Aluminum metal castings: lightweight revolution and multi-industry application expansion
In modern industry, aluminum metal castings have become an indispensable component in many industries due to their unique advantages. From automobiles to aviation, from household appliances to industrial equipment, the application range of aluminum metal castings is expanding day by day. This article will discuss the characteristics, production process, wide range of applications, advantages and precautions during the production process of aluminum metal castings.
1.Basic characteristics and classification of aluminum metal castings
(1) Physical and chemical properties of aluminum
Aluminum is a lightweight metal with good electrical and thermal conductivity and corrosion resistance. These properties make aluminum widely used in multiple industries. The density of aluminum is about one-third that of steel, which allows aluminum metal castings to significantly reduce the weight of the structure while maintaining high strength. It is very suitable for areas with strict weight requirements, such as the aerospace and automotive industries. . In addition, the surface of aluminum easily forms a dense oxide film. This oxide film can effectively prevent further oxidation of aluminum and provide good corrosion resistance.
(2) Classification and main uses of aluminum alloys
Aluminum alloys are materials whose mechanical properties are improved by adding other elements (such as copper, magnesium, silicon, etc.) to aluminum. Aluminum alloys can be divided into many types based on the added elements, and each type has its specific application scenarios.
For example, the 2xxx series of aluminum alloys contain copper and magnesium, have high strength, and are often used in the aerospace field; the 6xxx series of aluminum alloys contain magnesium and silicon, have good processability and corrosion resistance, and are widely used in the construction and automotive industries.The 7xxx series of aluminum alloys contain zinc and have ultra-high strength, and are usually used to manufacture high-strength structural parts.
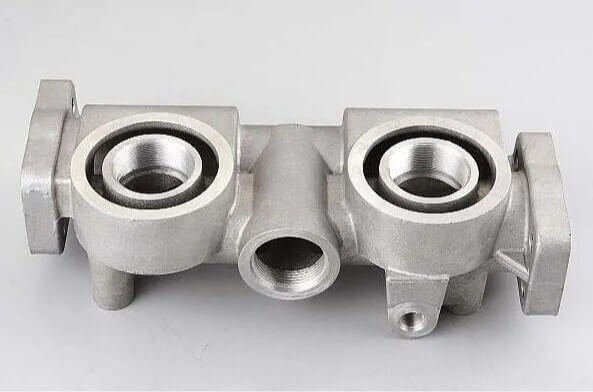
2.Production process of aluminum metal castings
(1) Overview of casting process
The production of aluminum metal castings is mainly carried out through the following casting processes:
1) Sand casting
This process uses a sand mold as a mold. First, a sand mold is made, and then molten aluminum liquid is injected into the sand mold to cool and form. The sand casting process is simple and low-cost, and is suitable for producing aluminum metal castings of various shapes and sizes. However, sand casting has a higher surface roughness and usually requires subsequent processing.
2) Metal mold casting
It is a process that uses metal molds for shaping. Metal molds are usually made of high-strength alloy steel and can be used repeatedly, making them suitable for mass production. The aluminum metal castings produced by metal mold casting have smooth surfaces and high precision. Due to the fast cooling rate of the metal mold, the castings have a denser structure and excellent mechanical properties. However, the production cost of metal molds is high and the cycle time is long.
3) Pressure casting
Pressure casting is an efficient and high-precision aluminum metal casting production process. This process uses a die-casting machine to quickly inject molten aluminum into the mold under high pressure to form. The die-casting process can produce aluminum castings with smooth surfaces and extremely high dimensional accuracy, with extremely high production efficiency and suitable for mass production. However, the cost of die-casting equipment and molds is high, and defects such as pores may occur during the die-casting process.
4) Low pressure casting
Low pressure casting is a process that combines the advantages of gravity casting and pressure casting. This process injects molten aluminum into the mold under low pressure conditions, avoiding the porosity problem that may occur in high-pressure casting while maintaining high production efficiency. Aluminum castings produced by low-pressure casting have good surface quality and high dimensional accuracy, and are suitable for producing high-quality small and medium-sized castings.
5) Investment casting
This process first makes a wax model, and then coats the surface of the wax model with multiple layers of refractory materials to form a shell. The shell is heated to melt the wax model and flow out, and then liquid aluminum is injected into the mold. Investment casting can produce aluminum metal castings with complex shapes and smooth surfaces, and is suitable for high-precision casting production in aerospace and other fields. However, the process of investment casting is complex, the cost is high, and the production cycle is long.
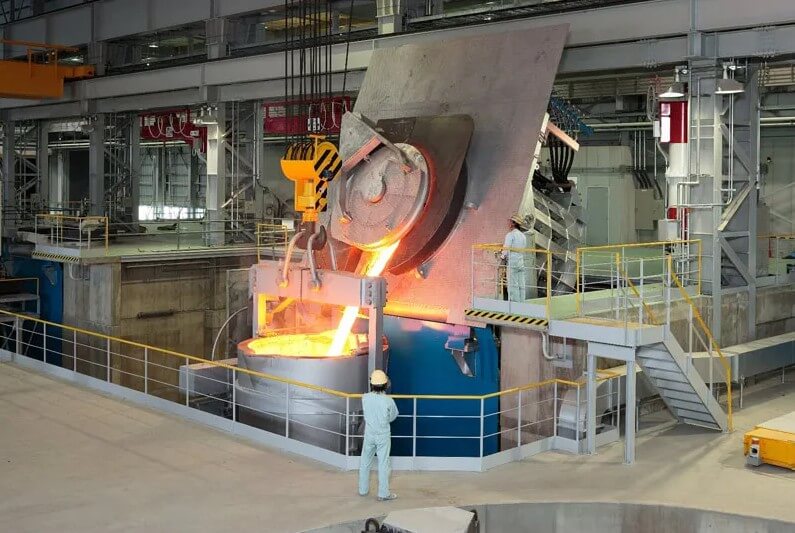
(2) Continuous casting technology
Continuous casting technology is an efficient casting method that can improve production efficiency and reduce costs. Mainly include the following categories:
1) Semi-continuous casting method:
Aluminum castings are produced by continuous pouring and cooling and are suitable for the production of large-sized aluminum plates and profiles.
2) Hot top casting method:
Maintain a high temperature at the top of the mold during the pouring process to reduce defects in the casting and improve the quality of the casting.
3) Electromagnetic casting method:
Using electromagnetic fields to control the flow and solidification of molten aluminum can produce high-quality, pollution-free aluminum castings.
4) Horizontal continuous casting:
Continuous pouring and cooling in the horizontal direction produce aluminum castings, which are suitable for producing small-sized, high-precision aluminum products.
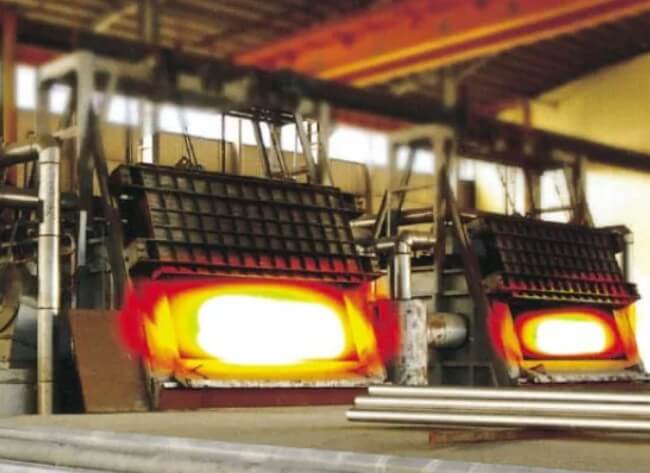
3.Application advantages of aluminum metal castings:
(1) Lightweight:
The density of aluminum is about one-third that of steel. Using aluminum metal castings can significantly reduce the weight of products, which is particularly important for automobiles, aviation and other fields, helping to improve fuel efficiency and reduce carbon emissions.
(2) High specific strength:
The higher specific strength (ratio of strength to weight) of aluminum alloy castings means that under the same load, aluminum metal castings can be designed to be thinner and lighter while maintaining sufficient structural strength.
(3) Corrosion resistance:
Aluminum metal castings have good corrosion resistance in the atmosphere and fresh water, are not easy to rust, and are suitable for long-term use in a variety of environments.
(4) Thermal conductivity:
Aluminum has good thermal conductivity and is suitable for manufacturing heat exchangers, radiators and other components, such as automobile engine cylinder heads and pistons.
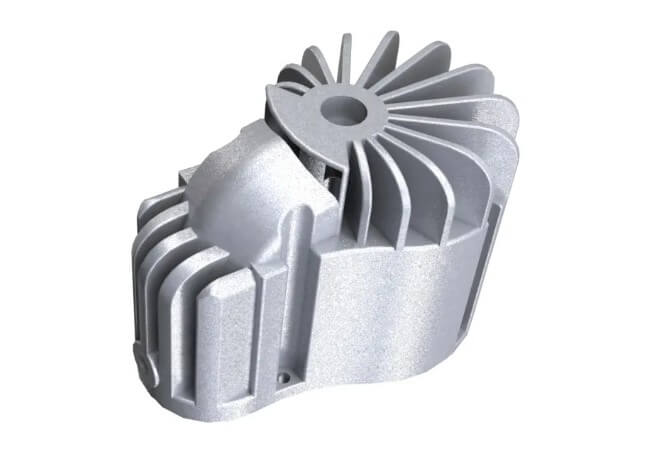
(5) Casting performance:
Aluminum has a low melting point and good fluidity, making it easy to cast parts with complex shapes. At the same time, aluminum castings have high dimensional accuracy and good surface finish.
(6) Recyclability:
Aluminum is an infinitely recyclable material. Recycling aluminum castings can save a lot of energy and resources and reduce environmental pollution.
(7)Aesthetics:
The surface gloss of aluminum metal castings is good, and rich colors and textures can be obtained through different surface treatment technologies (such as anodizing) to meet the needs of decoration and aesthetics.
(8) Economy:
Although the initial cost of aluminum castings may be higher than some traditional materials, considering the long-term energy savings and lower maintenance costs caused by its lightweight, aluminum castings have better economics overall.
4.Application fields of aluminum metal castings
(1) Aerospace
In the aerospace field, aluminum metal castings are widely used due to their high strength, low density and good corrosion resistance. Aluminum castings can significantly reduce the weight of aircraft and improve fuel efficiency and flight performance. For example, aircraft fuselage structures, engine components, landing gear and other key components all use aluminum castings in large quantities.
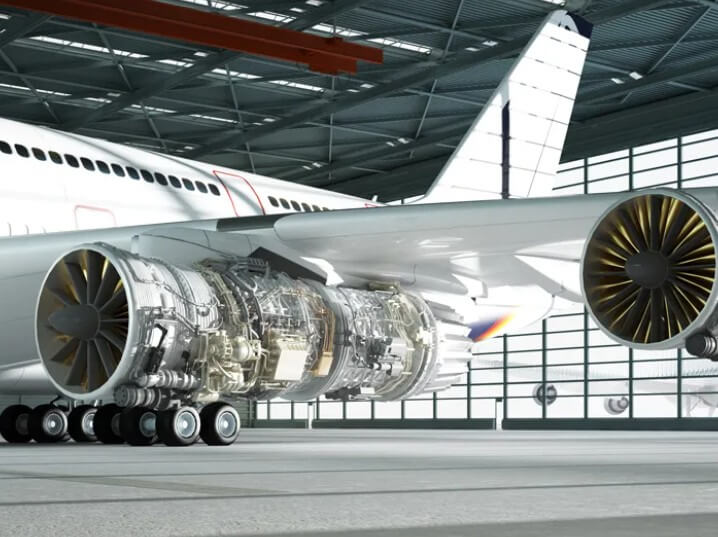
(2) Automobile industry
With the trend of lightweight automobiles, aluminum castings are increasingly used in automobiles. It can reduce the overall weight of the car, improve fuel efficiency and reduce emissions. In addition, it also has good corrosion resistance and thermal conductivity, and is suitable for manufacturing automobile engine parts, body structures, wheels, etc.
(3) Architectural decoration
The application of aluminum castings in the field of architectural decoration is mainly concentrated in doors, windows, curtain walls, decorative panels, etc. Aluminum castings have the advantages of beauty, corrosion resistance, and easy processing, and can meet the high requirements for material performance in architectural decoration.
(4) Electronic communication
In the field of electronic communications, aluminum metal castings are mainly used to manufacture housings, radiators, etc. for electronic equipment. Aluminum castings have good thermal conductivity and electromagnetic shielding properties, which can effectively improve the heat dissipation performance and electromagnetic compatibility of electronic equipment.
(5) Chemical industry:
Aluminum metal castings are widely used in the manufacture of key components such as containers, pipes, and reactors in chemical equipment due to their excellent corrosion resistance and good strength. They can effectively resist the erosion of corrosive media such as acids and alkalis, ensuring the long-term effectiveness of the equipment. Stable operation.
(6) Marine field:
Aluminum metal castings also play an important role in marine engineering, such as for the manufacture of helicopter deck modules for offshore oil drilling platforms. These modules are spliced together from aluminum alloy profiles. They are light in weight, have good strength and stiffness, have excellent corrosion resistance and are easy to maintain. In addition, aluminum alloy is also widely used in storage tanks of LNG cargo ships. Its excellent low-temperature performance ensures the safety of LNG during transportation.
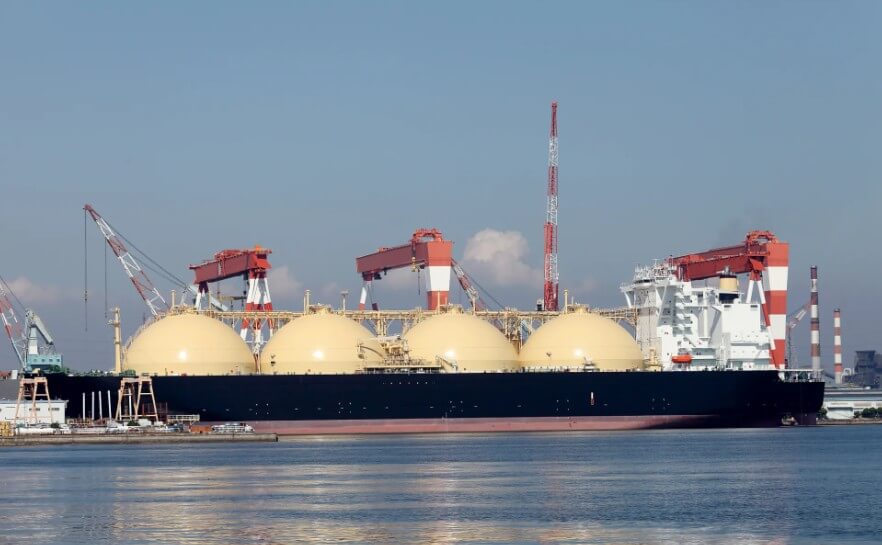
5.Precautions during the production process of aluminum metal castings
(1) Equipment inspection:
Before production begins, ensure that all equipment is operating normally, including key components such as lubrication systems, wire ropes, and switches, to avoid production interruptions or casting defects caused by equipment failure.
(2) Preheating treatment:
Preheat the dummy head, launder and related casting tools, and ensure that the filter is installed in place to prevent the aluminum liquid from being contaminated or causing cold shut-off defects during the casting process.
(3) Control pouring speed and temperature:
The pouring speed and temperature of aluminum metal need to be strictly controlled. Too fast a pouring speed may cause gas to be entangled and form pore defects; too high a temperature may cause coarse grains and affect the mechanical properties of the casting.
(4) The crystallizer is filled with aluminum water:
Make sure the crystallizer is filled with aluminum water before starting the casting process to prevent defects caused by insufficient aluminum water, such as shrinkage and cold shut.
(5)Finishing operations:
At the end of casting, stop the casting machine first and then stop the water to ensure that all the aluminum water in the crystallizer has flowed out to avoid shrinkage holes or looseness in the casting.
(6) Replace damaged parts:
Regularly inspect and replace damaged graphite rings or other key components to ensure casting quality and the smooth progress of the production process.
(7) Prevent oxidation and slag inclusion:
Aluminum metal is easily oxidized, and appropriate flux should be used to cover and protect it during the casting process to reduce the generation of oxidized slag inclusions.
(8) Control cooling speed:
The cooling rate of the casting needs to be moderate. If it is too fast, it may lead to an increase in internal stress and crack defects. If it is too slow, it may cause coarse grains and a decrease in mechanical properties.
6.Conclusion
Aluminum metal castings play an increasingly important role in modern industry because of their excellent properties. Through continuous technological innovation and application expansion, aluminum metal castings will continue to provide efficient and lightweight solutions for many industries.