Casting accuracy: the key to improving process level
Casting accuracy refers to the degree of conformity between the actual size of the casting and the design requirements. It is one of the important indicators to measure the casting process level. Improving casting accuracy can not only improve the quality and performance of the product, but also reduce production costs and improve production efficiency. This article will discuss the significance of casting accuracy, classification, influencing factors, how to improve casting accuracy, challenges faced, and how to evaluate accuracy.
1.Definition and significance of casting accuracy
(1) Definition
Casting accuracy is an indicator to measure the degree of conformity between the size, shape and surface quality of the casting and the design requirements. Improving casting accuracy can reduce the workload of subsequent machining, reduce production costs, and improve the performance and reliability of the casting. Precision casting technology can produce high-precision castings that meet complex shape and size requirements and are widely used in aerospace, automobile and other fields.
(2) Significance
1) Improving product quality:
High-precision castings can better meet design requirements and improve the overall performance and service life of the product. For example, in the casting of automobile engine cylinders, high precision can ensure the sealing and strength of the cylinders, thereby improving the performance and reliability of the engine.
2) Reduce production costs:
Improving casting accuracy can reduce the workload of subsequent processing, reduce material consumption and processing costs. At the same time, it can reduce rework and scrapping caused by unqualified castings, further reducing production costs.
3) Improve production efficiency:
High-precision casting technology can improve the stability and consistency of the production process, reduce the adjustment and repair time in the production process, and thus improve production efficiency.
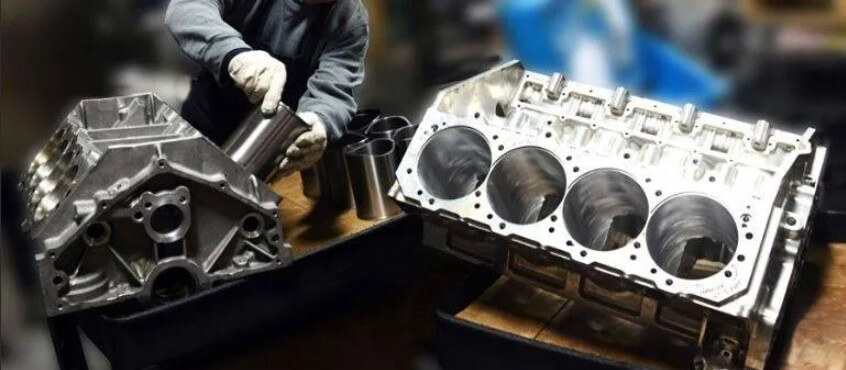
2.How to divide the casting accuracy level?
The division of casting accuracy levels is mainly based on the dimensional accuracy and surface roughness of the castings. According to different casting methods and processes, the accuracy level of castings is different. The following are some common casting accuracy level division standards:
Sand casting: generally CT8-12.
Water glass investment casting: generally CT6-9.
Silica sol investment casting: generally CT4-7.
The dimensional accuracy of castings is usually expressed by the IT standard tolerance level, and the dimensional accuracy of precision casting can be controlled within the IT8 standard tolerance. Generally, the dimensional accuracy of sand castings is IT15-18, and the dimensional accuracy of die castings can be controlled to IT11.
The surface roughness of the casting will also affect its accuracy level, which is usually expressed by the Ra value. Different casting methods can achieve different surface roughness. For example, the surface roughness of sand casting is generally Ra 12.5-50μm, while the surface roughness of precision casting can reach Ra 3.2-12.5μm.
It should be noted that the casting accuracy level is affected by many factors, including mold design, casting process, raw material quality and process operation. Therefore, in actual production, in order to obtain high-precision castings, it is necessary to comprehensively consider these factors and take corresponding measures to control and optimize the casting process.
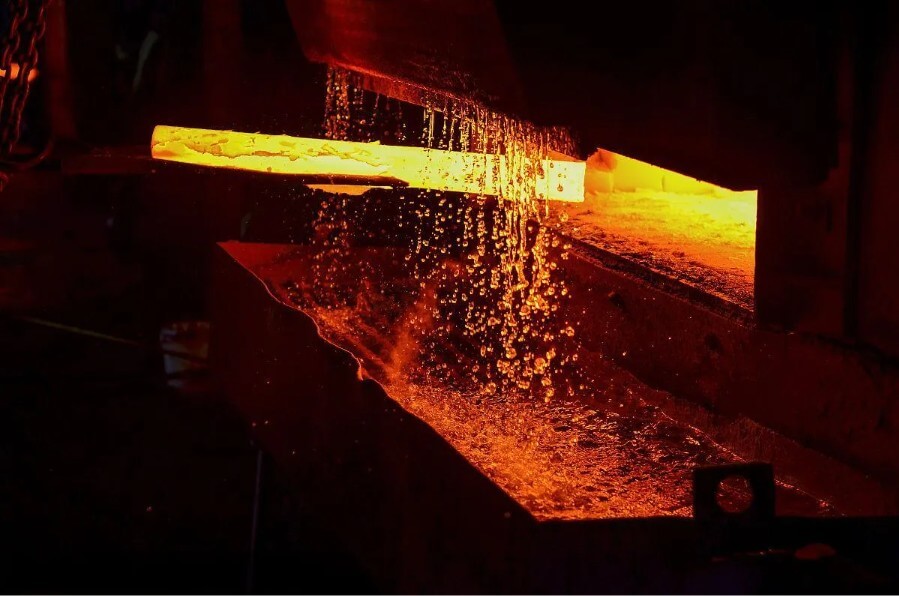
3.Factors affecting casting accuracy
The factors affecting casting accuracy mainly include mold design and manufacturing, material properties, casting process and subsequent processing:
(1) Mold design and manufacturing:
The design and manufacturing accuracy of the mold directly affects the accuracy of the casting. The dimensional accuracy, surface roughness, structure and material selection of the mold will affect the quality of the casting. For example, the shrinkage rate of the mold, the draft angle, the rigidity of the core and the positioning accuracy are all key factors affecting the casting accuracy.
(2) Material properties:
The properties of casting materials, such as shrinkage rate, fluidity, solidification characteristics, etc., have an important influence on the accuracy of castings. The carbon content and alloy composition in the material will affect the linear shrinkage rate and dimensional stability of the casting. For example, the higher the carbon content of the material, the smaller the linear shrinkage rate.
(3) Casting process:
The process parameters in the casting process, such as pouring temperature, pouring speed, cooling method, etc., will affect the accuracy of the casting. Pouring temperature that is too high or too low will cause changes in shrinkage rate, thereby affecting the dimensional accuracy of the casting. In addition, the selection of shell materials and the roasting process will also affect the accuracy of the casting.
(4) Subsequent processing:
The subsequent processing steps such as heat treatment, cleaning, and trimming after the casting is formed will also affect the accuracy of the casting. Heat treatment can improve the structure and properties of the casting, but improper heat treatment may cause deformation of the casting. During the cleaning and trimming process, improper operation may damage the surface of the casting or change the size of the casting.
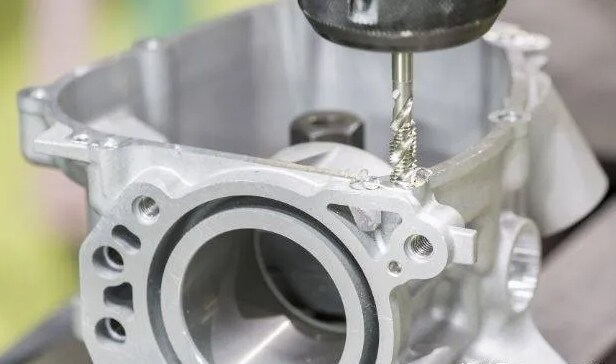
4.Measures to improve casting accuracy
(1) Optimize mold design and manufacturing:
Use high-precision mold manufacturing equipment and processes to improve the dimensional accuracy and surface quality of the mold. At the same time, through technologies such as numerical simulation, optimize the mold structure design and cooling system design to improve the service life of the mold and the accuracy of the casting.
(2) Strictly control material properties:
Select suitable casting alloy materials and strictly control their chemical composition and properties. By adding appropriate amounts of alloying elements, improve the fluidity and shrinkage rate of the alloy and improve the accuracy of the casting.
(3) Optimize casting process parameters:
Through experiments and numerical simulation methods, optimize process parameters such as pouring temperature, pouring speed, cooling speed, etc. to improve the accuracy of the casting. At the same time, use advanced pouring systems and riser designs to improve the shrinkage compensation conditions of castings and reduce defects such as shrinkage cavities and shrinkage.
(4) Strengthen quality control:
Establish a complete quality control system and conduct strict quality control on all links in the casting process. Use advanced testing equipment and technology to test the dimensional accuracy, surface quality, internal defects and other aspects of castings to ensure that the quality of castings meets the design requirements.
(5) Adopt new technologies and new processes:
Actively adopt advanced casting technologies, such as precision casting, lost foam casting, pressure casting, etc., to improve the accuracy of castings. At the same time, through the application of intelligent and automated technologies, improve the intelligence level of casting production, and further improve the accuracy and production efficiency of castings.
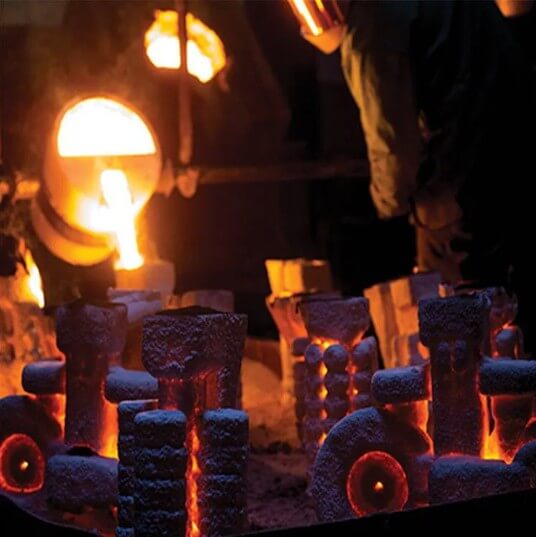
5.Current challenges facing casting accuracy
As a key basic link in the manufacturing industry, the casting industry plays a vital role in modern industry. However, with the advancement of technology and the continuous improvement of market demand, casting accuracy faces many challenges. These challenges not only affect the quality and performance of products, but also put forward higher requirements on the competitiveness and sustainable development capabilities of enterprises.
(1) Control of internal defects
Defects such as pores, inclusions, shrinkage holes and cracks inside castings are one of the main challenges facing casting accuracy. These defects are often formed during the casting process and are difficult to repair through post-processing. Porosity and inclusions can affect the mechanical properties of castings, shrinkage can lead to inaccurate casting dimensions, and cracks can cause castings to break during use.
Therefore, optimizing the casting process, improving the properties of the mold sand, and improving the smelting quality are the keys to improving casting accuracy.
(2) Solution to surface defects
Surface oxidation, sand defects, cold shuts, and other defects that may occur during the casting process can also seriously affect the accuracy and appearance quality of castings. Surface oxidation can reduce the corrosion resistance of castings, while sand defects and cold shuts can affect the surface finish and dimensional accuracy of castings.
To solve these problems, it is necessary to improve the mold design, control the casting temperature and time, and improve the efficiency of the post-casting cooling and cleaning process.
(3) Guarantee of dimensional accuracy
In the casting process of large-scale casting manufacturers, factors such as mold thermal expansion and contraction, metal shrinkage, and mold sand deformation can all lead to dimensional errors. These errors can directly affect the assembly and performance of castings. Therefore, ensuring dimensional accuracy is another important aspect of improving casting accuracy.
To ensure casting accuracy, manufacturers usually require strict dimensional control and fine mold making, and use high-precision processing equipment and testing methods.
(4) Consistency of material properties
In order to achieve the required mechanical properties, the casting process must ensure the consistency of the chemical composition and microstructure of the material. Inconsistency in material properties may cause performance fluctuations or even failure of the casting during use.
This requires manufacturers to not only strictly control the quality of raw materials, but also to implement precise management of the smelting and pouring processes.
(5) Environmental protection and energy efficiency
While pursuing high precision, the casting industry is also facing the dual pressures of environmental protection and energy efficiency. Strict environmental regulations require foundries to reduce emissions and reduce environmental pollution, while rising energy prices also make energy conservation an issue that companies must consider.
Therefore, while improving casting accuracy, foundries also need to be committed to greening and sustainability of production processes, and achieve a win-win situation of environmental protection and economic benefits through technological innovation and environmental protection investment.

6.How to evaluate casting accuracy?
Here are five tips on how to evaluate casting accuracy for your reference:
(1) Choose the right measuring tools
For castings of general accuracy, you can use conventional measuring tools such as vernier calipers, external diameter micrometers, internal diameter micrometers, depth calipers, etc.
For castings with higher accuracy requirements, you should use higher accuracy measuring tools such as micrometers, altimeters, three-coordinate measuring machines, etc.
(2) Use scientific measurement methods
Single-scale measurement method: Applicable to situations where dimensional accuracy requirements are not high. Attention should be paid to the use of measuring tools and accurate readings.
Three-point positioning measurement method: Measure at three locations of the measured dimension and calculate the average value. Applicable to situations where dimensional accuracy requirements are high.
Numerical control measurement method: Use computer-controlled measuring equipment for measurement and data processing. Applicable to situations where high dimensional accuracy requirements are required for castings.
(3) Pay attention to the processing and analysis of measurement data
Data recording: Carefully record the measurement values to maintain the accuracy and completeness of the data.
Abnormal data exclusion: Eliminate the interference of abnormal data when processing data to ensure the validity of the data.
Accuracy determination: Select the appropriate accuracy range and determination criteria according to the design requirements and actual use conditions of the casting.
(4) Application of advanced detection technology
Non-destructive testing technology: Such as ultrasonic testing, X-ray testing, etc., can detect internal defects and dimensional accuracy of castings without destroying them.
3D scanning technology: Use a 3D scanner to scan castings to obtain 3D shape and size information, which is suitable for dimensional detection of complex shaped castings.
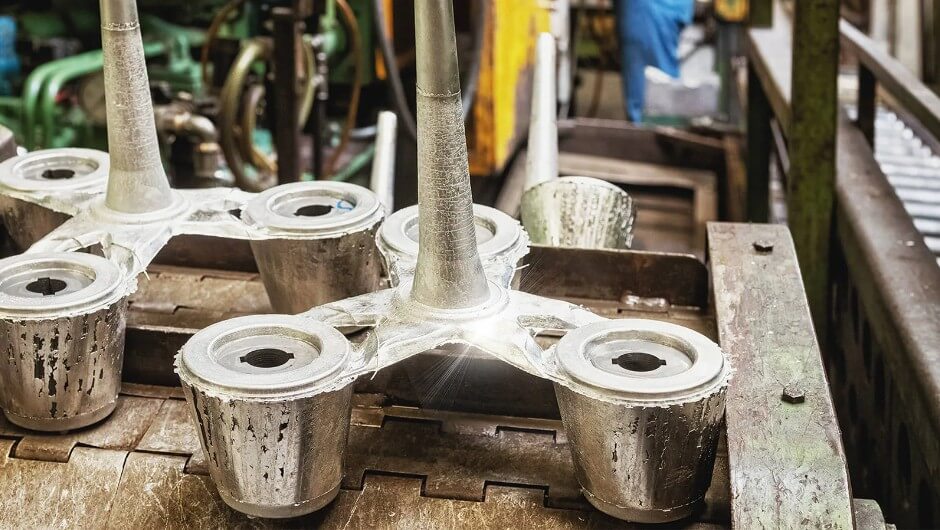
(5) Strengthen quality control and inspection
Strict quality control: Strengthen the monitoring of raw materials, process parameters and production processes during the casting process.
Regular inspection: Conduct regular inspection and sampling inspection on the produced castings to verify their dimensional accuracy and overall quality.
7.Summary
In short, casting accuracy is one of the key factors to ensure the quality of castings. Improving casting accuracy is of great significance to improving product quality, reducing production costs and improving production efficiency. Enterprises need to attach great importance to it and take effective measures to control it in the actual production process. Only by continuously improving casting accuracy can we improve product quality, meet market demand and enhance the competitiveness of enterprises.