Tilt casting process: principles, methods, applications and advantages
The tilt casting process is a special metal casting method that achieves smooth filling of molten metal by controlling the tilt angle and speed of the mold, thereby obtaining high-quality castings. This article will introduce the principles, methods, precautions, applications and advantages of the tilt casting process in detail.
1.Principle of tilt casting process
The basic principle of the tilt casting process is to tilt the mold at a certain angle during the casting process, and control the filling speed of the molten metal and the tilt speed of the mold so that the molten metal can fill the mold smoothly under the action of gravity. This process can effectively reduce defects such as pores and slag inclusions, and improve the density and mechanical properties of the casting.
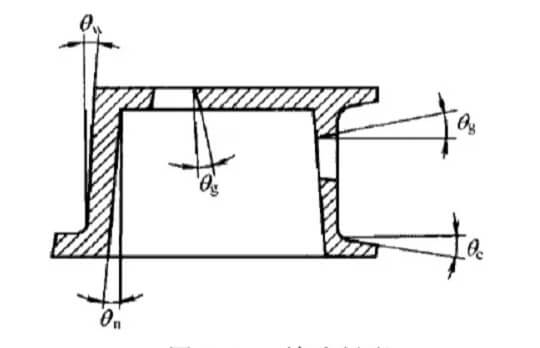
(1) Tilt angle of the mold:
The tilt angle of the mold is an important factor affecting the filling effect of the molten metal. A suitable tilt angle can ensure that the molten metal remains stable during the filling process and avoid eddy currents and splashes.
(2) Filling speed:
The control of the filling speed is the key to the tilt casting process. A reasonable filling speed can ensure that the molten metal does not produce air entrainment during the filling process and reduce the formation of pores.
(3) Mold movement:
During the tilt casting process, the mold usually reciprocates or rotates to promote the flow and exhaust of molten metal and improve the quality of the casting.
2.How to correctly pour molten metal into the tilted mold
Pouring metal into the tilted mold is a process that requires precise control and attention to multiple technical details. The following are some key steps and precautions:
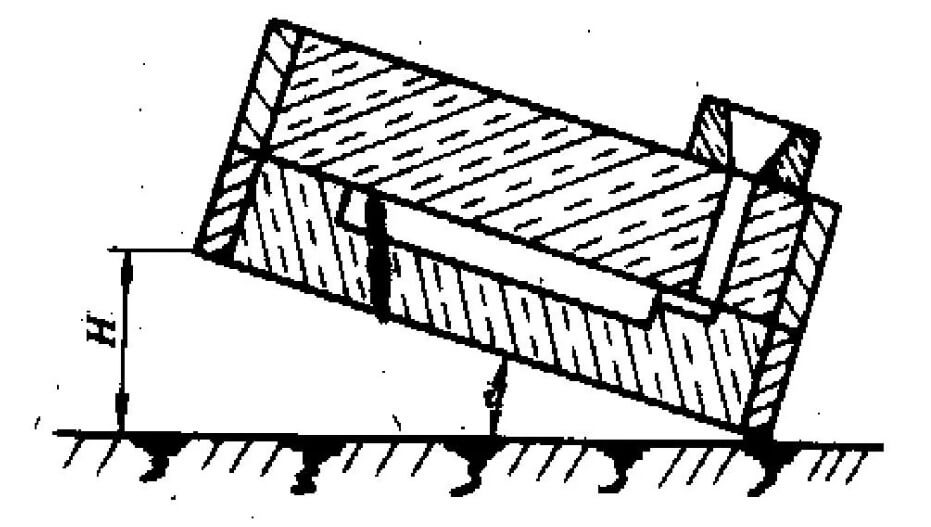
(1) Pouring system design:
Design a reasonable pouring system to ensure that the molten metal can smoothly fill the mold cavity. Generally, the gate should be placed at the lower part of the mold, and the vent should be placed at the highest point to facilitate the flow of molten metal and the exhaust of gas.
(2) Pouring speed control:
The pouring speed should be appropriately adjusted according to the characteristic wall thickness of the casting. For castings with different wall thicknesses, the pouring time will be different. For example, the pouring time of a casting with a wall thickness of 10mm can be 17 seconds, while the pouring time of a casting with a wall thickness of 20mm can be increased to 19 seconds.
(3) Pouring temperature:
Pouring temperature has an important influence on the quality of castings. When casting with a metal mold, the pouring temperature is generally 20-35°C higher than that of sand mold casting to ensure that the liquid metal can fill the mold cavity. However, the pouring temperature should not be too high, so as not to affect the structure and mechanical properties of the casting and reduce the service life of the metal mold.
(4) Tilt angle:
When tilting the mold, the appropriate tilt angle should be determined according to the structural characteristics of the casting. For castings with large surfaces, it may be necessary to tilt the mold more than 15° to ensure that the molten metal rises steadily in the mold cavity and avoid damaging the plastic film on the upper mold.
(5) Pouring method:
Depending on the characteristics of the casting, horizontal pouring, tilted pouring or vertical pouring can be selected. For castings that require tilted pouring, ensure that the sprue is located at the lower end so that the molten metal can rise smoothly and fill the mold cavity.
3.Application of tilted casting process
Due to its unique advantages, the tilted casting process has been widely used in many fields.
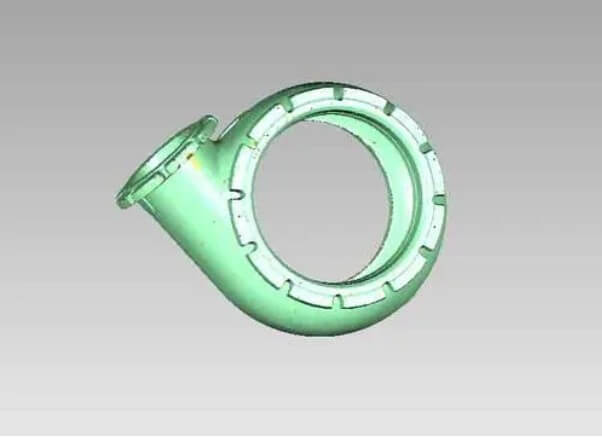
(1) Automobile industry:
The tilt casting process is often used to produce complex castings such as automobile engine cylinder blocks and cylinder heads. These castings require high strength and density, and the tilt casting process can meet these requirements.
(2) Aerospace:
In the aerospace field, the tilt casting process is used to produce high-performance aluminum alloy castings. These castings usually need to have excellent mechanical properties and corrosion resistance, and the tilt casting process can guarantee these performance requirements.
(3) Mechanical manufacturing:
The tilt casting process is also widely used in the mechanical manufacturing field to produce various complex-shaped castings. For example, castings such as pump bodies and valve bodies can achieve higher precision and performance through the tilt casting process.
4.Advantages of the tilt casting process
Compared with traditional casting processes, the tilt casting process has the following advantages:
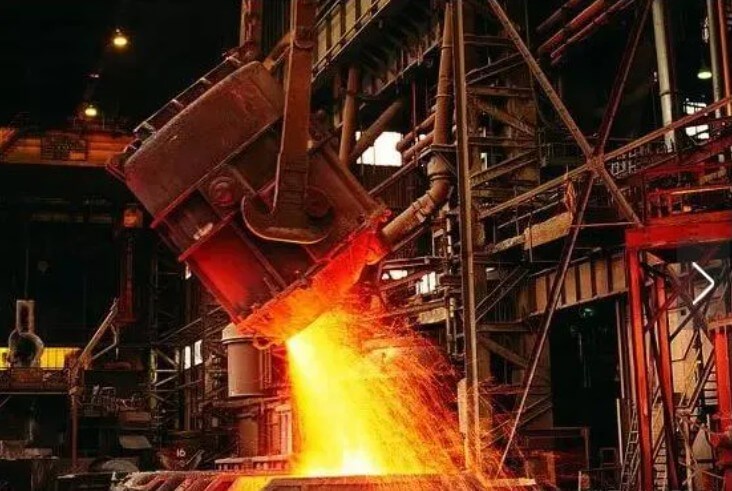
(1) Reducing defects:
The tilt casting process can effectively reduce defects such as pores and slag inclusions, and improve the density and mechanical properties of castings. During the tilt casting process, the molten metal is filled smoothly under the action of gravity, reducing the possibility of air entrapment and slag inclusions.
(2) Improve precision:
It can improve the dimensional accuracy and surface finish of the casting. During the tilt casting process, the filling speed of the molten metal and the movement of the mold are precisely controlled, which reduces the deformation and surface defects of the casting and improves the precision.
(3) Reduce energy consumption:
Tilt casting can reduce the energy consumption in the casting process. This is because during the tilt casting process, the filling speed of the molten metal and the movement of the mold are optimized, which reduces the energy consumption.
(4) Shorten the cycle:
It can shorten the casting cycle and improve production efficiency. During the tilt casting process, the filling speed of the molten metal and the movement of the mold are optimized, which reduces the casting time and post-processing time.
5.Conclusion
The tilt casting process is an efficient and high-quality metal casting method with broad application prospects. By continuously optimizing process parameters and control methods, the tilt casting process will play a more important role in future casting production.