Steel castings: materials, applications and process optimization
Steel castings are solid metal parts formed by pouring liquid steel into a pre-prepared mold and cooling and solidifying it. This manufacturing process gives steel castings excellent comprehensive properties, making them widely used in many important fields. This article will explore in depth the characteristics, application fields, material properties, and process optimization of steel castings.
1.Definition and characteristics of steel castings
(1) Definition
Steel castings are parts made of cast steel materials through a casting process. Their properties are similar to those of cast iron, but they are stronger than cast iron. The metallurgical manufacturing adaptability and variability of steel castings are strong, and they can be adapted to various engineering requirements by selecting different chemical compositions and microstructures. In addition, steel castings also have good welding and processing properties, and mechanical properties and performance can be selected in a wide range through different heat treatment processes.
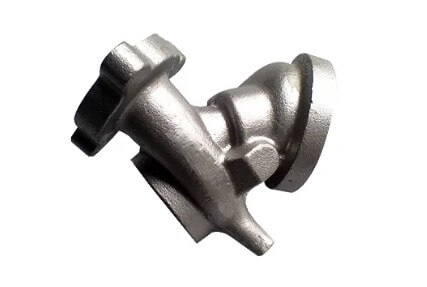
(2) Characteristics
1) Design flexibility:
Steel castings have greater design flexibility in shape and size, and are particularly suitable for manufacturing parts with complex shapes and hollow parts.
2) Metallurgical manufacturing adaptability:
Its chemical composition and organizational structure can be selected according to different engineering requirements. Through different heat treatment processes, mechanical properties and performance can be selected in a wide range.
3) Mechanical properties:
It has good mechanical properties, such as strength, hardness, etc., and the performance in different directions is not much different.
4) Welding performance:
It has good welding performance and is easy to connect with other parts.
5) Processing performance:
It is easy to cut, bend, weld and polish, and it is convenient to process into parts of various shapes and sizes.
6) Corrosion resistance:
Stainless steel castings have excellent corrosion resistance and can resist the erosion of chemicals such as acids, alkalis, and salts.
7) High temperature performance:
Some stainless steel materials have good high temperature performance, can remain stable at higher temperatures, and are not easy to deform and oxidize.
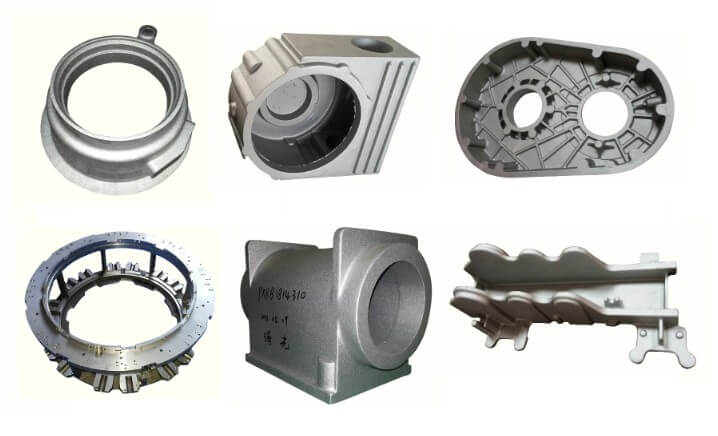
2.Application fields of steel castings
Steel castings are widely used in many fields. The following are some of the main application fields:
(1) Heavy industry
1) Engineering machinery: Steel castings are used to manufacture bucket plates, side blades, bucket bottom plates, etc. of loaders, bulldozers, and excavators.
2) Mining machinery: Used to manufacture liners, blades, etc. of ore and stone crushers.
3) Metallurgical machinery: Used to manufacture iron ore sintering conveyor elbows, iron ore sintering machine liners, scraper liners, etc.
4) Power equipment: Used to manufacture coal mill liners, coal hoppers, coal distribution pipes, etc.
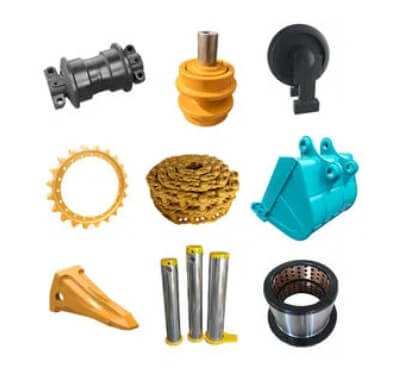
(2) Construction engineering
1) Construction machinery: Used to manufacture cement pusher tooth plates, concrete mixer liners, mixing floor liners, dust collector liners, etc.
2) Structural parts: Used to manufacture load-bearing structures of buildings, such as beams and columns.
(3) Steel Castings Transportation
1) Railways: used to manufacture railway wheels, bearing structures, track connectors, etc.
2) Ships: large ship castings such as rudders, anchor chain wheels, stern pillars, pump casings, etc.
3) Automobiles: used to manufacture key components such as automobile engine blocks, cylinder heads, gearbox housings, etc.
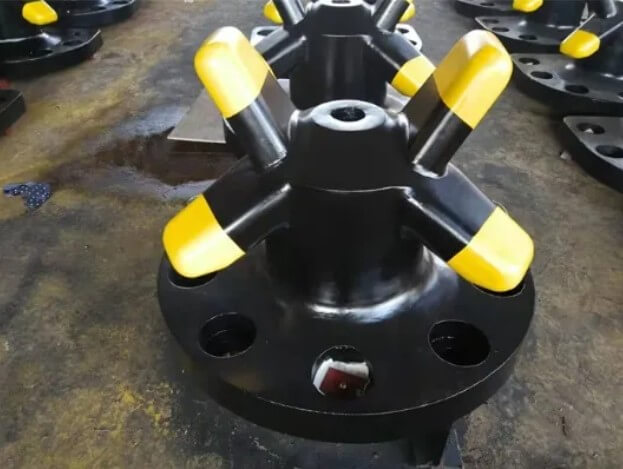
3.Casting Technology Analysis of Steel Castings
Steel castings are key components in many industrial applications, and their manufacturing process involves a variety of casting technologies. The following are several major steel casting casting technologies:
(1) Sand casting:
This is one of the most commonly used casting methods. Sand casting uses sand molds to form castings. This method is suitable for producing large and complex castings, but the accuracy and surface finish may not be as good as other methods.
(2) Investment casting:
Also known as lost wax casting, this technique uses a wax mold to form the casting shape, which is then melted and discharged by heating, and then injected with molten metal. Investment casting can produce high-precision castings and is suitable for complex and small castings.
(3) Metal mold casting:
This method uses metal molds instead of sand molds. Since metal molds can be reused, they are suitable for mass production. Castings produced by metal mold casting have good dimensional accuracy and surface finish.
(4) Pressure casting:
Molten metal is injected into the mold under high pressure. This method has a fast production speed and is suitable for mass production of thin-walled castings.
(5) Centrifugal casting:
Molten metal is poured into a rotating mold and centrifugal force is used to evenly distribute the metal on the inner wall of the mold. This method is often used to produce cylindrical castings such as pipes and wheels.
(6) Shell casting:
A prefabricated shell is made using resin sand or other materials, and then the molten metal is poured into the shell. After cooling and solidification, the casting is obtained. This method is suitable for the production of thin-walled, complex stainless steel precision castings, and has the advantages of high precision, low cost, and short production cycle.
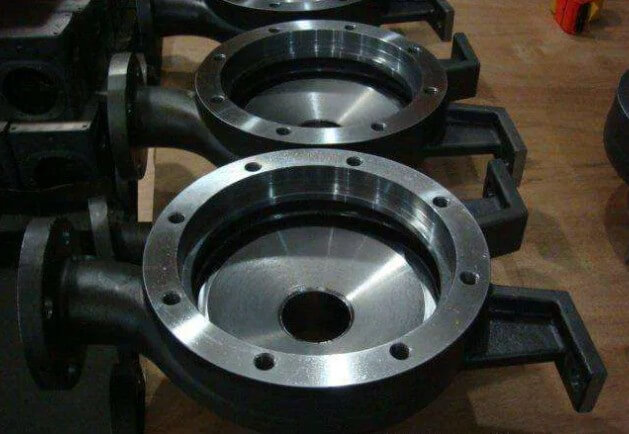
4.Key factors affecting the quality of steel castings
(1) Material selection and processing
The quality of steel castings is first affected by material selection and processing.
1) Material selection
Appropriate steel grade selection and strict material processing process are the basis for ensuring the quality of castings. The chemical composition control of steel is crucial, and different alloying element ratios will affect the physical and mechanical properties of steel. For example, an increase in carbon content can increase the hardness of steel, but may reduce its toughness; while an appropriate amount of alloying elements such as manganese and chromium can significantly improve the strength and corrosion resistance of steel.
2) Material processing
The purity of molten steel is also an important factor affecting the quality of castings. Impurities in molten steel, such as oxides and sulfides, will affect the mechanical properties and internal quality of castings. Therefore, during the smelting process, effective refining measures such as vacuum degassing and refining outside the furnace are required to remove impurities in the molten steel and improve the purity of the molten steel.
(2) Casting process design
The design of the casting process also has a significant impact on the quality of steel castings.
1) Mold design
The design of the mold needs to be precise to ensure that the size and shape of the casting meet the design requirements. The design of the pouring system should be reasonable to avoid pores or inclusions in the molten steel during the pouring process.
In addition, the control of cooling rate is also very critical. Different cooling rates will lead to different metal microstructures, thus affecting the mechanical properties of the casting.
2) Detailed process design
In the casting process design, the shrinkage rate and deformation of the casting also need to be considered. Since the molten steel will shrink during the cooling and solidification process, if the mold design is improper, it may cause defects such as shrinkage cavities and shrinkage in the casting. Therefore, it is necessary to reasonably set the riser and chill to control the solidification sequence and cooling rate of the casting and reduce the occurrence of casting defects.
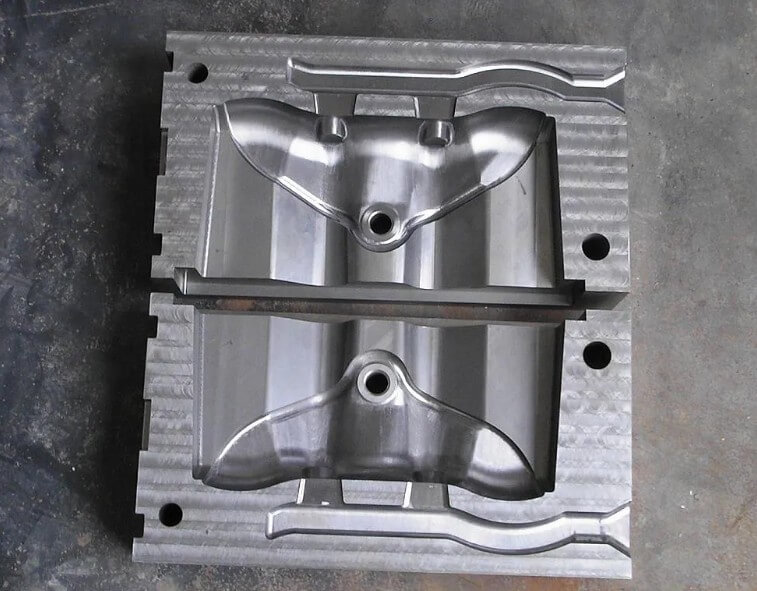
(3) Post-processing technology
Post-processing technology is an important link in improving the quality of steel castings.
1) Heat treatment process
The heat treatment process can improve the mechanical properties of steel castings, such as hardness, toughness and wear resistance. Through appropriate heat treatment processes, the organizational structure of steel can be adjusted and its performance can be optimized. For example, normalizing can refine the grains and improve the mechanical properties of steel; quenching and tempering can significantly improve the hardness and wear resistance of steel.
2) Surface treatment technology
Through surface treatment, the surface condition of the casting can be improved, and its corrosion resistance, wear resistance and aesthetics can be improved. Common surface treatment technologies include sandblasting, spraying, electroplating, etc. For example, sandblasting can remove oxide scale and impurities on the surface of the casting, improve the surface roughness and adhesion; spraying can form a protective film on the surface of the casting, improving its corrosion resistance and wear resistance.
5.What are the casting materials for steel castings?
(1) Carbon steel:
Carbon steel can be divided into low carbon steel (carbon content less than 0.25%), medium carbon steel (carbon content between 0.25% and 0.60%) and high carbon steel (carbon content between 0.6% and 3.0%) according to the carbon content. The strength and hardness of carbon steel increase with the increase of carbon content.
(2) Alloy steel:
Alloy steel can be divided into low alloy steel (total alloying elements less than or equal to 5%), medium alloy steel (total alloying elements between 5% and 10%) and high alloy steel (total alloying elements greater than or equal to 10%). These steels improve the properties of steel, such as wear resistance, heat resistance and corrosion resistance, by adding different alloying elements.
(3) Stainless steel:
Stainless steel is a cast steel material with good corrosion resistance, mainly including 304 cast steel and 316 cast steel. They are all austenitic cast steels with no or weak magnetism. 430, 403 and 410 cast steels are austenitic-ferritic stainless steels with magnetism.
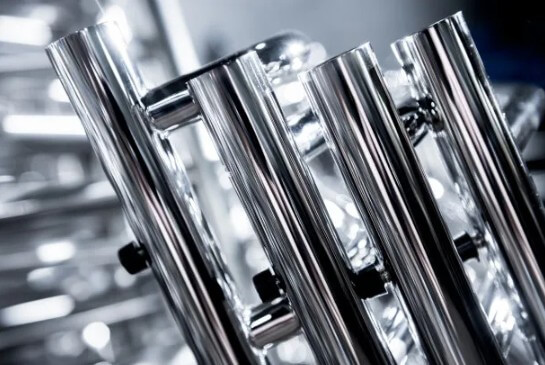
(4) Heat-resistant steel:
Heat-resistant steel is mainly used in applications under high temperature environments, such as chromium heat-resistant steel, chromium-nickel heat-resistant steel, chromium-manganese-nitrogen heat-resistant steel and aluminum-manganese heat-resistant steel. They have good oxidation resistance and thermal strength at high temperatures.
(5) Tool steel:
Tool steel is mainly used to manufacture various tools, such as cast knife steel and cast mold steel. They usually have high hardness and wear resistance.
(6) Special steel:
Special steel includes stainless steel, heat-resistant steel, wear-resistant steel, nickel-based alloy, etc. They have specific properties and are suitable for different special application environments.
(7) Cast steel for engineering and structure:
Cast steel for engineering and structure can be divided into cast carbon structural steel and cast alloy structural steel. They are mainly used to manufacture parts that bear heavy loads, such as rolling mill frames and hydraulic press bases in heavy machinery.
6.Summary
The selection of these casting materials depends on the specific application requirements of the steel castings, such as strength, wear resistance, heat resistance, corrosion resistance, etc. Different materials have different performance characteristics and are suitable for different working environments and usage conditions.