Sand casting aluminum: process and technology development
As a traditional metal forming technology, sand casting aluminum still plays an important role in modern industry. At the same time, with the advancement of technology, the sand casting aluminum process is also constantly innovating. This article will explore in depth the material and equipment selection, process flow, common problems and solutions, and the application of new materials and new technologies for sand casting aluminum.
1.Overview of sand casting aluminum
(1) Definition
Sand casting aluminum is a process that uses sand as the main molding material. By pouring molten aluminum into a sand mold and waiting for it to cool and solidify, aluminum castings of the desired shape and size are obtained.
(2) Introduction to the process flow and basic principles:
The basic process of sand casting aluminum includes making a model, preparing a sand mold, melting aluminum alloy, pouring, cooling, sand removal, and cleaning. First, a model is made according to the design requirements of the casting; then, a sand mold is made using the model, and the molding sand and binder are prepared. Next, the aluminum is melted and heated to an appropriate temperature. During the pouring process, the molten aluminum liquid is poured into the prepared sand mold. After it cools and solidifies, the sand is removed and cleaned to finally obtain the casting.
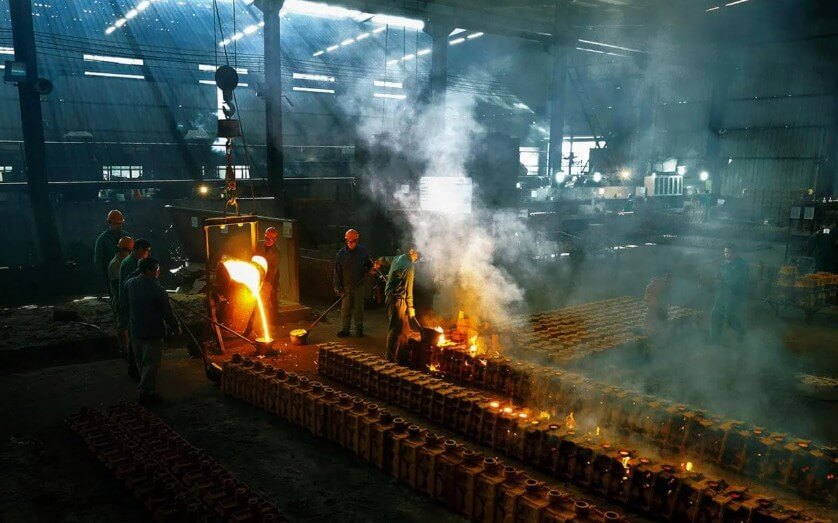
2.Material selection for sand casting aluminum
(1) Selection and characteristics of aluminum:
In sand casting, the selection of aluminum is very critical. Commonly used aluminum alloys include ZL101, ZL104 and other series. ZL101 alloy is widely used in the manufacture of various complex shapes of castings due to its excellent casting performance and mechanical properties; while ZL104 alloy is widely used in the manufacture of high-strength and high-hardness castings due to its high strength and hardness.
(2) Material types and functions of molding sand and binder:
Molding sand usually uses silica sand, and binder usually uses clay or synthetic resin. Silica sand is widely used because of its good high temperature resistance and low price; clay binder is widely used because of its good bonding performance and low price; and synthetic resin binder is widely used in the production of high-precision and high-complexity castings due to its high bonding strength and good high temperature resistance.
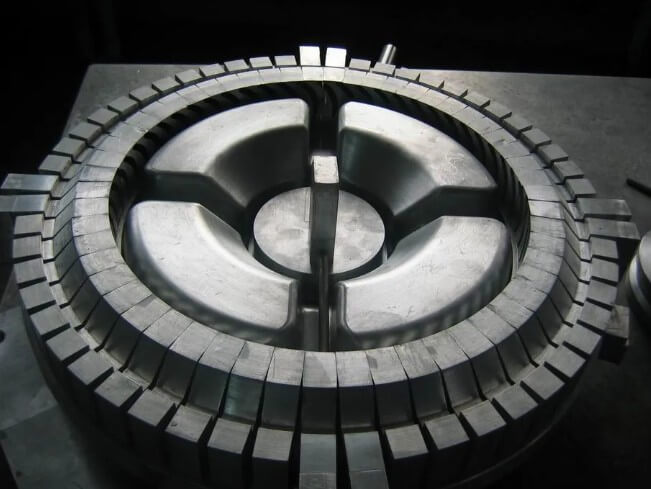
3.Introduction to the main equipment for sand casting aluminum
(1) Sand mixing equipment, molding equipment, smelting equipment, etc:
Sand mixing equipment is used to evenly mix the molding sand and binder, molding equipment is used to make castings, and smelting equipment is used to heat and melt aluminum. Commonly used sand mixing equipment includes sand mixers and sand grinders; commonly used molding equipment includes molding machines, compactors, and demolders; commonly used smelting equipment includes smelting furnaces and holding furnaces.
(2) Functions and operating points of each equipment:
Sand mixing equipment needs to control the mixing ratio and uniformity, molding equipment needs to ensure the dimensional accuracy and surface quality of the casting, and smelting equipment needs to accurately control the heating temperature and time to prevent aluminum oxidation or overheating.
The operating points of sand mixing equipment include controlling the sand mixing time and sand mixing speed to ensure that the molding sand and binder are fully mixed; the operating points of molding equipment include controlling the compaction pressure and demolding speed to ensure the dimensional accuracy and surface quality of the casting; the operating points of smelting equipment include controlling the heating temperature and time to ensure that the aluminum solution is fully melted and evenly heated.
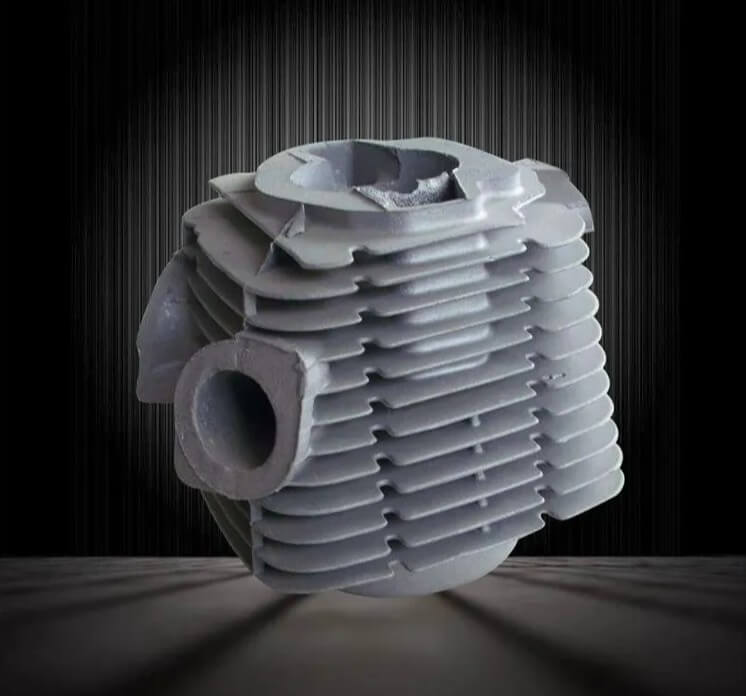
4.Process of sand casting aluminum
(1) Model making
1) Types and making methods of models:
The model is the basis of sand casting aluminum and is usually made of wood, metal or plastic. The model needs to be made with high precision to ensure that the size and shape of the casting meet the requirements. Wood models are used because of their ease of production and low cost; metal models are widely used because of their high precision and durability; plastic models are used because of their lightness and high precision.
2) Model design considerations:
When designing the model, factors such as shrinkage and draft angle during the casting process need to be considered to avoid casting defects. Shrinkage is the volume shrinkage of aluminum during cooling and solidification, which needs to be compensated when designing the model; draft angle is the side slope of the model designed to facilitate demolding, which needs to be reasonably designed according to the shape and size of the casting.
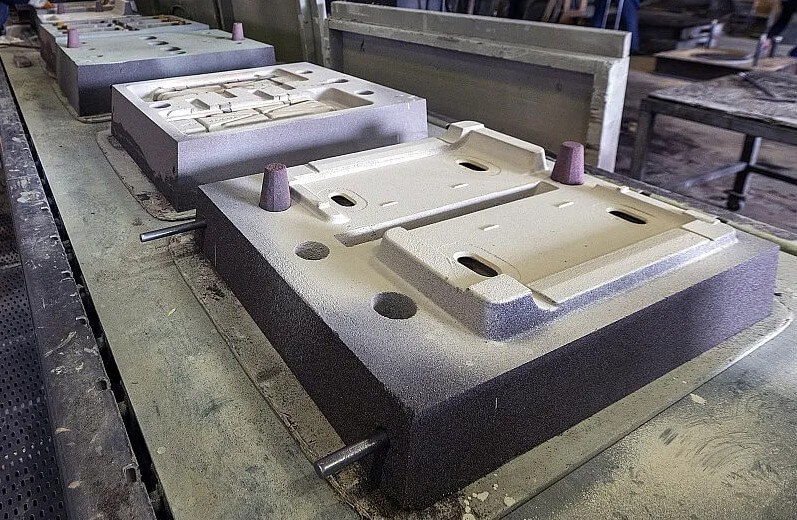
(2) Molding and core making
1) Preparation and use of molding materials:
Molding materials mainly include molding sand and binder. Molding sand needs to have good air permeability and fire resistance, and binder needs to provide sufficient strength to maintain the integrity of the sand mold. The preparation of molding sand includes steps such as screening, mixing and drying to ensure the uniformity and dryness of the molding sand; the use of binder includes steps such as brushing, spraying and mixing to ensure the uniformity and sufficiency of the binder.
2) Core making process and its importance:
The core box is used to form the complex cavity structure inside the casting. The accuracy of core making directly affects the quality of the casting. The core making process includes steps such as making the core box, filling the molding sand, drying and curing to ensure the dimensional accuracy and surface quality of the core box. The importance of core making lies in its ability to form the complex structure inside the casting and improve the overall performance and accuracy of the casting.
(3) Melting and pouring
1) Aluminum smelting technology and temperature control:
Smelting is a key step in the process of sand casting aluminum and needs to be carried out in a dedicated melting furnace. The temperature needs to be precisely controlled during the melting process to ensure that the aluminum is completely melted and does not overheat or oxidize. Commonly used melting furnaces include resistance furnaces, induction furnaces and gas furnaces, each with its own advantages and disadvantages, and need to be selected according to specific needs.
2) Key technologies in the pouring process:
During pouring, the flow rate and temperature of aluminum liquid need to be controlled to avoid the generation of bubbles and inclusions. The pouring process includes steps such as preparing the pouring system, controlling the pouring speed and temperature, and cleaning the pouring channel to ensure the smooth progress of the pouring process and the quality of the casting.
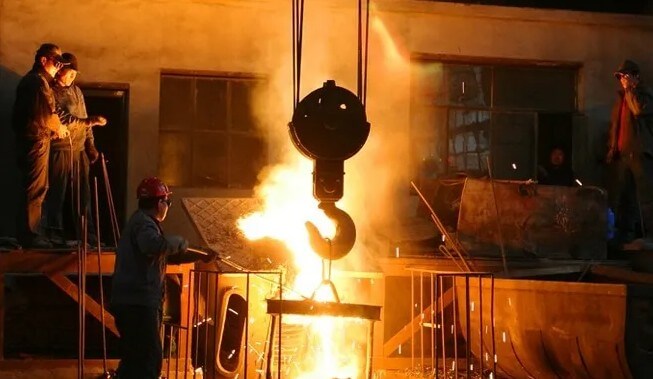
(4) Sand dropping and cleaning
1) Sand dropping and cleaning methods for castings:
Sand dropping refers to the process of separating the casting from the sand mold, usually by vibration or fluid impact. Sand dropping methods include mechanical sand dropping, hydraulic sand dropping, and air flow sand dropping, each with its own advantages and disadvantages, so you need to choose;
Cleaning includes removing sand and excess metal from the surface of sand-cast aluminum castings. Cleaning methods include sand blasting, shot blasting, and chemical cleaning, each with its own advantages and disadvantages, so you need to choose.
2) Subsequent treatment and surface finishing of sand-cast aluminum:
Subsequent treatment may include heat treatment, machining, etc. to improve the mechanical properties or dimensional accuracy of the casting. Heat treatment methods include annealing, normalizing, quenching and tempering, etc.; mechanical processing methods include turning, milling, grinding and drilling, etc., each has its own advantages and disadvantages, so you need to choose one.
5.Common problems and solutions of sand casting aluminum
Sand casting aluminum is a common metal forming process, but in actual operation, various problems are often encountered, affecting the quality and performance of the casting. The following are several common problems and solutions in the sand casting aluminum process.
(1) Undercasting and cold shut
1) Problem description: Undercasting refers to incomplete casting shape, while cold shut refers to incomplete fusion seams on the surface of the casting.
2) Cause analysis: Insufficient fluidity of molten metal, too low pouring temperature, too slow filling speed, etc.
3) Solution: Increase the pouring temperature and speed to ensure that the molten metal maintains sufficient fluidity during the filling process. At the same time, optimize the pouring system design to ensure that the molten metal can smoothly fill the cavity.
(2) Porosity
1) Problem description: Porosity appears inside or on the surface of the casting, affecting the mechanical properties and appearance of the casting.
2) Cause analysis: poor permeability of the molding sand, high gas content in the molten metal, poor design of the pouring system, etc.
3) Solution: reduce the gas content in the molten metal, increase the permeability of the sand mold, and add a gas outlet at the highest point of the cavity. Optimize the pouring system to prevent the molten metal from being drawn into the gas during the filling process.
(3) Sand sticking
1) Problem description: a layer of sand particles that are difficult to remove adhere to the surface of the casting, affecting the appearance and subsequent processing.
2) Cause analysis: improper selection of binder in the molding sand, excessively high pouring temperature, poor effect of the coating on the surface of the casting, etc.
3) Solution: add an appropriate amount of coal powder or other anti-sand sticking materials to the molding sand, and apply an effective anti-sand sticking coating on the surface of the casting. Control the pouring temperature to avoid excessively high temperatures that cause sand sticking.
(4) Shrinkage and shrinkage
1) Problem description: holes are formed in the casting due to volume shrinkage during solidification, affecting the density of the casting.
2) Cause analysis: pouring temperature is too high, cooling speed is too slow, shrinkage compensation system design is unreasonable, etc.
3) Solution: Optimize pouring temperature and cooling speed, scientifically and reasonably design risers and chillers to ensure that the casting can be fully compensated during solidification. At the same time, improve the structure of the casting to avoid excessive thickness difference.
(5) Cracks
1) Problem description: Cracks appear on the surface or inside of the casting, which seriously reduces the mechanical properties of the casting.
2) Cause analysis: unreasonable casting structure design, too fast cooling speed, improper heat treatment process, etc.
3) Solution: Improve the casting structure design to avoid sharp corners and excessive wall thickness changes. Control the cooling speed to avoid cracks caused by excessive internal stress. Optimize the heat treatment process to ensure that the casting can be evenly heated and cooled during the heat treatment process.
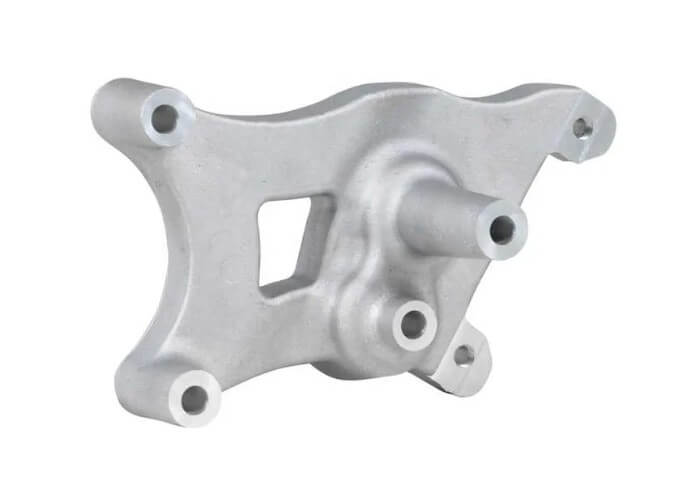
Summary:
Through the analysis of the above problems and their corresponding solutions, the quality and performance of sand casting aluminum can be effectively improved, casting defects can be reduced, and production efficiency can be improved.
6.Application of new materials and technologies in sand casting aluminum
(1) High-performance aluminum materials:
With the development of science and technology, new high-performance aluminum materials are constantly being developed. These materials have better strength, toughness or heat resistance and can meet higher standards of application requirements. For example, new high-strength aluminum alloy materials are widely used in aerospace and automobile manufacturing due to their excellent mechanical properties; new heat-resistant aluminum alloy materials are widely used in the manufacture of engine and turbine components due to their excellent high-temperature performance.
(2) Application of 3D printing technology in sand casting aluminum:
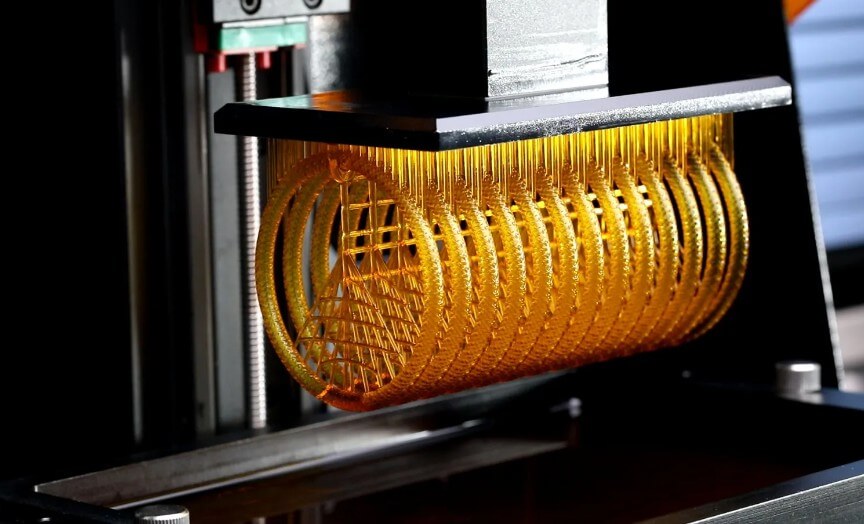
3D printing technology has also been introduced into sand casting aluminum to manufacture more complex and precise molds and core boxes, greatly improving the flexibility and efficiency of casting. 3D printing technologies include selective laser sintering (SLM), selective laser melting (SLA) and fused deposition modeling (FDM), each with its own advantages and disadvantages, so you need to choose.
7.Summary
The continuous advancement of technology, such as the application of new materials and the promotion of new technologies, will further promote the development of the sand casting aluminum industry, improve the quality and production efficiency of castings, and reduce production costs.