3D printing investment casting: an innovative path from digital models to physical objects
3D printing investment casting technology, also known as the technology that combines additive manufacturing with precision casting, is an advanced manufacturing process that combines 3D printing technology with traditional investment casting technology to create a new production model. The application of this technology in the casting industry, especially in new product development, has shown great potential.
This article will explore in depth the basic overview, basic principles and steps, application advantages and challenges, investment materials suitable for 3D printing, process optimization strategies, and practical application areas of 3D printing investment casting technology.
1.Basic overview of 3D printing investment casting technology
(1) Introduction to 3D printing technology
3D printing technology, also known as additive manufacturing technology, is based on the basic principle of three-dimensional digital design through computers, using 3D printing equipment to stack “printing materials” layer by layer, and finally transforming digital models into physical objects. This technology can be used to print a variety of materials such as metals, ceramics, plastics, resins, etc., with high flexibility and precision.
(2) Introduction to investment casting technology
Investment casting, also known as lost wax casting, is a casting process with a long history. It is done by making a wax mold, then wrapping it in a refractory material to form a shell, then roasting the wax mold to melt it and pouring the metal liquid to obtain the casting. This process can produce high-precision, smooth-surfaced castings, and is particularly suitable for the production of complex parts. However, traditional investment casting has problems such as long cycle, high cost, and low fault tolerance in the mold making process.
(3) Application of 3D printing in investment casting
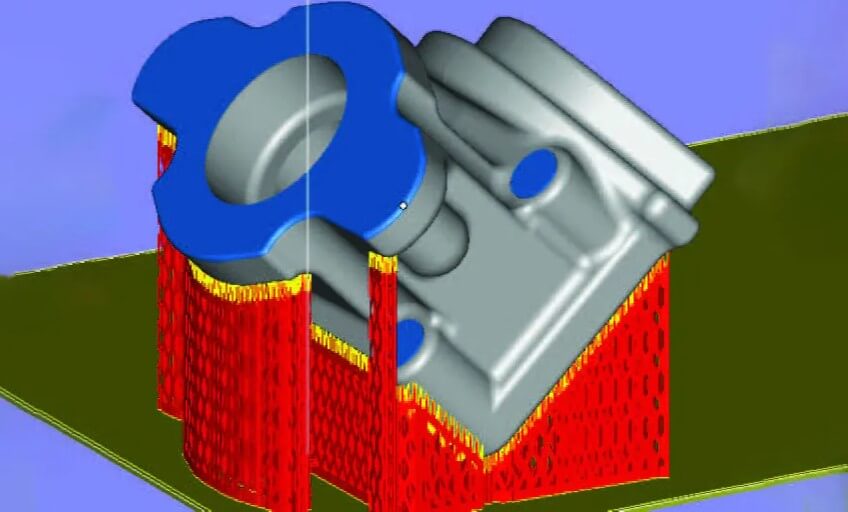
The combination of 3D printing technology and investment casting effectively solves these pain points. By using 3D printing technologies such as stereolithography (SLA), high-precision, high-surface quality wax or resin molds can be directly printed, greatly reducing the mold making time and cost. In addition, the application of 3D printing technology also makes prototype verification and process optimization in the casting process more convenient. By quickly printing out prototypes, designers can quickly make multiple iterative modifications to optimize product performance.
2.Basic principles and steps of 3D printing investment casting technology
As a rapid prototyping technology, 3D printing investment casting technology is gradually becoming the focus of attention in all walks of life with its unique advantages. The basic principles of 3D printing investment casting technology can be summarized as follows:
(1) Digital model creation:
First, a three-dimensional digital model is created using computer-aided design (CAD) software. This model is the basis for subsequent printing and casting.
(2) Model slicing:
The three-dimensional model is sliced into a series of two-dimensional layers so that the 3D printer can build the object layer by layer.
(3) 3D printing wax mold:
Wax molds are directly printed using 3D printing technology (such as light-stereolithography SLA). These wax molds have the characteristics of high precision and smooth surface, which are suitable for precision casting.
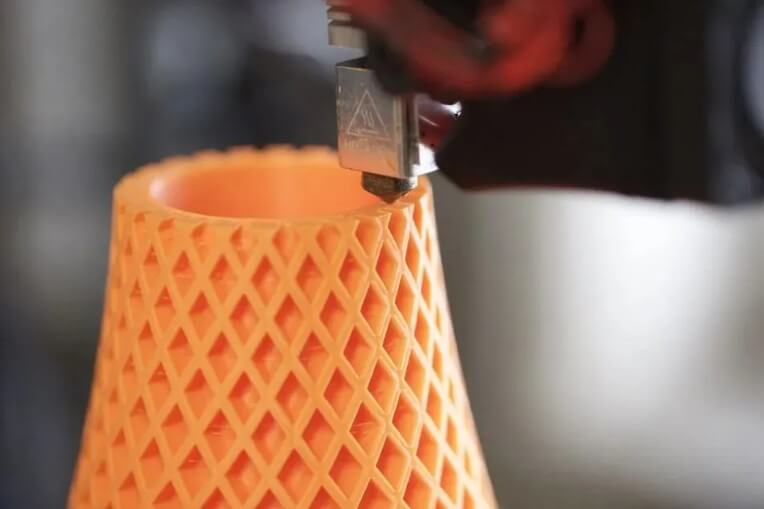
(4) Shell making:
Multiple layers of refractory material are applied to the surface of the wax mold to form a shell. This process includes steps such as slurry coating and sanding to enhance the strength of the shell.
(5) Dewaxing and baking:
The shell is heated to melt and flow out the wax model, and high-temperature baking is performed to remove residues and harden the shell.
(6) Metal pouring:
Molten metal liquid is poured into the preheated shell.
(7) Cooling and cleaning:
After the metal cools and solidifies, the casting is removed and cleaned to remove the shell and pouring system.
(8) Post-processing:
The casting is subjected to necessary post-processing such as heat treatment and machining to obtain the final product.
3.Application advantages and challenges of 3D printing investment casting technology
(1) Advantages of 3D printing investment casting technology
1) Shorten the production cycle:
3D printing technology can quickly produce complex wax or resin molds, greatly reducing the time and cost of mold making in traditional investment casting. Usually, the entire casting cycle can be shortened from several weeks to several days.
2) Improve design flexibility:
3D printing technology is not limited by traditional manufacturing processes and can realize the free design of complex structures. This allows designers to create complex geometric shapes and internal structures that are difficult to achieve with traditional methods.
3) Reduce material waste:
Compared with traditional casting processes, 3D printing technology greatly reduces material waste by stacking materials layer by layer. In addition, due to its precision, it also reduces the workload of subsequent processing.
4) Improve casting accuracy:
3D printed models have high dimensional accuracy and surface finish, which directly improves the accuracy of the final casting. Especially for small and precision castings, 3D printing technology can ensure perfect reproduction of details.
5) Adapt to small batch production:
For small batch or customized production, 3D printing investment casting technology has obvious advantages. It avoids the high cost of mold making, while being able to quickly respond to market demand and improve production flexibility.
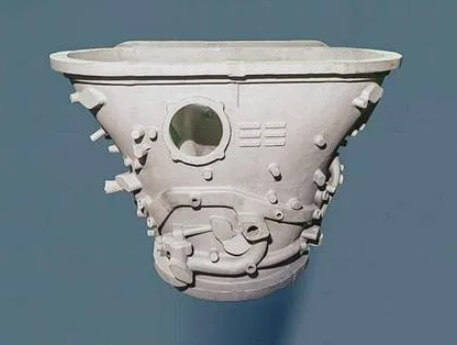
(2) Application challenges of 3D printing investment casting technology
1) Material performance limitations:
Currently, the performance of 3D printing materials is still somewhat different from that of traditional casting materials, especially in terms of strength and toughness.
2) Balance between manufacturing accuracy and speed:
High-precision 3D printing equipment often has a slow printing speed, while high-speed printing equipment is difficult to ensure the accuracy of printed parts.
3) Cost and large-scale production problems:
Although 3D printing investment casting technology has advantages in small batch production, its high cost problem is still prominent in large-scale production.
4) Technology maturity:
Although 3D printing technology has been applied in some fields, in other fields, such as aerospace, 3D printing technology is still in the exploratory stage in special places due to the extremely high requirements for material properties and manufacturing accuracy.
4.Investment casting materials suitable for 3D printing
(1) Photosensitive resin
Photosensitive resin is one of the commonly used materials in 3D printing and is formed by SLA (stereolithography) technology. Photosensitive resin has the advantages of high molding accuracy and smooth surface, and is suitable for making fine wax models. However, the strength and heat resistance of photosensitive resin are relatively poor, and post-processing is required to improve its performance.
(2) Degradable materials
Degradable materials, such as PLA (polylactic acid) and PBS (polybutylene succinate), have good environmental friendliness. In investment casting, wax models made of these materials can be completely decomposed during the casting process without manual removal, which greatly simplifies the production process. However, it should be noted that the strength and accuracy of degradable materials may not be as good as traditional wax materials.
(3) Wax material
Wax material is a traditional investment casting material with good fluidity and formability. 3D printing wax material usually adopts MJP (multi-nozzle jetting) technology, which can achieve high-precision wax model making. The disadvantage of wax material is that it is easily affected by temperature and humidity and needs to be stored and processed in a stable environment.
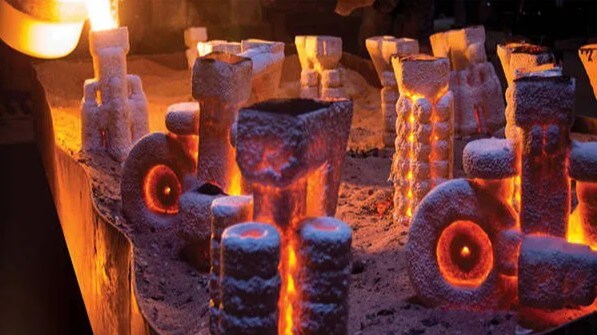
5.3D printing investment casting process optimization strategy
3D printing investment casting technology, as an important process means in modern manufacturing, has significant advantages in improving production efficiency and product quality. The following is the optimization strategy of 3D printing investment casting process to further improve its performance and application range.
(1) Material selection and optimization:
1) Selection of high-performance materials:
Select 3D printing materials with good thermal stability and small deformation, such as ceramic-based composite materials, to improve the accuracy and surface quality of castings.
2) Material modification:
By adding an appropriate amount of reinforcing phase, such as silicon carbide, aluminum oxide, etc., the mechanical properties and heat resistance of the material can be improved.
(2) Process parameter control:
1) Precise control of printing parameters:
Precisely control parameters such as printing speed, layer thickness, and printing temperature to reduce deformation and cracking.
2) Optimize post-processing process:
Post-process the printed wax model, such as grinding, polishing, surface coating, etc., to improve its surface quality and dimensional accuracy. In addition, for materials such as photosensitive resin, heat treatment is required to improve its heat resistance.
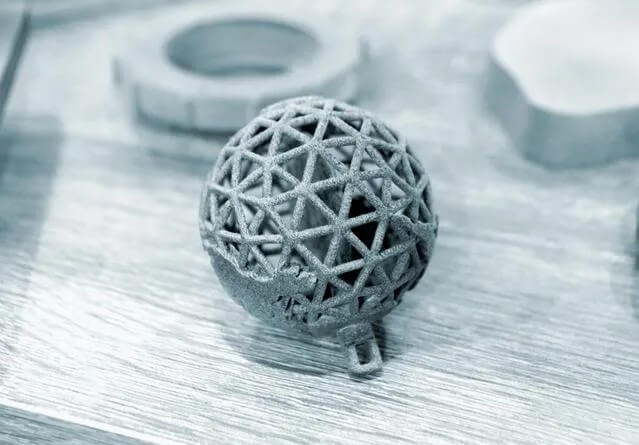
(3) Structural design optimization:
1) Topology optimization:
Use topology optimization technology to lightweight the casting structure, reduce material usage and production costs while ensuring performance.
2) Thermal stress analysis:
Through finite element analysis and other methods, the thermal stress of the casting during the solidification process is predicted and optimized to avoid thermal cracking.
(4) Equipment upgrade and maintenance:
1) Introduce high-precision equipment:
Use high-precision 3D printing equipment to improve the dimensional accuracy and surface finish of the casting.
2) Regular maintenance and calibration:
Perform regular maintenance and calibration on the equipment to ensure that it is in good working condition.
6.Practical application areas of 3D printing investment casting
As an innovative technology in modern manufacturing, 3D printing investment casting technology has been widely used in many fields.
(1) Manufacturing of high-temperature alloy parts in the aerospace field
In the aerospace field, the performance requirements for parts are extremely stringent, especially engine parts that need to withstand extreme conditions such as high temperature and high pressure. Traditional manufacturing methods are difficult to meet the precision and performance requirements of these complex parts. 3D printing investment casting technology can produce high-temperature alloy parts with complex internal structures and excellent mechanical properties by using high-performance metal powders and precise printing processes.
For example, an aircraft engine manufacturer used this technology to successfully manufacture a new type of turbine blade, which not only reduced weight but also improved thermal efficiency and reliability.
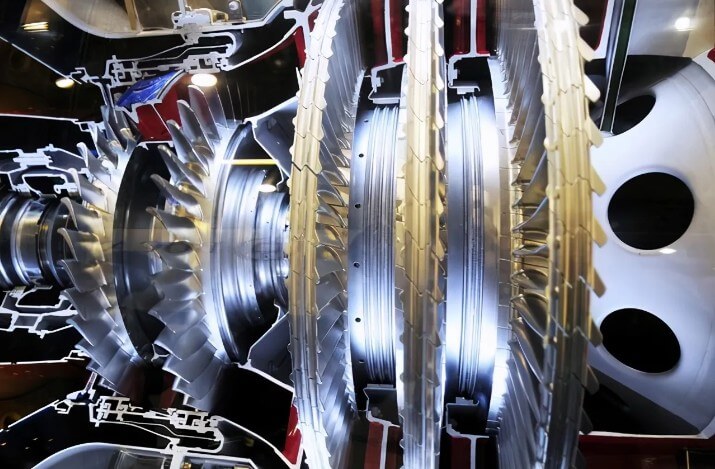
(2) Personalized implant production in the medical field
In the medical field, patients’ needs for implants are highly personalized and precise. 3D printing investment casting technology can quickly produce customized metal implants, such as artificial joints and orthopedic plates, according to the patient’s specific condition and anatomical structure. These personalized implants can better match the patient’s body, improve the success rate of surgery and postoperative recovery.
For example, a hospital used this technology to customize a titanium alloy bone plate for a patient with a complex fracture, successfully achieving precise reduction and fixation.
(3) Development of lightweight components in the automotive industry
With the automotive industry’s continuous pursuit of energy conservation, emission reduction and performance improvement, lightweight design has become an important trend. 3D printing investment casting technology can achieve effective material utilization and weight reduction by optimizing the structure of components.
For example, an automobile manufacturer used this technology to manufacture an aluminum alloy engine block, which not only reduced weight by 30%, but also improved heat dissipation performance and durability.
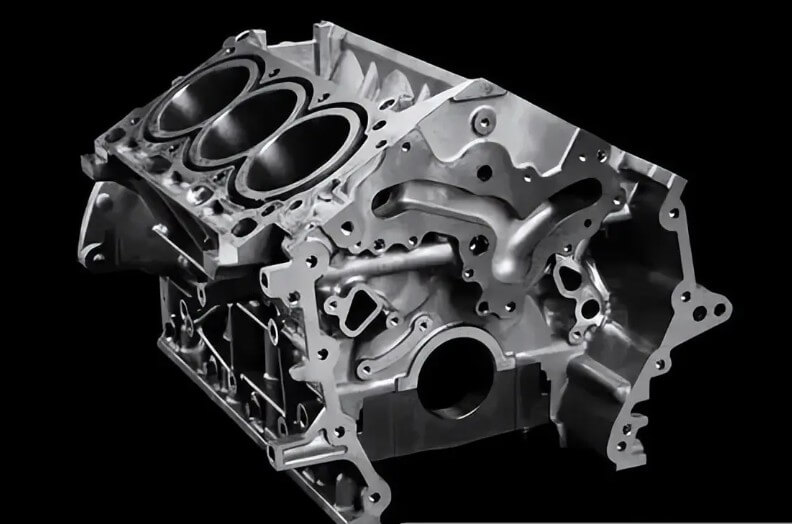
7.Summary
The application range of 3D printing investment casting technology is wide, including aerospace, automobile, medical, dental and other fields, especially in the manufacture of complex, high-precision metal parts. With the continuous advancement of technology and the reduction of application costs, it is expected that 3D printing investment casting technology will be more widely used in the future.