aluminum and zinc die castings: a comprehensive analysis of their differences
Aluminum and zinc die castings are two common metal products in modern industrial production. They each have unique characteristics and a wide range of applications. This article will explore the main differences between aluminum and zinc die castings in depth to help manufacturers make a more appropriate choice based on their specific needs.
1.Definition and characteristics of Aluminum and zinc die castings
(1) Zinc die castings:
Zinc die castings are alloys composed of zinc as the basis and other elements (such as aluminum, copper, magnesium, etc.) added. They are formed by high-pressure injection into a mold and then cooled. This process allows the manufacture of high-precision, complex-shaped parts. Zinc alloys have excellent die-casting properties. They have a low melting point and good fluidity, and can easily fill the fine structures of the mold, thus forming parts with smooth surfaces and precise dimensions. In addition, zinc alloys also have good mechanical properties and corrosion resistance, and are suitable for a variety of industrial applications.
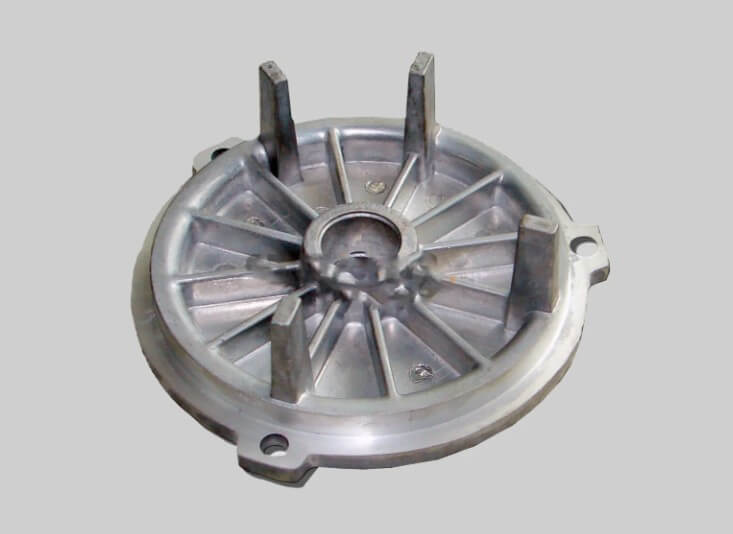
(2) Aluminum die castings:
Aluminum die castings are made of aluminum as the basis and alloy elements such as silicon, copper, magnesium, zinc, and manganese are added. Aluminum die castings have light weight, good mechanical properties and excellent corrosion resistance. Aluminum alloys have low density, high strength, good corrosion resistance, and excellent thermal and electrical conductivity, making them the material of choice for many high-performance applications.
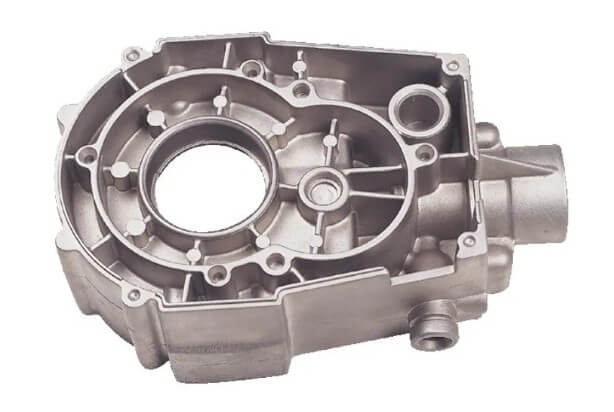
2.Application areas of Aluminum and zinc die castings
(1) Zinc die castings:
Zinc die castings are widely used in the automotive, electronics, communications and home appliance industries due to their excellent mechanical properties and cost-effectiveness. In the automotive industry, zinc die castings are often used to manufacture door lock handles, dashboard structural parts, etc.; in electronic and communication equipment, zinc die castings are used to manufacture housings and frames due to their good electromagnetic shielding properties; in home appliances, zinc die castings are used to manufacture decorative parts and functional parts.
(2) Aluminum die castings:
Aluminum die castings are mainly used in the automotive, aerospace, construction and sports equipment industries due to their light weight and high strength. In the automotive industry, aluminum die castings are used to manufacture engine parts, gearbox housings, suspension systems, etc.; in the aerospace field, aluminum die castings are used to manufacture aircraft and spacecraft structural parts due to their good corrosion resistance and high temperature performance; in the construction field, aluminum die castings are used to manufacture door and window frames, decorative parts, etc.; in the field of sports equipment, aluminum die castings are used to manufacture bicycle frames, skis, etc.
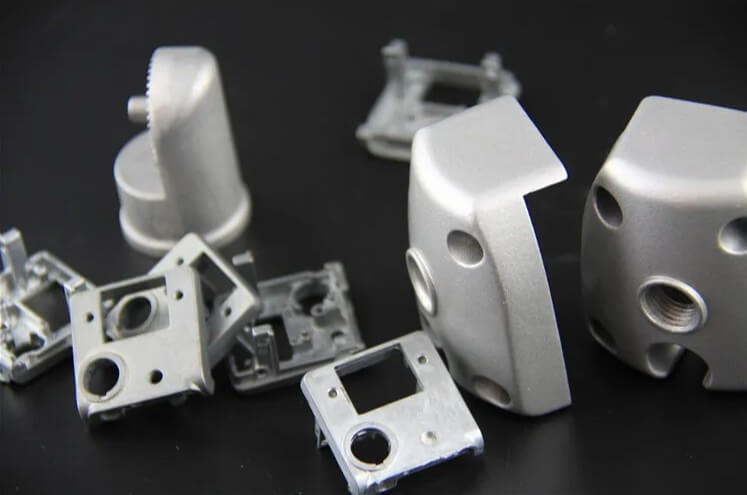
3.Detailed comparison of Aluminum and zinc die castings
Aluminum and zinc die castings have significant differences in material properties, manufacturing costs, service life and surface treatment. The following will compare various aspects of Aluminum and zinc die castings in detail.
(1) Material properties
1) Zinc alloy:
Zinc alloy has a low melting point of about 387°C, which makes it fluid during casting and easy to fill complex-shaped molds. However, the strength and corrosion resistance of zinc alloy are inferior to aluminum alloy, and it is easy to corrode and age under high temperature and harsh environment. The hardness of zinc alloy is 65 to 140, and the tensile strength is 260 to 440MPa.
2) Aluminum alloy:
Aluminum alloy has low density, high strength, good corrosion resistance, and excellent thermal and electrical conductivity. Its melting point is relatively high, about 660°C, which is suitable for applications that require high strength and corrosion resistance. The hardness of aluminum alloy is 45 to 90, and the tensile strength is 120 to 290MPa. In addition, aluminum alloy maintains good mechanical properties in both high and low temperature environments, making it the material of choice for many high-performance applications.
(2) Manufacturing cost
1) Zinc die castings:
The production cost of zinc die castings is relatively low, the production cycle is short, and it is suitable for large-scale production. The low melting point and good fluidity of zinc alloy can reduce energy consumption and production costs. In addition, the mold life of zinc die castings is long, which can further reduce production costs.
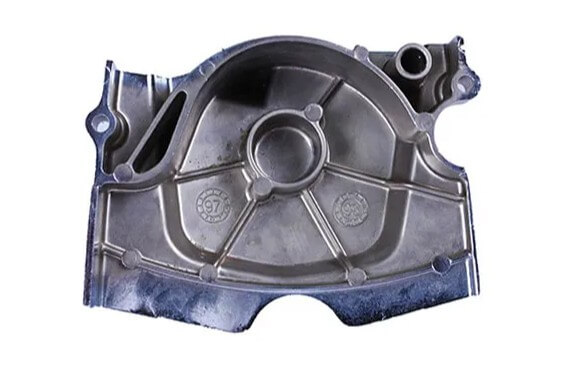
2) Aluminum die castings:
The production cost of aluminum die castings is high and the production cycle is long, but it has better performance and a wider range of applications. The high melting point and poor fluidity of aluminum alloy require higher energy consumption and more complex production equipment. In addition, the mold life of aluminum die castings is short, which increases production costs.
(3) Service life
1) Zinc die castings:
The service life of zinc die castings is short and they are prone to corrosion and aging, especially in humid and acidic environments. They have poor corrosion resistance and are prone to surface oxidation and corrosion, which affects the appearance and service life of parts.
2) Aluminum die castings:
Aluminum die castings have a long service life and have good corrosion resistance and aging resistance. A dense oxide film is easily formed on the surface of aluminum alloy to prevent further corrosion, and they are suitable for various harsh environments. Aluminum die castings have high strength and rigidity and can withstand large loads and impacts, extending the service life of parts.
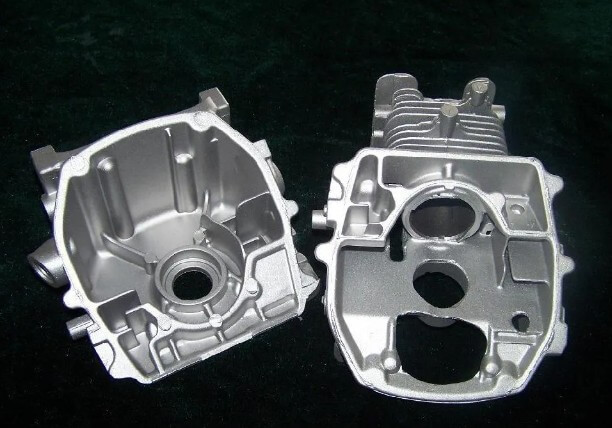
(4) Surface treatment
1) Zinc die castings:
The surface treatment of zinc die castings is relatively simple, and electroplating, spraying and other processes can be used to improve their appearance and corrosion resistance. The surface treatment effect of zinc alloy is better, and a smooth and uniform coating can be formed to improve the decorative and protective properties of parts.
2) Aluminum die castings:
There are more surface treatment options for aluminum die castings, such as anodizing, electrophoretic coating, etc., which can provide better protection and decorative effects. The surface treatment process of aluminum alloy is relatively complex, and it can form a coating with a variety of colors and effects to increase the added value of parts.
4.How to choose Aluminum and zinc die castings
When choosing between aluminum and zinc die castings, various factors should be considered, such as application requirements, cost budget and use environment. The following are some specific conclusions and selection suggestions.
(1) According to application requirements:
If high-precision, complex-shaped parts are required and cost-sensitive, zinc die castings are a good choice. For example, in the manufacturing of electronic equipment, communication equipment, automotive parts and household goods, zinc die castings have advantages due to their good fluidity and low melting point.
If high-strength, corrosion-resistant parts are required, aluminum die castings should be selected. For example, in the manufacturing of automotive parts, aerospace, sports equipment and other fields, aluminum die castings are the first choice due to their light weight and high strength.
(2) According to cost budget:
The production cost of zinc die castings is generally lower because zinc has a lower melting point, the die casting process is faster, the production cycle is short, and it is suitable for mass production.
The cost of aluminum die castings is relatively high, but aluminum is highly recyclable and may be more economical in the long run.
(3) According to the application environment:
Zinc die castings are suitable for use at room temperature and are suitable for manufacturing thin-walled parts and complex shapes.
Aluminum die castings are suitable for high and low temperature environments, as well as applications that require high strength and light weight.
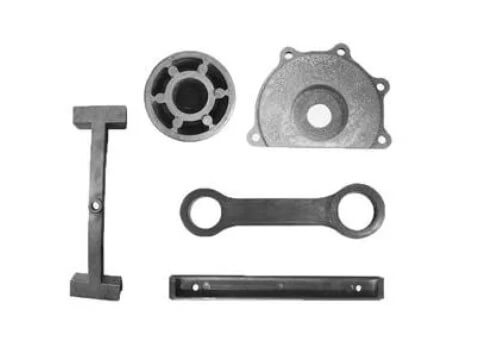
5.Future application trends of Aluminum and zinc die castings
With the continuous advancement of science and technology, the application prospects of aluminum and zinc die castings in multiple industries are becoming increasingly broad. Due to their unique performance advantages, these two materials are gradually becoming an indispensable component in the fields of automobiles, electronics, aerospace, etc. The following will discuss the future application trends of aluminum and zinc die castings respectively.
(1) Future application trends of zinc die castings
1) Environmental protection trend: With the enhancement of global environmental awareness, the application of green die casting materials will become mainstream. Environmentally friendly materials such as lead-free zinc alloys and recycled zinc alloys will be more widely used. At the same time, energy conservation and emission reduction in the die casting process and the practice of circular economy will also become an important development direction.
2) Intelligent production: The application of intelligent die-casting equipment and production systems will improve the production efficiency and product quality of zinc die-castings. The combination of big data and Internet of Things technology will realize real-time monitoring and optimization of the production process.
3) Multi-field application expansion: Due to its good conductivity, corrosion resistance and lightweight characteristics, the application of zinc die-castings in electronics, communications, medical and other fields will continue to expand. In particular, in electronic products that require electromagnetic shielding functions, the demand for zinc die-castings will continue to grow.
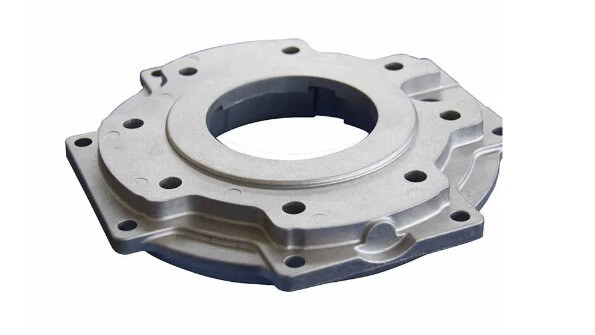
(2) Future application trends of aluminum die-castings
1) Automobile lightweighting: With the rapid development of the global automobile industry, the application of aluminum die-castings in the manufacturing of automobile parts will become more extensive. The demand for lightweighting makes aluminum die-castings play an important role in improving automobile fuel efficiency and reducing emissions.
2) Aerospace: Due to the high strength and lightweight characteristics of aluminum die-castings, their application in the aerospace field will continue to grow. The manufacture of aircraft parts will adopt more aluminum die-casting technology to reduce weight and improve navigation efficiency.
3) Intelligence and automation: The aluminum die-casting production process will be more intelligent and automated. The application of intelligent die-casting equipment and information management system will improve production efficiency and product quality and reduce production costs.
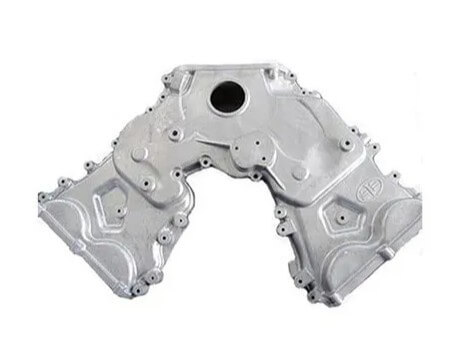
6.Summary
With the advancement of technology, the performance of zinc die-castings and aluminum die-castings will continue to improve to meet the needs of more fields. For example, by improving the alloy composition and die-casting process, the strength and corrosion resistance of zinc die-castings can be improved and their service life can be extended; by optimizing the mold design and manufacturing process, the production cost of aluminum die-castings can be reduced and production efficiency can be improved.
In general, aluminum and zinc die castings each have their own advantages and applicable scenarios. In practical applications, the most suitable materials and processes should be selected according to specific needs to achieve the best performance and economic benefits.