. However, in the production process, A356T6 aluminum castings often face some challenges. The following are some common problems and their solutions:
(1) Oxidation inclusions:
It is manifested as the inclusion of oxidized materials on the surface or inside the casting. The cause may be unclean charge or slag that has not been removed cleanly. Solutions include ensuring that the charge is clean, reducing the use of return charge, and using appropriate flux to remove slag.
(2) Porosity:
Gas forms holes inside the casting, affecting the strength of the casting. The cause may be poor design of the casting system or poor venting of the molding sand. Solutions include optimizing the design of the casting system to ensure smooth casting and improving the venting capacity of the molding sand.
(3) Shrinkage:
Porosity is formed due to poor shrinkage compensation during the solidification process of the casting. The cause may be improper riser design or excessively high pouring temperature. Solutions include improving the riser design to improve the shrinkage compensation effect and controlling the pouring temperature and speed.
(4) Cracks:
Cracks form in the casting during the cooling process. The cause may be unreasonable casting structure design or improper heat treatment. Solutions include optimizing the casting structure design to reduce stress concentration and strictly controlling the heat treatment process parameters.

8.Summary
With the advancement of technology, the development of A356T6 aluminum castings in the future will pay more attention to the improvement of performance and the reduction of production costs. The combined use of new materials and new technologies, such as the addition of rare earth elements and advanced casting technology, will further promote the application and development of A356T6 aluminum castings.