UAV parts molding: introduction to five molding processes
UAV are now being used more and more, whether in the express delivery industry, video shooting, or the agricultural field. Whether a UAV is easy to use has a lot to do with its parts materials and processing methods.
Different materials, such as plastics, metals, and composite materials, require different processes to be processed. At present, plastic injection molding is the main process, but with the expansion of other application fields, other processes are also used. So what is the process of UAV parts molding? The following will introduce it in detail.
1.Are all UAV parts made of plastic? What other materials are there besides plastic?
UAV parts are not all made of plastic. The material selection must take into account the final weight of the UAV, your preset material and processing costs, and what functional requirements this UAV wants to meet. The following will introduce three common materials:
(1) Plastic:
Such as ABS, nylon, etc., used for shells, connectors, etc., the advantages are lightweight, easy to mold, low cost, but limited strength.
(2) Metals:
Aluminum alloy: used for motor brackets, fuselage frames, etc., lightweight and high strength, good processing performance.
Stainless steel: used for shafts, fasteners, etc., strong wear resistance, used in high-load places, such as agricultural UAV.
(3) Composite materials:
Carbon fiber composite materials: used for wings and fuselage frames. This material has the characteristics of high strength and low density, which can significantly improve flight performance.
Glass fiber composite materials: The cost is lower than carbon fiber, and it takes into account both strength and lightness. It is suitable for small and medium-sized UAV structural parts.
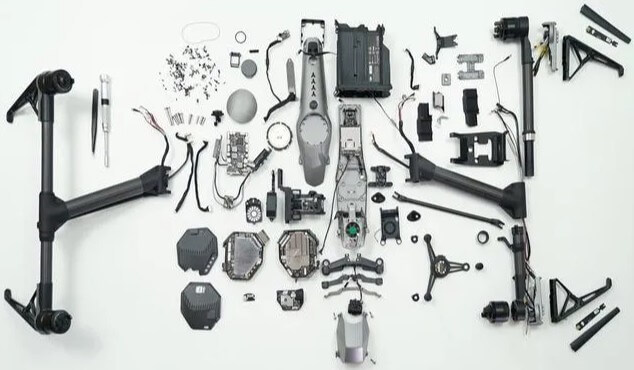
2.Based on these materials, different UAV parts molding processes are divided.
(1) Injection molding
Commonly used to manufacture plastic parts, with high production efficiency and low cost, suitable for mass production, it is the main process for UAV parts molding.
The following is the process of plastic injection molding:
First, design and manufacture the mold, heat and melt the plastic raw material in the barrel, and push the screw with high pressure to inject the molten material into the mold cavity;
The cooling system allows the molten material to solidify and form quickly, and the part is ejected after the mold is opened. Finally, post-processing steps such as de-gating and burr treatment are carried out.
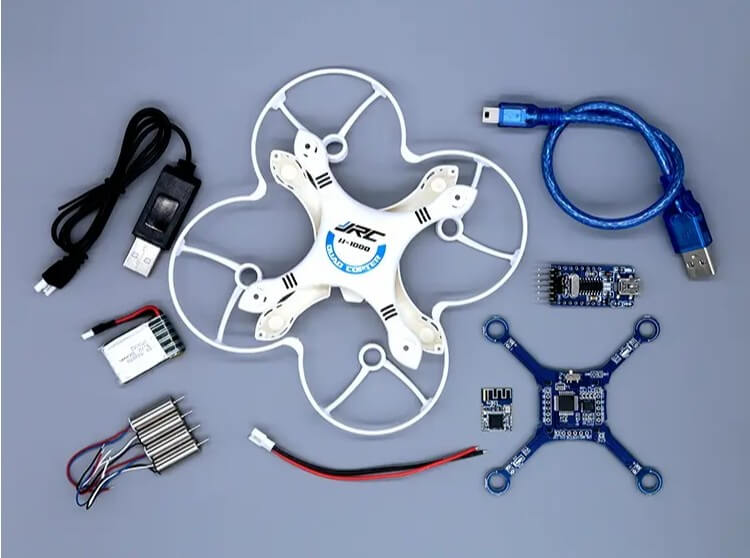
(2) 3D printing (FDM)
It is an emerging process for the UAV parts molding in recent years. It can be used for both plastic parts and metal parts.
The following is the process of 3D printing UAV parts:
Use modeling software to design a three-dimensional model, slice the model of the UAV parts, and then generate the printing path through the software;
During printing, the nozzle heats the plastic filament to a molten state. If it is a metal material, metal powder is required, and then it is stacked layer by layer according to the path. After each layer cools and solidifies, it serves as a support for the next layer until the part is formed.
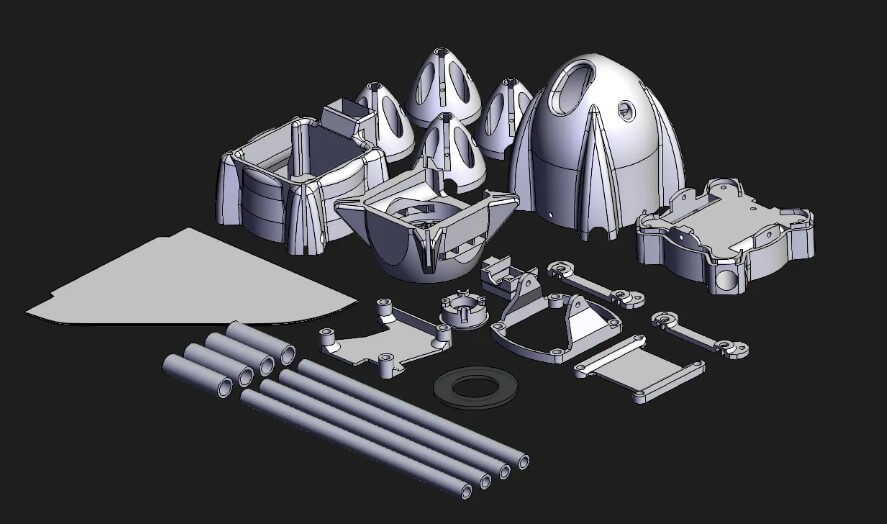
(3) CNC machining (CNC)
It is a precision machining process for metal parts. It mainly removes excess material from metal blanks through processes such as turning, milling, and drilling. It is usually used in combination with casting process to manufacture aluminum alloy frames.
The following is the process of CNC machining UAV parts:
Write the machining program according to the part drawing and fix the blank on the CNC machine tool; the machine tool controls the tool movement according to the program instructions to perform turning, milling, drilling and other cutting processes to remove excess material; after the processing is completed, measure and inspect, and perform secondary processing if necessary.
(4) Metal casting
The casting process is a popular metal forming process, suitable for UAV parts with complex shapes, and has low cost when mass-produced.
The following is the process of casting UAV parts:
Take die casting as an example: manufacture high-temperature resistant die-casting molds, heat the metal to a molten state, and inject it into the mold cavity at high speed through the injection system; cool the metal under pressure to solidify it, open the mold to remove the parts, and then remove the pouring head and surface treatment.
(5) Prepreg molding
This process is for composite materials (carbon fiber, glass fiber). The wings and fuselage frames of UAV made of composite materials have high strength, which can be more than 3 times that of plastics.
The following is the process of prepreg molding UAV parts:
Lay the prepreg resin fiber on the mold in the design direction, cover it with auxiliary materials such as demoulding cloth, seal it and put it into the autoclave; cure it under the set temperature, pressure and time conditions, demould it after cooling, and perform edge trimming.
3.Selection and comparison of five UAV parts molding processes
Process Type | Applicable Parts | Molding Method | Processing Precision & Strength | Cost Level | Suitable for Small-Batch Customization | Feature Summary |
CNC Machining | Metal parts for brackets and shells | CNC cutting | High | Medium-high | Supported | High precision, suitable for metal processing, ideal for functional structural parts. |
Injection Molding | Mass-produced plastic shells | Mold injection | Medium | Low (in batches) | Not suitable for small batches | Low cost but requires mold opening, suitable for standardized products. |
3D Printing | Prototype verification, small structural parts | Layer-by-layer stacking | Medium | Medium-high | Supported | Rapid prototyping with high design freedom. |
Pre-preg Molding | High-strength lightweight structural parts | Pre-impregnated fabric layup + hot-press curing | High | High | Controllable for scaling | Lightweight and high-strength, suitable for high-end drones. |
Small-scale Metal Casting | Motor housings, heat-dissipating structural parts | Gravity or die casting | Medium | Medium-high | Dependent on molds | Limited material options, only suitable for metal parts. |
If you don’t know what process to choose for your parts, I will provide several aspects for your reference below:
Batch size
Cost budget
Material type
Part complexity
Surface quality requirements
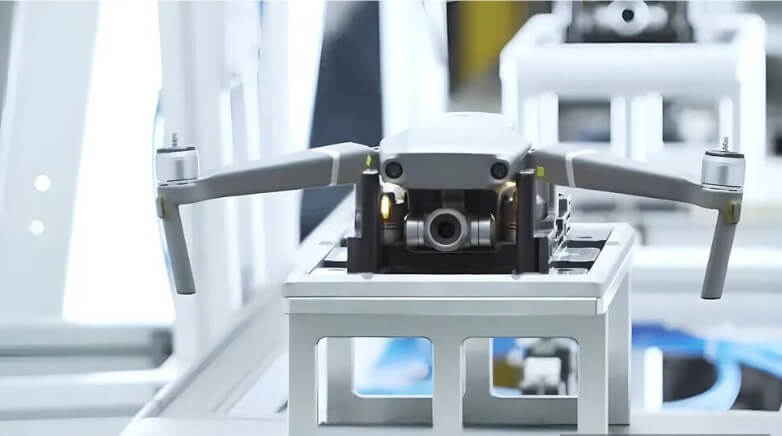
Because some processes are suitable for large batches, some processes are suitable for small batches, some are specialized in plastic molding, and some are specialized in metal molding. By considering the five factors mentioned above, you can get the most suitable manufacturing process by eliminating them step by step. If you still have questions, please feel free to contact us at any time, and our professional engineers will answer you at any time.
4.Common UAV parts and their materials and processes
UAV structures are mainly composed of the following types of parts:
Component | Function | Common Materials |
Frame | Bear the entire machine structure and connect the power and control system | Carbon fiber board, aluminum alloy, plastic |
Propeller | Provide lift | Nylon, glass fiber composite material, carbon fiber |
Motor Bracket / Gimbal Base | Fix power components or cameras, etc. | Aluminum alloy, CNC-machined plastic parts |
Shell | Protect internal electronic devices | Injection-molded ABS, PC, PA6 |
Landing Gear | Buffer landing impact | Nylon, aluminum, TPU elastic material |
Battery Bracket | Fix the battery and prevent vibration | Nylon, TPU, ABS |
PCB Bracket / Module Bracket | Support the assembly of electronic modules | Injection-molded plastic, 3D printing resin |
The core principles of material selection include:
Lightweight (increase flight time)
High strength (prevent impact damage)
Thermal stability (adapt to environmental changes)
Processability (suitable for CNC, injection molding, casting, prepreg, printing and other processes)
5.Advantages of integrated UAV parts molding
(1) Weight reduction:
Reduce the connectors between parts to avoid the extra weight added by the connectors.
(2) Improve structural strength and stability:
Integrated molding parts are an integral structure, and there is no problem of strength reduction due to loose connection parts or stress concentration, which can better withstand various loads during flight.
(3) Reduce assembly cost and time:
Reduce the number of parts and assembly processes, reduce manual assembly costs and time, and improve production efficiency.
(4) Improve flight performance:
Integrated molding can achieve a smoother appearance design, reduce gaps and protrusions between parts, and improve flight efficiency and control performance.
(5) Enhanced design flexibility:
It is easy to realize complex structural design and shape, and meet the needs of different functions and application scenarios.
6.Summary
This article introduces in detail the three major types of materials and five molding processes for the UAV parts molding.
From the above knowledge, we can know that what materials and processes are used to process UAV parts have a great impact on the performance of UAV. Plastics can quickly make a large number of cheap parts, metals are suitable for making strong and durable key components, and composite materials are light and strong. If you have a UAV parts molding project, you can negotiate with us LVXUN, and we will provide you with reliable one-stop service.