Casting technology: a combination of craftsmanship and practicality
Casting technology carries the profound heritage of the combination of craftsmanship and practicality. It is a method of pouring molten metal or other materials into a specific mold and waiting for it to cool and solidify to form the desired shape. This technology occupies a pivotal position in modern industry and is widely used in many fields such as machinery manufacturing, automobiles, aerospace, and medical devices.
1.Operation steps of casting technology
The operation steps of casting technology are numerous, and each step requires delicate operation and strict control to ensure the quality and performance of the final product.
(1) Mold preparation:
First, a mold needs to be prepared. The mold is usually made of high-temperature resistant materials such as metal or ceramic. The shape of the mold will determine the shape of the final product.
(2) Material melting:
The required material (such as metal, plastic, etc.) is placed in a furnace and heated until it is completely melted.
(3) Pouring:
Pour the molten material into the prepared mold. This process requires great care to ensure that the material evenly fills every corner of the mold.
(4) Cooling and solidification:
The material poured into the mold needs time to cool and solidify. The time required for this process depends on the type of material and the size of the product.
(5) Demolding:
Once the material solidifies, the product can be removed from the mold. This process may require the use of some tools to ensure that the product is intact.
(6) Post-processing:
The demolded product may also require some post-processing, such as grinding and polishing, to achieve the final desired finish and precision.
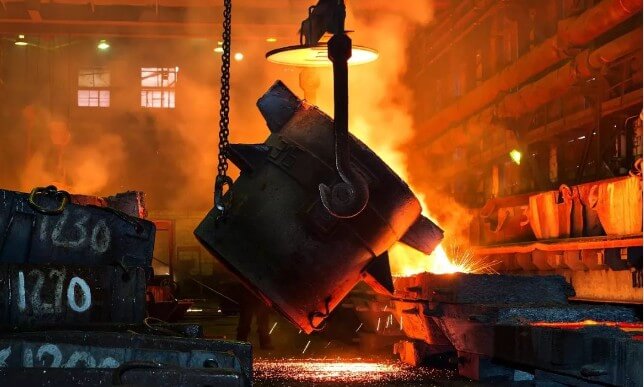
2.Analysis of the application fields of casting technology
(1) Automobile industry
The application of casting technology in the automobile industry is extremely extensive. Key components such as automobile engine cylinder blocks, cylinder heads, and transmission housings are usually manufactured using casting technology. Aluminum alloy has become the main material for automobile castings due to its advantages such as light weight, high strength, and corrosion resistance. Through advanced processes such as high-pressure casting and low-pressure casting, automobile parts with high dimensional accuracy and good surface finish can be produced, which helps to improve the fuel economy and safety of automobiles.
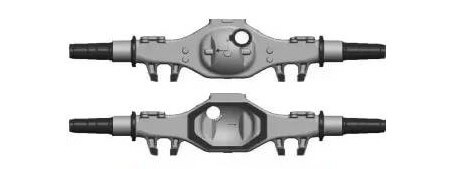
(2) Aerospace
The aerospace field has extremely high requirements for the performance of materials, and the application of casting technology in this field is also increasing. Difficult-to-process materials such as titanium alloys and nickel-based high-temperature alloys can be used to manufacture complex aircraft engine blades, fuselage frames and other key components through precision casting technology. These components not only need to have high strength and high toughness, but also need to maintain stable performance under extreme environments. Casting technology provides strong support for the development of the aerospace industry.
(3) Mechanical manufacturing
Mechanical manufacturing is one of the most traditional application areas of casting technology. Various machine tool beds, bases, gearboxes and other components are usually produced using materials such as cast iron and cast steel through sand casting and metal casting. Castings have good shock absorption and wear resistance, and can meet the requirements of mechanical manufacturing for part strength and stability.
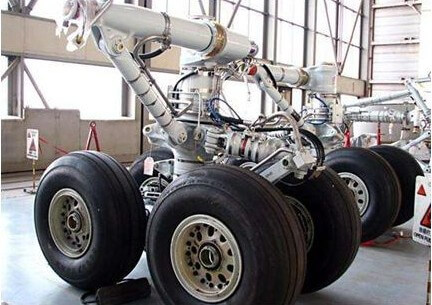
(4) Medical devices
With the continuous development of medical technology, the application of casting technology in the field of medical devices is becoming more and more extensive. Through precision casting technology, high-precision and high-surface finish medical device components such as surgical instruments, prostheses, and joint replacements can be produced. These components not only require high dimensional accuracy, but also good biocompatibility. Casting technology provides a reliable guarantee for the manufacture of medical devices.
3.The role of mold casting technology in the manufacturing process of aircraft, train and automobile parts
Aircraft, train and automobile have their own characteristics in mold casting. Different solutions are needed according to the specific requirements of different parts, such as choosing the most suitable material, casting method, post-processing, etc., which will affect the final result.
(1) Aircraft mold casting technology
Aircraft manufacturing has extremely high requirements for material strength and lightweight, and mold casting technology plays an important role in this field. Aircraft parts are usually made of high-strength alloy materials such as aluminum alloy and titanium alloy through precision casting process. These castings not only need to have extremely high strength and toughness, but also meet strict dimensional accuracy and surface finish requirements.
In the aircraft mold casting process, firstly, it is necessary to design and make a high-precision mold, and then inject the molten metal liquid into the mold. After it cools and solidifies, the required parts are obtained. In order to improve the quality and performance of castings, modern aircraft manufacturing often uses technologies such as vacuum casting and pressure casting. These technologies can effectively reduce defects inside castings and improve material utilization.
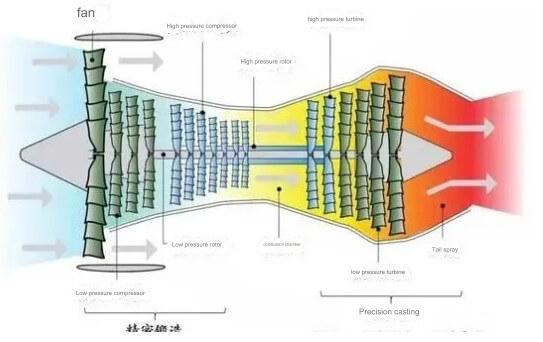
(2) Train casting technology
Train casting technology is mainly used in the manufacture of key components such as wheels and frames. Traditional train wheel casting mostly uses graphite molds, which take advantage of graphite’s high temperature resistance, high heat storage and low thermal expansion coefficient to ensure the dimensional accuracy and internal quality of the wheel. However, this method has problems such as difficulty in removing the riser and uneven rim structure.
In order to solve these problems, modern train wheel casting technology has introduced new casting mold materials and methods. For example, the bottom pouring molten steel technology is used to inject molten steel from the bottom of the mold, reducing the contact between molten steel and air, thereby reducing oxidation and air absorption, and improving the purity of molten steel. In addition, by optimizing the mold design and pouring process, casting defects can be effectively reduced and the overall performance of the product can be improved.
(3) Automobile casting technology
Automobile casting technology covers many aspects such as body structural parts and engine parts. The application of casting technology in automobile manufacturing can not only meet the needs of large-scale production, but also realize the one-time molding of complex-shaped parts.
Automobile casting technology mainly includes sand casting, metal mold casting and pressure casting. Among them, pressure casting is widely used in the production of automotive aluminum alloy parts due to its high production efficiency and good casting dimensional accuracy. By injecting molten metal into the mold under high pressure and solidifying it under high pressure, a casting with dense structure and smooth surface can be obtained.
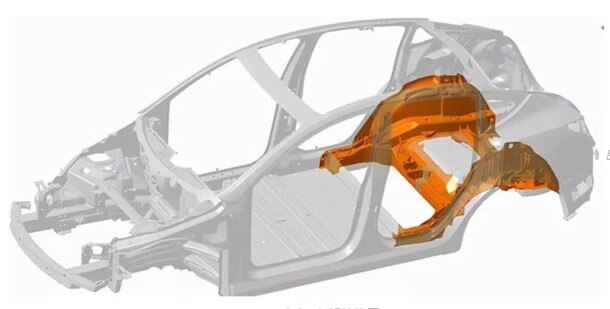
4.Conclusion
Casting casting technology, as an important manufacturing process, plays an irreplaceable role in modern manufacturing. It is committed to improving product production efficiency and product quality and reducing production costs. It provides strong support for the efficient and intelligent development of the manufacturing industry.